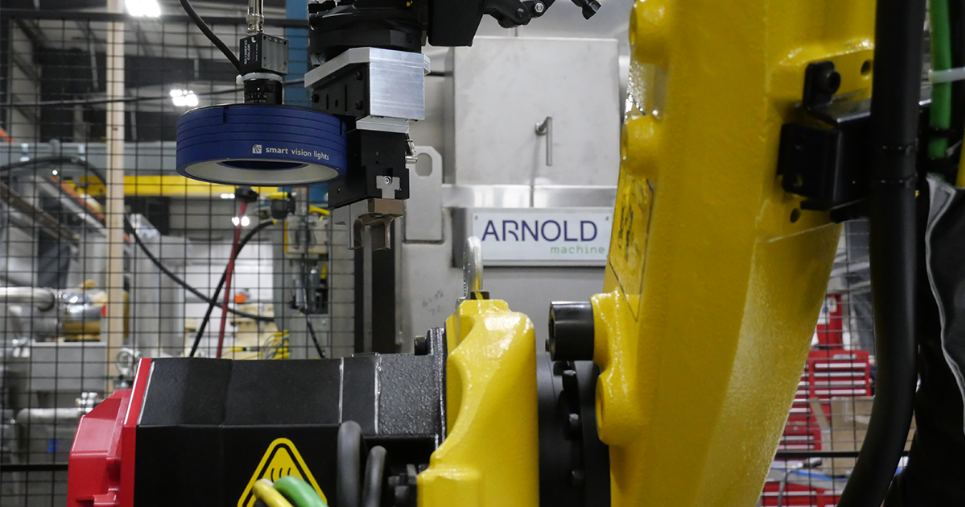
6 ADHESIVE SPRAYING EQUIPMENT PROBLEMS & SOLUTIONS
Adhesive spray equipment dramatically improves efficiency but can also cause several frustrating problems. Inconsistent processes, excessive waste, and decreased worker safety are just a few of the many common issues that plague these systems.
Automated solutions using advanced technology can resolve these adhesive spraying challenges. However, the downside is that this state-of-the-art equipment often comes with a hefty price tag.
Arnold Machine's specialized chain-on-edge equipment provides a comprehensive solution to these problems. Manufacturers can get this cutting-edge technology on their floors through our Machine-as-a-Service and avoid huge upfront costs.
Read on to learn more about the six spray equipment problems and how to solve them without a huge capital expenditure.
6 COMMON CHAIN-ON-EDGE SPRAYING MACHINE PROBLEMS
Optimizing chain-on-edge adhesive spray operations requires proactively addressing these six common problems.
1. Consistency Issues
Inconsistent setups and fluctuating operating conditions lead to defects and quality problems with adhesive spraying. This often requires rework and reduces yields. Operators must scrap or re-coat many parts, severely cutting into productivity and profit margins.
Variable part temperatures and inconsistent material viscosities are two other common consistency issues. These variabilities force operators to make numerous adjustments in pursuit of proper coating thickness and cure, significantly reducing efficiency.
2. Material Waste
Under-optimized equipment setups result in considerable material overspray and waste. Excess adhesive sprayed but not properly deposited on parts gets captured in filters and booth waste.
The overspray also leads to additional maintenance and cleaning requirements due to excessive adhesive buildup on fixtures and in the spray booth. The numerous expenses from material waste, cleaning, and maintenance quickly add up.
3. High Labor Costs
Substantial operator time spent on initial spray setup and subsequent changeovers contributes to high labor expenses. Personnel need to readjust multiple settings when switching between part types manually. This labor inefficiency also contributes to downtime between production jobs.
4. Safety Concerns
The high flammability and volatility of many sprayed adhesives pose severe health and safety hazards. Operators risk eye, nose, throat, and lung irritation. They may experience coughing, sneezing, shortness of breath, headaches, and dizziness from exposure to irritating and hazardous fumes and particulates.
5. Inconsistent Part Temperatures and Material Viscosities
Temperature fluctuations on incoming parts and material viscosity changes impede a consistent coating thickness and cure. This reduces efficiency and forces operators to readjust equipment settings to compensate frequently.
6. Significant Initial Investment
Acquiring state-of-the-art chain-on-edge adhesive spraying lines requires a major upfront capital investment. This financial burden can constrain the growth and adoption of the equipment. It can also prevent smaller companies from gaining a competitive edge.
CAUSES AND SOLUTIONS OF SPRAY EQUIPMENT PROBLEMS
Understanding the root causes of common chain-on-edge spraying issues allows for targeted problem-solving. Careful analysis reveals many addressable factors behind each problem.
Inconsistent Quality
Improper spray setups and uncontrolled variables cause inconsistent quality and rework. Standardizing procedures and environments stabilize processes. For example, documenting positional settings digitally establishes optimal baseline parameters.
