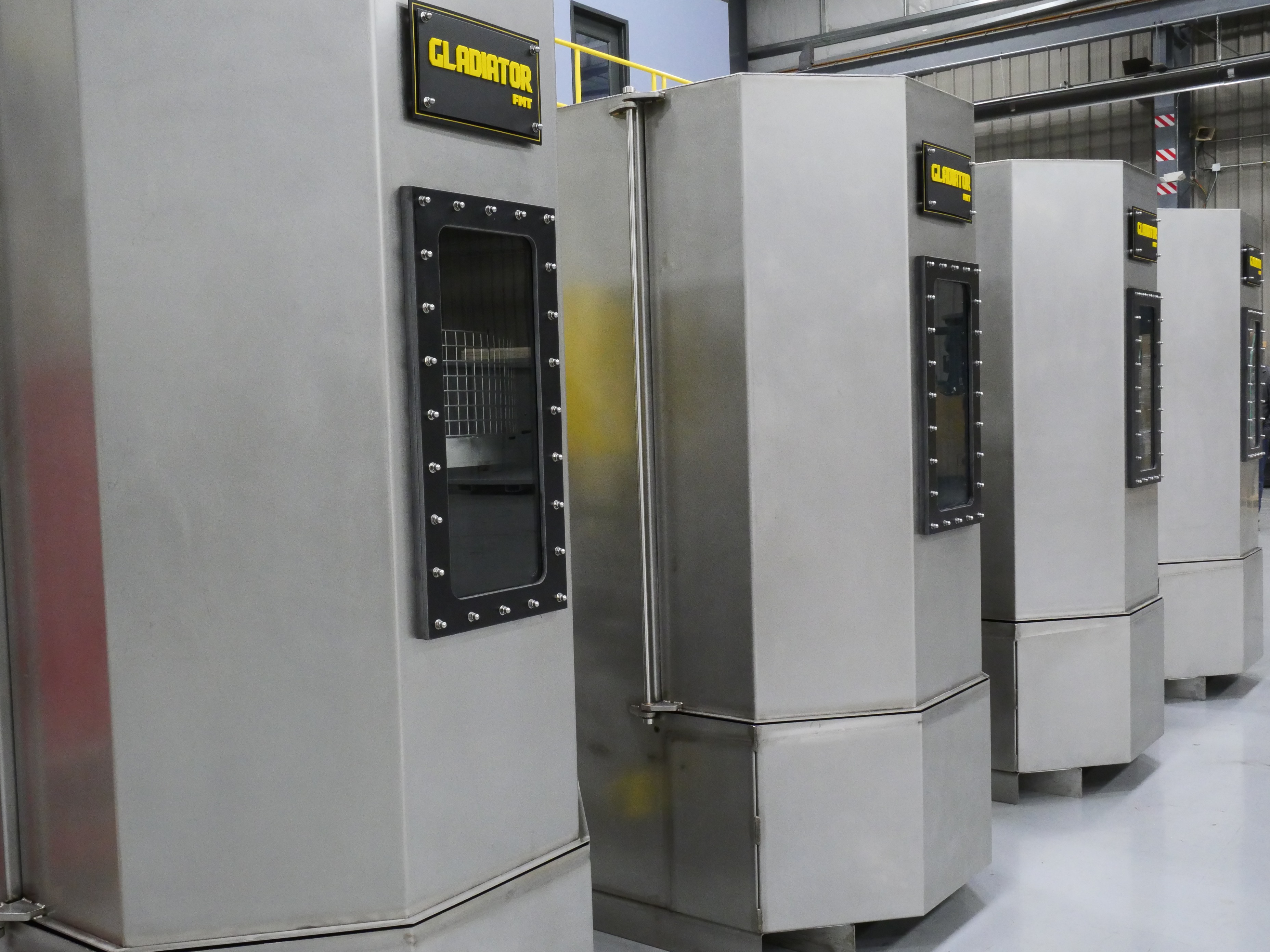
Automated Parts Washers: The Safest Way to Clean Parts
Going from manual washing to using a parts washer in transit authority repair centers.
Manual parts washing exposes transit workers to significant safety risks. Toxic chemicals and cumbersome equipment take a toll on long-term health and well-being. These hazards ultimately drain agency resources through medical costs, absences, and turnover.
