Chain-on-Edge Conveyors
Achieve faster throughput and superior coverage for your complex parts. Arnold Machine Chain-on-Edge (CoE) conveyors combine speed and precision for exceptional coating quality.
We build our paint booth conveyor systems to withstand the rigorous demands of high-volume production environments. This ensures your coating operations experience minimal downtime and deliver consistent results.
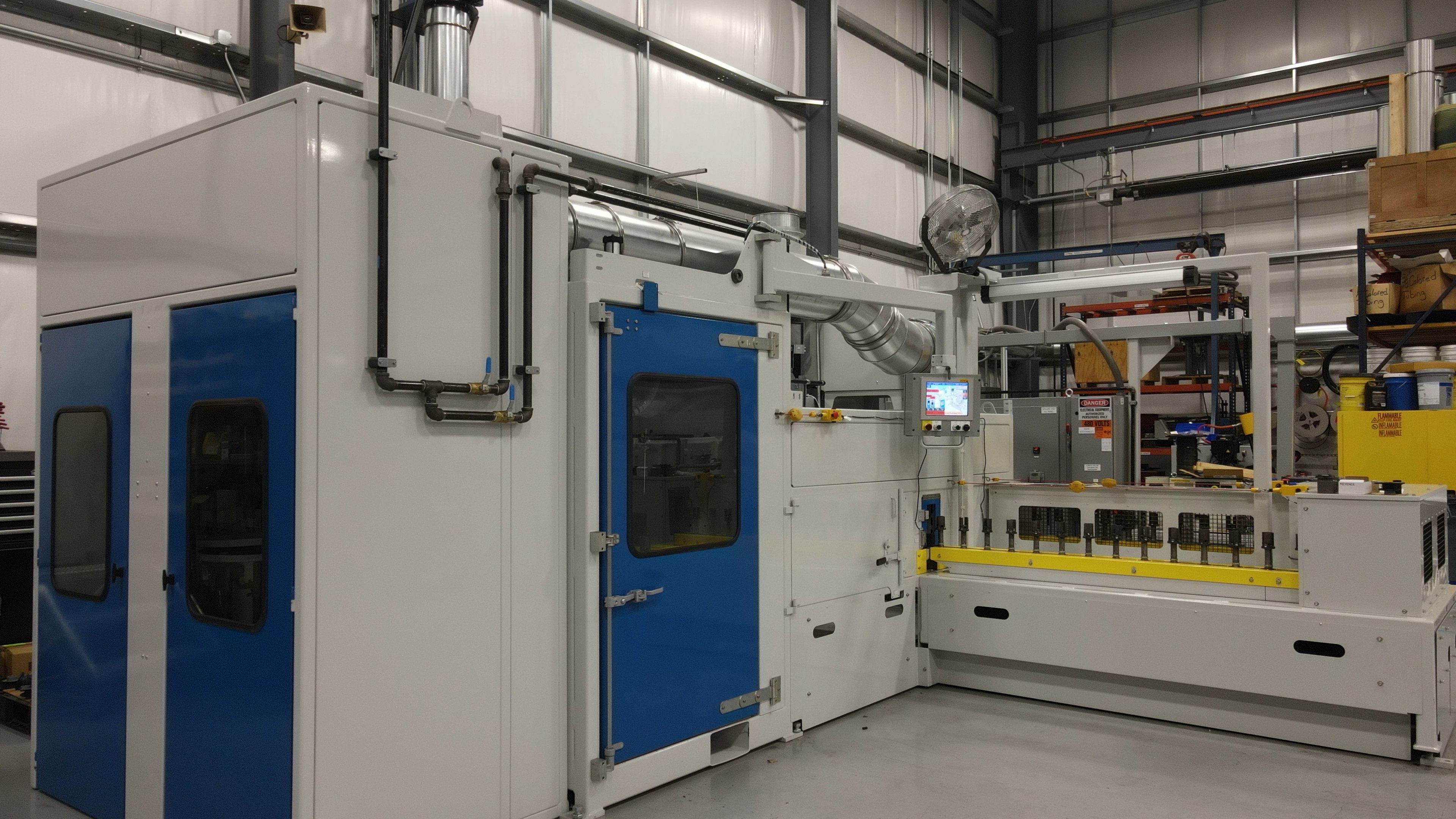
Benefits of Chain-On-Edge Conveyors
Chain-on-Edge Conveyor Options
How Chain-on-Edge Conveyors Work
Arnold Machine Chain-on-Edge cleaning lines streamline the coating process by transporting parts through a series of stations designed for loading, pre-heating, spray application, drying, and cooling. We designed the system to utilize and apply two (2) coating materials throughout the process (solvent or water-based adhesive primer and top coat). The system can also be configured for a single-coat adhesive.
Here’s a detailed look at how they work:
- Load Station: The operator manually loads the appropriate fixtures and parts onto the spindles presented in the load area. This area will have 6' of accessible fixtures for loading and an overhead light for easy visualization. The load station includes an operator work fan.
