8RB50 Rotary Basket Washer
The Arnold Machine 8RB50 Rotary Basket Immersion Washer is a versatile cleaning system designed for small parts with demanding cleanliness standards. This 3-stage machine includes washing, rinsing, and drying processes. Ideal for cleaning fuel system components, electrical parts, stampings, machined components, and virtually any other items that fit within its 6” x 12” x 18” basket capacity.
The machine presents a reliable design of over 40 years, featuring a four-over-four basket layout that allows for eight baskets to be loaded per cycle. Each cycle included a timed immersion and rotation within the wash basin, followed by a rinse cycle. Both processes are enhanced by high-pressure spray heads. Additionally, a freshwater rinse can be incorporated into the cleaning process. For the drying stage, a high-pressure heated blower is utilized, along with a timed cycle to ensure that the parts are thoroughly dried according to the requirements of each cycle.
Benefits of 8RB50 Rotary Basket Washers
- Completely manufactured in the United States
- Includes a freshwater rinse cycle
- Touch screen displays
- Dynamic motion basket cycle to ensure complete cleaning of hard-to-reach areas
- Customizable cleaning recipes allow simple changeovers between different parts and cleaning requirements
- Wash basin viewing window with integrated lighting
- Lift-off access covers for easy access to chip and debris basket
- Pump Screens for protection from chips and debris
- Large tank doors for easy access for cleaning and maintenance
- Stainless steel bag filters for wash and rinse tanks
- Solenoid valve for automatic maintenance of wash and rinse water levels
- Sixteen standard Kadon 6” x 12” x 18” baskets with lids
- Integrated fork pockets and lifting eyes
- One-year warranty on parts and labor for components and workmanship, and ten-year limited warranty on structural integrity
How 8RB50 Rotary Basket Washers Work
8RB50 Rotary Basket Washers can wash 8 baskets of parts at a time, typically in a four-over-four configuration. A typical wash cycle is heated wash > heated rinse > heated dry.
