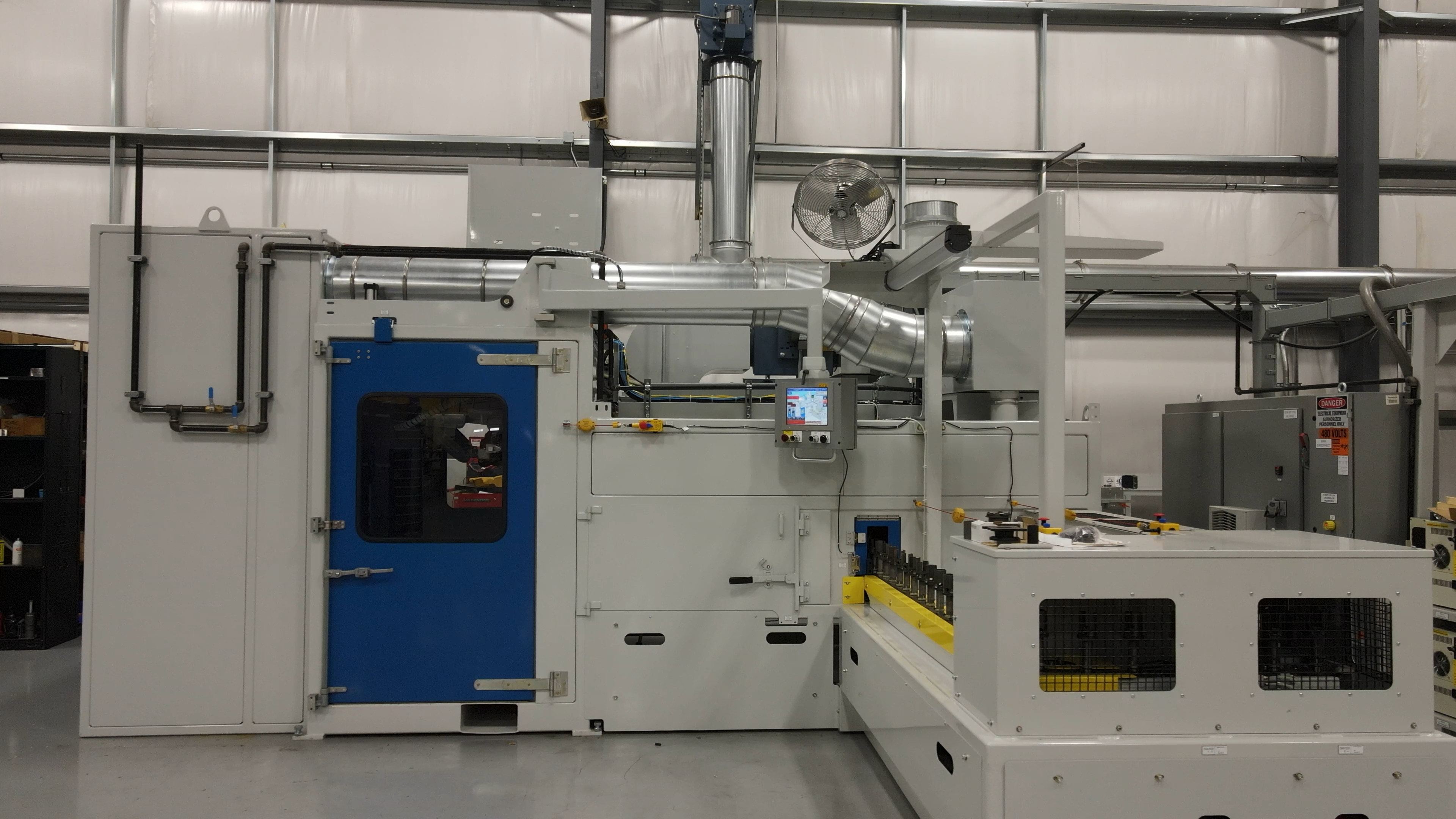
HOW TO INCREASE YOUR SPRAY COATING EFFICIENCY
Struggling with inefficient spray coating processes can be frustrating. Wasted materials, higher labor costs, and decreased output are common issues that can make it challenging to maintain productivity and profitability.
Optimizing your spray coating processes is essential for streamlining operations, as it addresses the root causes of inefficiency. Additionally, several effective strategies can help reduce costs and enhance your competitive edge.
Read on to learn more about increasing spray coating efficiency.
WHY IS SPRAY COATING EFFICIENCY SO IMPORTANT?
Standard spray methods have around 10-30% transfer efficiency, which often results in significant material waste. A mere 5% improvement in efficiency can potentially save around $300,000 annually. Consider the savings across 6 million parts, with $0.05 saved per part.
Improving spray coating efficiency is crucial for boosting productivity and profitability in manufacturing operations. Several key factors contribute to this enhancement. Evaluating current methods helps identify areas for improvement in equipment, labor, and logistics.
