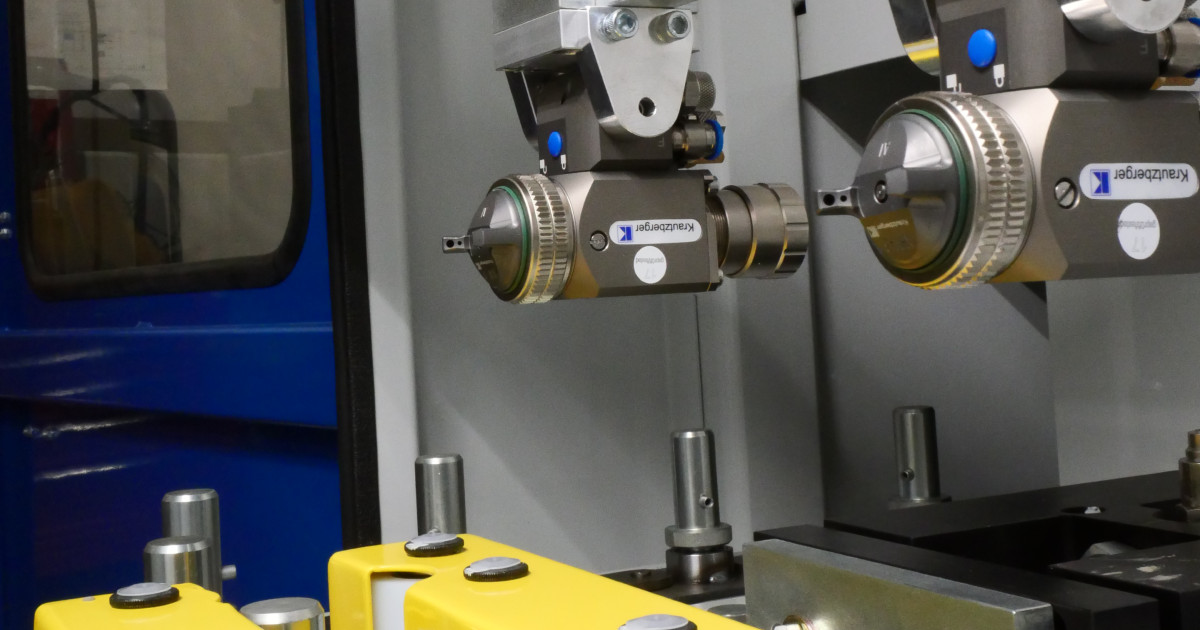
BENEFITS OF AUTOMATED SPRAY COATING SYSTEMS
Manual spray coating often results in inconsistent finishes and wasted materials. This increases labor costs and makes it difficult for companies to maintain consistent quality. These inefficiencies lead to increased expenses and production delays.
Automated spray coating systems offer a range of benefits that transform the coating process. These systems improve efficiency, quality, and customization while providing a significant advantage over manual methods.
Read on to learn more about the many benefits of spray coating automation.
WHAT ARE AUTOMATED SPRAY COATING SYSTEMS?
Automated spray coating systems apply coatings to products with precision and efficiency. Robotic arms, programmable controllers, and specialized spray gun nozzles work together to automate the process. This automation reduces human intervention and enhances overall performance.
Automation in coating processes offers significant advantages over manual methods. Improvements include:
- Improved transfer efficiency
- Enhanced quality control
- Increased throughput
- Customized solutions
- Operator safety
Explore these benefits below in greater detail to see how automated systems outperform manual coating methods.
IMPROVED TRANSFER EFFICIENCY
Automated spray coating systems significantly enhance transfer efficiency, saving costs and reducing waste. This key metric in spray coating processes refers to the amount of coating material that covers a part compared to how much material sprays past the part and is wasted. Transfer efficiency is expressed as a percentage. For example, 70% transfer efficiency means that 70% of the sprayed material reaches the part.
Manual vs. Automated Processes
In manual coating processes, an operator typically controls the spray gun parameters. This includes needle adjustments, pressure settings, and spray pattern changes. The effectiveness of manual processes depends on the operator's ability and judgment.
Hand movement and spray patterns can vary from part to part when using a handheld spray gun. This inconsistency often leads to more material consumption. Operators may not follow a defined path for coating, leading to inconsistent results and potential scrap.
