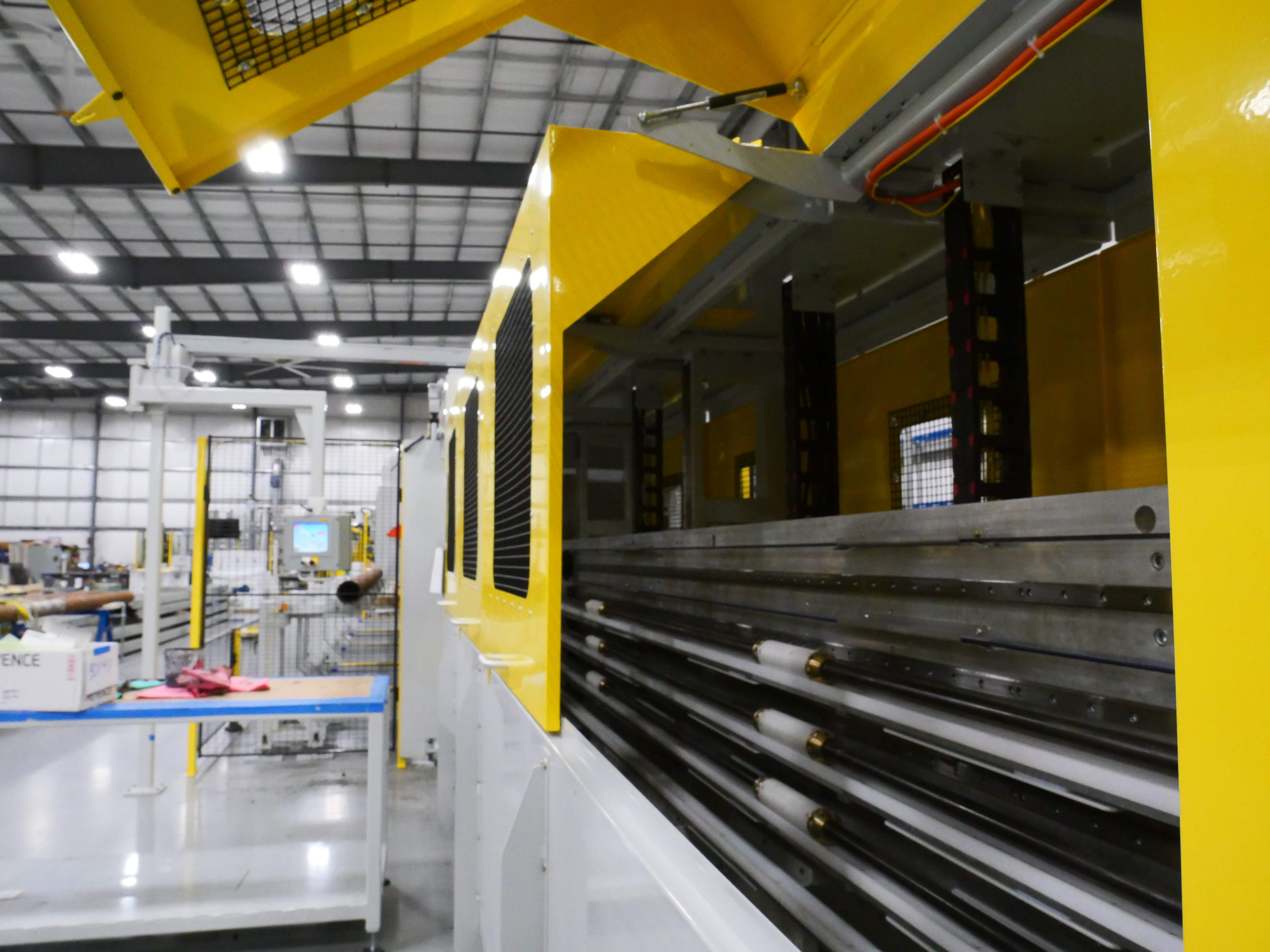
Increasing Capacity & Savings with an Automated ID Tube Spray System
Drilling Equipment Manufacturer Increases Capacity 6x with Automated Spray System
Many of the components used to extract oil and gas are used in harsh service environments. Drilling equipment is expensive and difficult to repair or replace in the field. That puts pressure on the firms who manufacture these critical assets to ensure they can stand up to abusive applications for years at a time.