For precision-clean applications, Arnold Machine can add an ultrasonic bath into the wash cycle. We can also configure your machine to have additional rinse cycles, including fresh water rinses.
The time of a wash cycle will vary based on the requirements of your application. A common wash cycle is 12-15 minutes–in this application, 8 baskets of parts are completely clean and dry in just 15 minutes.
Common Applications
The 8RB50 Rotary Basket Washer is ideal for applications that involve small parts, parts that can fit into baskets that are roughly 6" x 12" x 18".
This machine is used by manufacturers across a wide range of industries. It is particularly popular in the automotive industry for parts such as brake components, transmission components, and other small automotive parts.
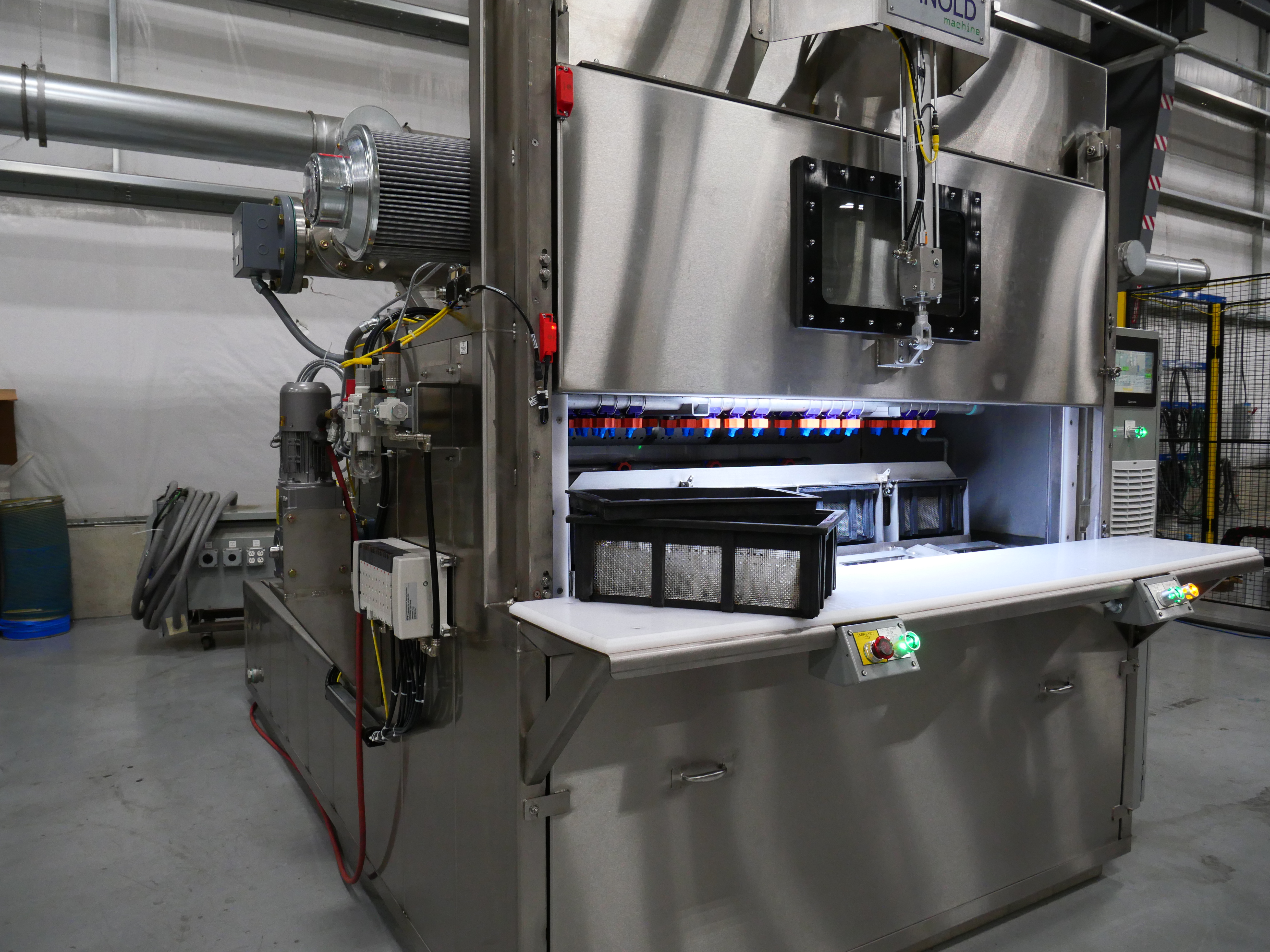
Specs
- Machine dimensions – 12' long x 9' wide x 8' tall – approx. 8,500lbs dry weight.
- 38” operator load height with stainless steel load table
- Base machine is 10gal stainless steel and features 2” insulation covered with 16gal polished stainless steel
- Tank floors are pitched to a 2” stainless steel drain valve
- Utility requirements:
- 480 VAC – 3 phase - 60 Hz – 200 AMP power
- 3/8”, 80 PSI compressed air
- 1”, 35 PSI fresh water supply
- Two 2” NPT tank drains
- Control system:
- NEMA 12 main control panel with sequester 480v, 200amp main disconnect.
- UL approved 24 VDC controls package with Allen-Bradley CompacLogix PLC and Weintek 10” touch screen control panel.
- Pre-programmed wash cycle recipes customizable to specific needs.
- 215 gallon wash and rinse tanks, each with 10hp, 125gpm pumps and 40Kw electric heaters.
- 15hp centrifugal dry off blower with 24Kw electric heat.
- 1/4hp basket rotate drive motor
Optional Items
- Ultrasonic Cleaning System
- Mist Collector
- 25-gallon Coalescing Oil Removal System (can be added to wash and/or rinse circuits)
- Automatic Chemical Monitoring & Addition
- Single Point Tank Drain
- Canadian CSA Certification
- Service Plan Options
- Additional Baskets & Customized Fixturing
- Automated loading and unloading
- Stainless steel solution pump
- High-pressure and high-flow applications
- Additional filtration options (progressive, multi-bag, cartridge, magnetic, etc.)
