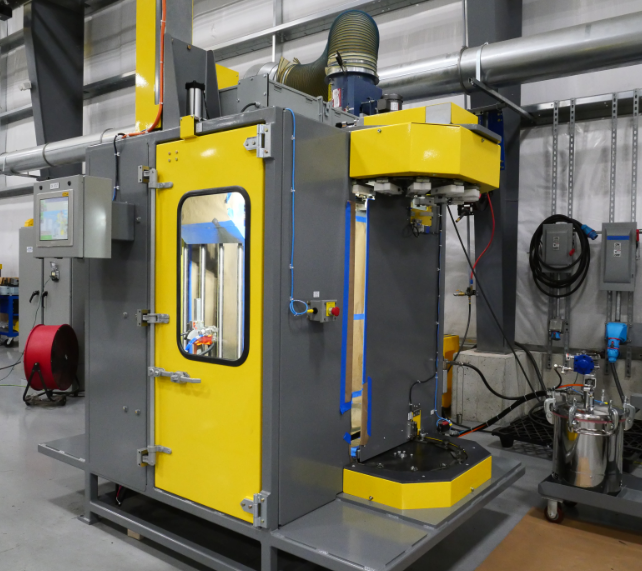
How to Control the Thickness of an Adhesive Bond Line
Achieving consistent adhesive bond line thickness is a common problem in many manufacturing industries. Line variations can compromise the adhesive bond integrity, durability, and performance, leading to costly rework or product failures. It’s challenging to deal with wasted materials and inconsistent results, especially where precision is critical.
Fortunately, advancements in adhesive application technology offer a reliable solution. Automated spray coating systems provide unparalleled precision, improved transfer efficiency, and consistent control. Read on to learn more about controlling adhesive bond line thickness.
WHY BOND LINE THICKNESS MATTERS
Applying the correct thickness is essential for maintaining the quality and effectiveness of the coating process. If the layer is too thin, it may not provide a strong bond, leading to issues like peeling or delamination. At the same time, excessive application can cause surface defects, longer curing times, and inefficiencies in production.
The proper thickness promotes uniform bonding, consistent mechanical properties, and proper curing. These factors are essential for durability and product performance, particularly in demanding industries such as automotive or aerospace. For example, most adhesive coating requirements range from 0.4 mils to 1.2 mils overall thickness (equivalent to 0.0004 to 0.0012 inches) and leave very little margin for error.
Ensuring proper bonding and curing results in smooth coatings with minimal imperfections. It also enhances adhesive efficiency and supports compliance with safety and environmental standards. Overall, optimizing adhesive thickness improves the coating process's quality and effectiveness.
THICKNESS CONSIDERATIONS
Adhesives are often used in automotive manufacturing to bond rubber components to metal parts (e.g., seals or bushings). The bond line is critical for a strong and reliable connection that can withstand vibrations, thermal cycling, and chemical exposure. A too-thin adhesive layer may lack the strength to prevent the rubber part from failing or detaching.
Conversely, a too-thick layer may reduce flexibility and performance in high-stress areas. Maintaining the correct bond line thickness ensures the adhesive can absorb and distribute stresses efficiently, improving the component's durability and longevity.
Composite materials are often bonded to metals or other composites in aerospace manufacturing. Precision in bond line thickness is vital here. An overly thick adhesive layer could add unnecessary weight and affect aerodynamic properties.
On the other hand, a layer that is too thin might compromise bonding strength and structural integrity. Proper thickness enables the adhesive to act as a strong yet lightweight bonding agent, contributing to the aircraft's overall performance and safety.
TRADITIONAL METHODS FOR ADHESIVE APPLICATION
Many industries employ alternative methods to control the thickness of adhesive bond lines.
These include:
Spray Application: The adhesive is sprayed onto the metal surface with precise control over the spray gun's settings, including nozzle size, spray pressure, and distance from the surface. This allows for uniform application of the adhesive.
Dip Coating: The metal part is dipped into a bath of adhesive, and the thickness is controlled by adjusting the dipping time, speed, and viscosity of the adhesive.
Roller Coating: The adhesive is applied via a roller, which allows for control over the thickness of the adhesive layer based on the roller's pressure and speed.
Brush or Manual Application: Operators carefully apply the adhesive to achieve the desired thickness, though this method is less automated and labor-intensive.
CHALLENGES OF TRADITIONAL METHODS
Controlling the thickness of an adhesive bond line presents numerous challenges for companies using traditional adhesive application methods. These challenges stem from several factors, including:
ACHIEVING UNIFORMITY
Companies face several challenges when trying to control the thickness of an adhesive spray coating application. One of the main difficulties is achieving consistent uniformity, as variations in spray pressure, nozzle size, or distance from the substrate can result in inconsistent adhesive layers.
ENVIRONMENTAL AND MATERIAL VARIABILITY
Environmental factors, such as temperature and humidity, can also influence how the adhesive is applied and behaves during curing, leading to uneven coatings. Maintaining the correct application speed and spray technique is essential, as human error or improper machine settings can result in excess or insufficient adhesive.