- Pre-Heat Station: For the primer to adhere to the part, it must be preheated to a predetermined temperature. The pre-heat station in the oven consists of forty-eight (48) spindles to maximize cycle time and oven efficiency. Once the parts have reached temperature in the pre-heat station, they will be conveyed to the primer spray station.
- Primer Spray Station: Parts will enter the spray booth, and the spindle will be engaged with a variable speed belt drive system for part rotation. Two (2) Krautzberger spray guns mounted to FANUC Paint Mate robots are utilized to apply the primer to the part.
The Spray Station controls airflow for maximum transfer efficiency and accommodates ease of cleanup and maintenance.
A Keyence flow sensor will verify that a specific amount of primer has been sprayed from the spray gun between the primer spray station and the primer dry oven. If it does not detect the primer flow, it won’t apply a top coat to the part in the top coat station. The primer pressure pot will be located in the material storage cabinet and provided with all gun connections to the pot.
4. Primer Dry Station: After parts exit the primer spray station, they enter the oven for a series of cycles in the primer dry station. This area will allow the primer to dry further before applying the top coat. There will be eight (8) spindles in this station.
Common Applications
Chain-on-edge conveyors are commonly used to coat straight or profiled cylindrical substrates that require inside or outside diameter coverage.
They efficiently coat multiple faces of a part when needed. Typically, they are used with aluminum or steel substrates ranging in diameter from 1 inch to 5 inches and up to 6 inches tall.
Our CoE conveyors are ideal for large production runs with consistent part sizes and shapes. These systems automate the painting process and reduce the need for manual involvement.
This leads to excellent process control and ensures each part is painted similarly. However, it is important to consider part size limitations and variations when choosing this system.
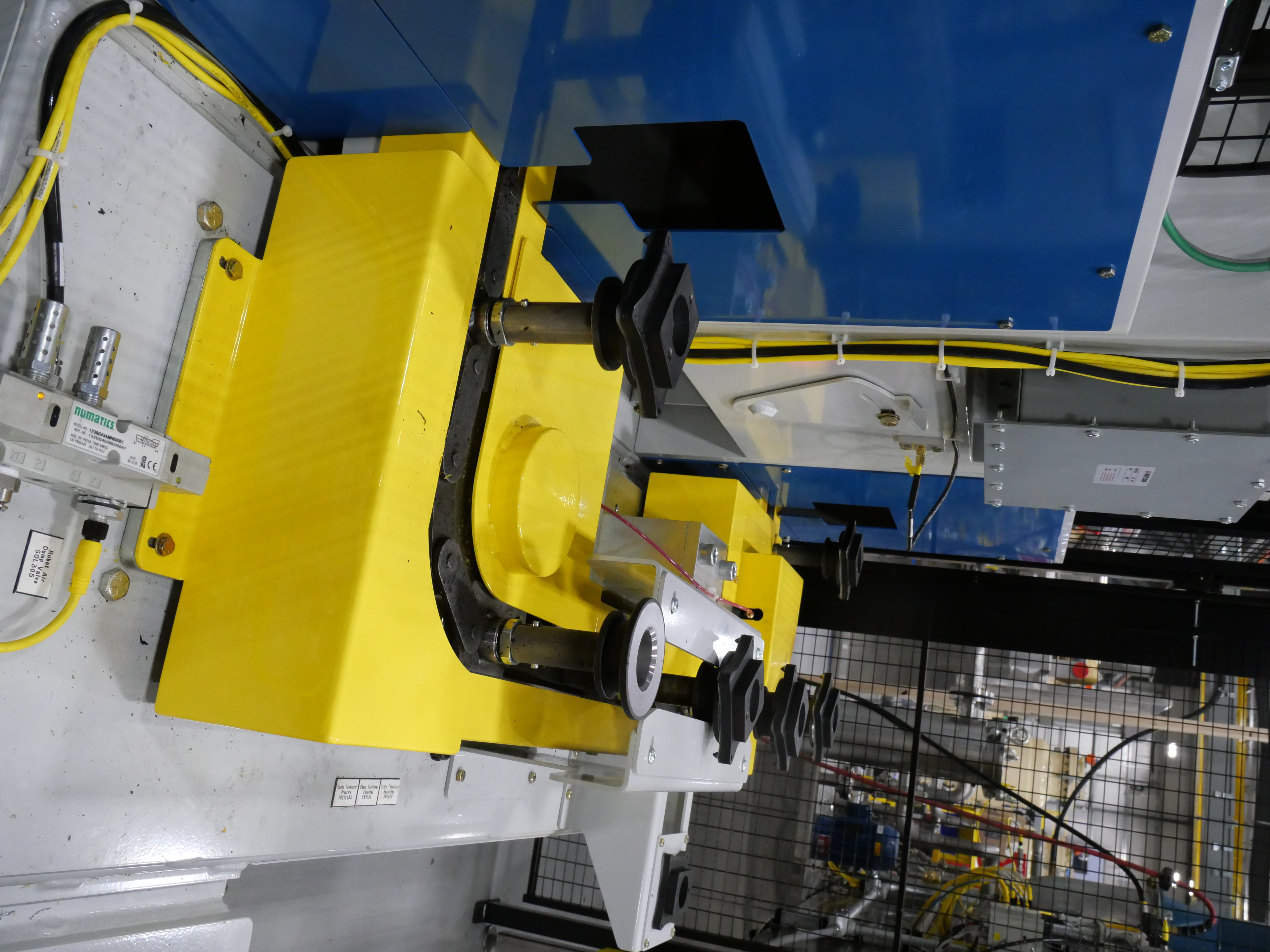
Specs & Features
Footprint – 17’W x 23’L x 11’8”H
Utilities
- One (1) 1” airline at a minimum of 60psi (clean and dry)
- One (1) 16” exhaust run out of building
- One (1) 1” water line for fire suppression system
- One (1) 480v, 3PH, 125A electrical drop
Oven
- The maximum oven temperature is 130°F
- Electric convection heating system and forced air
- The oven is designed to maximize paint coverage and thickness, and the heating systems are designed not to damage the coating.
