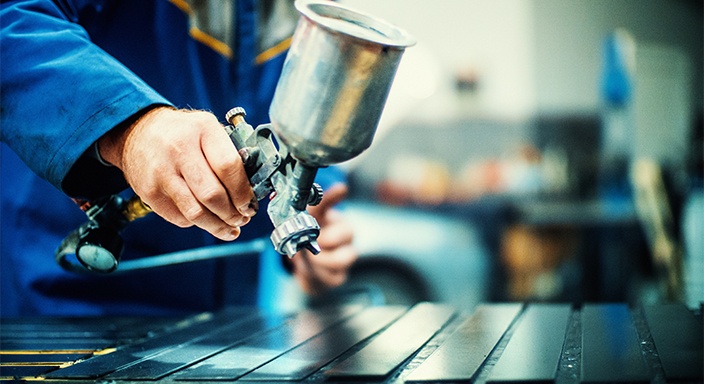
Automation or Human Labor? Here’s What to Consider
Automation has changed the dynamic between man and machine. But woeful stories of people losing their jobs to robots overlook a key fact about today’s economy: Automated manufacturing systems have played an outsized role in the recovery from the 2008 recession and continued strength of the American economy.
The writing is on the wall: Automation is here to stay. In the case of some businesses, their survival depends on it. Meanwhile, the world’s leading thinkers say businesses are better served finding ways to transition their human workforce into roles where they can excel.
If you’re considering automation, read on for some guidance on how to integrate it where it’s most appropriate.
Automated vs. human labor.
Determining cost of automation vs. cost of labor
Cost is the most common starting point in these decisions. Begin by clearly defining your goals and identifying the indicators used to gauge success (these might be revenue targets, scrap rates, rework requests or downtime / uptime ratios). These metrics are the key impartial benchmark you can refer to as you decide whether an automated or human setup is best for your business.
Next, collect as much information as you can about all the costs associated with human labor and automated systems.
- The costs of human labor.
- Wages and wage inflation.
- Training and non-wage benefits.
- Worker’s compensation insurance.
- Payroll taxes.
- Auxiliary safety equipment.
The costs above are relatively simple to determine. But managers need to account for some intangible costs, too. These are harder to quantify but just as critical to your comparison:
- Safety risk due to human error.
- Product loss / rework due to human error.
- Slower pace of human labor compared to automated processes.
- The costs of automated processes:
- Up-front hardware and software investment plus installation.
- Operator training and wages.
- Ongoing maintenance.
- Planned or unplanned stoppages due to part changeouts for
- flexible automation systems.
Automated systems come with fewer unknowns and intangibles. This doesn’t necessarily mean they’re better, and it doesn’t always make them the most cost effective choice. However, it can help you reduce unnecessary workforce maintenance costs (due largely to employee churn and redundant training expenses) and redirect your workforce toward tasks in which people can excel.
Calculating ROI for an automated vs. manual System
The key question is whether the up-front cost to implement automation will pay off within the lifecycle of the system. ROI can come from more than one place:
- The replacement of enough labor to result in cost savings that make the automated system worth the expense.
- The increased quality and capacity —and ensuing increased revenue potential— an automated system can bring that outweighs the lower-cost but lower-volume manual labor setup.
- Often, the combination of reducing labor and increasing high-quality output will result in a positive ROI in the long term.
Hypothetical ROI calculation
The following calculation is an example meant to serve as a template for your application. Costs of custom automation equipment can vary widely depending on your needs. Note that this calculation does not factor quality, throughput, interest, depreciation, maintenance, training, etc.
Suppose you have a partially manual system requiring three skilled operators working three shifts per day. Assume that the cost per operator is $50,000 a year for a total annual labor expense of $450,000.
Alternatively, suppose you identify a fully automated system that costs $400,000 to design, build and install. It will need one unskilled operator at $35,000 a year for two shifts per day, totaling $70,000 a year. Training is relatively inexpensive because the operator simply loads and unloads the machine. The total expense for automation is $470,000, translating to a first year ROI of -$20,000 ($470,000 automated system minus the $450,000 partially manual system).
However, the payoff begins in the second year because there is no capital investment for the automated system. With reduced labor costs, yearly production expenses are significantly lower compared to the manual system. Over two years, production with the automated system costs $540,000, while the manual system would’ve cost $900,000. That represents a return of $360,000, or a 90% ROI.
Is automation right for your process?
Automated systems are generally recommended for high-volume orders. It’s an even more attractive option when consistent quality and repeatability in a production run is paramount. Automated systems that increase consistency and reduce scrap rates can be further engineered to inspect parts before they proceed through the rest of the manufacturing process. If there’s an issue, the part is automatically scrapped before more components are added or further machining takes place, saving time and material input. This will come at significant cost up-front, but the machine’s high capacity and minuscule error rate mean it will begin to pay itself off.
Human operators cannot perform at maximum speed their whole shift and expect to produce perfect parts every time. We wouldn’t want them to try. The effects could be disastrous.
On the other hand, human labor generally comes with lower upfront costs and is valuable for low-quantity runs, unique one-off projects or research and development trials. In addition, operators can offer real value for processes that require critical thinking or where automation is not economical to integrate.
The automotive industry has embraced automation and will continue integrating it due to the better quality, efficiency and return on investment it provides. Accordingly, industry suppliers who choose to integrate automation have a leg up on the competition.
Such was the case when Arnold Machine built an automated assembly system for an engine mount for a major automobile manufacturer who wanted to decrease labor while increasing the production rate and quality. The machine we built utilized a FANUC robot, hydraulics and custom tooling that removed operators from difficult-to-verify processes and ultimately reduced the cycle time from more than a minute to less than 45 seconds.
For our customer, it was well worth the investment.
To learn more about the benefits of automation, read our guide to time and cost savings in manufacturing. If you’re looking for specific guidance on how you can automate your manufacturing processes, contact our team.