Advantages of Automated Solutions
Automatic solutions reduce the need for operator input. They allow for precise control of parameters and set points. This focus on consistent settings helps improve transfer efficiency. Automated systems can use defined paths for coating, reducing material waste.
Reducing manual intervention leads to more consistent results. This consistency typically results in higher transfer efficiency percentages compared to manual processes. Automated systems can significantly improve coating efficiency by minimizing variations and optimizing material usage.
ENHANCED QUALITY CONTROL
Automated spray coating systems offer significant advantages in quality control. These systems ensure consistent and precise coating application across entire surfaces. This precision minimizes common defects associated with manual application, such as uneven finishes, drips, or runs.
Precision and Consistency
We program our automatic spray coating systems for uniform coverage, thickness, and consistent precision. This level of consistency is difficult to achieve with manual processes.
Automated systems maintain consistent process parameters throughout the coating application. These parameters include spray pressure, nozzle distance, and drying conditions. By keeping these factors constant, the systems reduce the likelihood of defects like orange peel, blistering, or adhesion issues.
Real-Time Monitoring and Adjustments
Many automated coating systems come equipped with flow monitoring sensors and paint verification devices. These tools provide real-time feedback on crucial parameters such as temperature, pressure, and material flow. This immediate feedback allows operators to make quick adjustments during the application process.
The ability to monitor and adjust in real time ensures optimal coating quality. It minimizes defects and maintains consistent results throughout production runs. This level of control is a significant improvement over manual processes, where such precise adjustments are often challenging to implement.
Material Optimization and Waste Reduction
Automated systems excel at optimizing material usage. They precisely control the amount of coating applied to each part. This precision targeting minimizes overspray and reduces material waste compared to manually coating parts.
Excess coating is often applied unintentionally in manual applications. Automated systems eliminate this issue, leading to more efficient use of materials and improved cost-effectiveness.
Documentation and Traceability
Arnold Machine's automated systems often include comprehensive documentation features. These systems record each coated part's process parameters, material usage, and quality control data. This detailed documentation facilitates thorough quality assurance processes.
The traceability features enable manufacturers to track and analyze trends over time. This data-driven approach continuously improves coating processes and overall product quality. Such detailed tracking and analysis are typically not feasible with manual coating methods.
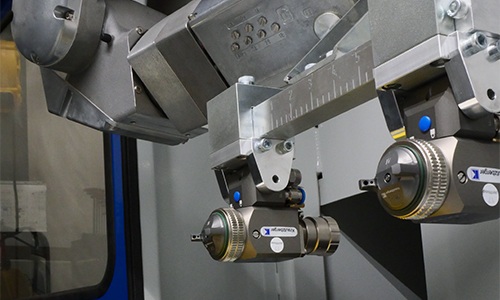
INCREASED THROUGHPUT
Automated spray coating systems offer significant production speed and efficiency advantages. These systems can operate continuously without the need for breaks or shifts. This continuous operation maximizes equipment utilization and minimizes idle time between coating cycles.
Accelerated Application Rates
Automated systems apply coatings at higher speeds than manual processes. This accelerated application rate allows for faster part processing, increasing throughput without sacrificing coating quality.
Arnold Machine's solutions are programmed to optimize process parameters, including spray pressure, nozzle distance, and coating thickness. The systems achieve faster coating speeds by fine-tuning these parameters while maintaining consistent quality.
Parallel Processing Capabilities
Many automated coating systems, such as Arnold Machine's Chain-on-Edge systems, can coat multiple parts simultaneously. These systems use multiple spray guns and robotic arms. This parallel processing capability significantly increases throughput by coating various parts in a single cycle.
The ability to process multiple parts at once reduces overall production time. It enables manufacturers to meet higher production demands without expanding their facility footprint.
Minimized Downtime
Automated systems often feature quick-change tooling and programmable setups. These features allow for rapid changeover between different parts or coating materials. The flexibility minimizes downtime associated with retooling and setup changes.
These systems maximize equipment utilization by reducing setup times. This increased efficiency contributes directly to higher throughput rates.
Scalability and Integration
Automated coating systems can be seamlessly integrated into existing production lines. This integration allows for the continuous flow of parts through the coating process, eliminating bottlenecks and optimizing overall production throughput.
