Roll Coater Systems
Arnold Machine Roll Coater Systems deliver consistent coating results in high-volume production environments. We engineer our customized solutions to fit seamlessly into your existing processes.
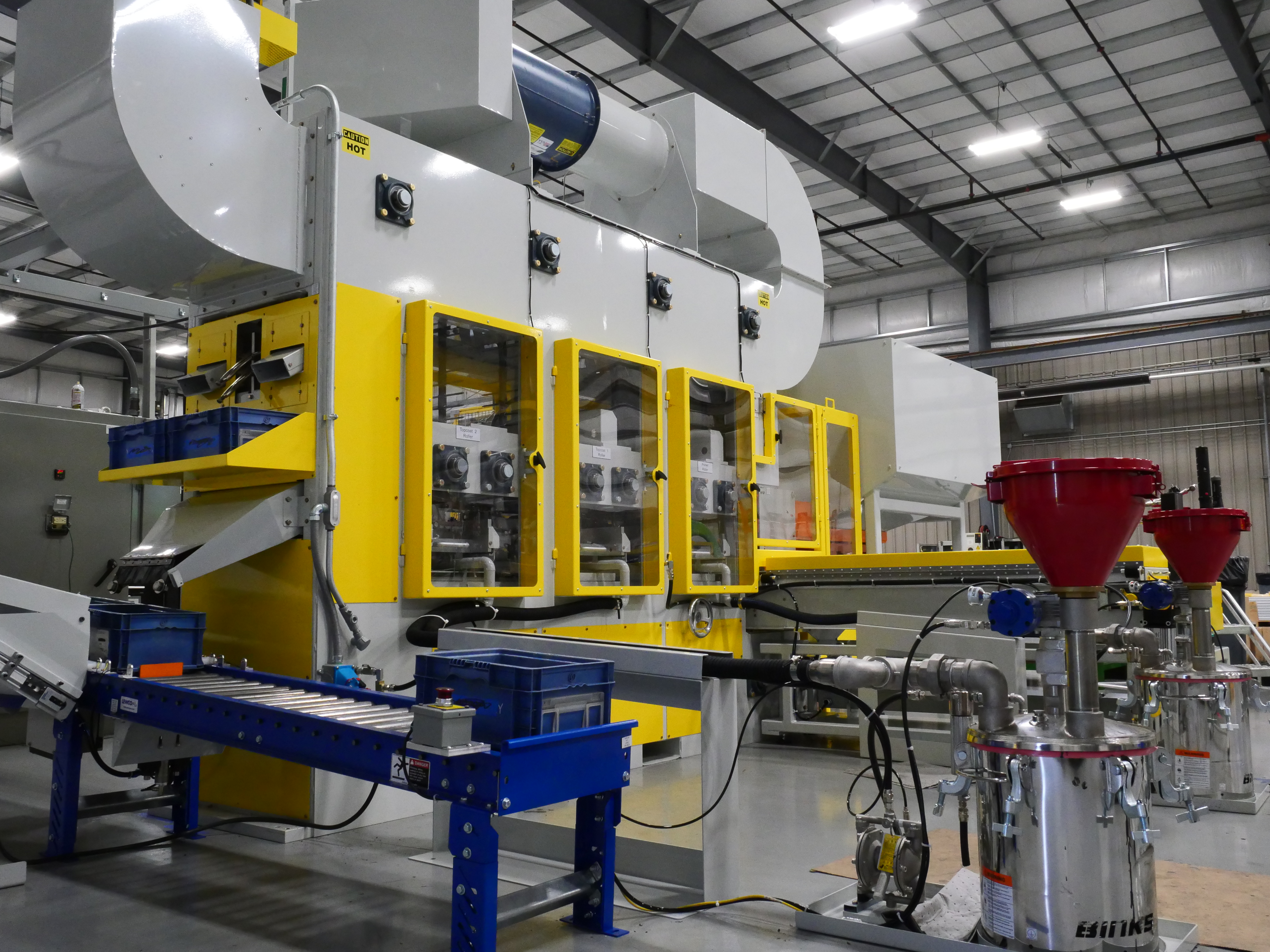
Benefits of Roll Coater Systems
How Roll Coater Systems Work
Here’s how our roll coater system efficiently coats your parts for consistent results:
Parts Loading: An operator places a bulk parts tote onto a powered tote dumper. After stepping behind a safety light curtain, the operator activates the dumper. Parts funnel into a bulk hopper and are transferred upward via a flighted conveyor or stepper feeder onto a belt conveyor. The belt positions the parts for loading onto spindle shafts at a continuous programmable speed.