- Filter pressure monitoring systems
- Additional heating options (gas, steam)
- Additional control options available (relay logic, Siemens, Mitsubishi, Omron, etc.)
- Oil separation (disk skimmer, belt skimmer)
- Sludge management (drag-out conveyor, clarifier)
- Powered exhaust (exhaust fan, mist collector)
- Noise reduction package
- Spray/immersion wash and rinse
Arnold Machine acquired FMT in July 2020, and Arnold Machine’s extensive automation experience, combined with FMT’s industrial parts washer expertise, allows us to offer unique automation capabilities to parts washers. Our products include features such as material handling and automated (or robotic) loading and unloading.
Trust Arnold Machine with Your Parts Washing Needs
Are you looking to improve your current parts-washing process? Arnold Machine specializes in designing and manufacturing custom parts washers tailored to your needs and requirements. We ensure that your equipment will meet the highest cleanliness standards and provide efficiency and durability. Contact us today to get a quote and discover how we can optimize your parts-washing process.
8RB50 Parts Washer FAQ
-
Will the 8RB50 fit in our available space?
-
How often will I need to drain and clean the tank?
-
What does the Arnold Machine 8RB50 custom parts washer cost?
See our resources—or case studies below—to help you in the research process.
FEATURED POSTS
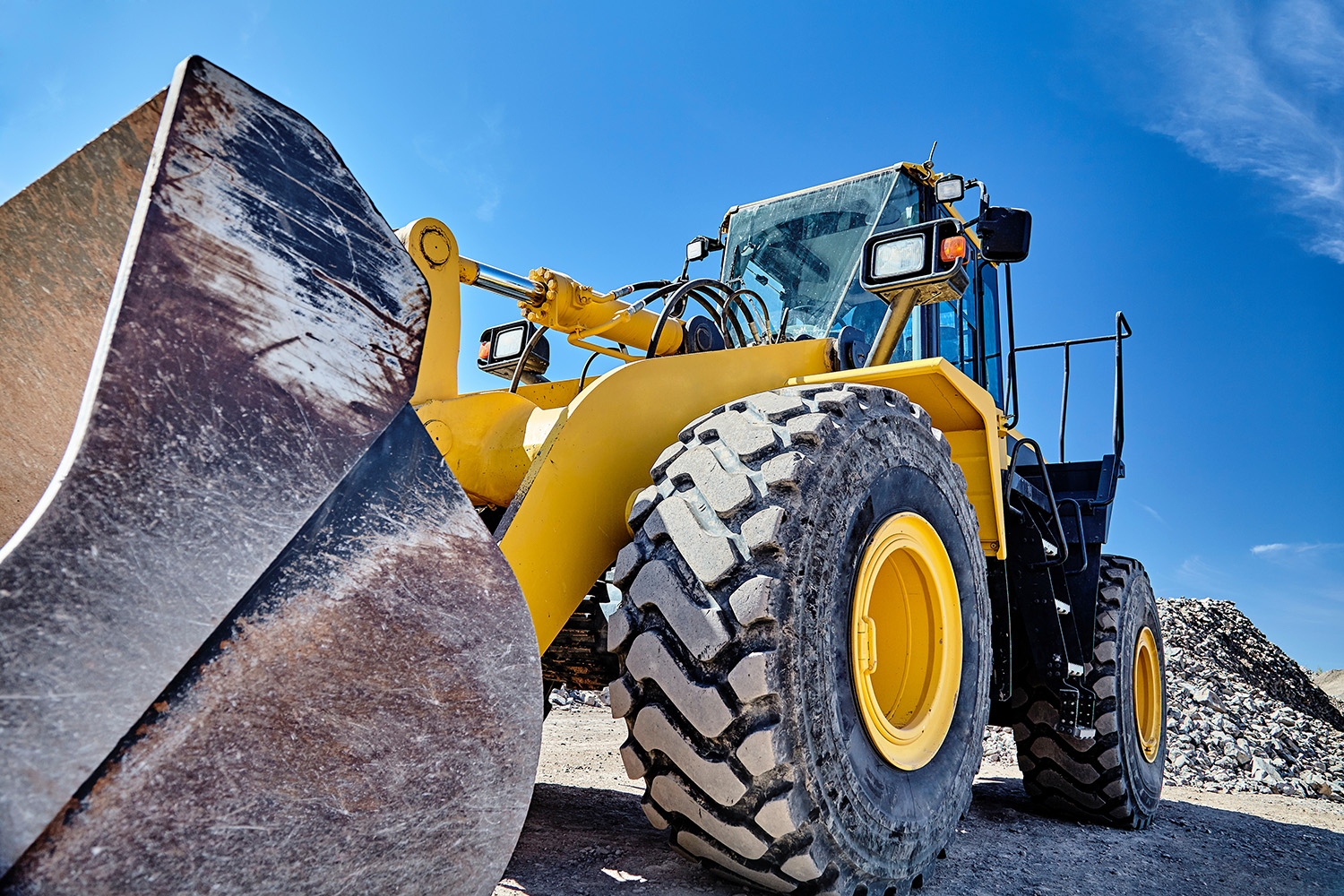
8RB50 Parts Washer: A Solution for Construction Manufacturers
Learn how a custom-designed 8RB50 Parts Washer helped a heavy-duty construction equipment manufacturer improve its corporate cleaning.
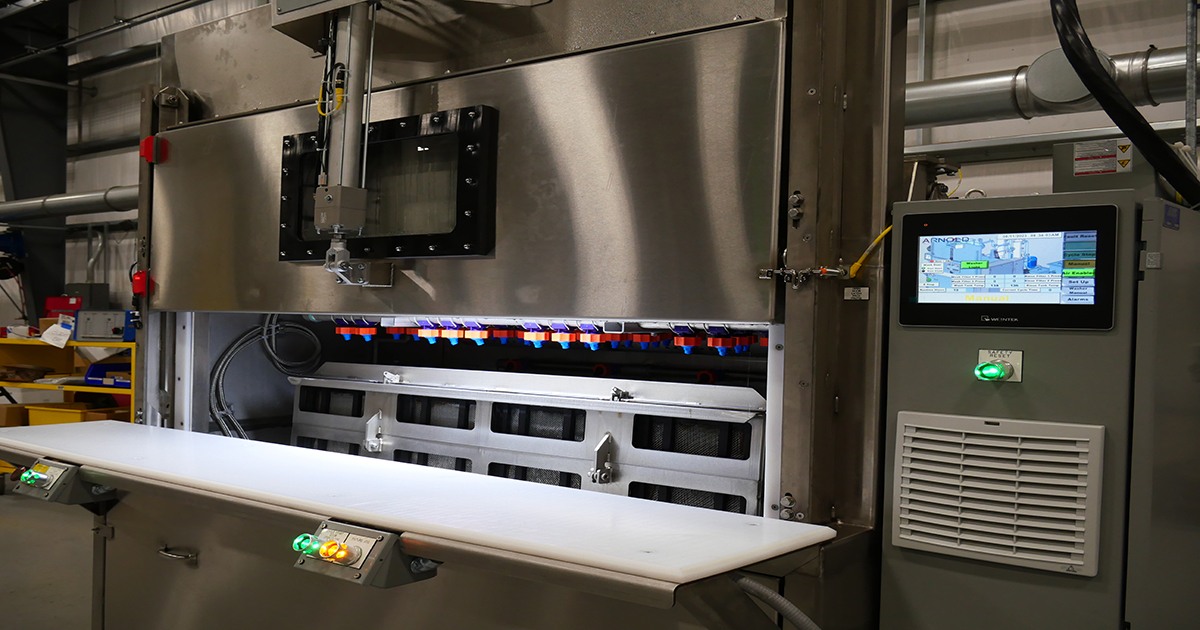
3-Stage Rotary Basket Washer Increases Capacity
Learn how a 3-Stage Rotary Basket Washer helped a major supplier of metal stampings meet its cleaning needs with increased capacity.
