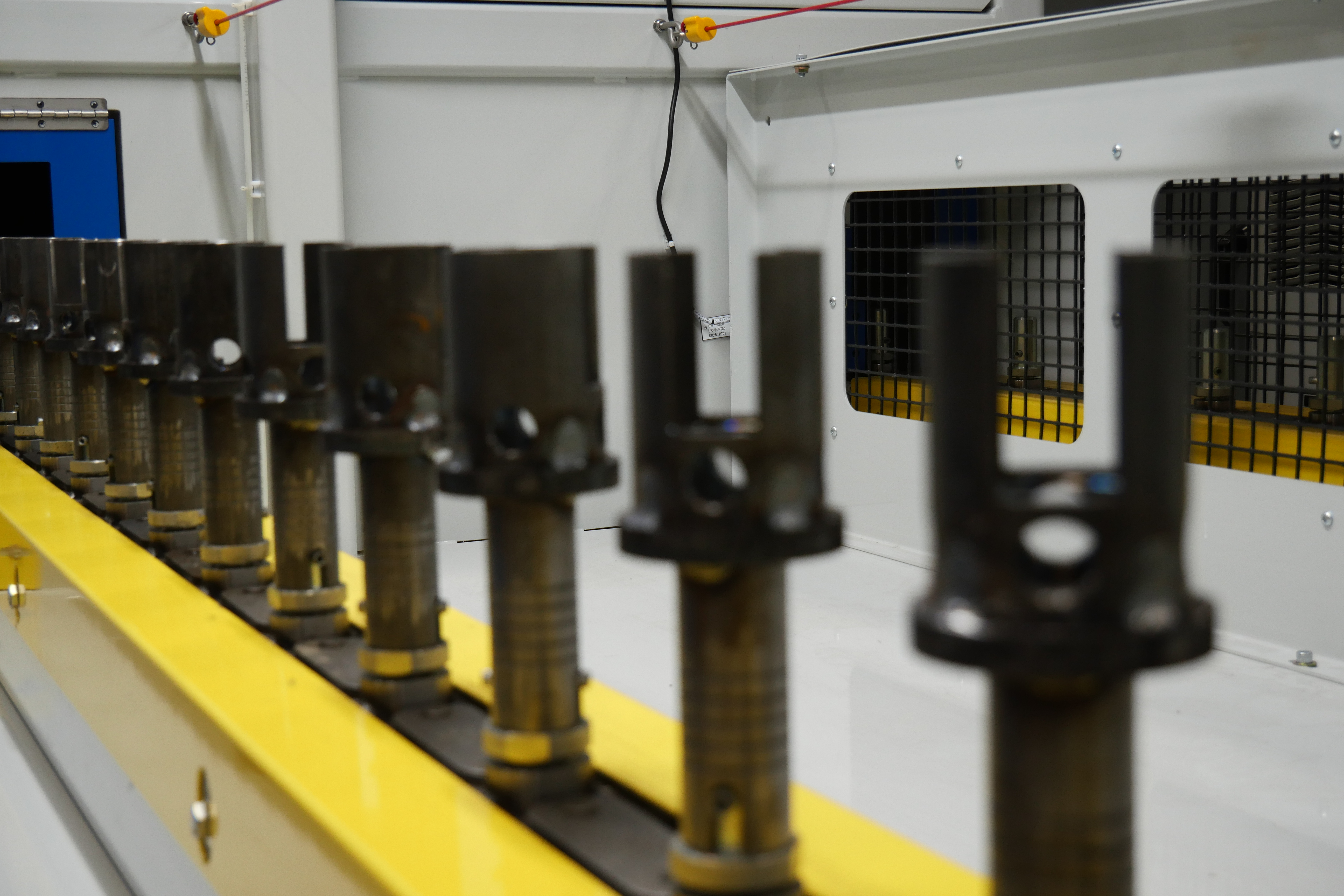
Designing a Custom Automated Anti-Corrosive Coating System for Auto Parts
Chain-on-edge spray coating systems provide a tried-and-true way to boost throughput and lower per-part costs for high-volume manufacturers in the automotive, aerospace, and manufacturing industries. Until recently, higher production and lower cost came at the expense of parts quality, coating consistency, and excessive overspray.
Today, smarter automated and robotic systems from equipment makers like Arnold Machine use indexed chain systems and advanced process-controlled nozzles to deliver precision coating at scale with minimal waste.
Below we look at a specific example of how a major automotive manufacturer was able to leverage Arnold Machine’s next-generation, chain-on-edge automation systems to achieve superior results while increasing productivity.
CASE STUDY: ANTI-CORROSIVE COATING FOR AUTO PARTS
A Tier 1 automotive supplier reached out to Arnold Machine to create an innovative spray coating machine that covers parts in an anti-corrosive water-based material.