Companies also must contend with material variations. Different substrates may require different amounts of adhesive, adding complexity to the process. Cost constraints often push for minimizing adhesive waste while making precise control more challenging. All these factors require ongoing calibration, monitoring, and adjustments to deliver consistent coating quality and performance.
OPEN-TO-ATMOSPHERE CONTAINERS
When an adhesive is being used from an 'open to atmosphere' container, the evaporation rate of solvent or waterborne materials can affect the material viscosity, leading to inconsistent spray properties and unrepeatable coating thickness.
AUTOMATED SPRAY COATING SYSTEMS: TAILORED SOLUTIONS FOR EVERY APPLICATION
Automated spray coating systems are available in various configurations to suit the unique needs of different manufacturing processes. Each system enhances precision, efficiency, and consistency while addressing specific operational challenges. Below are some of the configurations we offer:
CHAIN-ON-EDGE CONVEYORS
Our Chain-on-Edge (CoE) systems deliver unmatched efficiency to optimize your operations. These systems improve material flow, reduce labor costs, and provide a strong return on investment, making them ideal for high-volume production.
TUMBLE SPRAY COATING SYSTEMS
Tumble Spray Coating Systems ensure 100% coverage with minimal waste. By eliminating manual labor and maximizing efficiency, these systems provide consistent and reliable results for complex geometries or irregularly shaped parts.
ROLL COATER SYSTEMS
Roll Coater Systems are designed for high-throughput production environments. They minimize waste while providing superior coating precision, seamlessly integrating with your existing processes for maximum productivity.
INTERIOR DIAMETER (ID) TUBE SPRAY MACHINES
ID Tube Spray Machines optimize the internal coating process for tubes, ensuring uniform application and reducing material costs. These systems also enhance safety and deliver high-quality finishes, meeting the demands of modern manufacturing.
BENEFITS OF AUTOMATED SPRAY COATING SYSTEMS
Automated spray coating systems deliver unmatched precision and reliability in adhesive applications. They enhance manufacturing processes by streamlining operations and producing consistent, high-quality results.
Their advantages include:
FLOW RATE CONTROL
Monitoring the flow rate of adhesive coating systems ensures consistent application, improves product quality, and reduces waste. It enables real-time adjustments to optimize adhesive usage, minimize defects, and enhance process efficiency. Additionally, it aids in the early detection of issues, supports regulatory compliance, and contributes to cost savings and sustainability by reducing material waste and energy consumption.
SPRAY PATTERN OPTIMIZATION
Optimizing an adhesive coating system's spray pattern results in uniform coverage, improving bonding quality and reducing material waste. It enhances process efficiency by minimizing overspray and preventing defects caused by inconsistent application. Electronically controlled devices monitor, maintain, set, and adjust fluid, pot, and fan/atomization pressures to produce optimal outcomes.
COATING THICKNESS PRECISION
Precise control of dry film thickness in coatings is achieved through several key factors. Preheating incoming products is crucial for maintaining consistent part temperature, regardless of seasonal variations. Heating parts before the coating process supports uniformity in coating application, directly affecting the dry film's final thickness and quality.
The system incorporates electronic devices to fine-tune various process parameters, such as fluid, pot, and spray gun settings. These adjustments significantly influence how the coating material is applied. Continuous monitoring and adjustments ensure that each coating layer is applied consistently, achieving the desired dry film thickness with precision.
ADDITIONAL COATING PARAMETERS
The system begins by preheating parts so that all components receive adhesive consistently. This promotes uniform application regardless of external temperature fluctuations.
Additionally, it controls coating parameters such as fluid, pot, fan, and atomization pressures through advanced electronic controls. These exact settings can be saved within a recipe to provide repeatable and reliable results. Optional and customizable features allow end users to tailor the system to their specific needs.
WHY CHOOSE ARNOLD MACHINE FOR YOUR ADHESIVE COATING NEEDS
At Arnold Machine, our extensive industry experience is our greatest asset. With over 20 years of expertise in adhesive coating applications, we have built a reputation for delivering reliable, high-quality solutions tailored to our customers' unique needs.
Our team collaborates closely with leading adhesive manufacturers to verify that each system we design and implement provides optimal performance and compatibility. This partnership keeps us at the forefront of advancements in adhesive technology and allows us to recommend and supply solutions for the most demanding requirements.
In addition, we strongly emphasize controlling process variables to achieve consistent, repeatable results. From precision application techniques to system integrations that enhance efficiency, we focus on solutions that offer exceptional quality and long-term value for our customers.
ELEVATE YOUR ADHESIVE BONDING PROCESS TODAY
Automated spray coating systems provide superior control over bond line thickness, maximize efficiency, and produce consistent quality in adhesive bonding applications. They’re designed to meet the demands of modern manufacturing with advanced features that generate reliable and repeatable results.
Arnold Machine excels in adhesive coating technology and delivers tailored solutions for complex manufacturing challenges. Our focus on precision and reliability ensures consistent results that enhance production processes and product quality. Click below to learn more about our innovative systems.