Shaft Loading: Two separate actuated mechanisms secure parts to shafts located on an indexing chain conveyor. The conveyor moves two parts simultaneously on opposing sides of the chain.
Coating Process:
- Temperature Increase: Parts travel through a series of loops in an oven to raise their temperature.
- Primer Application: Parts pass over a spinning applicator wheel that applies the Chemlok primer.
- Top Coat Application: Parts move through another loop and then a second applicator wheel for a Chemlok top coat, followed by a final loop before receiving their ultimate coating.
- Part Rotation Monitoring: Throughout the coating process, two sensors monitor part rotation and ensure consistent application. These sensors can sometimes detect glare from coated parts, an issue that AMI will work to resolve.
Cooling and Unload: Coated parts travel along a conveyor to cool down to a temperature of 125-130°F. Formed sheet metal guides parts to the outside of the spindle and onto a gravity chute. A pneumatic diverter removes any defective parts (those where one of the sensors did not detect rotation during coating).
Final Steps: Acceptable coated parts drop into a large tote and are counted by a Keyence LRZ laser sensor. Two large totes (one empty, one full) are placed on a gravity roll conveyor. When the HMI signals that a tote is full, the operator pushes the empty tote into position and replaces the full tote with an empty one.
Common Applications
Roll coater systems offer a reliable solution for coating cylindrical aluminum or steel parts in various manufacturing settings.
These systems are ideal for components with a flat or straight surface, ensuring an even coating result. Smaller parts weighing under 2 lbs are particularly well-suited for this equipment.
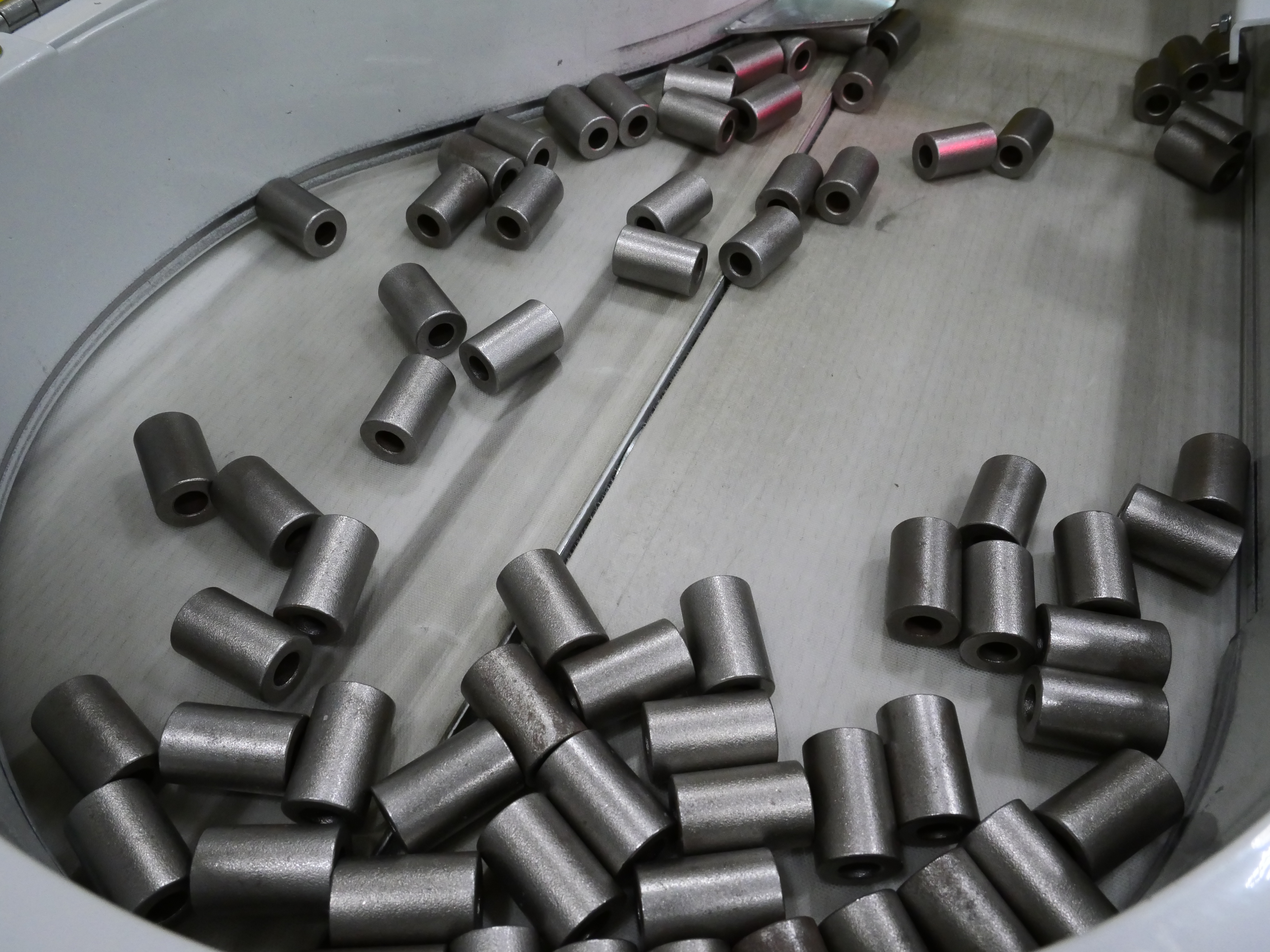
Specs & Features
Our Roll Coater Systems excel at efficiently applying solvent or water-based adhesive primers and topcoats to high volumes of small, cylindrical parts (outside diameters between 25-30mm and lengths of 40-100mm). This system is ideal for consistent adhesive application on the outer diameter of your parts, making it the preferred choice for high-volume production of small cylindrical components.
