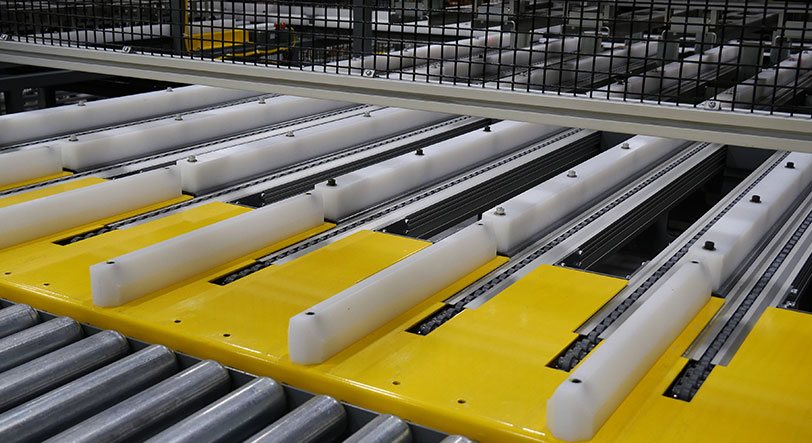
COMBINING AUTOMATION & PARTS WASHING
Creating an automated load/unload Inline-6 Rotary Basket Parts Washer for a firearms manufacturer
A world-renowned manufacturer of firearms, ammunition, and firearm accessories contacted Arnold Machine after deciding to bring magazine production in-house. They needed a highly customized automatic parts washing solution to meet a strict cleanliness specification.
The company decided to incorporate automation into its manufacturing process to address supply demands and any future labor issues proactively. This included automating tasks such as material handling, assembly, and inspection.
THE CHALLENGE
The customer wanted the ability to wash the magazines in between the stamping and welding processes. Each magazine needed to meet an ultra-precise cleanliness level to ensure no contaminant or oil would interfere with welding—as any leftover residue could lead to quality defects.
Adding to the challenge was that the magazines could not tumble against each other during the washing process. Otherwise, damage could occur to their intricate parts. The different part lengths also posed a problem. Arnold Machine needed to find a way to ensure thorough cleanliness while simultaneously washing different magazine lengths.
This project was the first collaboration between the recently acquired FMT Parts Washer division and our existing automation teams. It combined our unique knowledge and skill sets, serving as an excellent way to kick off the acquisition.
THE SOLUTION
After discussing the various challenges with the firearms company, our team designed an automated rotary basket industrial parts washer system that utilized:
- Arnold Machine Rotary Basket Parts Washer
- FANUC Vision Guided 6-axis Robot
- FANUC 2D Vision
- Multiple Conveyor Systems
Our engineering team determined the baskets needed an extra insert to ensure the parts remained stable during the washing process. They solved this by designing a 3D-printed insert that was attached to the bottom of the baskets.
The insert kept the parts separated and stable. This separation allowed for easy basket loading while preventing the magazines from tumbling against each other during washing, rinsing, and drying.
Our engineering team designed a “top-hat” solution for the multiple-part lengths issue. The top hat moved down until about 0.040” from the top of the parts. The adjustable top-hat allowed slight movement of the magazine parts so that the proper amount of solution could flush around to maintain the required cleanliness specifications.
THE DATA
Bringing the process in-house gave the customer much-needed quality control. It also provided the production capacity to prevent potential product shortages. The parts washer completes four wash cycles per hour for 24 baskets. Each basket holds 40 parts and produces an output of 960 magazines per hour.
The entire system only requires one part-time operator. They simply need to load parts into baskets and feed them onto the infeed conveyors. The automated load/unload Inline-6 Rotary Basket Parts Washer handles the rest.
THE RESULTS
Upon completing this system, Arnold Machine received overwhelmingly positive feedback from the end user. Discussions are already underway for future projects.
“[Client] could not be more pleased with the equipment received and the work performed by Arnold Machine. The entire team was professional, knowledgeable, and courteous. The design, quality, and craftsmanship of the Automated Washer is top notch, a machine we’ll be proud to display within our facility.”
“We look forward to running full production volume so that the machine can demonstrate its true capabilities. [Client] is happy to have found a hard-working company willing to step up to our demanding requirements and hopes to work together again on future projects.”
AUTOMATED LOAD/UNLOAD INLINE-6 ROTARY BASKET PARTS WASHER
The Arnold Machine engineering team chose to modify our standard rotary basket parts washer for the firearms manufacturing client. They did so because it’s ideal for accommodating various part sizes and geometries using standard or custom baskets and fixtures.
Arnold Engineers incorporated several external systems such as the FANUC Vision Guided 6-axis Robot, multiple conveyors, and FANUC 2D Vision to move the components to another line for a secondary process.
The machine operator only needs to load parts into baskets on the conveyor. The automated load/unload arm handles the rest of the work by transferring baskets in and out of the washer. This removes the need to load baskets into the washer manually.
Rotary Basket Parts Washer Benefits
The rotary basket parts washer offers several key advantages including:
- Allows for the quick loading of multiple baskets filled with parts. An operator can load several hours of baskets in just a few minutes.