Spray Booth
- Spray guns can be fixed-mounted, servo-mounted, or mounted to FANUC Paint Mate 200iA/5L robots equipped with an auto-purge cycle.
- Pneumatic clamp cylinder and roller assemblies are provided in each spray station to engage the spindle base and ensure fixture centerline with the spray gun.
- The controlled spray booth air flow helps maximize the paint thickness along with the spray gun and booth cleanliness.
- Booth air flow will automatically adjust speed to maintain the required flow. A Magnehelic gauge will be used to measure atmospheric pressure change.
- Part rotation will be controlled and adjustable at the HMI with two rotations in front of each gun as a minimum target (there is also a non-rotate spindle option).
- One (1) light in the spray booth allows operators and maintenance to visualize the process easily. The light is protected from overspray and is approved for the environment.
- The Spray Booth is designed with adjustable airflow to minimize material build-up inside the booth.
- The booth filter system comprises a roll pad filter and a box filter.
- Part presence sensors allow the machine to spray when a part is present. If a part is not present and the machine is in automatic mode, the machine will not spray.
- The booth's exhaust design prevents the LFL (lower explosive flammable) from exceeding 25%.
- The Spray Booth design and airflow are such that the pressure difference from outside to inside the booth does not exceed three (3) inches in the water column.
Fluid Delivery
- Separate pressure pots for each material with all gun connections.
- Two (2) Devilbiss 15-gallon pressure tanks with agitator.
- Four (4) Krautzberger RA6 w/100 mm 45 Degree Extension spray guns with 0.8mm needle.
- For optimum part coverage, two (2) guns are used per station (two for the primer station and two for the top coat station, for a total of four Spray guns).
- Adjustable HMI on/off timer for pressure pot agitation
- The paint pot agitation automatically maintains the HMI's speed (RPM).
- Pressure pot fluid level is monitored and displayed on the HMI. When the level reaches 20%, the HMI will flash an alarm to the operator. At 10% fluid level, the machine will fault until the level is replenished to not less than 75% of the maximum.
- When a primer or top coat must be added to the pressure pots, the HMI will guide the user through safely removing the lid.
- Before allowing the COE to operate after adding the primer and top coat, the HMI will request that the operator input the approximate gallons of material added to the pot.
- Inline Graco fluid filters ensure no foreign objects enter the system.
- Fluid pressure, fan air, atomization air, and trigger control can be accessed through the HMI and will be controlled separately for each gun. (FAN pressure is not available in the extension gun).
- Pressure pot, fan air, and atomization pressure are set up through a part recipe.
- Pot pressure and mechanical flow control on individual guns regulate fluid pressure. All guns will have the same pressure.
- The fluid recirculation pump is provided when the spray process is not operating to prevent materials from settling.
Safety Features
The system conveyor utilizes cover guides to minimize the moving components near an operator. The operator area has multiple safety devices, including a mushroom button emergency stop and pull cord E-stop. The oven and coating booth utilize safety internal locked doors.
Trust Arnold Machine with Your Coating System Needs
Arnold Machine understands that choosing the right coating system is crucial for your business. We offer a range of solutions and expert guidance to ensure you find the perfect fit for your needs. Our team is dedicated to providing exceptional service and support, from initial consultation to installation and beyond. Contact us today to discuss your coating system requirements and discover how we can help you achieve efficient and high-quality results.
Chain-on-Edge Conveyor FAQ
-
Can the system accommodate water-based material and/or solvent-based material?
-
What types of surfaces can this system coat?
-
What should I expect for preventive maintenance?