Precise and Customizable Coating:
The system comes standard with two coating stations, allowing for a primer coat and a top coat. Each coat is followed by a curing process in a 130°F electric heat oven for optimal adhesion. The system is designed to handle Chemlok/Chemosil, Cilbond, and Thixon adhesives, but it can be customized to accommodate your specific adhesive needs and part dimensions.
Standard Specifications:
- Part size:
- Outside diameter: 25 - 30 mm
- Inside diameter: 14 - 25 mm
- Overall length: 40 - 100 mm
- Coating:
- Two solvent-based adhesive applications (primer & top coat)
- Curing:
- 130°F electric heat oven (before & after each coat)
- Utilities:
- 60 psi compressed air
- 480V / 3PH / 73 FLA
- Dimensions:
- Length: 27.5 ft
- Width: 19 ft
- Height: 11.5 ft
Additional Features (Optional):
- Automatic solvent flushing
- Additional application rollers for different adhesives
- Gas-powered heaters
Safety Features (Standard):
- Safety guarding and light curtains at the bulk hopper load end
- Safety interlocked doors throughout the system
- Heater over-temperature alarms
- Fail-safe device preventing heater operation without exhaust fan
Trust Arnold Machine with Your Coating System Needs
At Arnold Machine, we understand the critical role of reliable and efficient coating systems in your manufacturing process. With extensive experience designing automation equipment across various industries, we’ve developed a deep understanding of diverse coating needs.
Our team of seasoned engineers leverages this expertise to create high-performing, repeatable, and safe solutions tailored to your specific requirements. We remain at the forefront of automation technology through continuous learning and collaboration. Strategic partnerships provide early access to emerging technologies, which we actively integrate into customer solutions.
Roll Coater System FAQ
-
How does the system apply adhesive material and what is the transfer efficiency on a roll coater?
-
How many operators are required to operate the system?
-
Does the system utilize any devices to detect primer and top coat?
