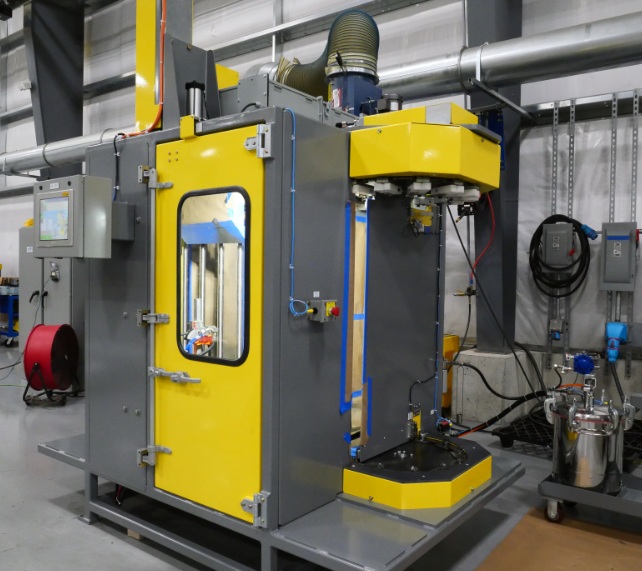
WHAT TO LOOK FOR IN AN ADHESIVE APPLICATION SYSTEM
Adhesive application systems represent a significant investment, and poor choices can lead to wasted materials, production delays, and inconsistent quality. These issues directly impact manufacturing costs and delivery schedules.
However, the right adhesive system is just the beginning—a partnership forged with the manufacturer will shape your long-term success. This is important because a well-matched system ensures compatibility with your substrate materials and meets your production requirements.
Read on to learn the essential criteria for evaluating adhesive application systems and providers.
WHY APPLICATION-SPECIFIC SYSTEM SELECTION MATTERS
The right equipment significantly impacts both bond performance and production efficiency. Precise adhesive placement reduces costly material waste and ensures consistent product quality. A well-matched system delivers optimal bond strength and durability across your production run.
Your application system must perfectly match your substrate materials and production requirements. It ensures proper adhesion compatibility with plastic and metal surfaces and maintains consistent application patterns while meeting your specific production speeds and automation needs.
Beyond performance benefits, proper system selection enhances workplace safety and environmental compliance. The right system minimizes worker exposure to potentially hazardous materials through proper containment and application methods. It also helps your facility meet industry regulations, and achieve functional and aesthetic requirements for your products.
IMPORTANT SYSTEM REQUIREMENTS
Manufacturers must evaluate several critical factors when selecting an adhesive application system. These requirements confirm the chosen system will provide strong performance and meet current and future production needs.
Application method (e.g., spray, dispense, roll)
The right application method forms the foundation of an efficient adhesive system. Modern manufacturing requires systems to adapt to changing production demands and handle diverse coating materials. Advanced application methods like spraying, dispensing, and rolling offer flexibility for different product designs.
The ultimate goal(s) should determine the final application method choice. The system must support anticipated production volumes and maintain consistent quality standards. Coating technologies allow seamless upgrades as your requirements evolve and innovations emerge.
System Versatility
Manufacturing demands equipment that adapts to multiple production scenarios. The ideal solution accommodates different product types and yields uniform results. This adaptability helps manufacturers meet evolving market requirements.
Effective coating equipment features adjustable spray patterns, pressures, and flow rates for varying needs. Quick changeover capabilities enable rapid switches between product runs and material types. Multiple mounting options offer complete coverage for diverse part sizes and shapes.
Adhesive Material Compatibility
Material compatibility fundamentally impacts application success. The system must handle diverse adhesive types while delivering reliable performance standards. Each adhesive requires specific parameters for viscosity, flow rates, and curing methods.
Adhesive application systems excel at managing varying adhesive properties and chemical compositions. Equipment must achieve precise coverage through proper atomization and spray patterns. Advanced technology also incorporates safety features to manage environmental concerns and maintain clean operation protocols.
Throughput Capacity
Production speed affects every aspect of manufacturing success. The best system processes required volumes and upholds rigorous quality standards. Manufacturing lines must meet production deadlines and customer expectations.
High-performance equipment offers adjustable processing speeds for varying batch sizes and product types. Advanced spray technologies guarantee uniform coverage at elevated production rates. Multiple spray heads and efficient nozzle designs eliminate bottlenecks while preserving coating integrity.
Maintenance Requirements
Regular maintenance keeps application equipment running at peak performance. Accessibility to key components reduces downtime and ensures smooth operation. Simple maintenance procedures help operators sustain quality standards.
Modern designs include easy-access panels and quick-change components for essential servicing. Built-in diagnostic tools detect potential issues before they cause production delays. Clear maintenance schedules and readily available parts minimize costly repairs and unexpected downtimes.
Production Line Integration
Manufacturing success depends on smooth workflow between all production components. A new adhesive system must match current conveyor speeds and material handling processes. Proper integration ensures consistent production rates without bottlenecks.
The machinery footprint must fit available floor space without disrupting existing operations. Compatible control systems allow seamless communication between production stages and flexible mounting options accommodate various part sizes.
HOW TO FIND THE RIGHT SYSTEM MANUFACTURER
You might wonder “What to look for in an adhesive application system builder?” The right partner should demonstrate the ability to deliver immense value throughout the lifespan of the equipment.
Here are several essential considerations that will allow you to make a more informed decision:
Expertise in Adhesive Technology
Success in adhesive applications hinges on a deep technical understanding. Expert manufacturers combine knowledge of material properties, curing methods, and chemical compatibility to deliver optimal bonding solutions. This expertise enables them to evaluate production environments and recommend precisely engineered systems for each application.
The most qualified manufacturers demonstrate mastery across diverse substrates and application methods. They maintain rigorous testing facilities to validate material performance and develop solutions for challenging production requirements. By integrating coating technology expertise with automation capabilities, these builders optimize both equipment reliability and operational efficiency.
Comprehensive Training
Manufacturing teams need thorough education to maximize equipment performance. The best builders give hands-on instruction to operators and maintenance staff. Each training program should cover setup, safety, daily operation, and troubleshooting methods.
A quality manufacturer includes clear documentation and online learning resources for continued education. Regular refresher courses help teams stay current with best practices and system updates. Effective training programs reduce errors while improving production quality and equipment lifespan.
Customer Support Excellence
Long-term manufacturing success requires dedicated support from equipment providers. A quality builder delivers comprehensive consultation throughout the selection and installation process. Each support interaction should demonstrate commitment to system performance.
The best manufacturers provide rapid response times and clear documentation for operational needs. Their service teams offer scheduled maintenance visits and proactive system optimization recommendations. Regular software updates and readily available spare parts minimize costly production delays.
Ongoing Technical Assistance
Manufacturing success depends on reliable access to expert technical support. Dedicated service teams ensure rapid solutions for production challenges. Round-the-clock assistance supports uninterrupted system operation.
Quality manufacturers provide multiple support channels for technical questions and emergencies. Their service programs include regular system checkups and process optimization recommendations. Timely software updates and easy access to replacement parts help prevent production delays.
YOUR PARTNER IN ADHESIVE APPLICATION SYSTEMS
Arnold Machine brings decades of proven expertise in building custom adhesive application systems. Our comprehensive approach combines technical excellence with dedicated customer support through every phase of your project. Contact our team today to explore how we can optimize your adhesive application process.