Other Coating Systems and Related Machines
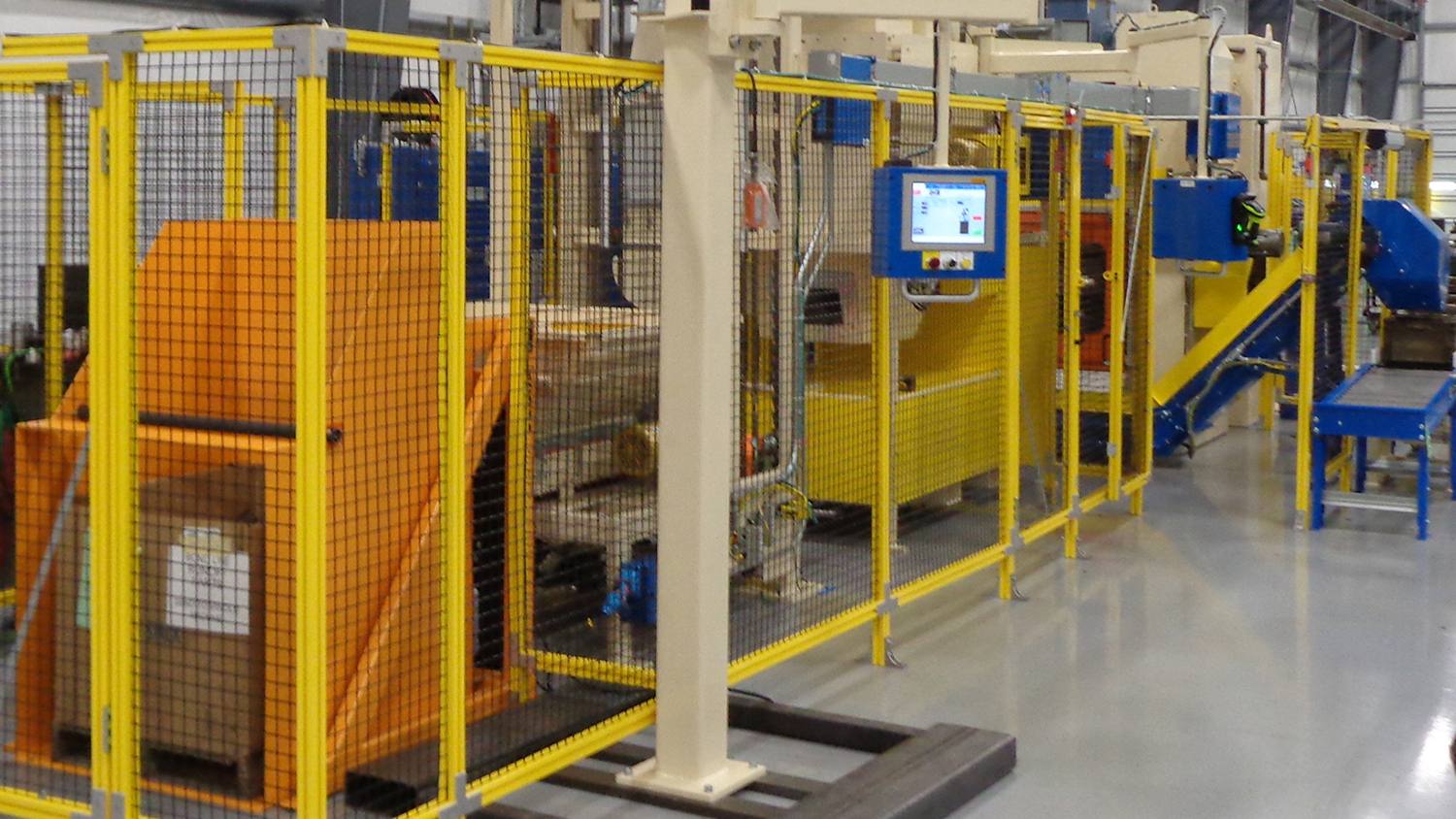
Tumble Spray Coating Systems
Achieve unmatched protection and efficiency with our fully automated Tumble Spray systems. Experience 100% coverage, significant labor savings, and consistent results in your coating operations.
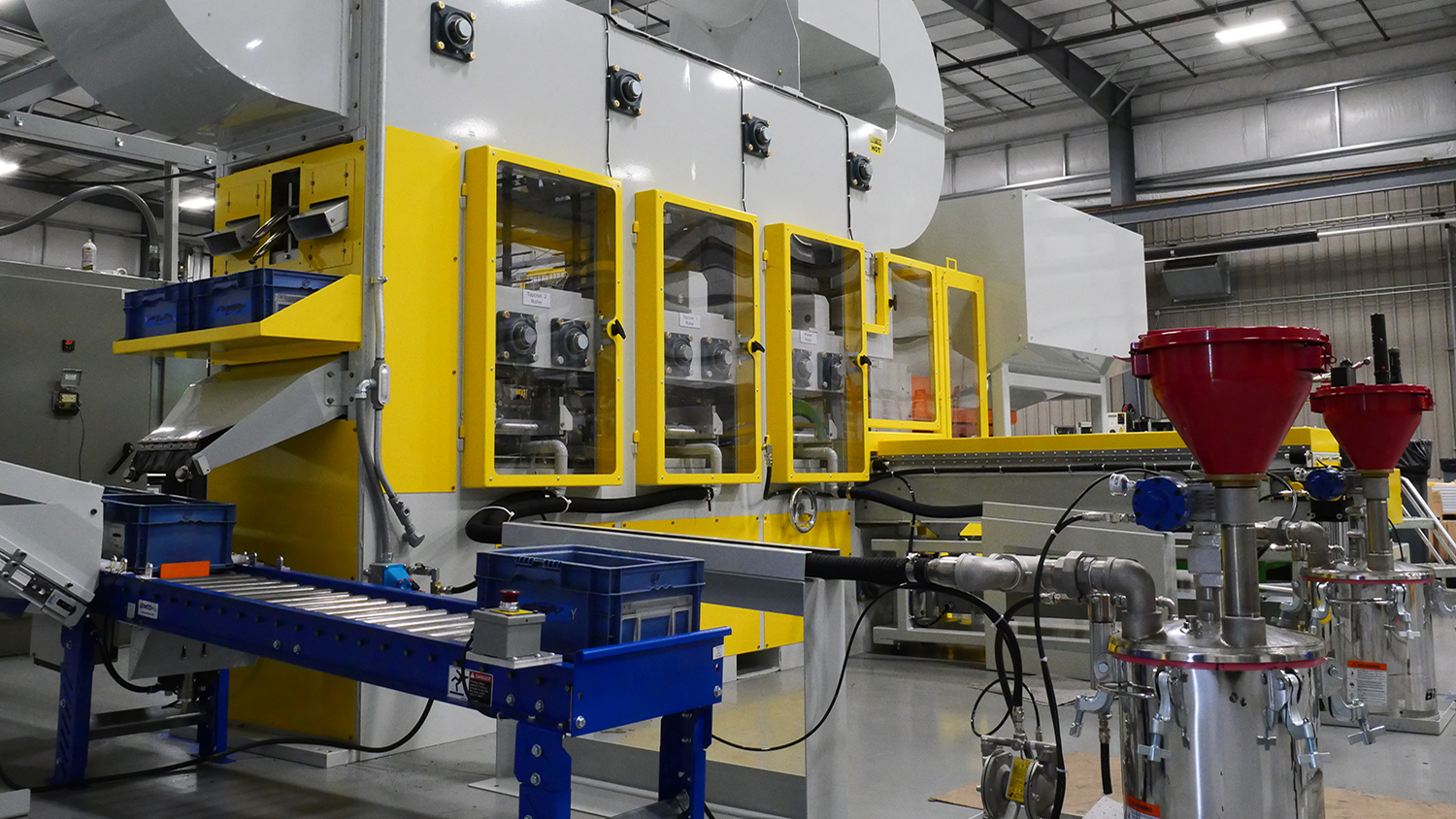
Roll Coater Systems