Other Coating Systems and Related Machines
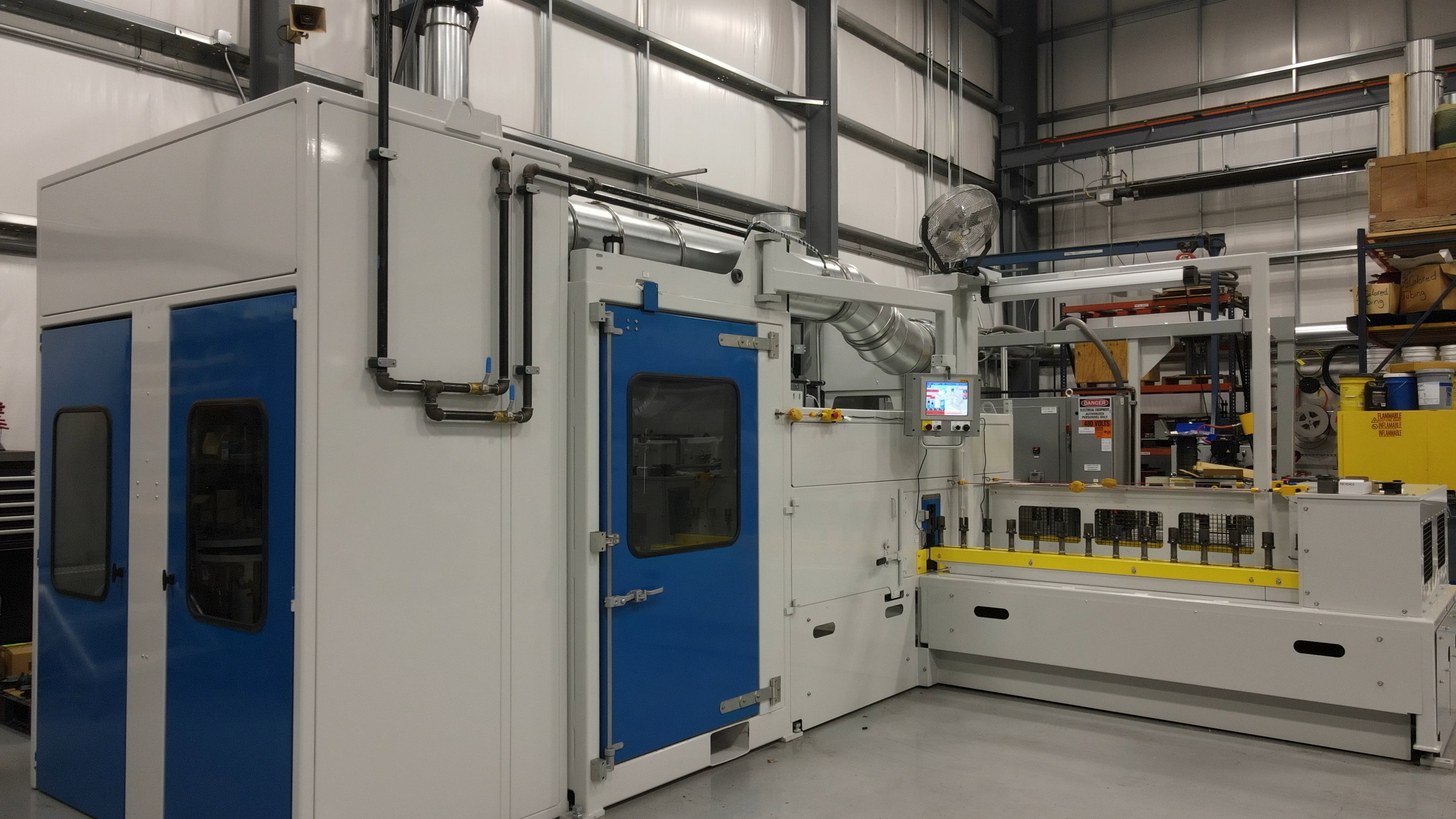
Chain-on-Edge Conveyors
Boost your profitability with our innovative CoE systems. Advanced robotics automate your processes to increase transfer efficiency and reduce labor costs.
