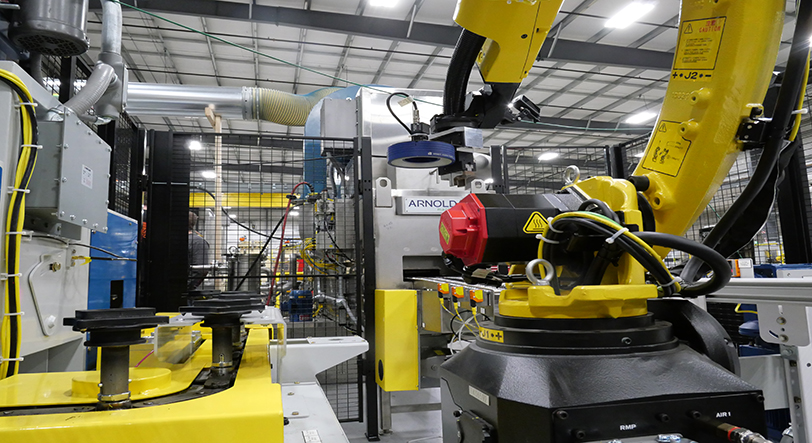
CHOOSING BETWEEN A SINGLE-COAT & TWO COAT CHAIN-ON-EDGE CONVEYOR
Chain-on-edge conveyors provide an efficient way to move and align individual components for processes that require precise positioning, such as painting or coating operations. As a leading maker of coating equipment, Arnold Machine supplies both single-coat and two coat chain-on-edge systems for different types of coating or painting operations.
Keep reading as we explore the differences between our single-coat and two coat systems, the applications for which each is best suited, and important factors to consider when choosing between the two. We’ll also consider a case study to illustrate this process in action.
SINGLE-COAT VS. TWO COAT CHAIN ON EDGE CONVEYORS
Is a single-coat chain-on-edge (COE) or two coat chain-on-edge conveyor best for you? It depends on your application and the scale of your operation. Let’s consider the features and benefits offered by each, and the applications for which they are best suited.
Single-Coat Chain-on-Edge Conveyors
Single-Coat (or mini) COE conveyors work on the same principles as full-sized units but at a smaller scale. Like two coat COE machines, mini systems allow products to be moved through the paint booth either in intermittent “indexed” motion or continuously.
However, there are also important differences. In comparison to two coat systems, Single-Coat COE units feature:
- Lower capacity: Accommodate fewer components per batch, usually between 24 and 48 fixtures, making them more suitable for moderate throughput operations.
- Single coating station: Includes only one spray gun operating at a single coating station, allowing items to be processed with one layer of paint or adhesive.
- Smaller footprint: Typically fits within a 6’x8’ footprint (excluding heating/drying modules), more suitable for operations where floor space is limited. Units are custom-built, so actual sizes vary.
- Shorter oven dry times: Shorter preheat and drying times, with a typical oven cycle time averaging about one minute, compared to 2 minutes in the two coat system. This makes Single-Coat COE systems best suited to handle one coat applications with moderate part-to-part cycle time requirements and production volumes.
- More flexibility: Designed with smaller batch producers in mind, Single-Coat COE systems are built to be quick to adjust for different products and simple to reconfigure for handling larger parts than full-scale models.
- Simple part geometry: Single-Coat systems offer effective exterior coverage and with additional options available for the system, can coat the interior diameters of hollow or ring-shaped components.
- Lower cost: Mini COE units cost about half as much as a two coat system, so they’re a viable alternative for smaller or multi-line operators.
Single-Coat COE systems are ideal for one-coat applications where cost, flexibility, footprint size, and cycle times are more important than overall throughput capacity. The modular design of these machines also improves convenience and efficiency during installation, especially on smaller shop floors.
In addition, our Single-Coat COE systems are equipped with advanced robotic spray gun technology, allowing for more accurate paint and adhesive placement than most existing COE systems. That can lead to reduced overspray, easier cleanup, and big savings on coatings.
Single-Coat COE systems are most commonly used in automotive and industrial applications for coating simpler components such as brackets, bushings, and mounts, where a single-layer application meets performance standards. It’s also a practical choice for general manufacturing processes that require protective or adhesive coatings without the need for multi-layer adhesion.
Two Chain-on-Edge Conveyors
Two Coat COE units are designed to deliver effective at-scale processing of components, especially where two layers of coating are required. In comparison to SIngle-Coat COE systems, they feature:
- Higher capacity: Full-scale units can handle more parts per batch, typically up to 180 fixtures, increasing throughput.
- Double coating stations: Feature two spray guns included in two independent coating stations that can be separately adjusted.
- Smaller footprint: Requires more space, usually about 8’ wide x 24’ long. Footprint also includes integrated loading, heating, and drying modules and paint and coating storage areas.
- Longer oven dry times: Longer preheat and drying times benefit the application of two layers of paint or coating, while still allowing for a 2-3 second part-to-part cycle time, depending on part geometry.
- Less flexibility: These are harder to reconfigure for different parts due to larger batch sizes and more specialized construction.
