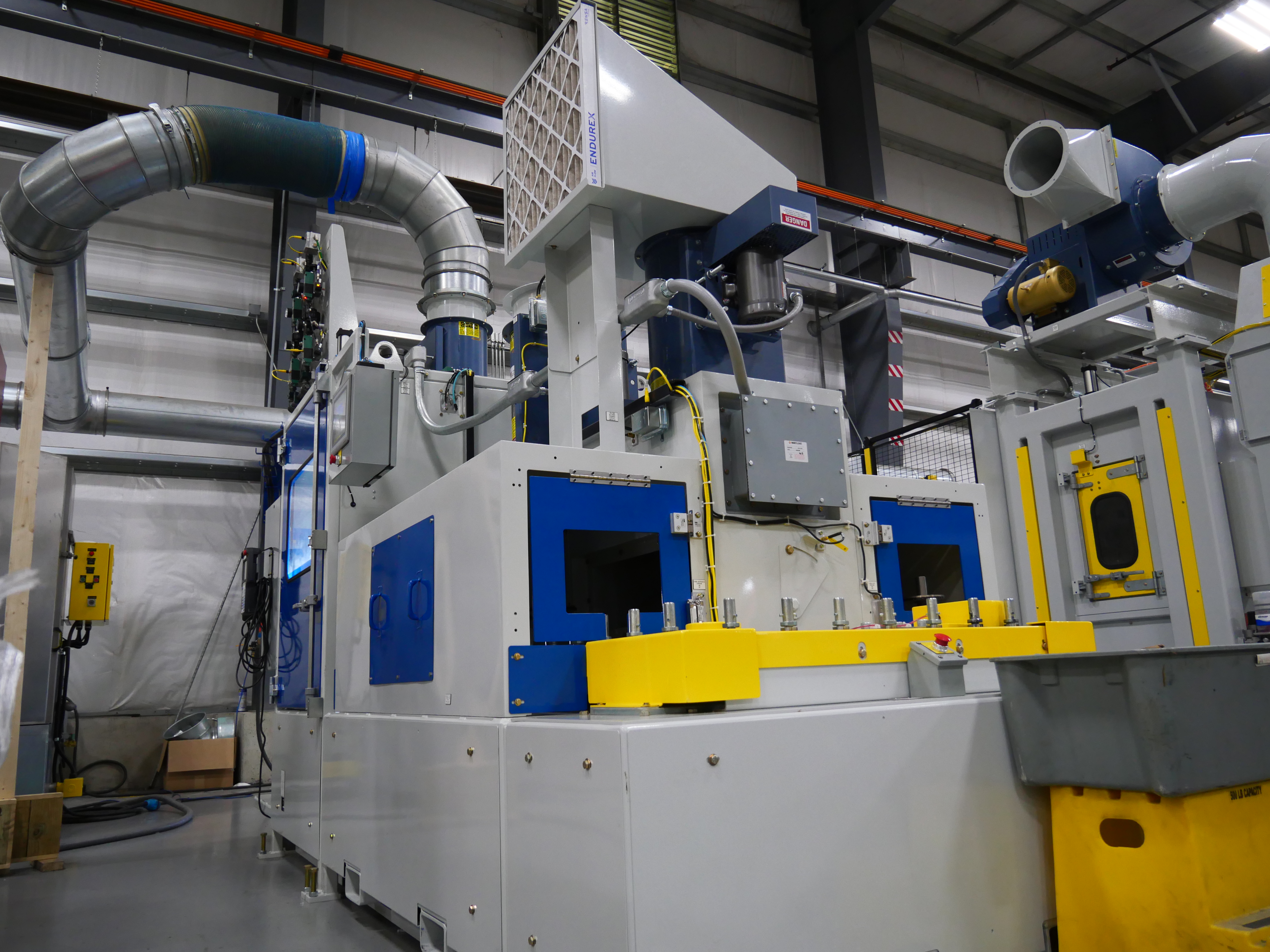
AUTOMATED SPRAY SYSTEMS: THE KEY TO INCREASED EFFICIENCY
Many businesses struggle to make their industrial painting and coating processes efficient. Engineering managers face many challenges due to inconsistent coating quality, material waste, and high labor costs.
Automating this process improves the end product while significantly reducing operational expenses. Manufacturers have seen transformative production improvements from implementing state-of-the-art chain-on-edge spray systems.
Read on to learn how these innovative solutions revolutionize industrial painting and coating processes.
ENHANCING EFFICIENCY WITH AUTOMATED SPRAY SYSTEMS
Automated spray systems transform the painting process and bring many efficiency benefits. The systems significantly reduce material wastage while precisely controlling spray patterns and volumes. The result is lowered operating costs and maximized material usage.
Simultaneous cleaning and new part setups boost efficiency compared to past sequential methods. This parallel operation slashes changeover times versus staggered processes. Operators can perform changeovers on one station while others continue production.
Other features that optimize workflows include pre-programmed spray positions and the ability to create 'recipes.' These allow quick changeovers between parts, reducing setup times and easing transitions. By selecting the correct recipe, operators can swiftly adjust spray gun fluid and air pressure settings, oven temperatures, spray times, rotation speeds, and line speed.
The beauty of automated spray systems is their inherent flexibility and precision—right down to the level of individual components. For instance, operators can flag the spindle where a changeover occurs, permitting simultaneous cleanout and introducing new parts. This feature streamlines the process, saving valuable time and promoting efficiency.
Another benefit is the reduced need for manual labor. Increased automation enhances production efficiency and minimizes the likelihood of human error. The result is a consistent level of quality that bolsters both the reliability and lifespan of the finished products.