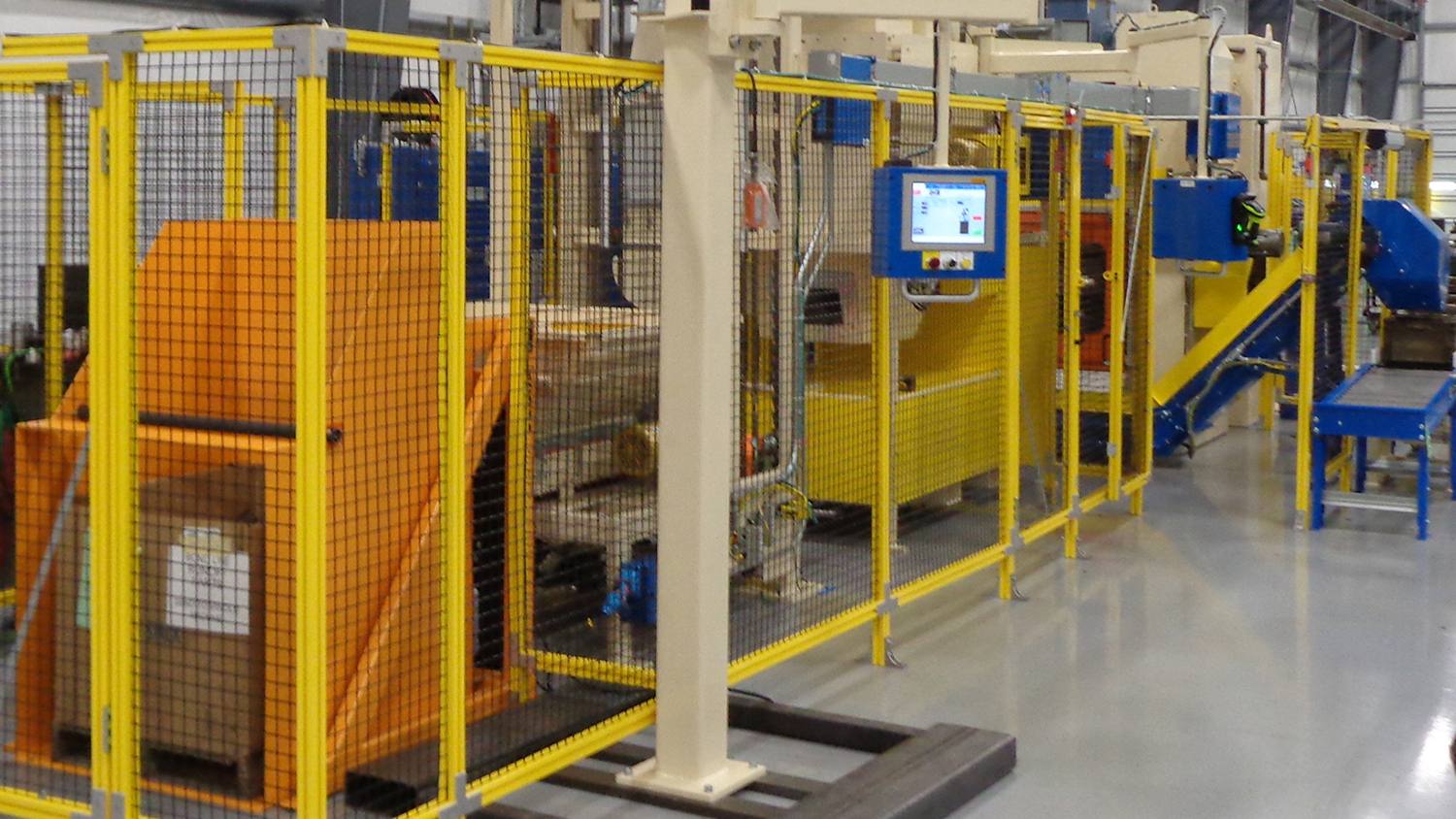
Tumble Spray Coating Systems
Achieve unmatched protection and efficiency with our fully automated Tumble Spray systems. Experience 100% coverage, significant labor savings, and consistent results in your coating operations.