Regulating temperatures through part preheating also minimizes variabilities. Programmable fluid and air pressure regulators additionally enable optimized and repeatable settings.
Excess Material Waste
Under-optimized fluid pressures and overspray lead to excessive material waste. Adjusting equipment settings and recirculating excess fluid reduces unnecessary loss. Introducing flow meters also improves cost visibility by quantifying actual material usage per part.
Huge Labor Costs
Manual equipment setups and changeovers drive up labor costs. Automating adjustments with programmable controllers cuts operator labor needs. Digitally storing positional settings further simplifies changeovers between product variants. Highly visible spray gun mount graduations enable consistent positioning as well.
Hazardous Conditions
Volatile adhesives and open system designs create hazards like fumes and fire risks. Enclosed ventilation with active monitoring and fire suppression protects operator safety. Strict PPE protocols also minimize exposure.
Temperature and Viscosity Fluctuations
Inconsistent temperatures and viscosities lead to uneven coatings. Monitoring and controlling environmental, part, and fluid conditions even out variabilities. Inline sensors give real-time viscosity and temperature data to guide automated adjustments. Preheat ovens additionally stabilize part temperatures.
Large Equipment Investments
Purchasing equipment demands significant upfront capital investment. Innovative models like Machine-as-a-Service (MaaS) offer flexible “pay-as-you-go” options that reduce financial barriers. This enables adoption without the costs and risks of ownership.
THE MACHINE-AS-A-SERVICE REVOLUTION
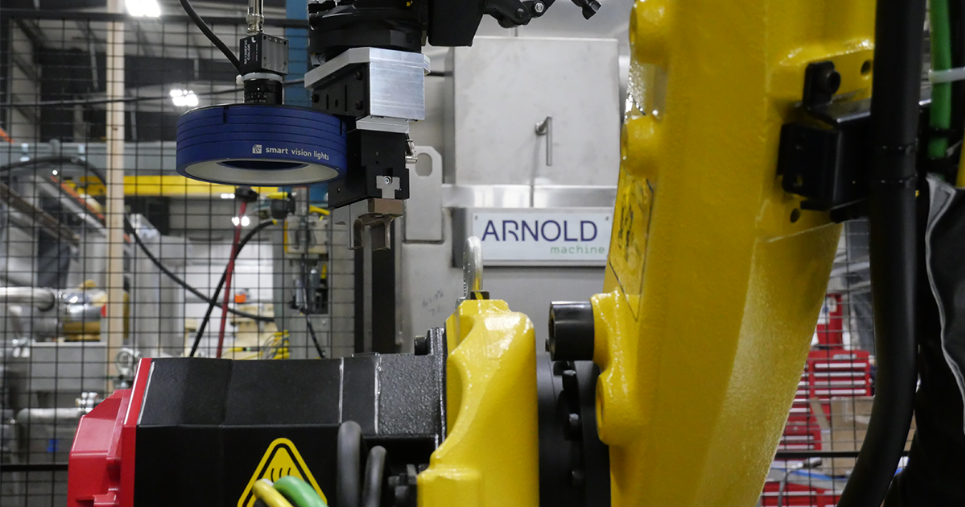
Arnold Machine offers a revolutionary Machine-as-a-Service solution that makes cutting-edge technology accessible to all manufacturers.
Rather than a large upfront capital expenditure, users only invest in installation and training. MaaS directly aligns costs with production needs through usage-based charges. It converts equipment acquisition into an operating expense rather than a capital expenditure.
Additional benefits of MaaS include gaining actionable performance insights to empower data-driven decisions. Proactive maintenance minimizes downtime risks. Companies also enjoy flexible engagement terms and instant access to upgrades.
The MaaS robotic solutions automatically control viscosity for adhesive spraying. This allows real-time adjustments to pressure and temperature based on viscosity data. It optimizes the spray application parameters on demand.
Arnold Machine provides end-to-end guidance and support with dedicated technical experts. This comprehensive assistance makes the MaaS model effective at removing growth barriers without major financial burdens.
ARNOLD MACHINE’S INNOVATIVE SOLUTIONS
Arnold Machine specializes in automated Chain-on-Edge spray systems that apply coatings precisely and consistently. Automation improves uniformity, reduces material waste, and provides significant labor savings compared to manual application.
Our coating systems control key variables like viscosity, temperature, and air pressure to optimize efficiency and quality. We automate positional setups to improve consistency between coated parts, streamlining operations for high-mix, low-volume clients.
Safety and process control are paramount in our designs. Our spray booths are fully enclosed to reduce solvent hazards. Recirculating fluid systems prevent line clogs. Integrated controls enable real-time monitoring and instant automated adjustments to viscosity and temperature.
