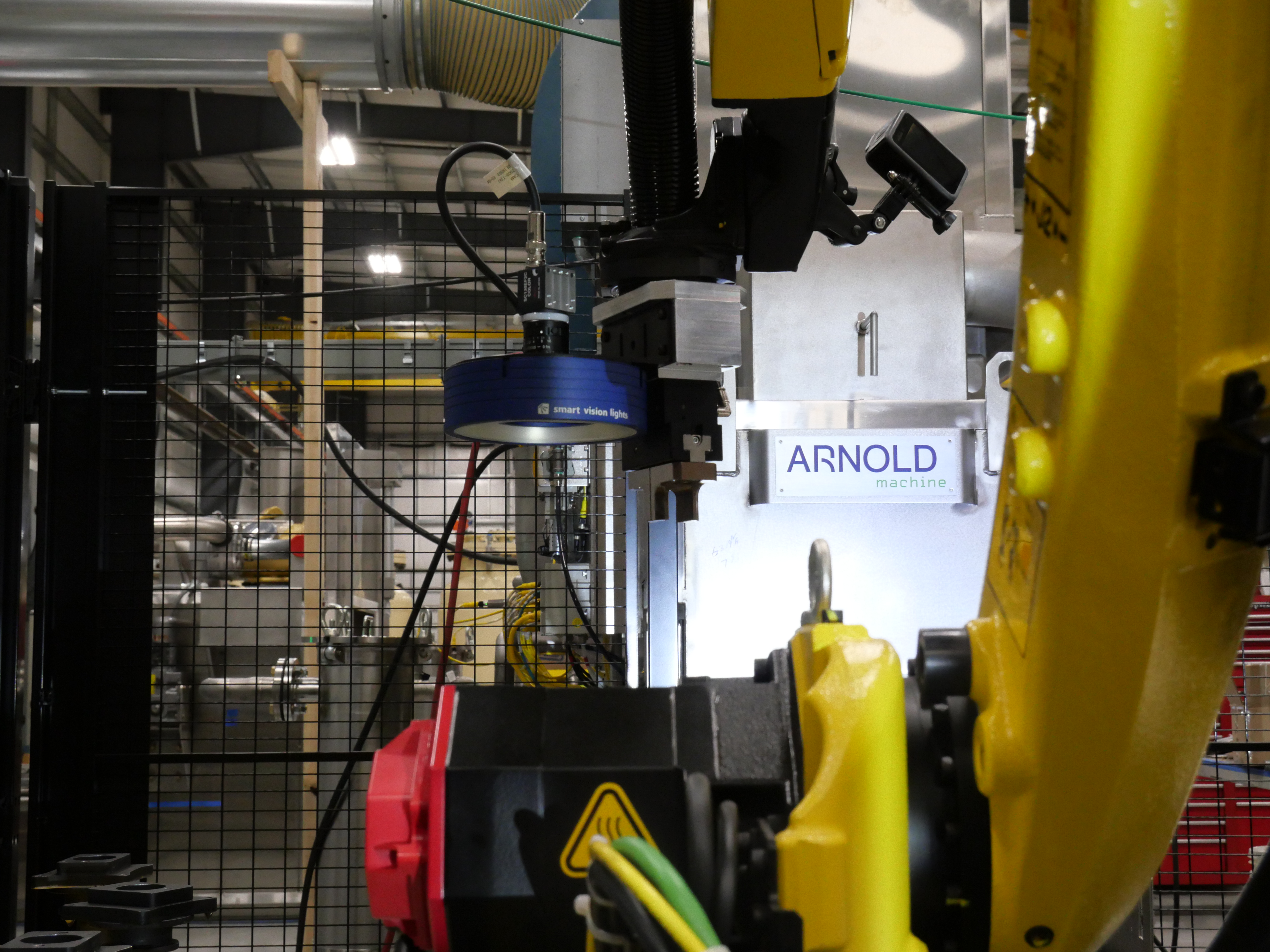
5 SIGNS IT’S TIME TO UPGRADE TO AN AUTOMATED SPRAY COATING SYSTEM
Manual spray processes may have served you well, but as production demands rise, the cracks begin to show. From inconsistent finishes to rising labor costs, outdated coating methods can quietly erode throughput, quality, and profitability.
If you're wondering when to upgrade to an automated spray system, the answer often lies in the operational red flags you can’t afford to ignore. Here are five signs it’s time to make the switch—and how automation can transform your coating line into a true performance driver.
1. INCONSISTENT COATING QUALITY
One of the biggest red flags is poor coating consistency. Manual processes often lead to variable spray patterns and uneven application, especially when different operators or shifts are involved. This inconsistency creates quality control issues, costly rework, and customer dissatisfaction.
