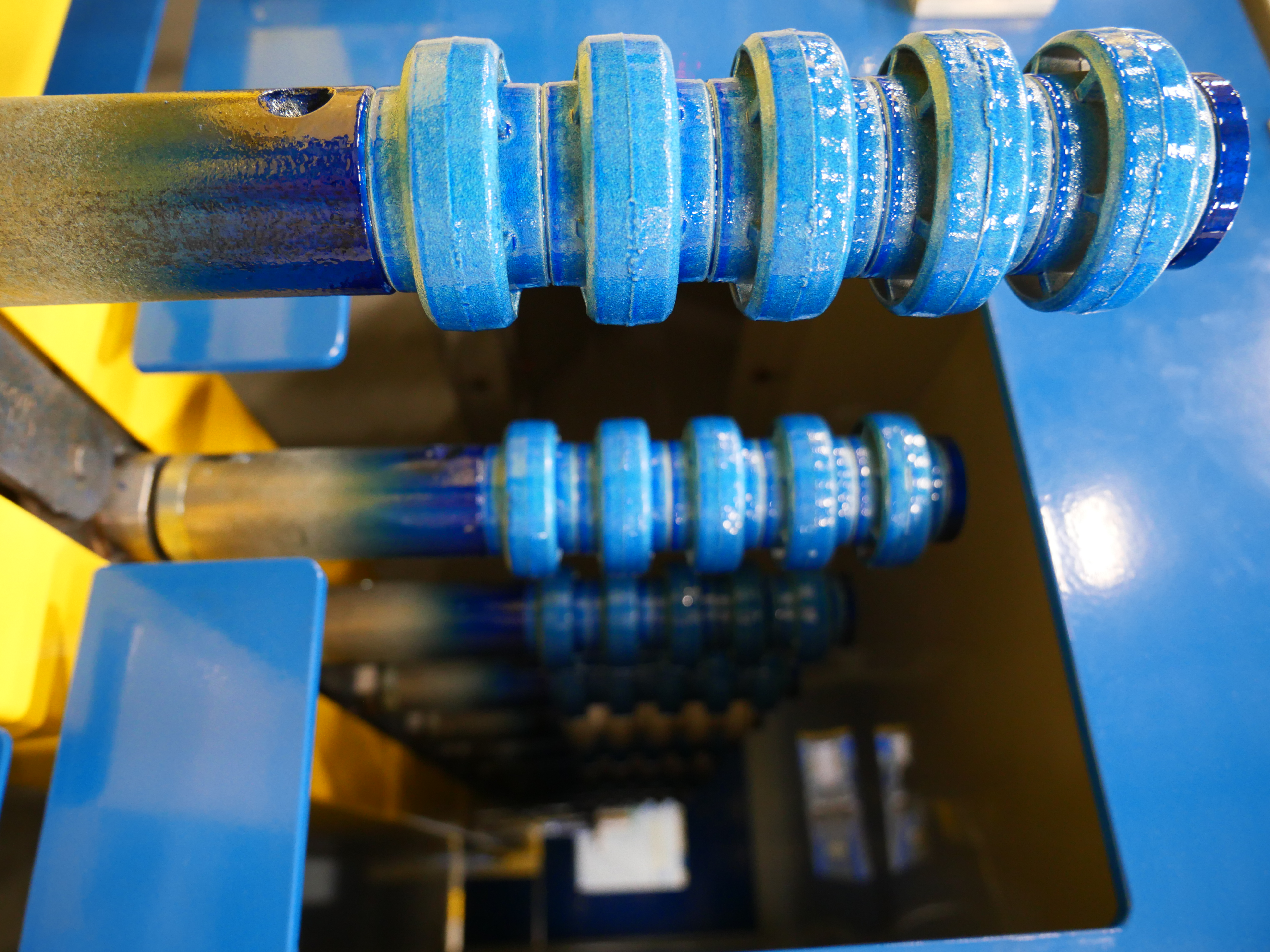
Process Control in Automated Adhesive Dispensing Systems
Automating the application of adhesives to components across manufacturing sectors has provided suppliers an opportunity to maximize their value to OEMs in two important ways:
- Quality, consistency and speed are optimized across production runs while the risk of human error is eliminated.
- The unpredictable (and ever-rising) direct and indirect costs of employing human labor are replaced by more predictable and controllable system costs.
To make sure these ideal scenarios become reality in your operation, it’s important to understand that automated adhesive dispensing systems depend on fine-tuned process controls. And the best way to implement them is through partnership with an experienced automation provider who understands exactly what you need.
