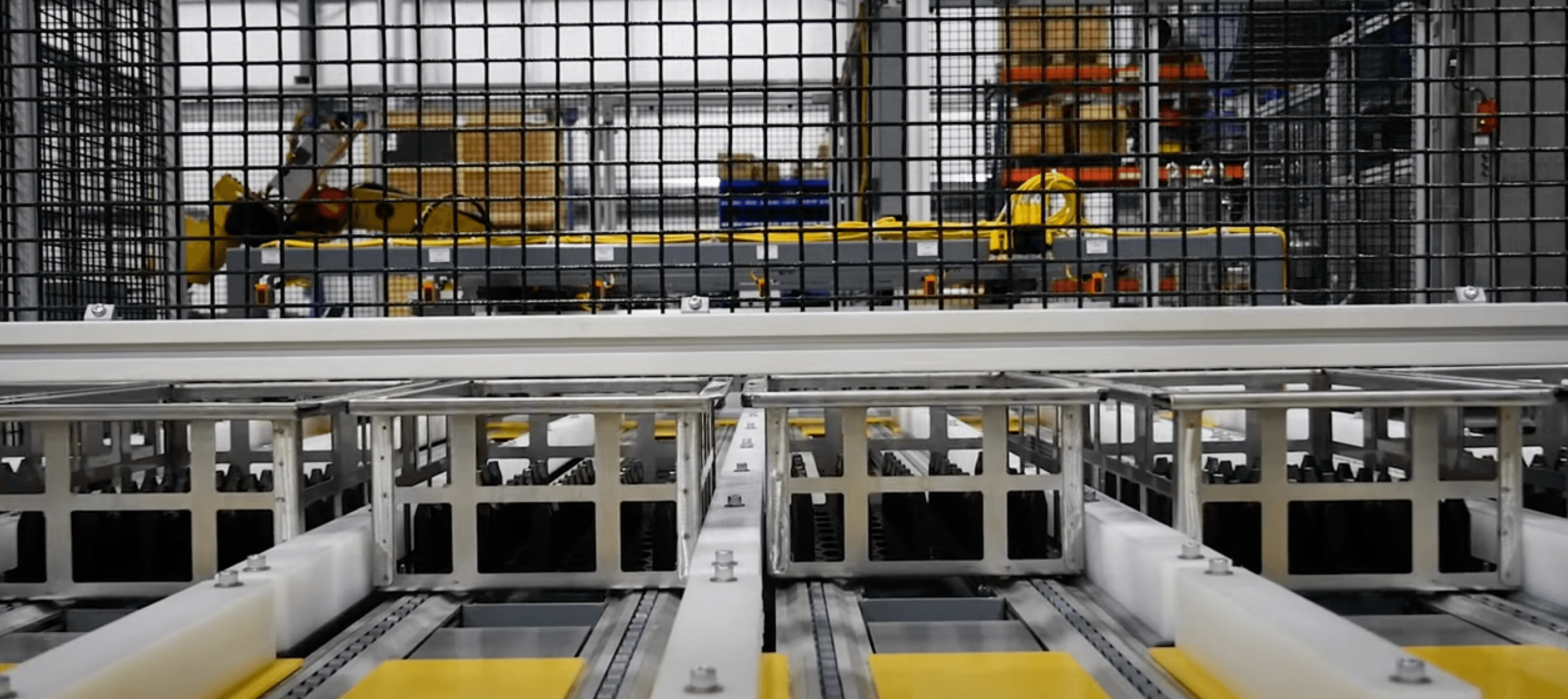
PARTIAL IMMERSION VS. FULL IMMERSION ROTARY BASKET WASHERS
Engineering managers know that rotary basket parts washers are essential for keeping their manufacturing processes running smoothly. Partial and full immersion are two methods to ensure efficient and consistent cleanliness.
Understanding the subtle yet impactful differences will allow you to make a more informed decision. Read on to learn which type of rotary basket washer is right for your production line.
PARTIAL IMMERSION VS. FULL IMMERSION PARTS WASHERS
Deciding between partial and full immersion washers requires careful consideration of your part sizes, shapes, and required cleanliness levels. These choices will directly influence the type of rotary basket washer you need.
Partial Immersion Rotary Basket Parts Washers: Ideal for Complex Parts
Choose partial immersion washers for parts with intricate designs or internal cavities. These washers use a dynamic cleaning process where solutions circulate and penetrate the parts for thorough cleaning.