Roll Coater Systems deliver consistent coating results in high-volume production environments. They integrate smoothly into your production line for optimal results.
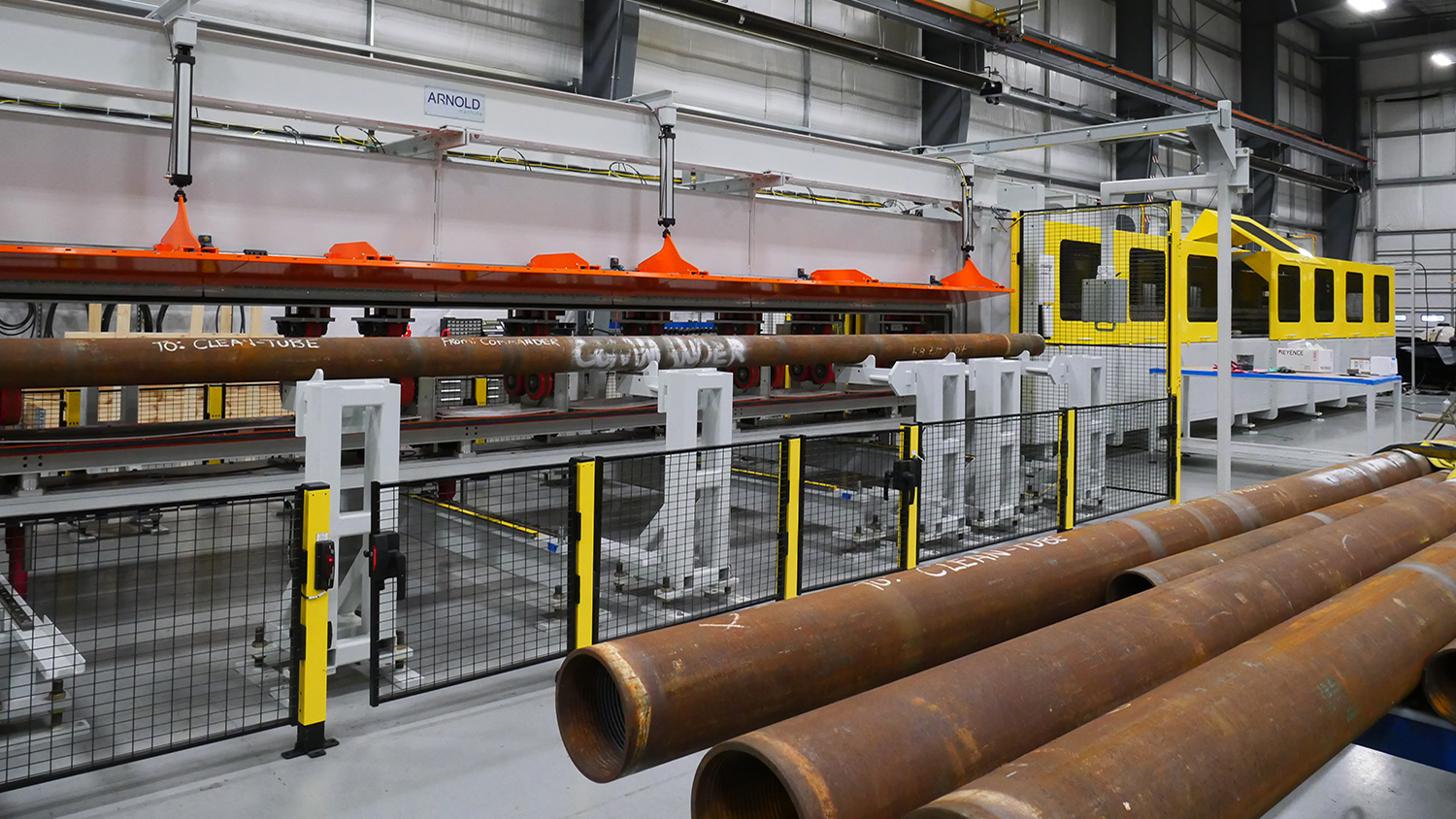
Interior Diameter (ID) Tube Spray Machines
Maximize your tube coating efficiency while minimizing material expenses. Safeguard your workforce with a controlled and secure coating process.