Arnold Machine was tasked with designing a cutting-edge spray pattern that would cover small automotive parts with the desired thickness of an anti-corrosive agent for coating. The customer was looking to expand their capabilities in anti-corrosive coating applications and trusted our team to provide an effective, high-productivity solution.
Background
This system was a brand new process requested by the customer. There were many challenges in learning and maintaining an entirely new process and coating was no exception. Previously, the customer was outsourcing this process as they had no experience coating parts. As a value add, the customer decided to keep the coating operations in-house as there would be savings in packaging, transportation, and scheduling.
The customer set aside 12 months to understand the various areas of coatings, the process, and all associated job measures. From selecting the right anti-corrosion product, to developing the type of equipment to perform the job, to choosing the right personnel to perform the work— Arnold Machine worked with the customer in various phases to help spearhead the learning process and provide the various levels of automating the process.
Our team was able to create a multi-station “one-stop shop” that utilized an automated washer, robotic transfer, and automated painting system.
The Challenges
Arnold Machine’s engineering team faced two main challenges in developing the all-new automated coating system: keeping paint away from unwanted areas and improving transfer efficiency to meet quality requirements.
Specifically, our engineering team also needed to deliver a solution that:
- Allowed a small part with complex surfaces to be coated effectively
- Kept coating from the raw cast finish on the top of the part
- Ensured coating thicknesses fell within a range to maintain the part’s aesthetic appeal
The system also required a high level of refinement in the robotic programming and spray gun control systems. Finally, the solution needed to include a fully integrated no-touch washer to ensure no fingerprints, dust, or debris on coated surfaces.
The Solution
To meet these needs, Arnold Machine created a fully integrated indexing chain system that moved parts through a series of individual process stations, each fully designed and built in our facility in Tiffin, OH.
Our chain-on-edge solution features a single robot system designed to load and offload parts while also inserting and removing part masks manufactured out of regular steel. Once in place, parts move in sequence through stations that:
- Preheat parts for optimal coating adhesion
- Coat plants according to one of several product “recipes”
- Allow coated parts to fully cure before further processing
Our solution allowed the most complex part surfaces to be effectively coated to the required thickness and was capable of processing up to 60 parts an hour.
To do this, our team equipped an LR Mate Paint robot with a FANUC America Corporation M10, 2D vision system and a Krautzberger M18 automatic HVLP automatic spray gun. The robot was able to apply the anti-corrosive to part corners and jagged areas that traditional coating methods would not have been able to reach. We also installed a pneumatic tip cleaner to clean the spray gun tip between cycles.
To see how an Arnold Machine Chain-on-Edge spray coating machine works, check out this video:
The Result
Arnold Machine was able to provide a washer and coating system that allowed the customer to have an in-house solution for applying the anti-corrosive to the product. The resources utilized for logistics, packaging, and transporting to an outside supplier are no longer required.
The customer is now able to offer a shorter lead time since the product is now cleaned and coated at the final stages of production. As an added value, the customer can expand their manufacturing ability to offer quality products in other anti-corrosive markets. The customer was pleased to have a single source integrator to create the whole system in one place.
MAAS: INVEST IN A SERVICE, NOT A MACHINE
Modern advanced spray coating solutions allow manufacturers to keep costs per part low and volumes high while achieving ever more refined results and higher product quality.
However, if you’re a market entrant or even an established player looking to launch a new part, diversify your product line, or upgrade an existing system, the upfront capital investment in a purpose-built, chain-on-edge system can still be a significant barrier—and a major risk factor.
That’s why Arnold Machine offers our chain-on-edge equipment as a machine-as-a-service (MaaS).
MaaS allows Arnold Machine to build a cutting-edge coating system for your application and deliver, install, and operate it at your facility for as long as you need it. What’s more, you’ll only pay for your machine when you actually use it. You’ll be charged per minute of production, but you won’t be charged for downtime, scheduled stoppages, or planned maintenance.
Arnold Machine’s MaaS is a sophisticated, scalable approach to targeted insourcing. Instead of making a risky long-term bet on return on investment, you’ll add value from the beginning by:
- Limiting risky capital investment
- Increasing efficiency while lowering taxes
- Reducing your dependence on manual labor
- Flexibility to adapt or return equipment as your needs change
ARNOLD MACHINE: ADDING VALUE, LOWERING BARRIERS
At Arnold Machine, we build premium customized automated equipment for washing, spraying, and painting high-volume manufactured parts including class-leading chain-on-edge automated spray coating systems.
Our coating systems are designed to help you increase processing volume and efficiency without compromising on quality. We’re proud to deliver innovative, US-designed and built systems that help you unlock more value from your products. We’re also lowering the barriers to accessing our technology with our equally innovative machine-as-a-service offerings.
Click below to learn more about our automated spray coating systems or to talk to our knowledgeable staff about how we can meet your specific parts coating needs.