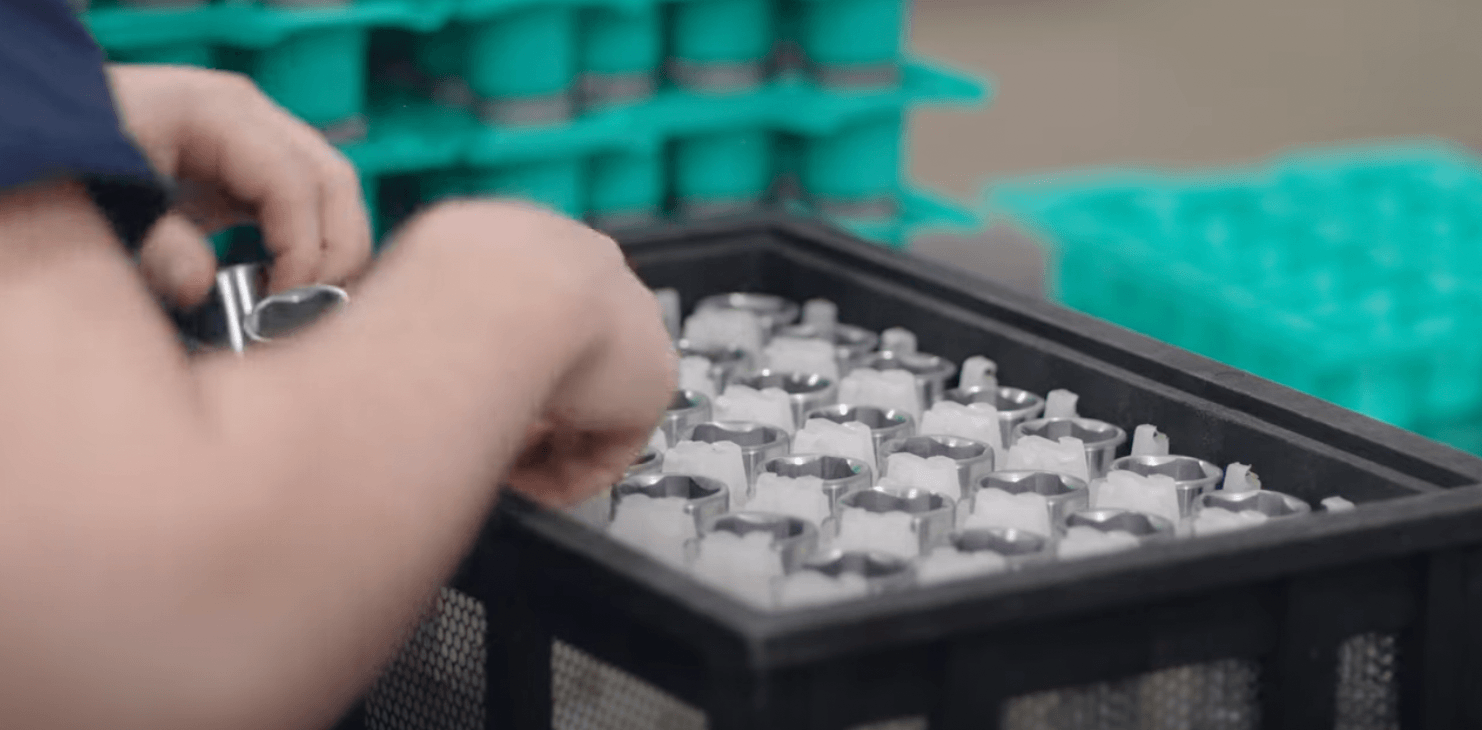
They are suitable for electronics and precision engineering industries. This is because they clean delicate components effectively. Adjustable flow rates and precision nozzles enhance their use for sensitive parts.
Full Immersion Rotary Basket Parts Washers: Best for Uniform and Heavily Soiled Parts
Full immersion washers are better for larger, uniformly shaped, or heavily soiled parts. They submerge parts fully in cleaning solutions. This method removes heavy grime and contaminants effectively. These washers are standard in the automotive and heavy machinery sectors. Their design includes high-capacity pumps and robust agitation systems.
Wash Duration Variability
The wash time for partial and full immersion rotary basket washers is usually similar. However, it can change depending on how complex the parts are and how much dirt is on them.
Due to their targeted cleaning process, partial immersion washers may require more time for detailed components. Full immersion washers typically have more consistent wash times, but heavily soiled parts may need extended cycles.
Handling of Contaminants
Partial immersion washers are well-suited for removing contaminants from intricate parts with complex geometries. They are particularly effective against light to medium contaminants such as dust, small particles, and oils that can be dislodged through targeted spray and circulation.
Full immersion washers are ideal for tackling heavier contaminants, such as large debris, thick grease, or stubborn residues. The full submersion allows consistent and thorough cleaning, which is crucial for parts with uniform contamination.
