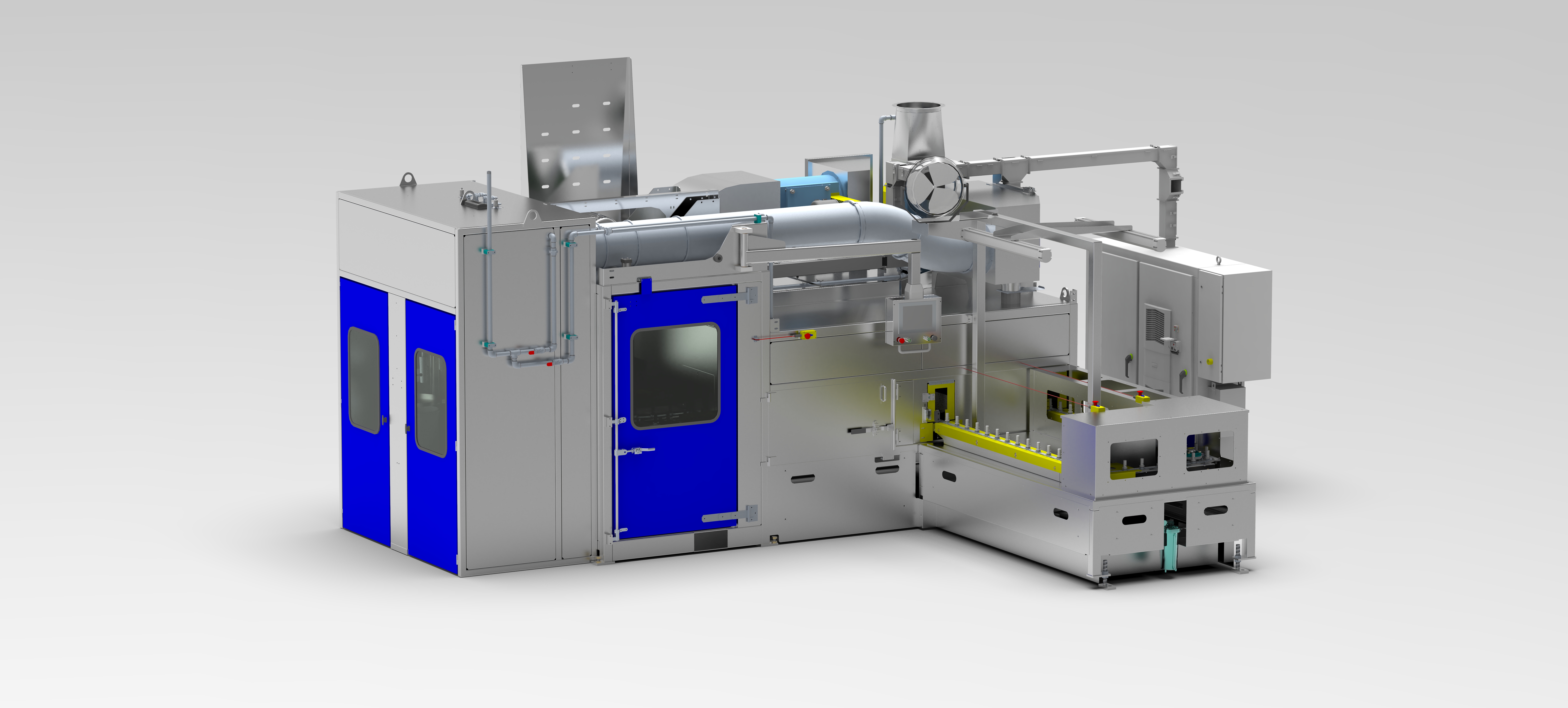
Cost of Automated Spray Coating Systems
Many manufacturers struggle with inefficient coating processes, inconsistent quality, and high labor costs. These issues can hinder productivity and profitability. Finding an effective solution to address these pain points is often difficult.
Automated spray coating systems can revolutionize your production line by offering advanced solutions tailored to your needs. These systems streamline operations and provide significant financial advantages.
Read on to learn more about the cost of spray coating automation and the value it adds to your operations.
AUTOMATED SPRAY COATING SYSTEM BENEFITS
Adding an automated spray coating system to your production floor offers numerous advantages, including:
Improved Transfer Efficiency: Advanced technologies ensure precise coating application. This reduces wastage and enhances material usage.
Enhanced Quality Control: Consistent and uniform application minimizes defects and produces high-quality finishes.
Increased Throughput: Higher production rates reduce lead times and improve response to customer demands.
Customized Solutions: Tailored configurations meet specific production needs and enable coating various parts and materials.
Automated spray coating systems optimize existing processes and open up new opportunities for innovation and growth. They enable manufacturers to stay competitive in a rapidly evolving market.
INITIAL INVESTMENT
The cost of automated spray coating systems varies significantly based on several factors:
- System complexity
- Part size
- Desired throughput rate
- Customization requirements
- Number of material coats
- Precision needs
- Integration with other equipment
Providing a precise cost without specific details is challenging. However, here are some rough estimates:
- A mid-range system for small to medium-sized production facilities: $250,000 to $450,000
- More advanced systems with higher throughput and additional features: $750,000 or more
- Overall cost range: Several hundred thousand to millions of dollars, depending on project scale and requirements
Additional features such as robotic integration, conveyor systems, curing equipment, and control software can substantially increase prices. Customized features or special requirements will also add to the overall cost.