- Permits fast unloading so the operator can walk away to perform other tasks. There’s no need to stand idly by during the entire wash cycle.
- Enables efficient batch processing. The operator only needs to load/unload baskets at the beginning and end of the cycle.
Rotary parts washers are well-suited for batch, precision, and ultrasonic cleaning with 2 to 8 basket capacities. Customers can choose between manual operation or fully automated systems that include spray, partial or full immersion, or ultrasonic cleaning.
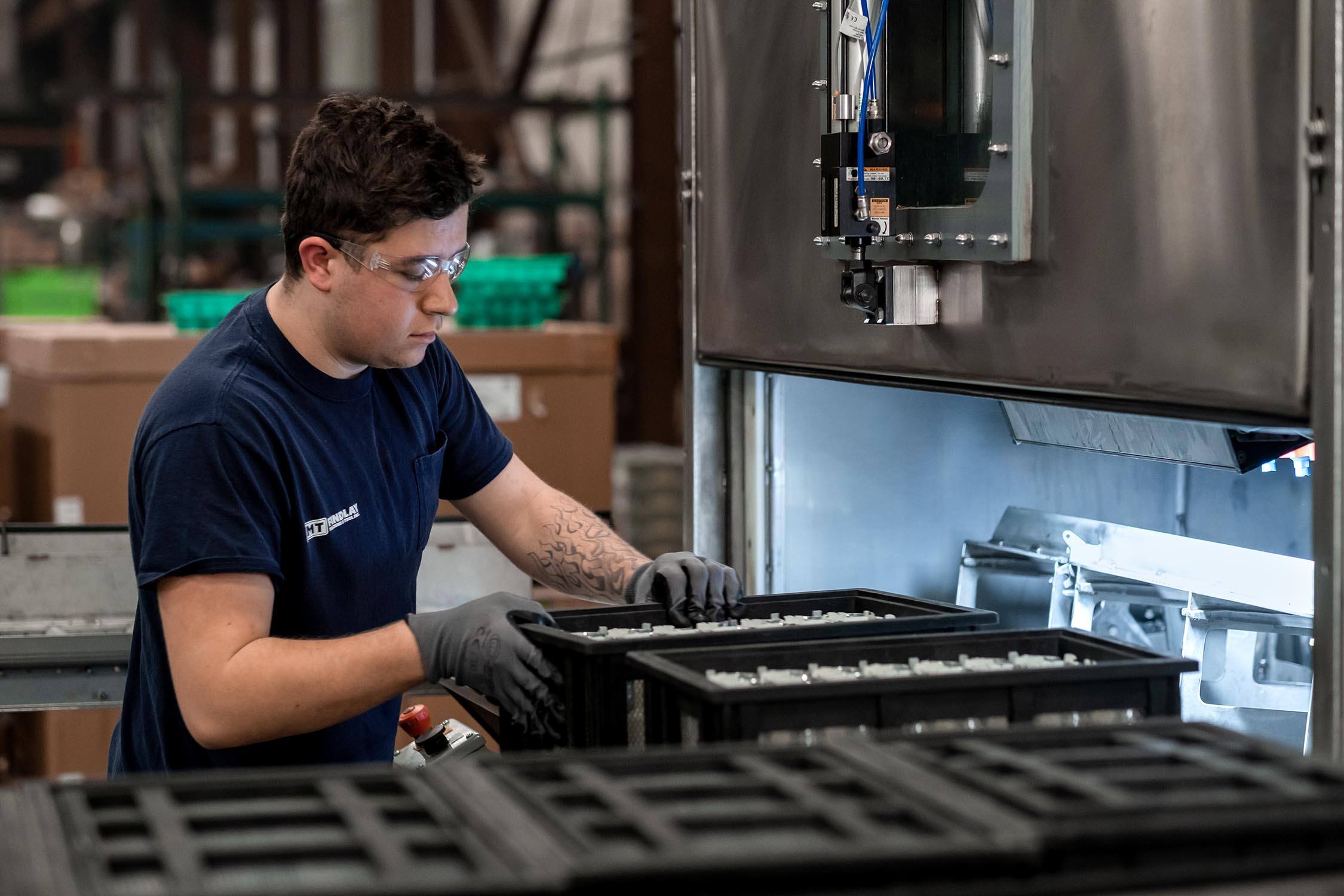
The rotary basket washer's custom-engineered design offers numerous configuration options that include, but are not limited to:
- Multi-stage washing with additional wet stages
- Heated rinse and heated dry cycles
- Automated loading and unloading
- Programmable logic controls (PLC)
- Human-machine interface (HMI)
The inline-6 rotary washer suits high-volume small parts cleaning across aerospace, medical devices, and electronics manufacturing industries. Adding ultrasonics allows the machine to meet high clean specs.
For larger components, manufacturers can also benefit from a pass-through washer with automated unloading that’s integrated into the production line.
CUSTOMIZED PARTS WASHING SOLUTIONS
Arnold Machine’s acquisition of FMT's parts washer division combined robust washing systems with automation and engineering expertise. This unified capability creates fully automated washing solutions that few can match.
The Arnold Machine Engineering team will design and build a customized rotary washer to meet your parts-washing needs. Click below to learn more about our innovative parts washers and the value they offer.