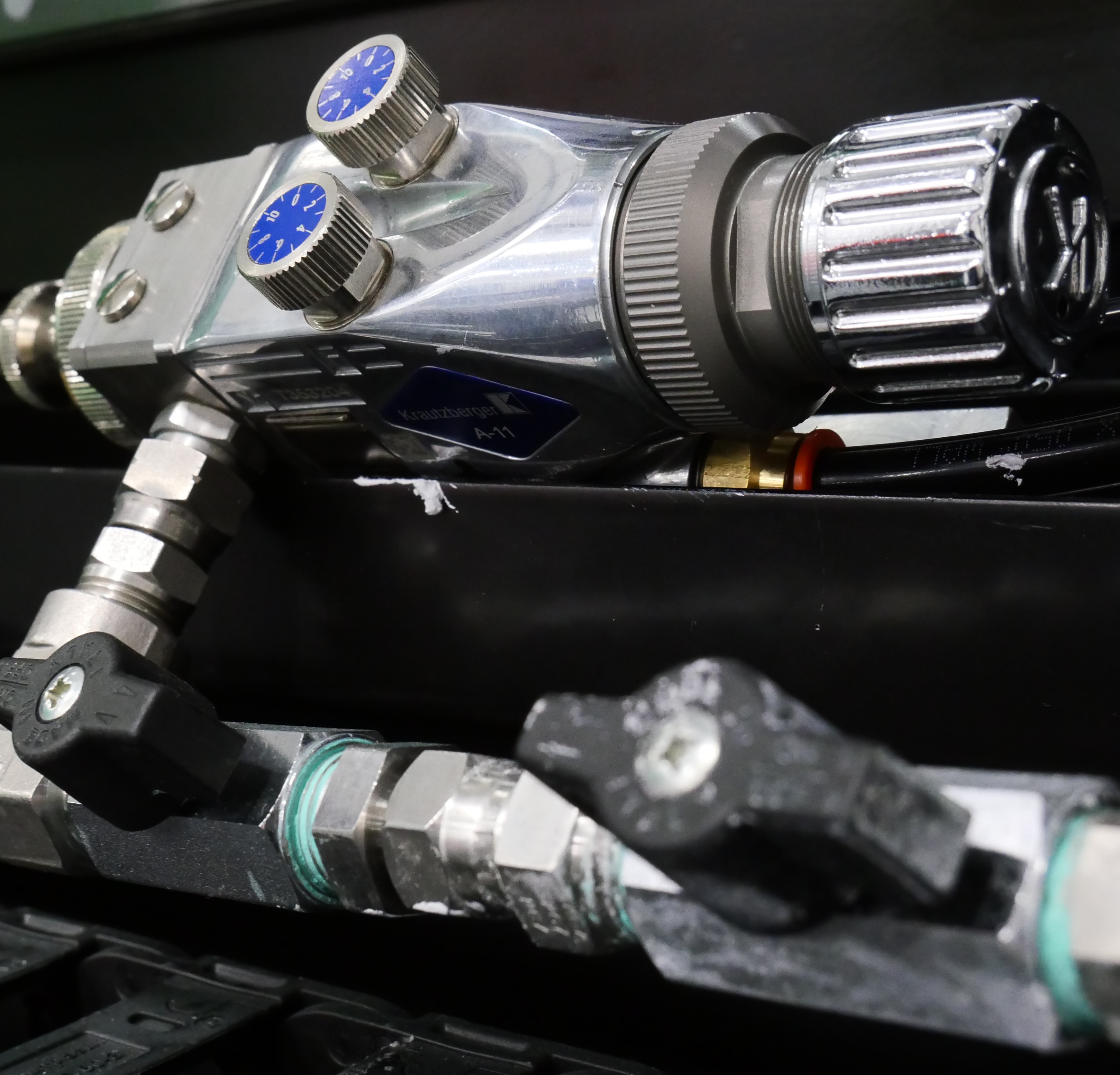
BEST COATING SYSTEM FOR AUTOMOTIVE ANTI-VIBRATION COMPONENTS
Ensuring the durability and performance of anti-vibration components is a critical task for automotive manufacturers. These parts must endure extreme conditions and frequent exposure to harsh chemicals. Finding viable options that balance quality, efficiency, and cost-effectiveness is a constant struggle.
Coating systems improve the lifespan of components by creating durable bonds between materials. They offer a reliable way to deliver long-lasting performance and protection. Read on to learn more about the best coating system for automotive parts.
THE CRITICAL ROLE OF COATING SYSTEMS
The coating process enhances durability and performance by creating a strong, reliable bond between metal and rubber materials. This bond prevents delamination under stress and makes sure the component remains intact during operation.
Arnold Machine’s automated coating systems are tailored to meet specific customer needs, ensuring consistent results and reducing manual input. These systems streamline production, improve quality, and allow manufacturers to handle complex parts easily.
Coating parts also help protect against corrosion, wear, and chemical exposure. Specialized machines, such as chain-on-edge conveyors, optimize the process and apply the adhesive precisely. This delivers quality, improves structural integrity, and increases long-term performance under various conditions.
