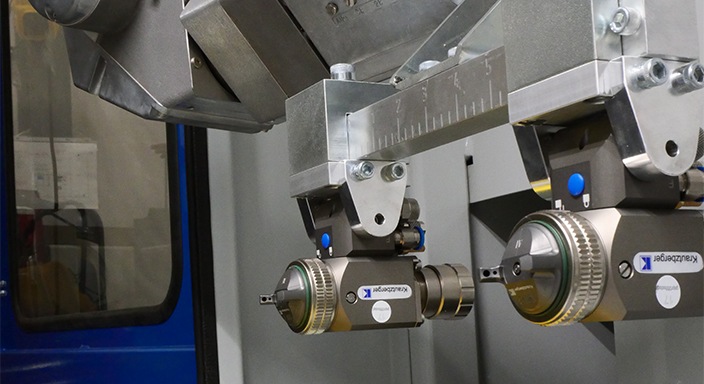
Increasing Production with an Automated Chain-on-Edge Spray System
Automotive manufacturer dramatically improves production rate with automated chain-on-edge spray system
When manufacturers commit to automating some of their operations, they must accept some tradeoffs that come with the territory.
Perfection is impossible. Manufacturers can’t have the fastest, cheapest, safest and most efficient system all at once.
Below, we discuss an automated spray machine design that has helped many automotive manufacturers alleviate some of the common challenges that accompany tradeoffs in automating production.
CHALLENGE: The Cost Of High Speed - Reduced Transfer Efficiencies
Rubber-to-metal bonded parts are practically universal across automotive manufacturing applications. To keep overall production costs as low as possible, manufacturers have introduced systems that automate the adhesive application process for these high-volume components.
A popular iteration of this idea is to send components past stationary spray nozzles that dispense adhesive. Here’s the typical setup we see:
- Cylindrical metal components are loaded onto a chain-on-edge conveyor.
- Sometimes the components pass through a pre-heating oven to reach a consistent temperature to optimize adhesive application.
- The parts then pass by fixed-position nozzles that spray the adhesive.
- To fully cover the diameter of the parts, they are rotated as they pass the nozzle.
Continuous motion chain-on-edge machines such as what’s described above can spur increased production rates. But the increased rates these machines provide come with these critical disadvantages: Decreased transfer efficiency and reduced control over spray patterns and the amount of material applied.
SOLUTION: Indexing Chain-On-Edge Plus Electronic Traversing Spray Guns
Productivity in manufacturing is a function of volume over time. Successful automation doesn’t always mean processes are faster. In studying systems like these, we’ve concluded that some processes can move slower and still be much more productive if volume dramatically improves.
The automated indexing chain-on-edge and electronic traversing spray gun system we designed proves the point. Here’s how it works:
- Parts are attached to spindles on a chain-on-edge conveyor. But instead of just one part per spindle, our system stacks multiple parts onto each spindle.
- As before, the parts enter a pre-heat oven.
- Next, the parts reach the spray station—and stop.
- The spray station features spray guns with extension kits. When the conveyor stops, the guns extend downward into the part stack. On their way back up, the nozzles dispense adhesive.
- As before, the parts rotate on their spindles to allow for full inside diameter coverage.
- After the wands exit the stacks, the parts move on to drying.
The impact this improvement can make is compelling. Suppose that a system that processed one part at a time could apply adhesive to each part every two seconds. That’s five parts per ten seconds or 30 parts per minute.
Now, suppose the improved system stacks parts three high and the two-wand spray system applies adhesive to six parts every ten seconds. That’s 36 parts per minute. Extrapolate that over an eight-hour work shift and the improved design can process 2,880 more parts than its predecessor.
BENEFITS
Consider these additional process control benefits:
- Our design allows for control of the spray application speed as well as spray timing with servo control. The guns only spray when inside the part stack. They apply the coat evenly, reducing material usage.
- Precise flow meters guarantee that adhesive is dispensed evenly every cycle. This also allows operators to detect and address adhesive flow problems faster.
- Loading and unloading of the system is much easier because it’s synchronized with stop cycles.
- Overall, the system is more productive, more precise and less wasteful. And if manufacturers choose to add optional robotic pick-and-place capabilities, human involvement is further reduced, adding to the overall precision and reliability of production.
Read More: Benefits of Automated Spray Coating Systems
Improve Your Existing Automated Processes
As this case study shows, initial automation of a process is never the end of the story. Technology improves. Designs mature. There will always be an opportunity to improve.
Our team knows that “automation” isn’t the novelty it used to be. Today, true process improvement often means revisiting existing automated processes to make them a better version of themselves.
If your facility is ready for a next-generation automation upgrade, we should talk.