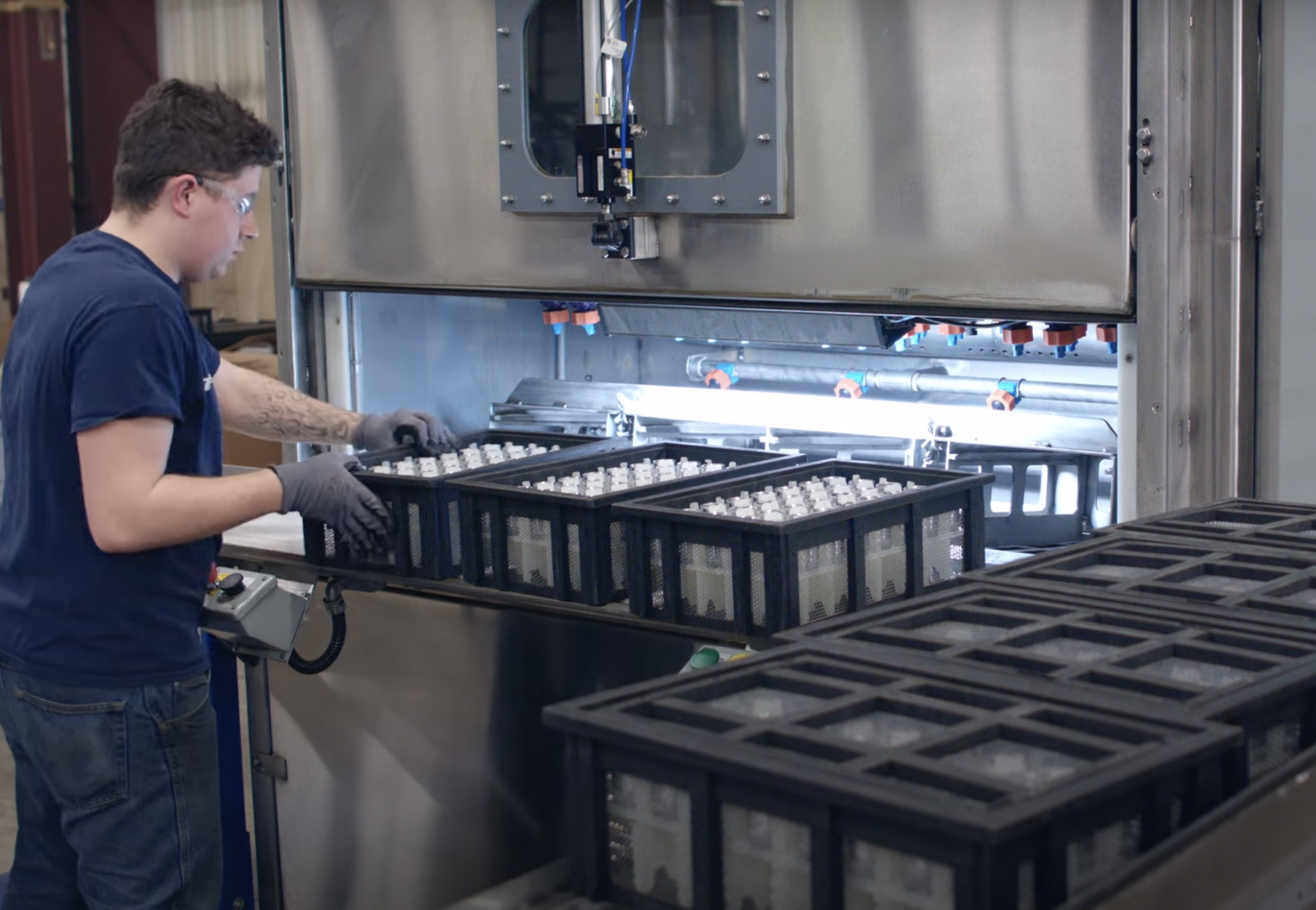
What is a Fully-Automated Rotary Basket Parts Washer?
Learn about the features and benefits of fully-automated Rotary Basket Parts Washers and their advantages over manual cleaning processes.