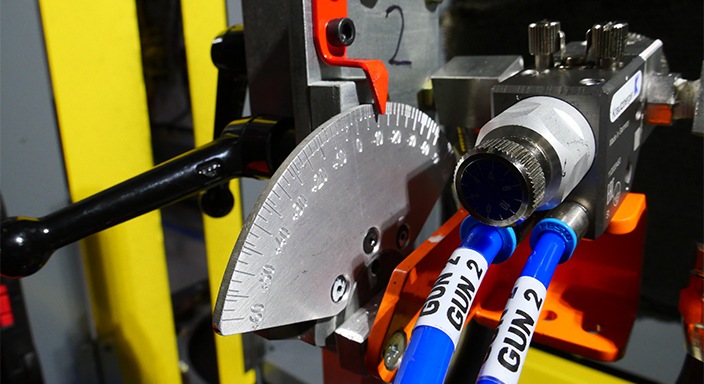
Increasing Production & Consistency with an Automated Rubber-to-Metal Adhesive Spray Coating System
Automated, rubber-to-metal spray coating ensures less material waste and requires minimal operator skill
The Challenge:
A leader in heavy duty equipment, anti-vibration manufacturing approached Arnold Machine after an adhesive used for applying an adhesive bonding agent to steel alloy bushings in their coating process became obsolete. The customer decided to use that opportunity to upgrade their manual processes to automatically apply the adhesive to reduce the level of operator skill needed and to reduce material costs.
The Data:
Arnold Machine designed, manufactured, and commissioned an automated, rubber-to-metal adhesive spray coating system that automatically applied a single coat adhesive agent to the outside surface of multiple steel alloy bushings. Arnold Machine manufactured an indexing system to allow for multiple parts to be stacked (up to 46”) and utilize (2) automatic spray guns to apply in a single station. The system has proven to be efficient and provide a consistent repeatable end-product by:
- Minimizing Overspray & Wasted Material
- Repeatable & Consistent Coating of Adhesive
- Minimal Operator Skill Required
The Results:
The system has proven to increase production throughput and apply a consistent coverage. After being in production for over two months, the end user has noticed a reduction in material usage and an improvement in environmental air quality at the facility.
The Solution:
The main objective was to consistently and efficiently apply an adhesive bonding agent to steel alloy bushings. For Arnold Machine, the process is similar to previous automated indexing lines produced. The experience and diverse background of Arnold Machine made this an efficient design and build.
The challenge was efficiently cradling the fixtures and allowing the operator to remove with ease. Arnold Machine collaborated with the end users using multiple conceptual models and designs to achieving the best ergonomic method.
The system utilizes an enclosed spray cabinet; proprietary, non-sparking chain conveyor; and a removable pressure pot.
The solvent-based adhesive agent resides in a 5-gallon pail with agitation. Agitation, pot pressure, and spray gun functions are all controlled and monitored in one location, easily accessible to the operator. The material is then automatically supplying two automatic spray guns within the booth.
The steel alloy components are stacked up to 46 inches high on a pole-type removable fixture. Full fixtures are operator loaded to a servo powered indexing conveyor. The conveyor design allows for top and bottom containment.
An electromechanical switch is utilized to determine if the substrate is indeed loaded and presented to a coating booth. This process is performed while the conveyor operates at a continuous programmable speed. The loaded fixture then conveys through a coating booth where a pneumatic coupler engages to the bottom side of the fixture to rotate the fixture at a programable speed.
Two automatic spray guns transfers in a linear motion to coat the steel alloy components. The process requires the steel alloy components to receive specific film thickness which varies from one part type to the next.
The human interface allows for recipe storage for the various part types. Contributing factors for the recipe are the linear speed the material is applied, the fixture/part rotation speed, spray gun positioning settings, and spray gun fluid and pressure settings.
Once the steel alloy components have been coated to a specific film thickness, the process allows for some buffer stations to begin drying the wet adhesive. Finally, the operator will then remove the fixture from the conveyor and transfer to a secondary process. The system utilizes safety features to eliminate the operator from exposing themselves to the automated spray process. Solvent laden air is also exhausted to improve air quality around the system.