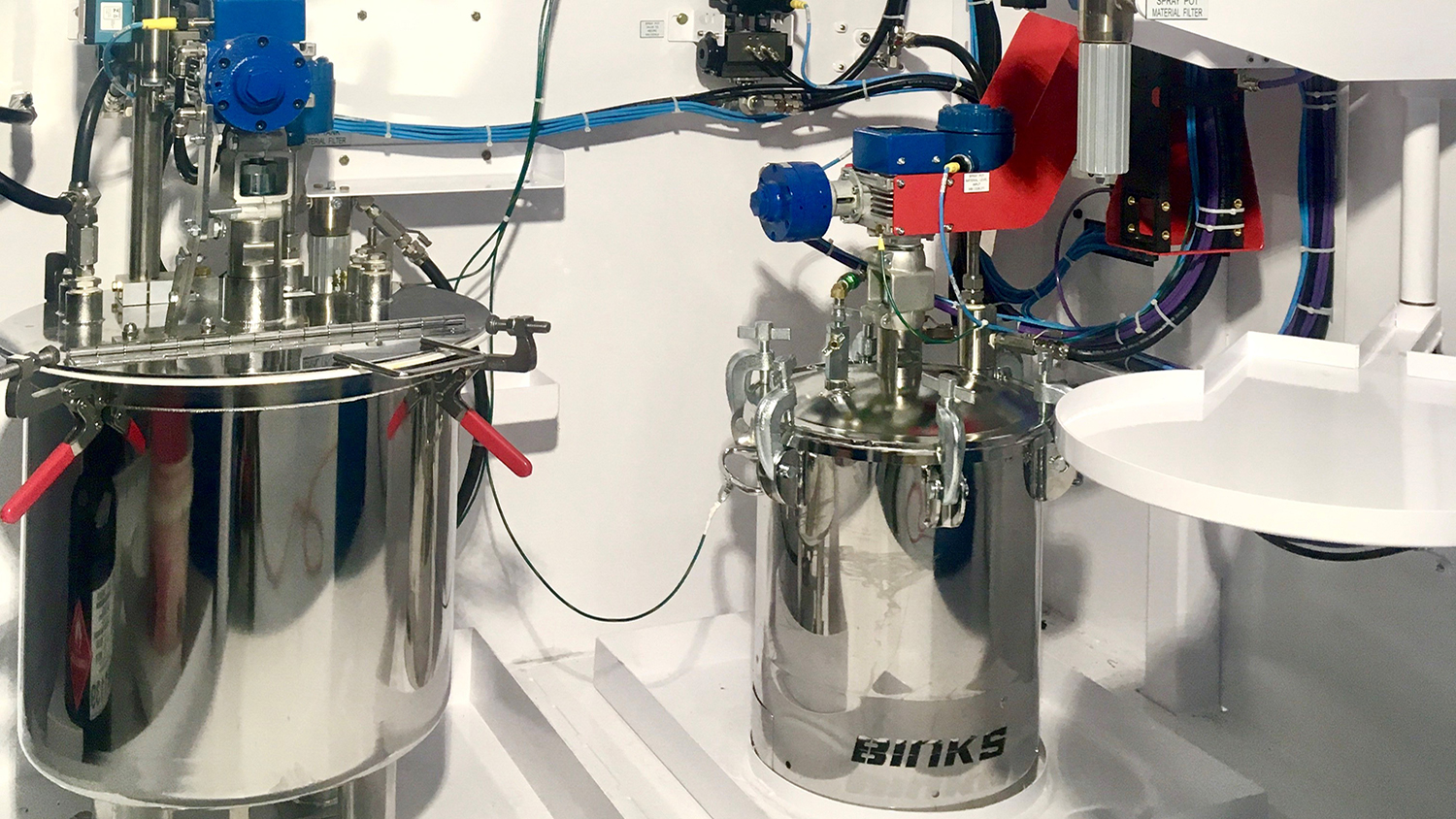
Automatic Viscosity Bulk Mixing Stations
Maintain consistent material viscosity to optimize your production. With our dependable, automated solution, you can achieve reliable coating results and minimize downtime.