CHAIN-ON-EDGE CONVEYORS: PRECISION COATING FOR COMPLEX COMPONENTS
Chain-on-edge conveyor systems from Arnold Machine precisely handle complex automotive components for a uniform coating on every surface. These turnkey solutions integrate seamlessly into existing production lines, improving efficiency and reducing downtime. Real-time monitoring allows operators to make on-the-fly adjustments to maintain high-quality control.
High-performance adhesives are expensive, so minimizing waste is a top priority. The chain-on-edge system excels in this area with real-time monitoring and a specialized application method that adjusts the coating to each component's exact needs.
This system offers great control for parts with complex shapes and specific adhesive needs. It ensures the coating bonds properly and maximizes adhesive performance while minimizing material waste, resulting in significant cost savings and improved product quality.
A user-friendly HMI interface lets operators store and recall batch recipes easily. This simplifies changeovers, lowers downtime, and improves the system's overall efficiency. The system's advanced analytics capabilities provide valuable insights into production trends and component-specific performance metrics.
BENEFITS OF THE CHAIN-ON-EDGE CONVEYOR SYSTEM
The chain-on-edge conveyor system is known for its versatility, reliability, and advanced technology. With robotic handling and PLC-controlled systems, these automated solutions minimize the need for manual input, and every part is coated accurately. The system’s versatility in adapting to different coatings also makes it ideal for diverse manufacturing needs.
Manufacturers benefit from this system’s ability to boost productivity. With fast changeovers and reduced downtime, production lines operate more efficiently. The system’s precision leads to fewer defective parts, saving both time and materials. Chain-on-edge helps automotive manufacturers achieve zero defects and meet demanding OEM and supplier requirements.
ROLL COATER: IDEAL FOR HIGH-VOLUME PRODUCTION
The roll coater system offers unmatched efficiency for manufacturers focused on high-output needs. This system works best with products that have similar shapes and coating requirements.
It applies a uniform layer to each part so that every product meets quality expectations. The roll coater provides higher throughput than the chain-on-edge system, making it well-suited for large-scale production.
Advanced controls ensure consistent quality across all parts. Each component adheres to stringent standards similar to those of the chain-on-edge system. Automated calibration keeps application parameters precise throughout production runs, enhancing reliability and consistency.
The roll coater's ability to use nearly all the coating material during application sets it apart. It boasts nearly 100% transfer efficiency, meaning virtually all coating material is applied to the parts. This helps manufacturers minimize waste, maximize cost savings, and meet tight deadlines without sacrificing quality.
WHY CHOOSE THE ROLL COATER FOR HIGH-VOLUME APPLICATIONS?
The roll coater is particularly effective for parts that require a smooth, uniform finish on the outside diameter. Components like bushings, outer metals or cylindrical shapes benefit from this system's efficient and precise application. Thorough surface coverage ensures that the adhesive bonds properly, protecting against wear, corrosion, and exposure to harsh environments.
This system also excels when manufacturers need to produce many parts quickly. The roll coater’s advanced control features allow operators to fine-tune the coating process. This guarantees that each part is coated to the same standard, reducing the risk of rework and seeing to it that production goals are met on time.
CASE STUDIES: SUCCESS IN AUTOMOTIVE MANUFACTURING
A leading automotive supplier sought to improve the efficiency of its rubber-to-metal bonding process. The Arnold Machine chain-on-edge conveyor system optimized adhesive application and significantly reduced material waste.
The system’s real-time monitoring allowed for precise adjustments during the coating process, increasing overall throughput and improving consistency across all parts. This upgrade helped the company maintain high-quality standards while minimizing production costs.
Another automotive manufacturer needed a reliable solution to apply anti-corrosive coatings to metal parts. The chain-on-edge conveyor system was chosen for its ability to handle complex part geometries with precision.
The system’s automated controls made sure that each part received an even coating, resulting in fewer defects and reduced rework. The company experienced a great improvement in product durability. The system also allowed them to meet strict industry standards for corrosion resistance without compromising production speed.
COMPARING ALTERNATIVES: CHAIN-ON-EDGE AND ROLL COATER ADVANTAGES
Methods like tumble spray coating offer consistent coverage for batch production, eliminating masking needs, and are well-suited for parts requiring complete coating. However, they often fall short in terms of throughput. The chain-on-edge and roll coater systems offer significantly greater speed and efficiency for high-volume applications.
It's important to note that the ideal coating system depends on the specific part geometry and adhesive requirements. Tumble coating or submersion methods are better for parts that need full coverage. These methods work well for complex shapes and deliver better results. Arnold Machine offers a range of solutions to meet diverse manufacturing needs.
Manual application introduces even more challenges. This method is highly dependent on the operator’s skill. It results in more waste and often leads to higher scrap rates. In contrast, the chain-on-edge and roll coater systems provide consistency, accuracy, and efficiency.
EXPERT COATING SOLUTIONS FROM ARNOLD MACHINE
The chain-on-edge conveyor system is the best choice for manufacturers needing precise, consistent coatings for automotive anti-vibration components. Its efficiency and accuracy make it the top option for reducing waste and improving productivity.
Arnold Machine is a leader in providing advanced coating solutions. We build customized systems to address complex coating challenges and boost production efficiency. Click below to learn how we can help optimize your operations.