- More complex part geometry: With two individually adjustable spray stations and a larger spray booth, two-coat COE systems can coat both interior and exterior diameters of parts.
- Higher costs: Typically cost twice as much as comparable mini units.
In general, a full-size COE paint or coating system is a better solution for applications that require enhanced adhesion, durability, and corrosion resistance. A two-coat system is ideal for high-volume production where consistent, high-quality coatings are needed to meet stringent performance and longevity requirements.
Commonly used in the automotive and industrial sectors, this coating process enhances metal components like engine mounts, suspension bushings, and vibration control parts with primers for better adhesion and topcoats for added protection. It’s also applied in aerospace, heavy equipment, and marine industries, where components face harsh environments and demand superior coating performance.
Both the two coat and single coat CoE systems have adjustable part rotation speeds in the spray booth and can be configured for either indexed or continuous motion.
The following table summarizes the differences between single-coat and two coat COE conveyor systems used in coating and painting applications.
Single-Coat vs. Two-Coat Chain-on-Edge Conveyors |
||
---|---|---|
Feature |
Single-Coat CoE |
Two Coat CoE |
Footprint |
6’ x 8’ (6’ x 14’ with modules) |
8’ wide x 24’, including operator section |
Coating Stations |
1 spray gun, single coating station |
2 spray guns per station, two independent stations |
Oven Dry Times |
Shorter |
Longer |
Part Capacity |
Lower (24 - 48 batch count) |
Higher (approx. 180 batch count) |
Rotation |
Adjustable |
Adjustable |
Motion |
Indexed/continuous |
Indexed/continuous |
Design |
Modular |
Integrated |
Throughput |
Lower |
Higher |
Cost |
Lower |
Higher |
FACTORS TO CONSIDER WHEN CHOOSING A CHAIN-ON-EDGE SYSTEM
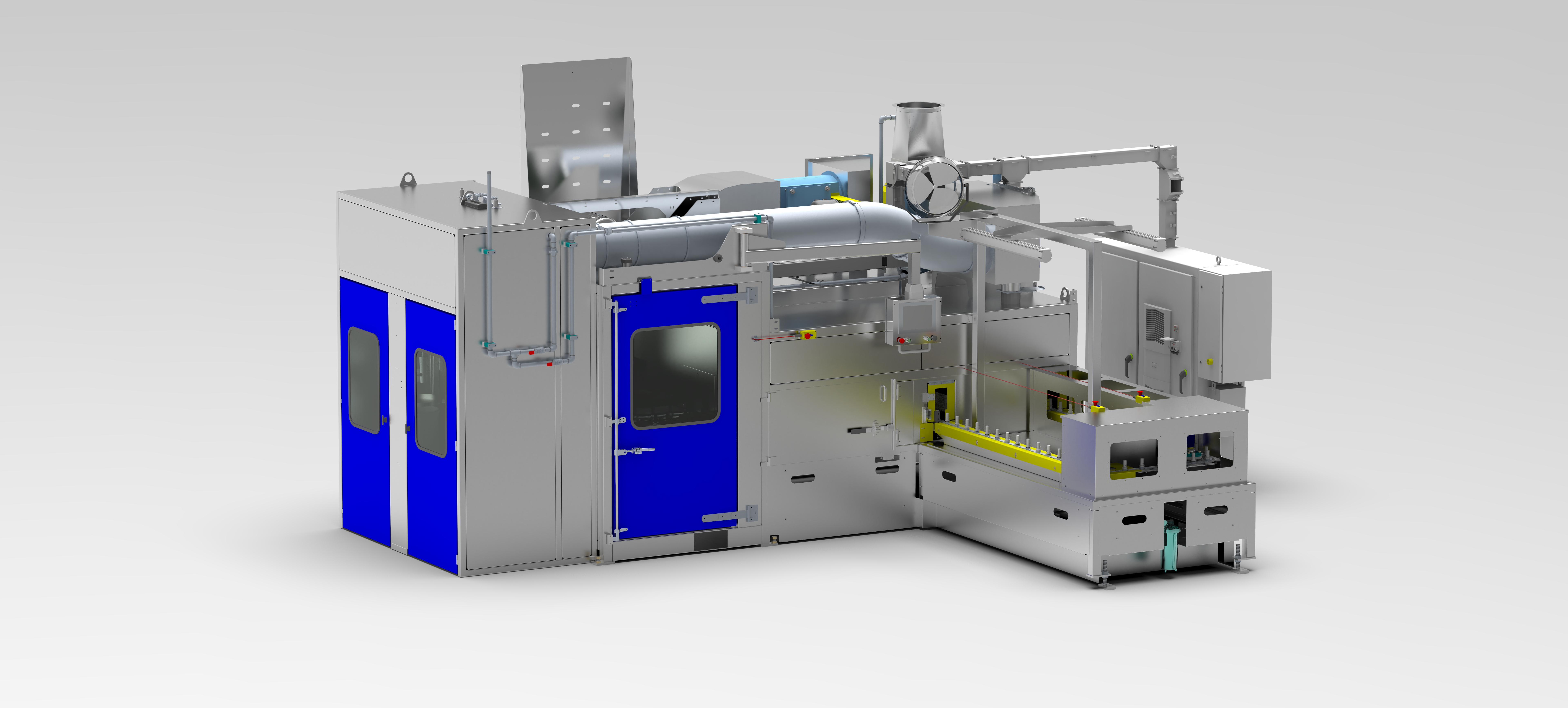
Here are eight key factors to consider when choosing between a single-coat COE or two coat COE system for your coating or painting application.