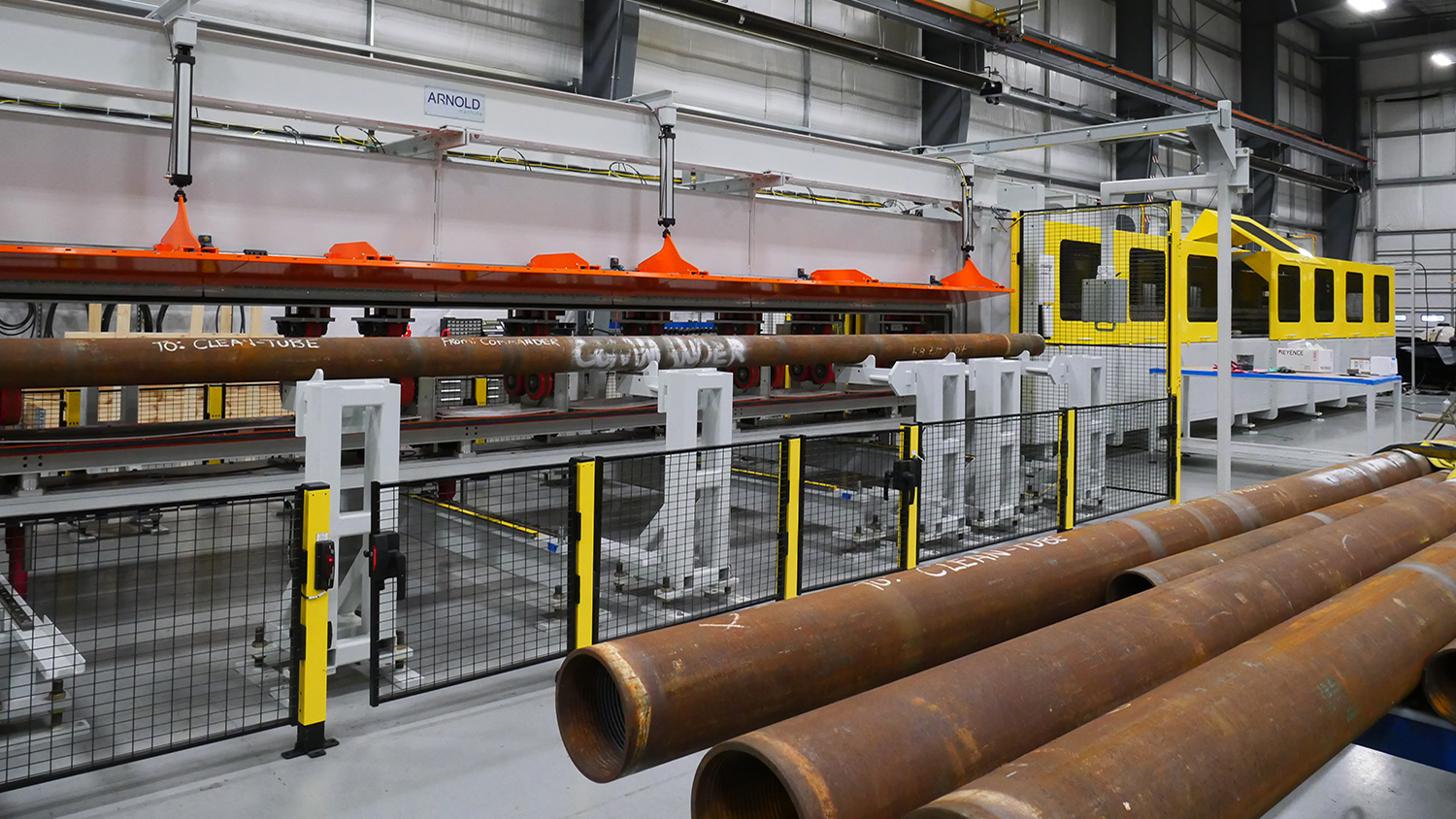
Interior Diameter (ID) Tube Spray Machines
Precision coat interior tube surfaces with our specialized ID spray machines. Optimize your process with our solutions designed for consistent results and efficiency.
