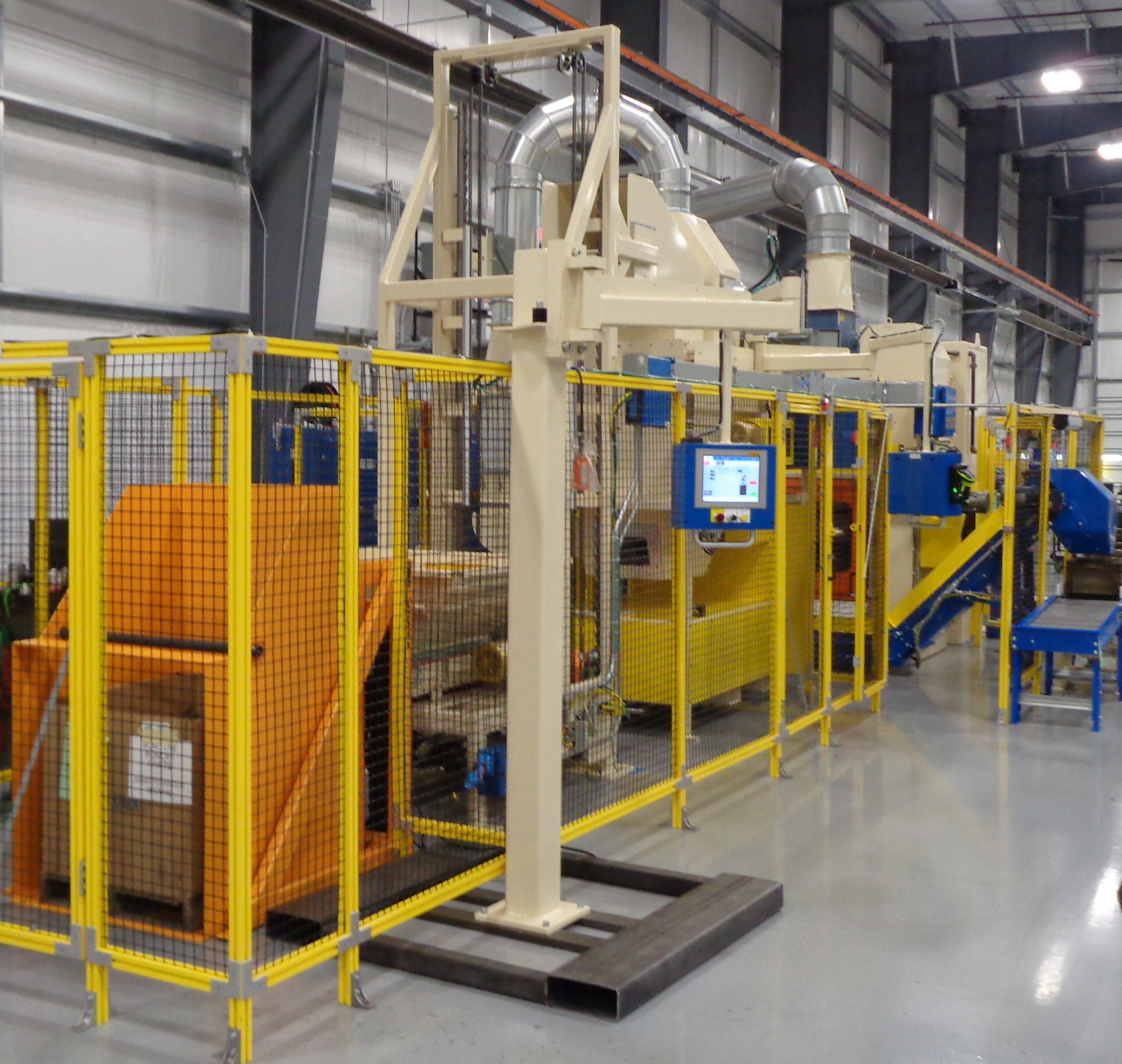
Improving Adhesive Application with an Automated Tumble Spray Machine
Automated tumble spray machines dramatically improve the consistency, quality and efficiency of adhesive application.
Automated tumble spray machine improves quality and consistency for major automotive supplier
It’s sometimes the case that advanced automated solutions take their cues from the more rudimentary systems that precede them.
Other times, a careful assessment of inefficient production shows that the best solution changes almost everything about a process.
Such was the case when a major North American automotive supplier improved precision and consistency in manufacturing by integrating an automated spray process that looked nothing like what came before it.
CHALLENGE: A Product / Process Mismatch Hampers Efficiency
At issue was the application of adhesive to window metals used to make anti-vibration components in cars and trucks. In this stage of the process, adhesive is applied to small tubes with many “windows” cut out of them.
Our customer’s original application process was the dip-and-spin method—loading the parts into baskets, dipping the baskets into an open tank of adhesive and then spinning the baskets to dry the parts. This process achieved total coverage of adhesive but also caused a problem: Parts with complex geometries are at risk of adhesive pooling. This occurs when more adhesive than desired clings to part edges compared to flat surfaces.
Another problem was the open tank of solvent-based adhesive. Evaporation of solvents reduced the amount of adhesive available for application and compromised the viscosity of what was available.
The customer devised an alternative approach, which was to attach these parts to spindles on a traditional chain-on-edge conveyor system. The adhesive was applied via a spray gun that activated as parts passed by.
The system worked, but not very well. Window metal components are mostly empty space. Much of the sprayed adhesive never attached to the surface. It took much longer to ensure total coverage of adhesive compared to parts without cut-outs. The customer had merely traded old problems for new ones.
Our team determined a totally new direction was needed to make the process faster and less wasteful.