1. Production Volume
For large-scale producers handling high volumes of standardized parts, a customized two coat COE system is likely the best fit. Smaller producers managing diverse projects for different clients may benefit more from the flexibility of a mini system.
2. One or Two Coats?
If you’re applying both a primer and topcoat to your components (or think you might in the future) then you’ll need the dual coating stations of a Two Coat COE unit. Two separately adjustable spray stations can also be configured to deliver the same coating while giving you better coverage and less wastage than a one-gun single-coat system.
Committed to single-coating work? A single-coat COE system is probably right for you unless you need the added capacity of a system.
3. Part Geometry
Do you need to coat the inner and outer surfaces of a hollow or ring-shaped part? You will most likely need the dexterity of a robot arm within the full-size system, even if you are only applying one layer of coating. For applications where you just need to coat the outside of a part such as a mounting or bushing, a one-coat CoE system will likely do the trick with our fixed spray gun option.
4. Adjustability
How easy is it to configure your unit for different products? Both of our COE systems are designed with the multi-SKU producer in mind and can be adjusted quickly to accommodate different product sizes and geometries, however, two coat systems are focused on the high-volume production of standardized parts and the required amount of fixturing could be more costly for a high mix of products.
5. Available Space
How much space do you have in your facility? If things are tight, then the smaller footprint and more modular construction of a single-coat system might allow you to make better use of the space you have available.
6. Integration
Looking to integrate your coating operation with an existing conveyor system or handling infrastructure? A two coat COE system offers the end-to-end integration and full customizability you’ll need. These units are purpose-built with the size and design flexibility to seamlessly connect with other systems.
7. Scalability
Do you expect to take on more work in the future? There are two ways you can go. You could buy into a lower-priced single-coat COE system and use the cash you save to upgrade to a full-sized operation when demand for your services increases.
Alternatively, you could invest in a two coat COE system, and run it at lower capacity until business picks up. This is also a good option if you’re only providing single-layer coating services now but hope to step up to providing two-layer services later.
8. Budget
In most cases, your bottom line will be the cash you have available to invest in chain-on-edge technology, and how soon you need your investment to pay for itself in increased turnover.
A single-coat CoE unit typically costs about half as much as a two coat CoE system, making it cheaper to enter the market. On the other hand, investing in a full-size system lets you match throughput to demand as you grow and benefit from long-term return on investment.
Want the advantages of a full-size coating machine but not ready to make a capital investment? Consider Arnold Machine’s innovative Machine As A Service (MaaS) offering as a way to access the paint and adhesive capacity you need at a fraction of the cost of purchasing your own equipment.
CASE STUDY: SINGLE-COAT VS. TWO COAT CHAIN-ON-EDGE CONVEYOR
Now let’s take a look at a real-world example of how one manufacturer navigated the choice between a mini or two coat chain-on-edge machine.
Case Study: Single-Coat vs. Two Coat Chain-on-Edge Machines |
Background A leading manufacturer of anti-vibration components required a coating solution for their metal-to-rubber bonding process. Initially, they utilized a two coat COE conveyor system to coat a variety of metal substrates. However, due to increasing demand for lower-volume, high-mix production runs, they sought a more flexible and cost-effective alternative. Challenge The two coat COE machine offered high throughput but proved inefficient for smaller batch sizes, leading to excessive material waste, prolonged changeover times, and higher operational costs. The manufacturer needed a solution that maintained coating quality while optimizing efficiency for smaller production runs. Solution Arnold Machine provided a single-coat COE system as a compact and adaptable alternative to the existing two coat system. The single-coat COE allowed the manufacturer to retain key performance characteristics while offering greater flexibility and cost efficiency. Implementation & Results After implementing the Single-Coat COE machine, the manufacturer experienced:
Conclusion By integrating a Single-Coat COE machine into their coating process, the manufacturer successfully optimized production for low-volume, high-mix applications while maintaining high-quality coating adhesion. The transition from a large COE system to a more adaptable solution allowed them to improve efficiency, reduce costs, and enhance overall operational flexibility. For companies facing similar production challenges, Arnold Machine’s Single-Coat COE system provides a proven solution for optimizing adhesive coating applications. |
WHY CHOOSE ARNOLD FOR YOUR CHAIN-ON-EDGE SOLUTION?
Arnold Machine is a leading manufacturer of advanced chain-on-edge painting and adhesives machinery. We understand that choosing the right coating system is crucial for your business. That’s why we offer a range of fully customized solutions including both full-size and single-coat chain-on-edge conveyor systems.
Trust our experienced team to deliver the cutting-edge coating technology your business needs, along with expert advice and guidance at every stage of your ownership or leasing journey.
Contact us to request a quote, or click below to learn more about our fully automated spray-coating systems.