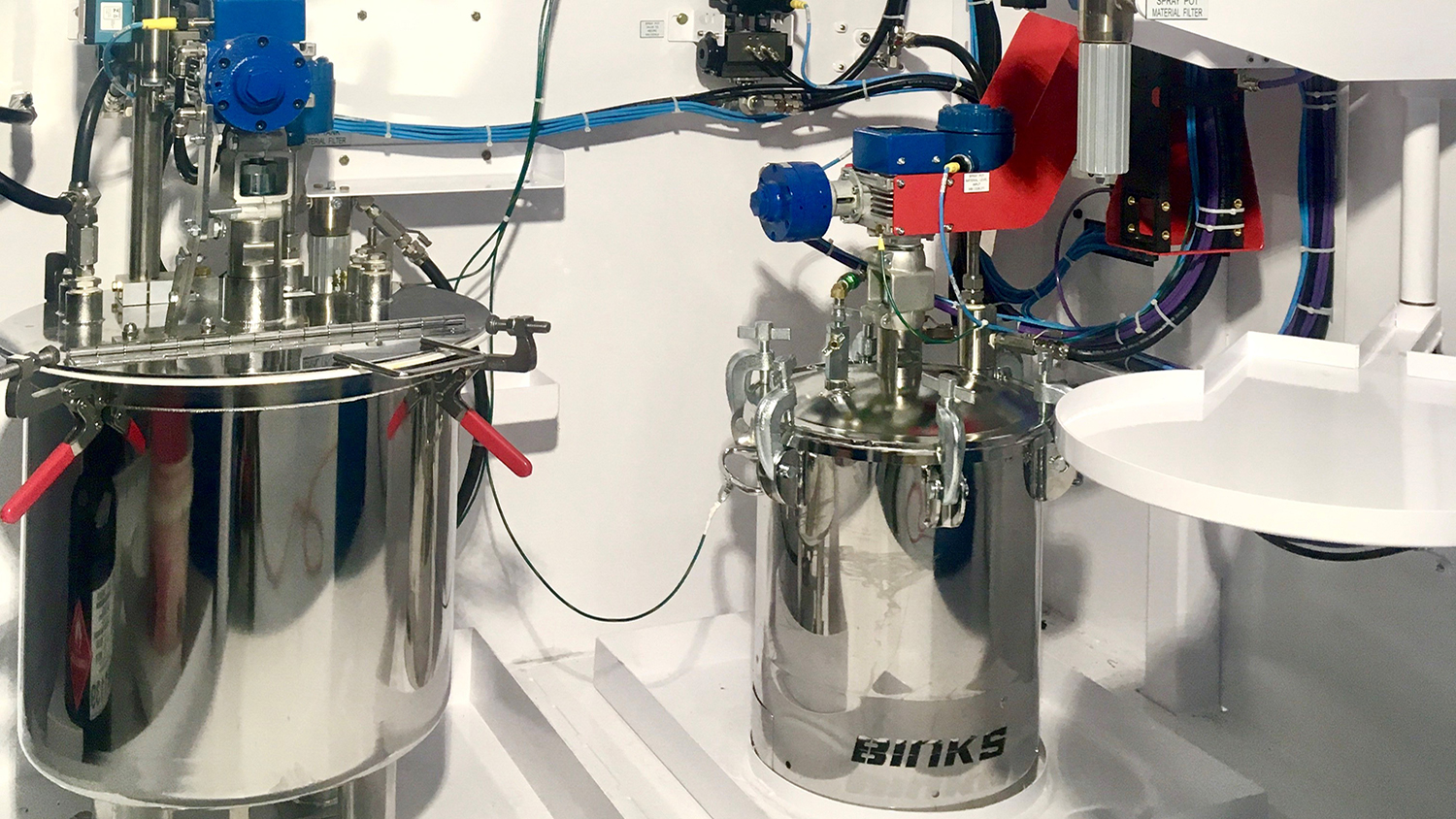
Automatic Viscosity Bulk Mixing Stations
Maintain consistent material viscosity and streamline your production. Ensure coating results and minimize downtime with our reliable, automated solution.