Additionally, exploring alternative coating techniques, investing in new technologies, and restructuring workflows can eliminate bottlenecks and reduce waste. These steps are essential for enhancing overall performance and reducing operational costs.
4 WAYS TO IMPROVE SPRAY COATING EFFICIENCY
There are four primary options for improving spray coating efficiency: outsourcing, insourcing, adding operators, and investing in automated coating solutions. Each approach offers unique benefits and challenges, and the best choice will depend on the specific needs and circumstances of the business.
1. Outsourcing
Outsourcing your part coating process can be an effective solution for businesses looking to increase capacity without incurring the costs and responsibilities of in-house production. Specialized coating providers offer a wealth of expertise, equipment, and resources. They can help reduce internal staff workload and minimize infrastructure demands.
However, outsourcing also comes with a few potential drawbacks. Companies may face communication challenges, longer lead times, and a loss of direct control over the coating process. Quality control can be more difficult to maintain, and shipping costs and logistics can add complexity and expense to the overall operation.
2. Insourcing
Insourcing, or bringing the coating process in-house, allows companies to maintain greater control and flexibility over their operations. This approach ensures quality control and enables quick adaptation to changing demand. Companies can more easily accommodate shifts in product requirements with in-house resources.
However, insourcing also requires significant upfront investment in equipment, facilities, and training. Companies must have the necessary resources and expertise to manage the coating process effectively. Scalability can also be a challenge as production needs grow.
3. Adding Operators
Companies often consider increasing staff as their first solution to boost coating output. More workers dedicated to coating can potentially increase production. This approach may also help reduce lead times for customer orders.
Finding skilled labor presents a significant challenge in today's job market. Retaining these workers can be equally difficult for businesses. Increased labor costs accompany the addition of operators to a company's workforce. These expenses include wages, benefits, and necessary training programs.
Manual processes have inherent limits to their scalability. Adding more operators may not always yield proportional increases in output. Companies must carefully weigh these factors when considering staff expansion.
4. Investing in Automated Coating Solutions
Automated coating solutions offer significant potential for improving spray efficiency and quality. These systems deliver consistent results with greater accuracy and speed than manual processes. Automation reduces human intervention, minimizing errors and waste while increasing overall throughput.
Precision matters in adhesive spray coating. Even slight variations can impact your bottom line significantly. For example, getting the adhesive thickness just right can lead to cost savings of up to $780,000 or more annually.
Automated solutions improve transfer efficiency and reduce material waste over time. Labor costs decrease as machines handle more tasks, contributing to long-term cost reductions for businesses. Worker safety also improves, with employees facing less exposure to potentially hazardous materials.
BALANCING STRATEGIES FOR OPTIMAL OUTCOMES
Evaluating strategies to improve spray coating efficiency requires considering business needs and goals. Outsourcing can reduce costs but may sacrifice quality control and flexibility. Adding operators seems intuitive, yet finding skilled labor poses challenges. Automated solutions offer potential savings despite initial investment.
Machine-as-a-Service (MaaS) combines outsourcing benefits with greater efficiency and control. MaaS is a middle ground between full outsourcing and in-house operations. Analyzing requirements helps businesses find effective solutions based on their circumstances. The best strategy depends on individual company objectives within the spray coating process.
Investing in automated coating solutions brings improved accuracy, consistency, and throughput. These benefits lead to long-term cost savings and enhanced competitiveness. A balanced approach considers specific business needs while recognizing automation's potential for optimized efficiency.
REAL-WORLD EXAMPLES
Arnold Machine partnered with a Tier 1 automotive supplier to develop an advanced spray coating system for small auto parts. The customer needed precise application of anti-corrosive material.
We created a multi-station setup featuring automated washing and robotic painting. This integrated solution processes up to 60 parts per hour with consistent quality, allowing the customer to streamline their production process significantly.
In another instance, an automotive manufacturer specializing in anti-vibration components sought to optimize coating operations for rubber-to-metal bonded parts. Arnold Machine designed a high-speed Adhesive Roll Coating System that merged two separate processes into one seamless operation.
This system handled varied parts at double the previous speed and maintained 100% transfer efficiency, allowing the customer to meet demanding production rates with minimal waste and reduced manual intervention.
IMPROVE EFFICIENCY THROUGH OUR AUTOMATED SPRAY SOLUTIONS
At Arnold Machine, we understand the importance of optimizing spray coating efficiency for manufacturers. We’re experts in designing and building automated spray coating systems. We’ve helped countless businesses achieve significant improvements in productivity, quality, and cost savings.
Ready to improve your part coating efficiency? Take the next step today by assessing your current processes and exploring the options outlined in this guide. Click below for an in-depth look at the value our automated spray coating systems offer.