Our customer, a major global equipment manufacturer, was feeling that pressure. An existing process for applying adhesive to the inside diameter of down-hole tubes was slow, wasteful and risky. They needed to reduce delays in manufacturing, increase production capacity and eliminate worker safety hazards.
Below, read how our process helped this customer integrate an automated spray system that made them six times more productive.
CHALLENGE: An imprecise, wasteful process
The down-hole tubes our client manufactures reach 25 feet long and can weigh up to two tons. The insides of the tubes must be coated in adhesive so that rubber molded to the inside of the tube adheres to the metal.
Because adhesion of the rubber to the tube is so critical to the part’s end use, workers had to ensure the adhesive they applied to the tube achieved a consistent dry film thickness (DFT) of between one and two mils.
But the adhesive application method made it almost impossible to achieve consistent results.
Here’s a rundown of the original process:
- Tube sections were hoisted up and then positioned at a 45-degree angle to the ground in a cradle.
- Workers climbed onto a mezzanine to access the high end of the tube and manually poured a base coat of adhesive into it.
- The tube was rotated during pouring to achieve more complete adhesive coverage.
- Next, the tube was left to dry in ambient air before the process was repeated for a topcoat.
Our customer wanted to overhaul the process for several reasons.
First, only around 50% of the adhesive poured down each tube stuck to its inner surface and the rest dripped out the bottom. At $50 to $100 a gallon, the cost of wasted adhesive added up quickly.
Second, quality tests routinely showed higher DFT readings at the top of the tubes where the material was poured. By pouring adhesive into the top of a rotating tube and relying on gravity to do the rest, the material kept running over itself before making its way further downward.
Third, climbing atop the mezzanine and pouring the volatile adhesive by hand posed worker safety risks.
Fourth, it took a long time for the adhesive to dry in ambient air. From first application of the base coat to final drying of the top coat, the process routinely took 12 hours.
Finally, the company had no way to test whether they’d achieved their target DFT other than by conducting destructive tests on completed tubes.
Our task was to develop an automated system that solved all five of those problems.
