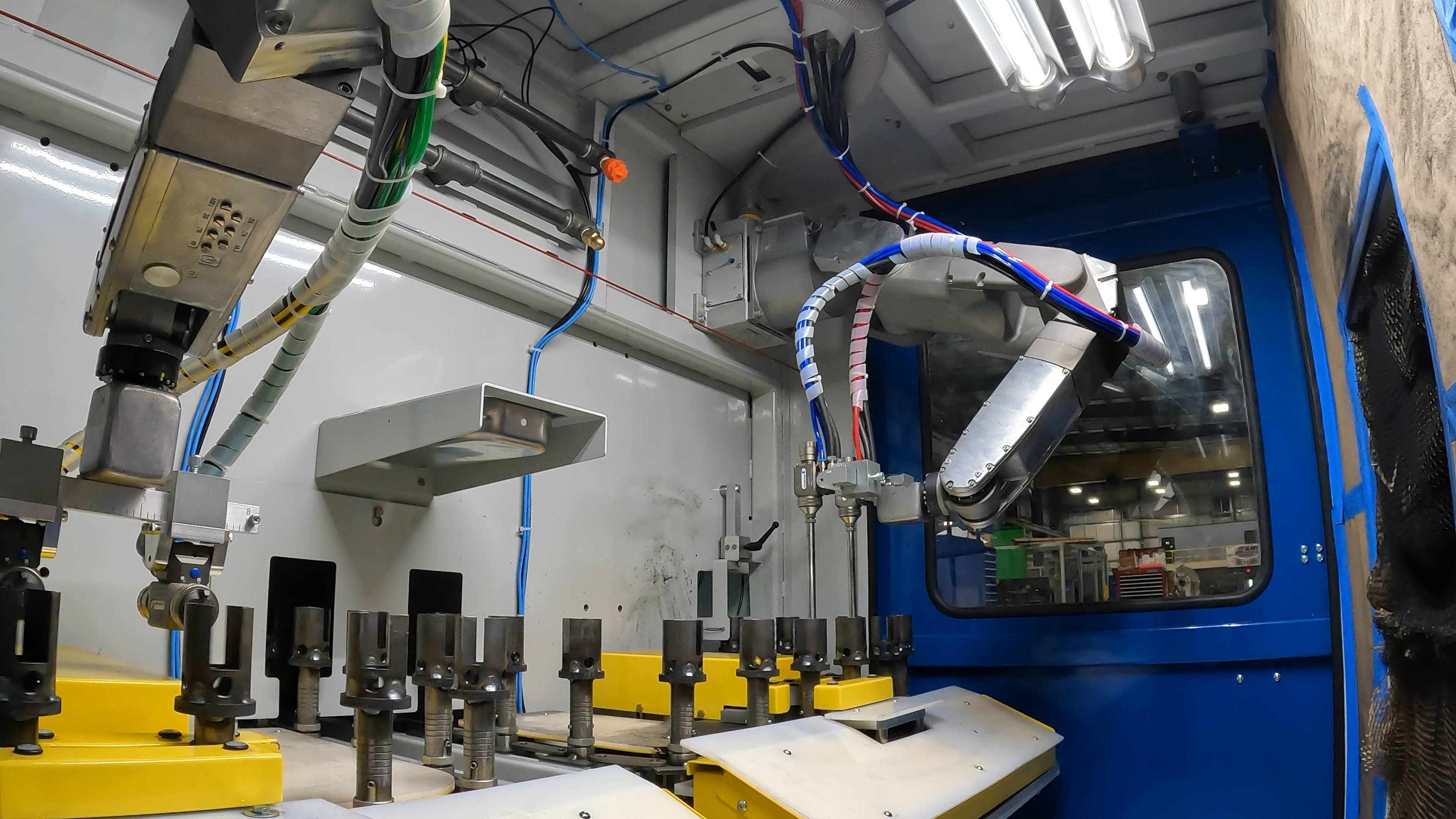
3 Reasons to Consider Spray Equipment Automation
Automation has long been the solution to insulating industrial service providers against ever-rising labor costs and increasing the precision and consistency of operations. In spraying processes such as wet paint and adhesive application, adding automation can improve uniformity, reduce material waste, and provide significant labor savings compared to manual spraying.
By reigning in the variables of the spraying process, namely viscosity, temperature, air pressure, and equipment set-up, finishers can refine their processes to optimize efficiency and quality.
Spray Booth Exterior
Viscosity and Temperature in Spray Coatings
The viscosity of a spray coating and temperature of the substrate are two variables that are not typically well controlled during manual painting processes. The viscosity of a coating must be high enough to sufficiently coat a part without causing the moving mechanisms of the equipment to stick. If the viscosity is too low, the coating can run or require extraneous coats to achieve the desired overall thickness, adding to the time required to complete the job.
Similarly, a cold substrate increases drying time, adversely affecting production efficiency. Automated spray systems essentially remove human error and variance from the equation. The user simply sets the desired viscosity for the given coating system, and the controls are able to properly monitor and mix the spray coating to the specified consistency. Additionally, built in heating systems can be used to pre-heat the substrate, resulting in an efficient and predictable dry time.
Air Pressure Settings in Manual Spray Guns
The air pressure setting on spray guns is another hard to control variable, even by those experienced in the finishing industry. Many operators tend to increase the pressure, intuitively thinking this will result in reduced processing times. However, excess pressure can lead to significant overspray and material waste, while not resulting in faster throughput.
However, erring on the low side of pressure adjustments creates its own problems. Insufficient pressure in a given spray system can lead to a blotchy or otherwise uneven finish. By reducing the variability in the operating pressure of the spray system, more consistent results can be achieved while material waste is minimized.
Read More: Benefits of Automated Spray Coating Systems
The Overall Setup in Manual Spray Systems
The overall set up of manual systems can be cumbersome and lead to inconsistent results that may vary between operators or even piece to piece. The distance between the nozzle and workpiece, speed of the operator making a pass, and overlaps between passes are all factors which can easily lead to a large degree of variance.
Automated systems can help customers define these parameters according to the best practices for a given application, and easily repeat the process on subsequent jobs.
Automated spraying systems not only reduce the amount of labor required for a given job, but can significantly improve finishing results and consistency between parts. Multiple types of equipment are available to suit batch or continuous processing applications and for a range of throughput requirements.
Today’s systems can be scaled to any level of production and are capable of unprecedented versatility, opening up the market to finishers who specialize in high mix, low volume work. By automating spray equipment, finishers can streamline their operations and reduce the variance that results from inconsistencies in viscosity, substrate temperature, air pressure, and equipment set-up.