Featured Posts
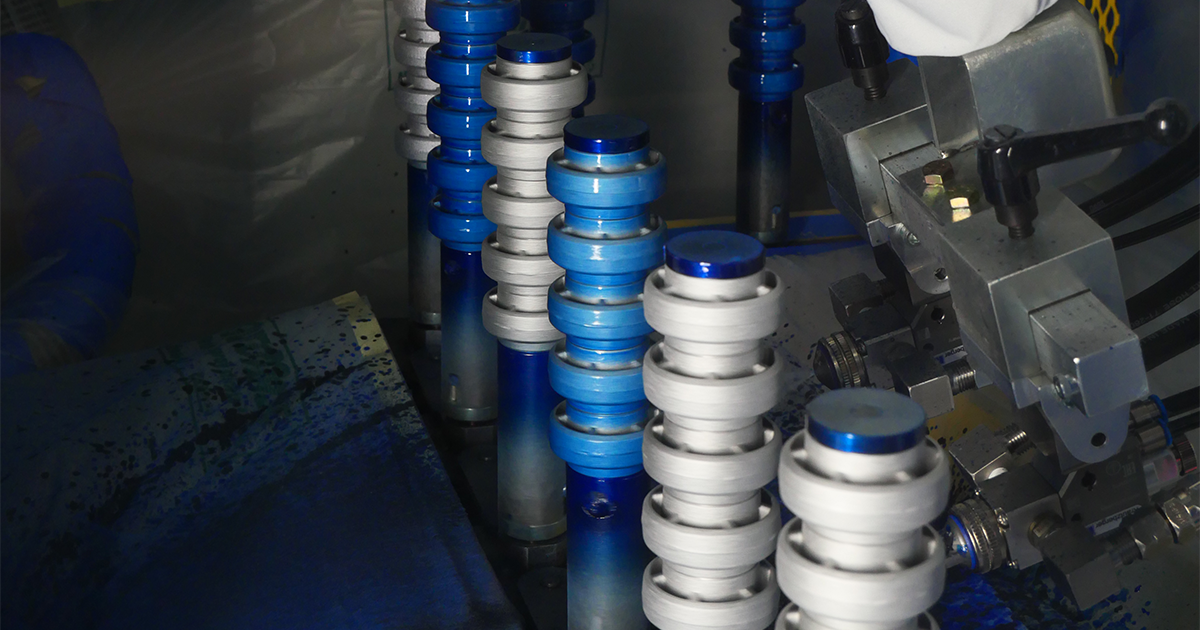
Chain on Edge System for Adhesive Coating
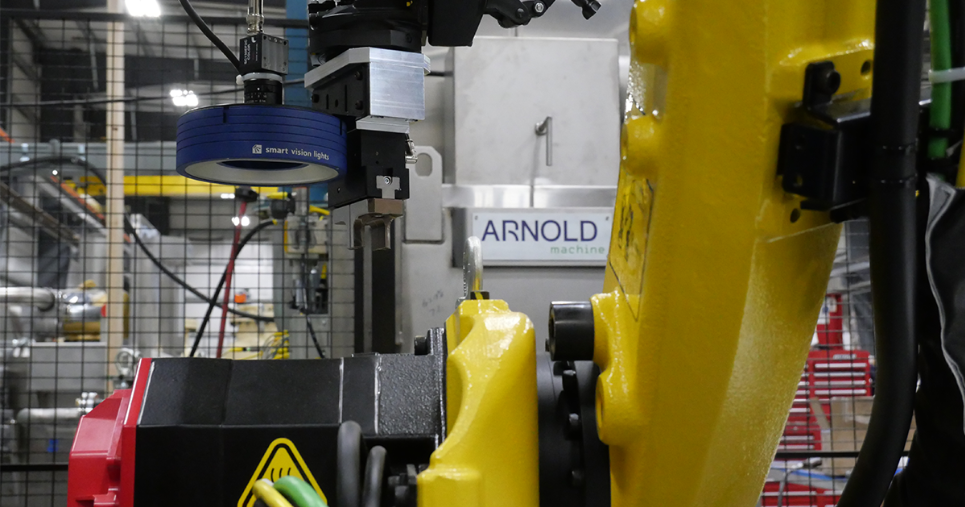
How Much Does a Chain On Edge Paint Line Cost?