Automated spray systems from Arnold Machine are programmed for precise, repeatable application. Parameters like spray gun settings, nozzle distance, and rotation speed are controlled via a centralized logic control system. The result? A high-quality finish on every part, with virtually no variation.
Plus, with real-time monitoring and feedback capabilities, operators can track key metrics like material flow and spray gun performance to ensure consistent results throughout the production line.
Arnold’s Chain-On-Edge spray systems are ideal for adhesive, paint, and rust-preventive applications, delivering uniform coating thickness even on parts with complex geometries. For industries with VOC compliance requirements or tight tolerance specifications, this level of precision is not optional—it’s essential.
2. HIGH MATERIAL WASTE AND LOW TRANSFER EFFICIENCY
Still relying on handheld spray guns? You’re likely experiencing low transfer efficiency, meaning more coating ends up wasted than applied. Material waste doesn’t just raise operating costs; it also inflates energy consumption, increases emissions, and complicates cleanup and environmental compliance.
Arnold Machine’s systems utilize precision spray patterns and optimized air and fluid controls for consistent coating coverage with minimal overspray. That means higher transfer efficiency, lower material costs, and fewer environmental headaches. Automated systems also allow you to measure improvements in real time, so you can calculate ROI and justify the upgrade with data.
In particular, the Single-Coat Chain-On-Edge Coating System uses an HVLP spray gun with integrated fluid recirculation, agitation, and material flow sensors to ensure uniform application and minimize waste. These systems support sustainable practices and can help your facility meet increasingly strict environmental regulations without sacrificing performance.
3. RISING LABOR COSTS AND LABOR SHORTAGES
With skilled labor becoming harder to find, especially for specialized tasks like manual spraying, many manufacturers are feeling the pinch. If you’re increasing headcount just to meet daily quotas or reallocating valuable personnel to cover coating operations, it’s time to rethink your approach.
Automated coating systems reduce your dependency on manual labor. Once programmed, these systems can operate autonomously or with minimal oversight. This frees up staff for other tasks, helps stabilize operating costs, and reduces exposure to hazardous materials—all while boosting overall efficiency.
Arnold Machine also offers Machine-as-a-Service (MaaS) options for customers needing scalable solutions with lower upfront investment. The MaaS model includes lifetime service, software updates, and remote diagnostics, making it an attractive path for companies looking to automate without the capital expenditure.
4. FREQUENT MAINTENANCE AND DOWNTIME
Outdated manual systems often require constant adjustments, regular nozzle replacements, and ongoing operator oversight. These interruptions not only increase maintenance costs but also disrupt your production schedule, leading to missed deadlines and strained customer relationships.
Arnold Machine designs its finishing systems with reliability and uptime in mind. Features like automatic chain tensioning, centralized lubrication, and filter change alerts help extend the life of your equipment and reduce unplanned downtime. Every piece of equipment is engineered with rugged 304 stainless steel construction and designed for real-world manufacturing environments.
Systems also include built-in safety features like fire suppression, explosion-proof booths, and safety interlocks, protecting both your equipment and your team. Maintenance expectations are clear and manageable, with access panels, chip baskets, and routine inspection points making it easy to keep systems running at peak performance.
5. LIMITED PRODUCTION CAPACITY OR THROUGHPUT
A manual coating setup might suffice for small batches, but when demand rises, it quickly becomes a bottleneck. If you're turning down orders or struggling to scale production, that's a clear sign it's time to upgrade.
Arnold Machine’s Chain-On-Edge systems are engineered to handle both high- and low-volume production. With features like servo motor-controlled conveyors, robotic or servo-driven spray heads, and programmable spray cycles, these systems significantly improve productivity. You can run multiple parts in parallel with precise, repeatable results, maximizing throughput without expanding your floor space.
Systems are also designed to integrate with upstream or downstream processes like washing, curing, or inspection, streamlining your entire production line. This seamless integration capability reduces work-in-progress (WIP) inventory, minimizes manual handling, and ensures consistent process flow.
WHY AUTOMATED SPRAY SYSTEMS ARE THE SMARTEST INVESTMENT FOR MANUFACTURERS
If your coating process shows any of these signs, it may be time to evaluate when to upgrade to an automated spray system. Arnold Machine’s solutions improve coating quality, reduce waste, lower maintenance costs, and enhance production line efficiency, resulting in long-term return on investment.
With decades of experience designing and building automated spray systems, Arnold Machine is a trusted partner for manufacturers across the automotive, aerospace, and industrial sectors. We tailor each solution to your specific needs—from standard machines like the Single-Coat Chain-On-Edge system to fully customized, multi-station applications.
Whether you're looking to reduce human intervention, achieve consistent outcomes, or cut operating costs, our systems deliver improved productivity, lower risk, and a clear competitive edge.