Our more custom systems also offer scalability to accommodate changes in production volume or part complexity. Manufacturers can easily adjust throughput to meet fluctuating demand without significant investment in additional equipment or resources.
OPERATOR SAFETY
Automated spray coating systems significantly enhance operator safety compared to manual processes. Arnold Machine's solutions precisely control coating applications, minimizing overspray and reducing airborne particles. Reducing exposure to potentially hazardous chemicals improves respiratory health and lowers the risk of skin contact for operators.
Accident Prevention and Hazard Reduction
Manual coating processes often involve handling spraying equipment and moving parts, increasing accident risks. Automated systems incorporate safety features like interlocks and sensors to prevent accidents. These design elements prevent the likelihood of operators coming into contact with moving parts or hazardous materials.
Consistent and uniform coating applications reduce the need for manual reapplication. This minimizes the time operators spend in potentially hazardous environments. Operating these systems remotely or via an HMI allows monitoring from a safe distance, further reducing exposure to dangerous materials.
Ergonomic Considerations and Training
Another essential feature is the ergonomic design. This focus on operator comfort minimizes strain and fatigue, reducing the risk of repetitive strain injuries and musculoskeletal disorders often associated with manual coating processes.
While operator training remains essential, automated systems typically require less complex safety protocols than manual processes. This can streamline safety training while maintaining compliance with regulations. The overall result is a safer work environment with reduced physical risks for operators.
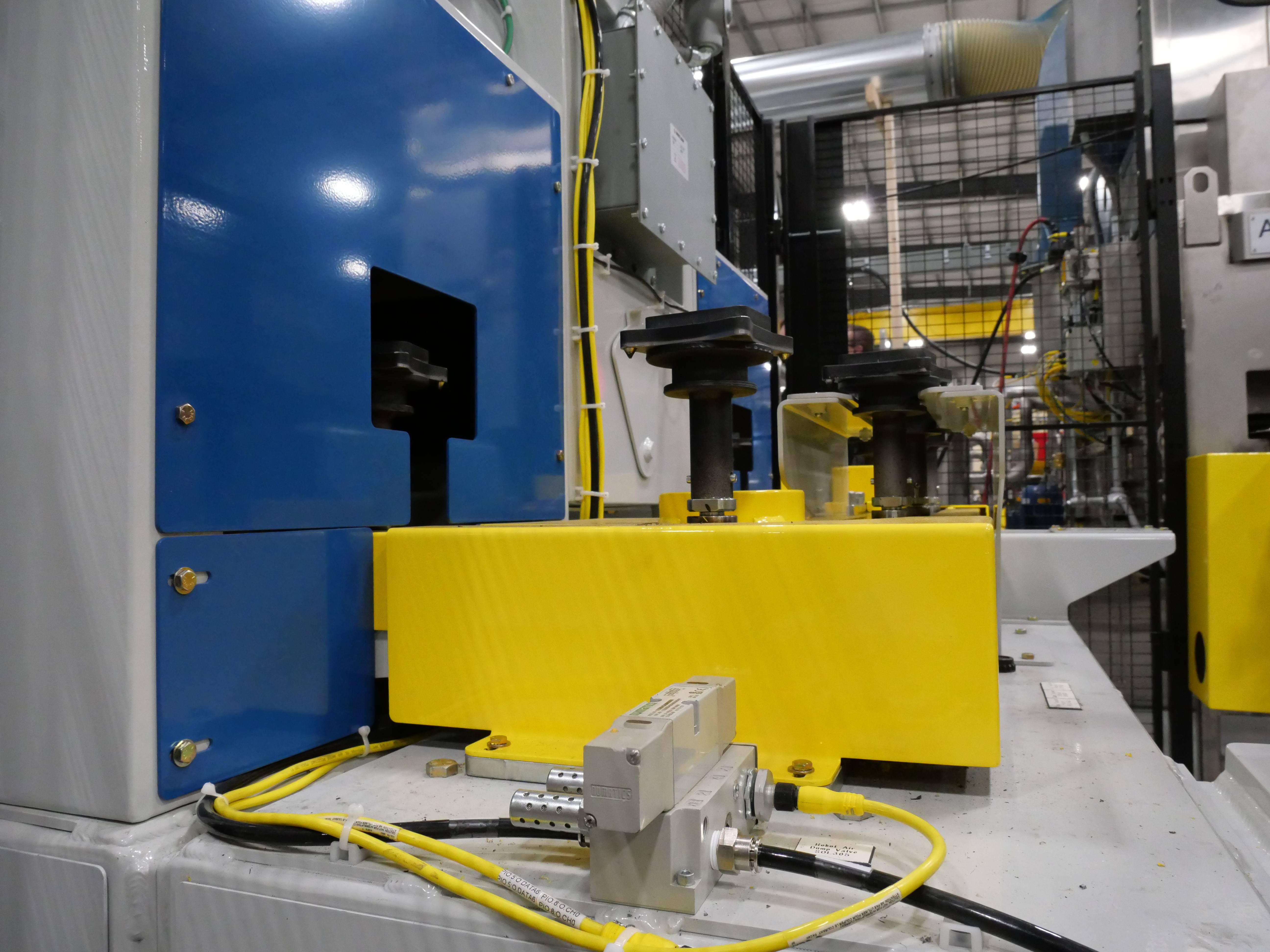
CUSTOMIZED SOLUTIONS
Arnold Machine excels in developing tailored coating systems for unique customer applications. Our expertise in customization allows us to address specific challenges across various industries. We work closely with manufacturers to create solutions that enhance product performance and efficiency.
Aerospace Component Protection
A manufacturer of metallic abrasion strips for rotor blades approached us with a complex challenge. They needed a coating system to protect delicate substrates from extreme temperatures and corrosive environments. The process also required an integrated curing oven.
Our team collaborated with the manufacturer to develop a multi-layered coating process. This customized system protects against temperature fluctuations, moisture, and chemical exposure. The result was significantly increased rotor blade lifespan and improved performance in demanding aerospace environments.
The tailored solution reduced the manufacturer's maintenance and replacement costs. It also enhanced its market position by offering products with superior durability and reliability.
Anti-Vibration Component Coating