Automated adhesive dispensing systems process control.
Key process control variables
Whether an adhesive is sprayed or applied as a bead, automated adhesive dispensing systems must account for many variables to be successful. If these aren’t monitored and managed, the benefits of automating the process are erased. The main variables are summarized below.
Adhesive temperature & viscosity
These are separate variables, but the way they relate has a major impact on automated adhesive dispensing. The viscosity of an adhesive is critical because if that value is off—even just slightly—it can have an adverse ripple effect throughout the rest of the process.
If it’s too viscous, the adhesive may not travel through the applicator at the right pace or volume. Increasing air flow to compensate for sluggish movement can introduce unpredictability and wear out a system more quickly. On the other hand, if adhesive isn’t viscous enough, it may travel through the applicator too chaotically and result in unpredictable application. In addition, adhesive may not optimally adhere to the part substrate if it’s not viscous enough.
Automatically controlling the viscosity and temperature of an adhesive is imperative for optimizing adhesive application.
Substrate temperature
It follows that part substrate temperature should also be controlled. A temperature mismatch between a part substrate and the adhesive could result in the adhesive not adhering to the substrate as designed. If this mismatch isn’t noticed and corrected, the delivery of defective parts is the least of your worries. In some situations, part failure could be fatal.
To ensure that part substrate temperatures are compatible with adhesive temperatures, automated adhesive dispensing systems often include ovens or other heating stations built in.
Air flow
Air management is critical to the safety and success of automated adhesive application in a few ways.
First, air flow management helps in the adequate heating of parts to the predetermined temperature at which adhesive application is most successful.
Second, most industrial adhesives contain volatile organic compounds (VOCs) which are harmful to humans and are strictly regulated by governmental authorities. Good air flow management in adhesive application captures VOCs, preventing their release into work areas or into heated areas within a system.
Third, controlled air flow boosts the consistency of spray application and enhances the overall safety of the automated system.
Part travel and orientation
The basic movement of parts through the stages of a process is critical to the success of automated adhesive dispensing. How parts move varies widely depending on what kind of automated process is in place:
Index systems are designed as either dial or chain-on-edge, sending parts past application guns. In some settings, parts are manipulated on the dial or chain if the spray gun is fixed in place to ensure specified adhesive coverage. In others, parts can stay stationary while the application gun has single-axis motion or is mounted to a robot with multi-axis motion capability.
Tumble spray systems cover whole surface areas of simple parts via a tumble chamber not unlike a household washing machine or dryer. They’re a high-volume alternative to dip lines.
Robotic spray systems are best specified for parts with complex geometries that require “smarter” application with the help of robots.
Regardless of the system type, the orderly movement of parts must occur in concert with all the other operations in a system. As we describe below, that complex choreography is managed thanks to advanced computers, cameras and sensors integral to any automated system.
Measuring automated adhesive dispensing process control
High-tech tools keep automated adhesive dispensing systems operating as designed. Sensors, gauges and cameras placed throughout automated systems monitor thousands of variables in real time, providing critical information including:
- The viscosity and temperature of adhesive material prior to application.
- The temperature of part substrates.
- How rapidly and at what volume adhesive is emitted from the applicator.
- Changes in system air pressure.
- Orientation of parts at various stages in the process.
- Whether the bead or spray pattern of applied adhesive meets specified parameters.
These data are organized in a system’s programmable logic controller (PLC). This is effectively the brains of an automated system, capable of receiving input parameters and then telling all the automated parts of an operation what to do.
PLCs also perform critical quality control functions at various stages in the process. Because the actions of automated systems are dictated by recipes loaded into the PLC, those actions can be stopped if sensors that communicate with the PLC detect variables not included in the recipe. Automating this go / no-go function means production can stop the moment a problem is noticed, significantly reducing material waste. And because a computer makes the decision, subjective interpretation by human inspectors is eliminated from the equation.
What makes a true automation partnership?
If you’re considering integrating an automated adhesive dispensing system into your facility, you’ll need an automation partner. But how do you know who’s for real?
The right automation partner proves its worth right away, digging into the specifics of the operation you hope to automate and sharing examples of how similar challenges have been met. Arnold Machine provides true partnership, helping customers design and build automated systems that meet their present and future needs. We also round out our expertise with key integration partnerships with the industry’s biggest players, ensuring your automated processes are set up for success for as long as they’re in service.
Read this article to see how we helped a real-world customer integrate an automated spray machine into their facility.