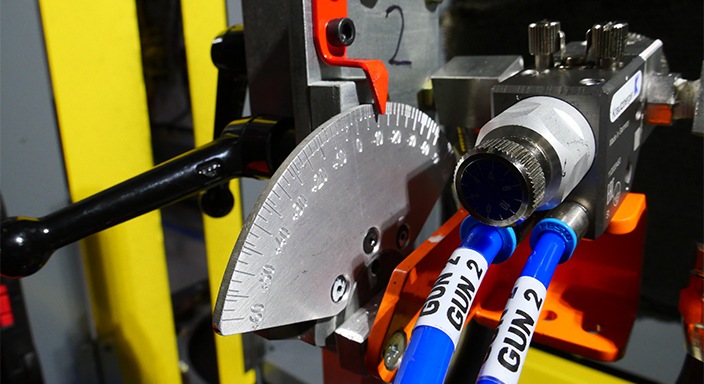
Automated Rubber-to-Metal Adhesive Spray Coating System
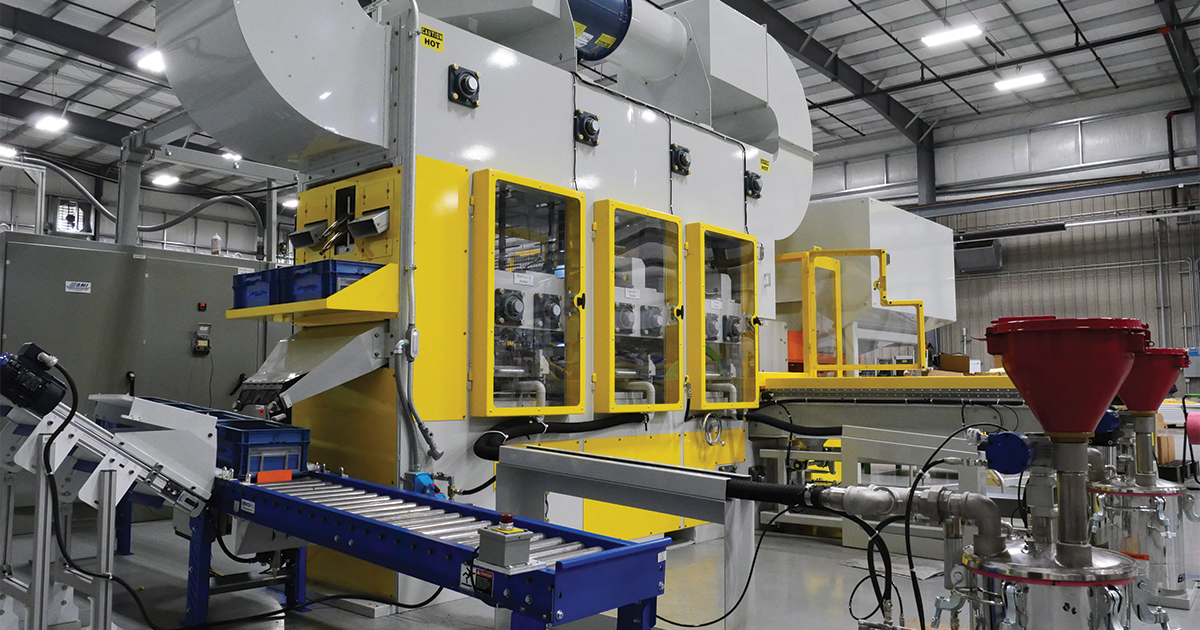
Choosing the Right Paint Conveyor System: Factors to Consider
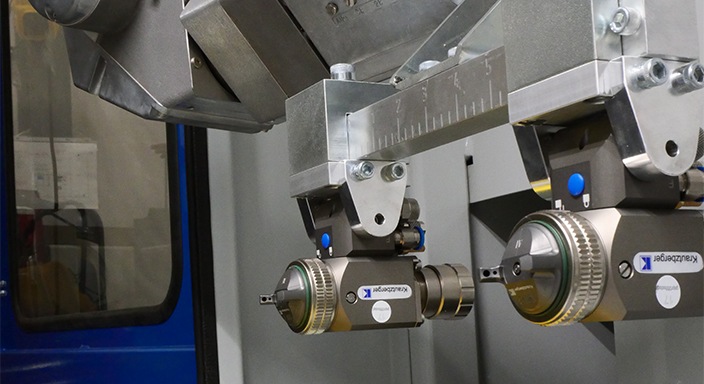
Automated Chain-on-Edge Spray System
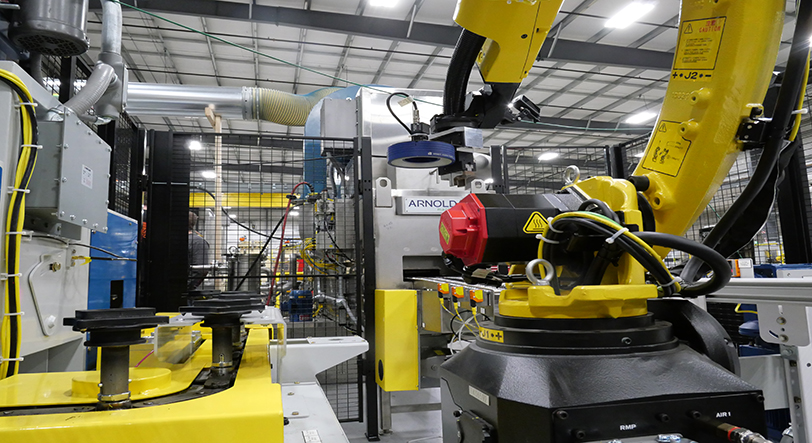