An anti-vibration component manufacturer sought our expertise for a unique adhesive coating challenge. They needed to transition from a manually applied product to an atomized coating while maintaining their existing fixturing process. The manufacturer was apprehensive about integrating automation into their established workflow.
Arnold Machine conducted a thorough site visit and conceptual engineering process. We developed a customized coating system that accommodated their specific fixturing requirements. The new system could coat up to 12 parts on a fixture and fit within the confined footprint.
This tailored solution minimized labor costs and changeover time while achieving significant material savings. It also allowed the manufacturer to upgrade their technology and prepare for expansion.
Benefits of Customization
Our customized solutions offer manufacturers numerous advantages. They experience improved product performance and longevity, leading to long-term cost savings. Tailored systems often result in more efficient processes, reducing labor and material costs.
Companies that invest in customized coating solutions gain a competitive edge in their markets. These specialized systems enable the production of higher-quality products, enhancing reputation and attracting more customers. Our customized solutions help manufacturers stand out by addressing unique challenges.
ARNOLD MACHINE SPRAY COATING SYSTEMS
Arnold Machine's automated spray coating technology is characterized by versatility. These advanced systems adapt to diverse coating materials, substrates, and industry applications. We tailor each solution to specific requirements, from painting to adhesive application and protective coatings.
Investing in automated coating technology yields substantial long-term benefits. Users experience significant savings through reduced material waste and improved efficiency despite initial costs. Lower labor costs further contribute to a strong return on investment over time.
Every coating solution we design prioritizes customization and seamless integration.
We design each system to meet unique production needs while fitting into existing manufacturing processes. This approach streamlines workflows and boosts overall efficiency. Regular maintenance and thorough operator training ensure peak performance, maximizing equipment lifespan and minimizing downtime.
TRANSFORM YOUR COATING PROCESS WITH ARNOLD MACHINE’S EXPERTISE
Automated spray coating systems improve efficiency, quality control, and production speed compared to manual processes. They optimize material usage and reduce waste. Arnold Machine specializes in creating customized coating solutions that deliver significant long-term benefits and a competitive edge.
We lead the industry in automated spray coating systems. Our expertise in customization and integration ensures optimal performance for diverse applications. Explore our advanced solutions to enhance your coating processes and achieve significant long-term benefits.