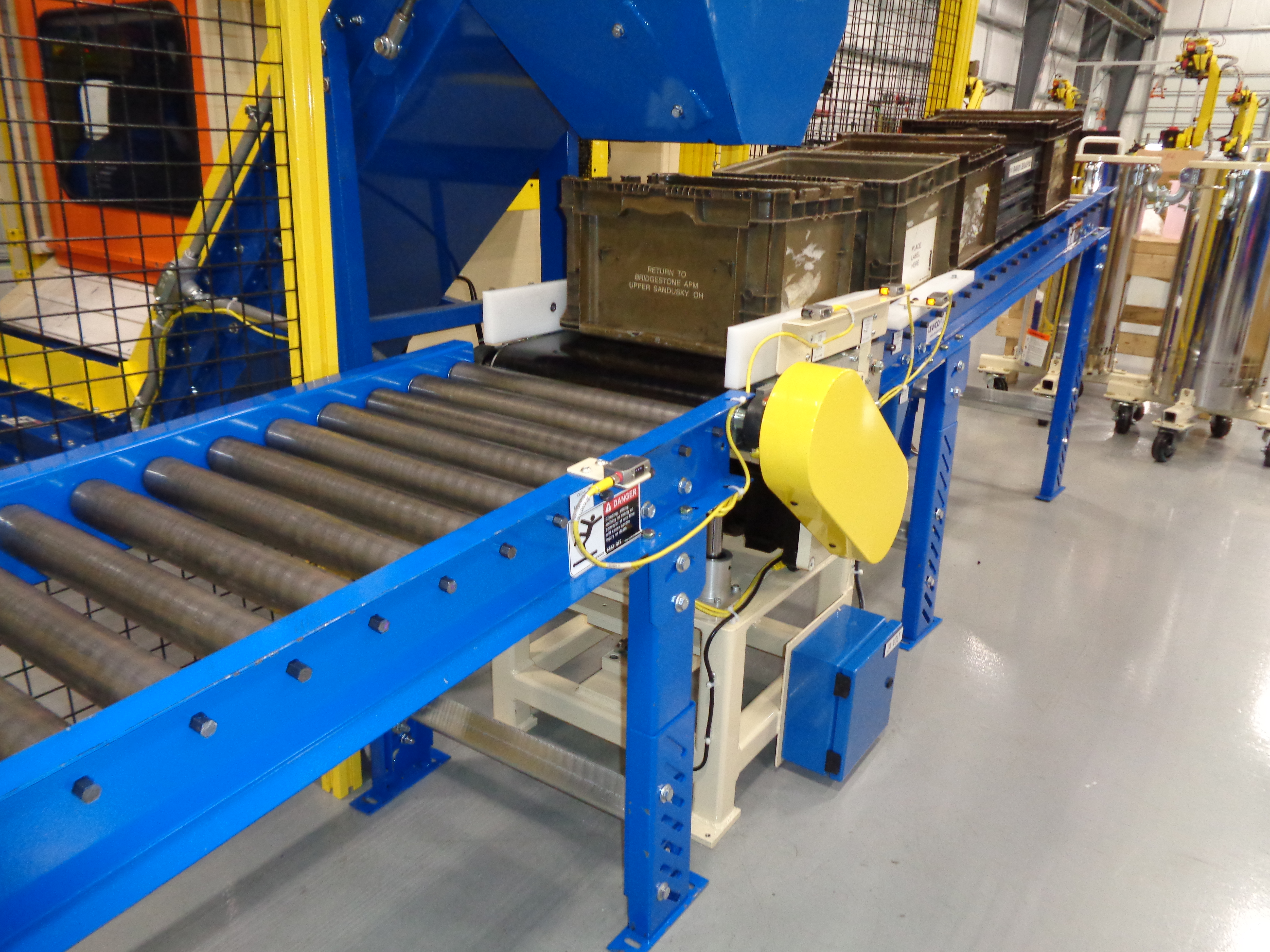
SOLUTION
An automated tumble spray machine that featured hands-free transfer through multiple stages. The machine also included a more systematic loading scheme whereby loads were set by weight. Here’s how it works:
- Parts are dumped onto a conveyor until the desired load weight is reached.
- Parts are then transferred to a preheated oven and heated to reach a uniform temperature.
- The parts then move to the tumble chamber where adhesive is applied for a specified amount of time to achieve full coverage.
- If parts receive two coats, they continue tumbling in the chamber as the first application dries.
- Then, the second coating is applied.
- Next, a top coat is applied.
- Following all coating applications, the parts are unloaded from the chamber into containers and moved to the next processing stage.
- Tumble spray booth within automated tumble spray adhesive dispensing system, Arnold Machine, Inc.
Many facets of this system dramatically improve the consistency, quality and efficiency of adhesive application.
First and foremost, significantly less adhesive is used because it is applied in a closed chamber in a fixed amount. It only took a couple practice runs to determine the exact amount of adhesive required to achieve total coverage of the parts.
Next, the time it takes to apply adhesive to loads is also reduced. Rather than coat parts one at a time, many parts are processed in bulk.
Third, the hands-free transfer of parts from stage to stage improves precision and consistency by eliminating human involvement.
Finally, the machine includes bulk storage and mixing cabinets so that adhesive can be prepared more safely and stays in an ideal condition for the duration of its use.
Time To Update Your Automated Processes
Modern manufacturing is marked by the rapid advances in automation technology. Legacy manufacturers, such as our customer in this case study, know that their place at the top of the heap is never guaranteed.
The manufacturers in our collection of spray equipment case studies knew this, too. If you’ve already automated a process in your facility, don’t stop there. Think about what comes next.
And if you’re having a hard time seeing where the next opportunity lies, let’s work it out together. Contact us if you’re ready to plan the automation upgrade your facility needs.