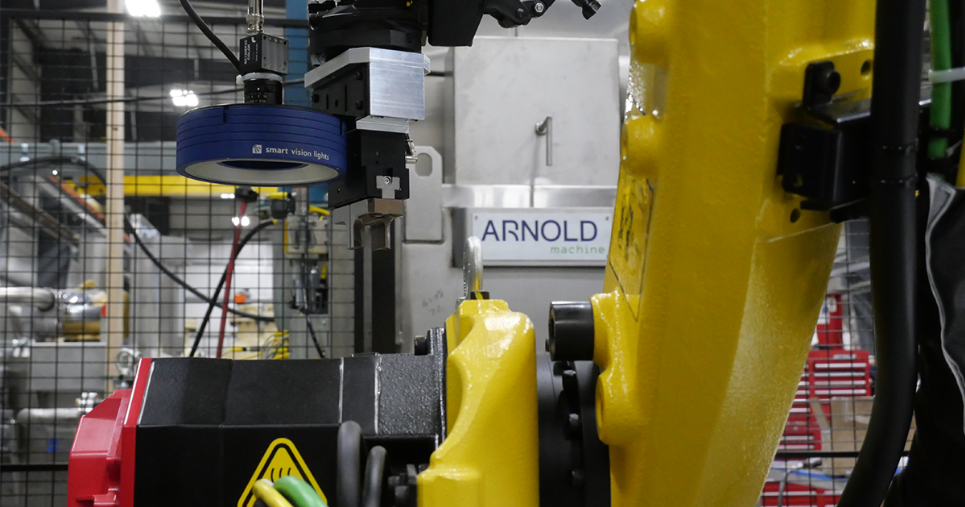
OTHER BENEFITS OF AUTOMATED SPRAY SYSTEMS
Automated spray systems streamline manufacturing processes and embody a commitment to safety and regulatory compliance. They’re designed with safety measures and controls that align with industry standards.
However, they do a lot more than just improve efficiency. They offer many other benefits that can make a difference in your production line:
- Consistent Quality: Automated systems consistently apply paint, adhesive, and other materials. This leads to uniform quality across all products. This consistency is hard to achieve with manual processes.
- Increased Production Speed: These systems often work faster than manual methods, allowing for higher throughput and more efficient use of time in production.
- Reduced Labor Costs: Automated systems handle tasks typically requiring manual labor. This increased efficiency saves labor costs and allows you to allocate workers to more critical tasks.
- Enhanced Precision: They can apply materials with greater precision than is typically possible by hand, reducing over-spray and improving finish quality.
- Data Collection and Analysis: Many automated systems can collect data about the spraying process. You can use it to improve efficiency, troubleshoot, and maintain quality control.
- Environmental Benefits: Automated systems are better for the environment than manual spraying. They minimize the amount of excess spray and make the most of the materials used. This leads to less waste and more efficient operations.
- Minimizing capital investment: Machine-as-a-Service (MaaS) enables manufacturers to get a state-of-the-art, automated chain-on-edge system on their factory floor for a minimal upfront cost.
A notable application is their ability to spray and apply complex profiles via robotic arms. This advanced capability opens up new possibilities in manufacturing. It allows for detailed work that would be hard or even impossible with manual operations.
REAL-WORLD SUCCESS STORIES
A Tier 1 automotive supplier enlisted Arnold Machine to design and manufacture an automated system for applying anti-corrosive coatings. The innovative solution used a robotic spray cell with integrated part washing and curing to coat complex, small parts consistently.
The automated process achieved uniform paint coverage and reduced waste from overspray. The state-of-the-art coating system increased process efficiency and opened up the potential for new business areas.
Another automotive manufacturer sought to improve its adhesive application process for high-volume rubber-to-metal bonded parts. Arnold Machine custom-designed an automated chain-on-edge spray system using indexing conveyors and electronic traversing spray guns.
The automated spray solution increased efficiency and quality by precisely controlling the spray pattern and amount. This level of control is a significant upgrade over continuous motion methods, which are limited to processing one part at a time.
Chain-on-edge technology positively impacts more than just process speed. It also enhances quality and efficiency in specialized applications. These two case studies demonstrate the versatility of chain-on-edge technology to transform a wide range of manufacturing processes.
UNVEILING THE VALUE OF OUR COATING SYSTEMS
Arnold Machine leads the way in industrial coating innovation with our customized robotic and automated spray systems. We focus on creating solutions that apply adhesives and coatings with precision and efficiency. Here's how our systems stand out:
- Customization: We build each system to meet our client's needs and solve their toughest spray coating challenges. We can add many different levels of customization to enhance system performance.
- Versatility and Precision: Our automated spray systems are highly versatile. They can manage different production levels, fit into current production lines, and adjust to different part sizes and volumes.
- Safety and Process Control: We design every machine to comply with safety regulations and tackle challenges related to flammability and volatiles. Automatic adjustments for adhesive viscosity and substrate temperatures enhance repeatability, safety, and compliance.
- Product Range: We offer a variety of products, including index and chain-on-edge spray machines for round parts, ID tube spray machines for long tubes, tumble spray adhesive lines, and automatic viscosity bulk mixing stations.
Arnold Machine's commitment to advancing coating technology is evident in every system we create. We aim to provide unparalleled value to industries looking to enhance their coating processes.
EMBRACING EFFICIENCY AND INNOVATION
Automated spray systems have reshaped industrial efficiency and quality for the better. They offer speed, intelligence, safety, and sustainability advantages. Embracing these systems equips manufacturers to meet the demands of an increasingly fast-paced and complex industrial landscape.
Let Arnold Machine help you take your spray production line to the next level. Click below to learn more about the costs of a chain-on-edge paint line and how you can get one on your factory floor with no capital investment.