Environmental Impact Considerations
Partial immersion washers tend to be more environmentally friendly due to their efficient use of water and cleaning agents. Their targeted approach reduces waste and energy consumption. This makes them suitable for industries aiming to minimize their environmental footprint.
Full immersion washers typically require more water and energy. This leads to a higher environmental impact. However, technological advancements can help mitigate these effects through more efficient system designs and eco-friendly cleaning agents.
Understanding these additional aspects of each washer type provides a more comprehensive view. It helps engineering managers choose a washer that meets their immediate cleaning needs and aligns with their long-term operational goals and environmental responsibilities.
TABLE COMPARISON
Here's a simple comparison between partial and full immersion rotary basket washers to help engineering managers choose the best washer for their needs.
Feature/Aspect |
Partial Immersion Washers |
Full Immersion Washers |
Suitability |
Complex parts with internal cavities, delicate components |
Uniformly shaped parts, heavily soiled components |
Cleaning Method |
Dynamic process with solutions circulating and penetrating parts |
Complete submersion in cleaning solutions |
Ideal Industries |
Electronics, precision engineering, aerospace, medical device manufacturing |
Automotive, heavy machinery, general manufacturing |
Customization Options |
Adjustable flow rates, targeted spray nozzles, variable immersion depths, specialized agitation patterns |
High-capacity pumps, intense agitation systems, temperature controls, chemical treatment options |
Technical Specifications |
Precision spray nozzles, automated systems, multi-stage cleaning processes, custom fixtures |
Similar technical specs with variations in pump strength, tank size, and control systems to accommodate full immersion |
Operational Focus |
Targeted cleaning, enhanced precision for sensitive parts |
Uniform and thorough cleaning of larger, more robust parts |
Environmental Considerations |
Energy-efficient operations, adaptable to specific cleaning requirements |
Potentially higher water and energy usage due to full immersion needs |
TECHNICAL SPECIFICATIONS AND CUSTOM FEATURES
At Arnold Machine, we have decades of experience manufacturing high-performance industrial parts washers. This includes designing custom fixtures and integrating advanced automation features such as robotics.
We've successfully implemented solutions in a wide variety of industries over the past few decades. Our commitment to innovation and quality makes us a trusted partner for all industrial parts cleaning needs.
Core Technical Specifications
At the heart of our rotary basket washers are robust technical specifications designed to meet diverse industrial requirements:
- Load Capacity and Solution Tank Size: Tailored to handle different part sizes, ensuring versatility in cleaning applications.
- Pump Strength and Efficiency: Engineered for optimal cleaning effectiveness with energy-efficient operation.
- Control Systems: Advanced control systems like Allen Bradley PLC & HMI offer precise operational control. They can be customized to specific process requirements.
Customization and Special Features
Our washers build on a strong technical foundation and include special features and customization options:
- Precision Spray Nozzles: Customizable to target specific areas of parts for thorough cleaning.
- Automated Systems: Enhance productivity and integrate seamlessly with existing production lines. This offers flexibility in automation levels based on your needs.
- Multi-Stage Cleaning Processes: Configurable for complex cleaning requirements. This ensures that each stage of the washing process is optimized for the parts being cleaned.
- Custom Fixtures: Designed to accommodate unique part geometries for efficient and effective specialized component cleaning.
Enhanced User Experience
- Soundproofing and Build Quality: Our focus on soundproofing and high-quality welded pipe joints ensures a durable, user-friendly, and noise-minimized operation environment.
- Integrating Technical Specifications With Customizable Features: Underlines the adaptability of Arnold Machine’s rotary basket washers. They work well for both large and heavy parts and sensitive components.
REAL-WORLD EXAMPLE: ARNOLD MACHINE’S CUSTOM SOLUTION
A client in the heavy parts manufacturing sector presented Arnold Machine with a unique challenge. They needed a washer to handle specific cleaning requirements.
We designed and built a customized 8RB50 partial immersion rotary basket washer. This solution focused on efficient cleaning and integrated smoothly with the client's production line.
The 8RB50's design showcased the flexibility of partial immersion washers in handling unique industrial needs. Our customization expertise allowed us to meet the client's specifications.
This real-world example demonstrates the adaptability of partial immersion washers. Such washers can be tailored for specific applications where standard models might not suffice.
Check out the video below that shows an 8RB50 in action.
HIGH-QUALITY ROTARY BASKET PARTS WASHERS
Arnold Machine is your go-to source for high-performance rotary basket cleaning solutions. We specialize in custom-designing efficient and durable rotary basket washers to meet your unique industrial cleaning requirements.
Click below to explore our rotary basket washers and discover why more manufacturers trust Arnold Machine to wash their parts.