INSTALLATION COSTS
Installation costs range from $10,000 to $100,000, depending on system size, complexity, facility layout, and location. It's important to note that more complex and customized cells with multiple robots and advanced features could cost even more.
Impact of the Painting Process
Different painting processes, such as spray painting, roll coating, or submersible coating, require unique equipment and setup. These variations significantly influence the final installation price. For example, a submersible coating system might require different facility modifications than a spray painting system.
Customization and Facility Factors
Customization needs, such as specialized fixtures or production line integration, will increase expenses. Facility layout, utilities (compressed air, electricity), and structural or ventilation modifications also affect the final price. Environmental and safety compliance often necessitates additional equipment, permits, and training.
Location and Logistics
Location influences installation costs due to shipping, travel expenses for installation technicians, and labor rates. These factors can significantly affect the total installation budget and should be carefully considered when implementing an automated spray coating system.
Getting an Accurate Estimate
Given these variables, providing a precise cost without specific details about the painting cell's requirements is challenging. However, the range mentioned above provides a general guideline for budgeting purposes.
TRAINING COSTS
Implementing automated spray coating systems requires comprehensive operator training. This covers system operation, part handling, maintenance, troubleshooting, and safety protocols. The program's length and depth depend on the system's complexity and the operators' prior experience.
Safety training is crucial and covers topics like hazardous material handling, personal protective equipment (PPE) use, and emergency procedures. Some customers opt for advanced training programs for specialized coating techniques or system optimization.
Training costs vary based on duration, trainer expertise, location, and customized materials. Comprehensive training maximizes ROI through safe operation, optimal performance, and efficient equipment use. This investment enhances long-term system value.
INITIAL INVESTMENT VS. LONG-TERM BENEFITS
Automated spray coating systems deliver exceptional value over time. While a typical system might require a significant initial investment, the long-term financial rewards quickly outweigh these costs.
For example, a system costing $400,000 can generate substantial annual savings through increased efficiency, reduced labor costs, and minimized material waste. Key factors leading to positive ROI include:
- Reduced Labor Costs: Automated systems minimize manual intervention, cutting labor expenses significantly.
- Minimized Material Wastage: Precision application technology ensures efficient material use, reducing wastage.
- Enhanced Productivity: Continuous operation of automated systems boosts throughput and enables efficient order fulfillment.
A case study involving a tier 1 automotive supplier demonstrates the potential ROI. They implemented an automated coating system and experienced a 40% reduction in reject rates and a 30% increase in production throughput. This resulted in an annual savings of $250,000 and an additional revenue boost of $700,000. The system paid for itself within the second year of implementation.
Additionally, a global leader in polyurethane product manufacturing significantly improved their operations by adopting an automated adhesive coating system. The company used manual processes that caused material waste and low efficiency. They saw notable enhancements after switching to automation.
The new system ensured consistent coating thickness and quality, reduced rejection rates, and increased production throughput by 20%. Automation reduced manual intervention and enabled continuous operation, greatly boosting productivity.
Long-Term Financial Benefits
Beyond direct cost savings, these systems consistently enhance product quality. Higher quality products can command better prices and attract more customers. The increased production capacity also enables businesses to handle larger orders and diversify their product offerings.
While the initial investment may seem substantial, the long-term benefits and ROI make automated spray coating systems a financially sound decision for businesses aiming to optimize efficiency and profitability.
PRIMARY FACTORS LEADING TO POSITIVE ROI
- Reduced Labor Costs: Automated systems minimize manual intervention, cutting labor expenses significantly.
- Minimized Material Wastage: Precision application technology ensures efficient material use, reducing wastage.
- Enhanced Productivity: Continuous operation of automated systems boosts throughput and enables efficient order fulfillment.
These three factors combine to deliver substantial long-term financial benefits. Automated spray coating systems are a wise investment for businesses looking to improve their ROI.
TOTAL COST OF OWNERSHIP
Evaluating the Total Cost of Ownership (TCO) is crucial when considering automated spray coating systems. This includes operational and maintenance costs beyond the initial purchase and installation.
Operational Costs
Operational costs encompass energy consumption (electricity, air, gas), coating materials (adhesives, primers, solvents), and labor for system oversight. Energy consumption will depend on the system's size, operation duration, and equipment efficiency. While automated systems reduce manual labor, skilled technicians are still needed to operate and maintain the equipment, monitor the coating process, and troubleshoot any issues.
Maintenance Expenses
Maintenance expenses include routine inspections, cleaning, lubrication, and replacement of worn parts. Unexpected breakdowns may occur, requiring repairs and potentially causing downtime. Regular maintenance ensures the system's longevity and optimal performance.
Depreciation
Automated coating systems are capital investments that depreciate over time. Calculating depreciation expense is essential for accurately assessing TCO and determining the system's economic life.
Additional TCO Factors
Additional TCO factors include ongoing training and regulation compliance. The cost of coating materials will depend on the type of coating being applied, the quality of the materials, and the production volume. By considering all these factors, businesses can understand the actual cost of owning and operating an automated spray coating system over its lifetime.
MAXIMIZING ROI WITH AUTOMATED SPRAY COATING SYSTEMS
Automated spray coating systems offer significant long-term benefits that outweigh initial costs. These systems improve efficiency, reduce waste, enhance quality, and boost productivity, leading to solid ROI.
As experts in automated spray coating systems, Arnold Machine understands each business's unique needs. We can help you navigate costs and benefits, ensuring you make an informed decision aligned with your business goals.
Click below to learn more about our innovative spray coating systems.