Programmable regulators and preheat ovens directly address common adhesive spraying issues. Intelligent controls maintain optimal fluid and air settings between jobs, eliminating manual tweaking. Our chain-on-edge systems enable continuous processing at shorter cycles versus intermittent indexing, allowing more spindles to coat higher volumes flawlessly.
We tailor each automated spray system to the precise needs of our clients. This level of customization helps manufacturers refine and future-proof their adhesive coating processes by reducing labor, improving quality, and maximizing efficiency.
FUTURE-PROOF YOUR OPERATIONS WITH ARNOLD MACHINE
Adhesive spraying equipment shouldn’t hinder quality and efficiency. Arnold Machine’s Chain-on-Edge and MaaS systems resolve common spraying issues and address complex challenges.
Don’t let production problems, costs, and safety risks hinder your manufacturing operations. Click below to learn how our cutting-edge Chain-on-Edge machines will revolutionize your production processes like never before.
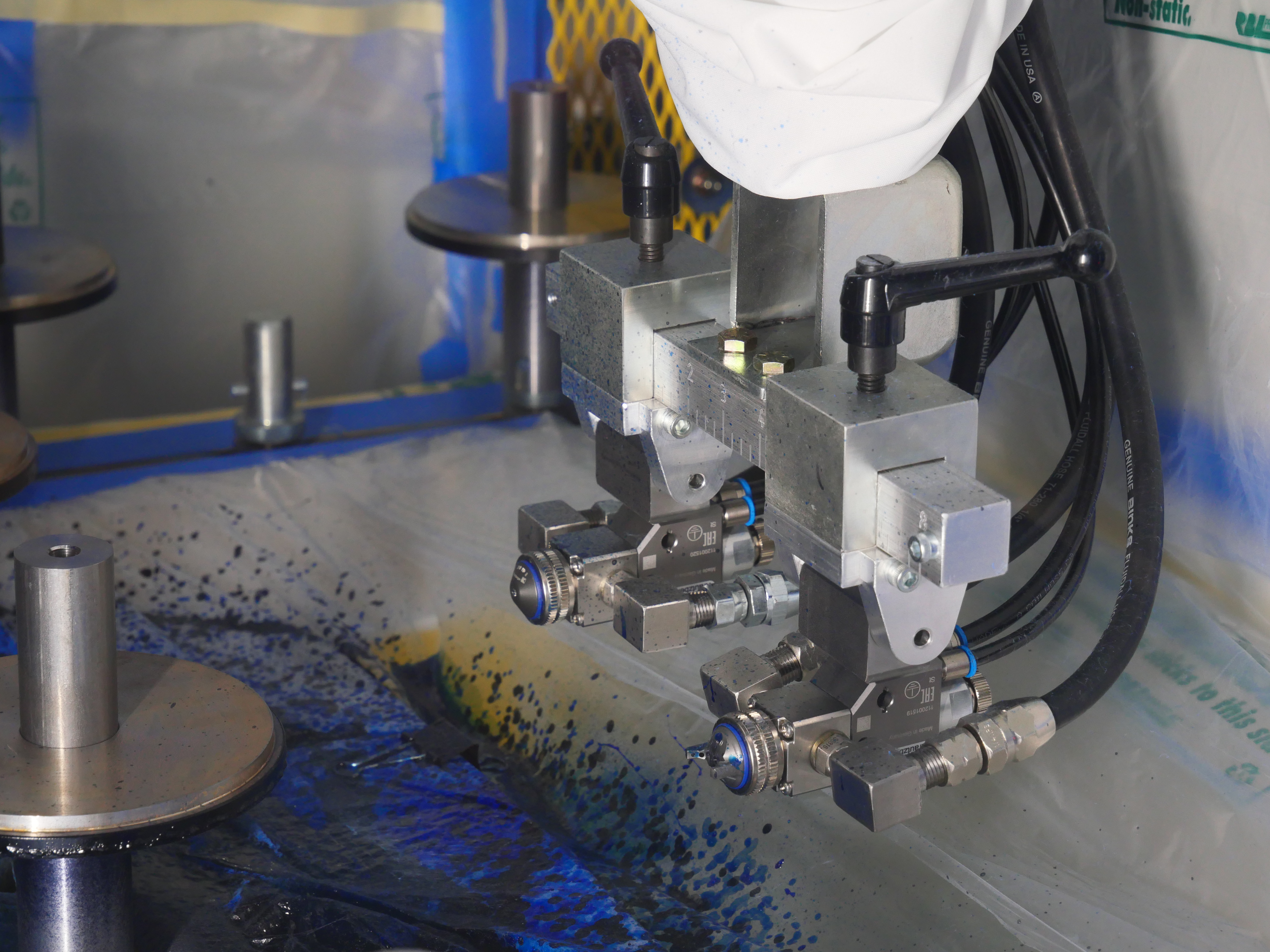