Automated parts washing systems provide a safer solution compared to manual washing. They eliminate direct contact with hazardous chemicals that threaten worker health and safety.
Read on to learn how automated parts washers for transit authorities improve employee safety.
HAZARDS OF MANUAL WASHING
Solvents like gasoline and degreasers used in manual parts washing contain toxic chemicals. Repeated skin contact or fume inhalation can lead to health issues like respiratory illness, organ damage, and cancer.
The sharp scrapers and brushes that remove dried grease can slip out of workers' hands and cause deep lacerations. The manual cleaning process also involves repetitive lifting that strains muscles, tendons, and joints over time.
The health and safety hazards of manual washing processes have cascading adverse impacts. Providing additional safety training and precautions cannot fully protect staff against the intrinsic risks involved.
Unlike some competitors, Arnold’s parts washers do not use chemical solvents to clean equipment. Our aqueous-based solution is much safer for both your parts and your employees.
Automated washing systems are the only way to remove the hazards and their detrimental effects. With automation, worker health, retention, and productivity see marked improvements.
Read More: Benefits of a Parts Washer vs. Manual Cleaning Methods
HOW AUTOMATION IMPROVES SAFETY
Automated washers improve safety because they isolate workers from hazardous chemicals and materials. Parts get loaded into a sealed chamber, sprayed with a safe aqueous-based cleaning solution, and scrubbed clean - all without worker involvement. This eliminates the risks of direct contact with dangerous substances.
This video shows how safely an employee can run an Arnold Machine Gladiator FRT automated parts washer.
Advanced sensors and programming allow you to fine-tune the wash process for optimal results. Adjustable cycles, specialized nozzles, and intelligent soap metering provide customizable cleaning while maintaining employee safety.
BOOSTING PRODUCTIVITY
By automating washing tasks, you eliminate the hand and arm strains often arising from repetitive scrubbing motions and the lifting of heavy machinery. With less downtime needed for recovery, employee attendance records improve.
Workers can then optimize their time on critical tasks like inspections, repairs, and preventative maintenance. Additionally, vehicles undergo more regular servicing, which results in fewer unexpected breakdowns.
COST SAVINGS
Reduced employee injuries lead to significant cost savings for transit agencies by lowering costs associated with medical claims, worker's compensation, and lawsuits. Insurance premiums often decrease as well with improved safety protocols.
Experienced employees represent a crucial asset lost when turnover results from workplace hazards. Retaining skilled workers avoids replacement and retraining costs. Healthy and engaged workers also deliver higher productivity over their tenure.
IMPROVING WORKPLACE CULTURE
Manual washing processes create a workplace culture of danger and risk. Workers understandably develop negative associations with maintenance duties. Automation removes the most hazardous tasks from daily routines. This cultural shift leads to greater employee satisfaction, engagement, and morale.
With reduced focus on safety incidents, management attention shifts to more strategic priorities. Resources go towards maximizing asset utilization and improving rider services. A collaborative environment focused on optimization takes hold across the organization.
ENSURING ONGOING SAFE OPERATION
Proper maintenance and training are vital to the safe performance of automated parts washers. Check regularly that internal components like chip baskets and filter bags are free of obstruction and buildup.