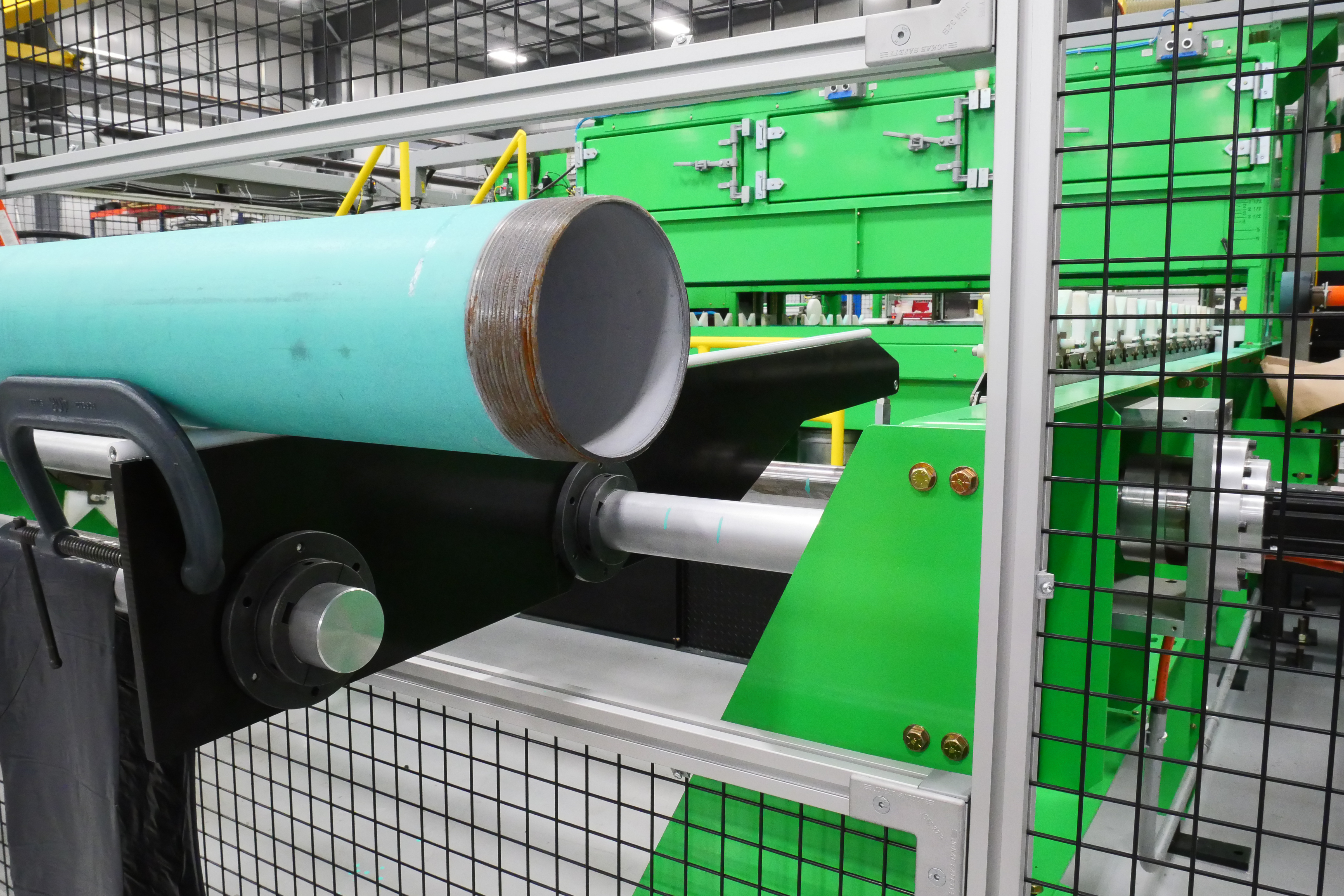
SOLUTION: A 5-stage automated ID tube spray system
Automated spray systems provide manufacturers many ways to save. The machine our engineers designed in this case turned adhesive application on the down-hole tubes from partly vertical to totally horizontal. Here’s how the five-stage process works:
Stage 1: The tube is heated in a preheated oven so that its surface temperature is consistent. Consistent surface temperatures prior to application promote better adhesion.
Stage 2: The tube is transferred to a spray booth. During application, a lance exits an adjacent lance booth and enters one end of the tube in the spray booth. Then, as the lance exits the tube, its nozzle sprays atomized adhesive into the inside surface of the tube. The tube rotates to achieve total coverage.
Stage 3: The tube moves into a base coat drying oven for a drying cycle.
Stage 4: The tube enters another spray booth and a topcoat of adhesive is applied in the same way as the second stage.
Stage 5: The topcoat dries in a drying oven just as in the third stage.
The system also included enclosed materials and adhesive mixing cabinets.
Integrating this automated system made an immediate impact.
First, by atomizing the adhesive rather than just pouring it, far less material was used. The cost savings was instant.
Second, the system features flow meters showing exactly how much material is applied. Operators now can verify that they’re achieving the required DFT in real time—no destructive tests necessary.
Third, hands-free application of adhesive and transfer of tubes from stage to stage means workers no longer need to climb on platforms or handle dangerous chemicals.
Fourth, the entire cycle now takes around two hours. Compared to the previous 12-hour cycle time, automation allowed our customer to do six times the work in the same amount of time.
Read More: Benefits of Automated Spray Coating Systems
Are you exploring automation?
Manufacturers committed to staying competitive know that the search for better, safer and more productive processes never ends. In our spray equipment case study collection, read how manufacturers integrated automated systems that resulted in significant production improvements.
Have you noticed production pitfalls in your facility that automation can address? Are you having a hard time visualizing a solution to a complex problem?
Let’s take a look together. Contact Arnold Machine now to discuss the challenge with our team.