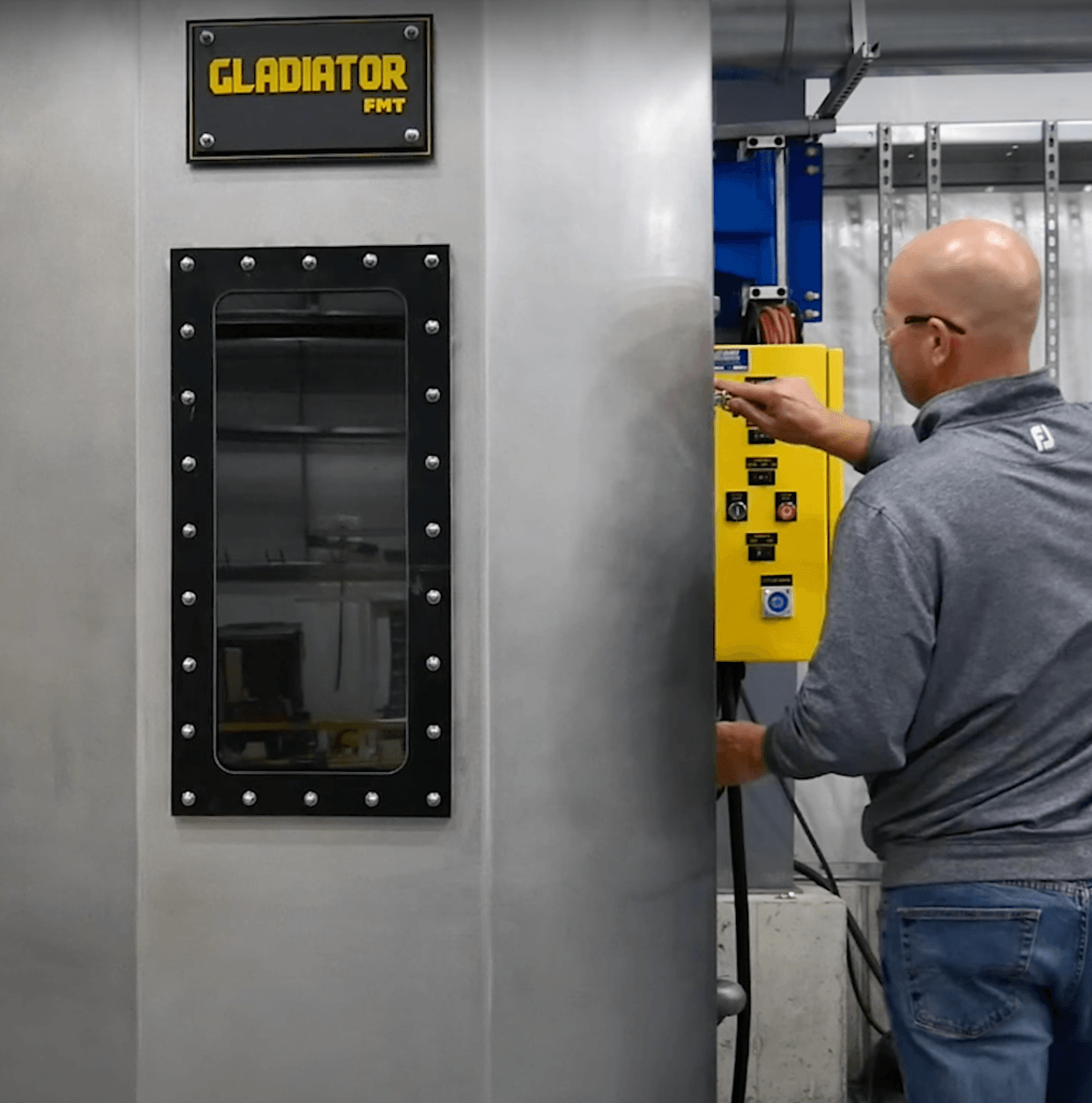
Follow the equipment provider’s recommended schedule for servicing moving parts and replacing worn items. A reputable manufacturer will train technicians on proper operation, maintenance, and troubleshooting. Periodically refresh training to accommodate staff turnover.
Automated systems are designed to be low maintenance when correctly cared for. But regular attention by trained staff is vital to avoid safety issues. Monitor worn items closely and replace them as needed to ensure your washer is running safely and smoothly.
HOW TO CHOOSE THE RIGHT MANUFACTURER
Choosing a reputable manufacturer for your automated parts washer will deliver more than just reliable equipment. The ideal partner understands your operation's needs and will customize solutions just for you, unlocking additional benefits that boost efficiency and safety.
Seek a manufacturer that customizes automated washers based on your workspace needs. They should tailor the wash cycles, dimensions, and features to match your requirements. Customized machines improve performance beyond one-size-fits-all models. Make sure they also provide solid warranties and ongoing support.
At Arnold Machine, we have decades of experience building automated washers for the automotive, heavy equipment and transit industries. We work closely with our clients to design customized washers that enhance safety and efficiency across maintenance workflows.
WHICH PARTS WASHER IS RIGHT FOR YOUR FACILITY?
Automating the hazardous manual washing process substantially improves worker safety. This protects transit agencies from injuries, absences, and turnover costs. Workers can instead apply their skills to more strategic maintenance tasks.
Click below to discover how to select the right parts washer for your operations.