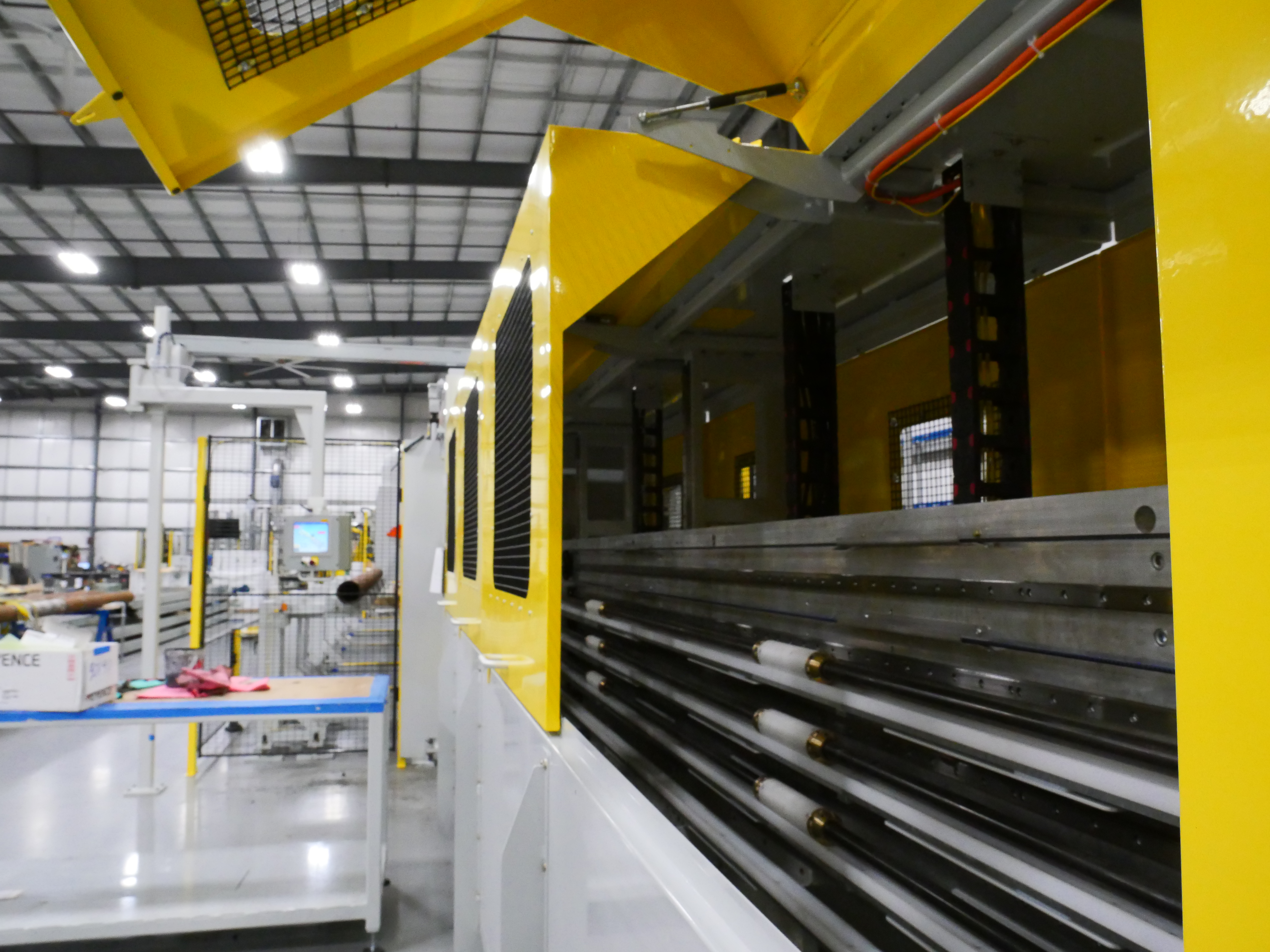
BEST COATING SYSTEM FOR PIPE COATING IN THE OIL & GAS INDUSTRY
Oil and gas extraction equipment must endure extreme operating conditions in the field. These expensive specialized components present significant challenges for on-site repairs or replacements. Companies that manufacture these systems face considerable pressure to deliver long-lasting solutions.
Traditional pipeline coating methods often fail to adequately protect against wear or damage. Innovative advancements, such as Inside Diameter (ID) Tube Spray Machines, dynamically outperform conventional methods.
Read on to learn more about the best coating system for oil and gas pipes.
TRADITIONAL VS. MODERN COATING SYSTEMS
There are three types of coating systems that manufacturers use:
Traditional Coating
Spray coating and dipping are two common oil and gas pipe coating techniques. However, these approaches have significant limitations and challenges. They usually result in slow, wasteful, potentially dangerous adhesive application processes for down-hole tubes.
Traditional methods may result in manufacturing delays and low production capacity. Manual handling of materials can also pose worker safety hazards. Advanced coating solutions can help mitigate these issues by streamlining processes and reducing labor-intensive tasks.
Flow Coating
Flow coating is another common alternative. It involves the controlled application of a liquid coating that flows evenly along the inside diameter of the pipe. However, this method often produces a subpar dry film thickness and exposes workers to dangerous VOCs. Compared to modern systems, the difference in quality and consistency is a night and day difference.
Modern Coating
Innovative pipe coating technologies have been developed to overcome the limitations of conventional methods. Advancements include sophisticated robotic systems and cutting-edge materials. These modern solutions greatly improve efficiency, safety, and overall coating quality compared to traditional approaches.
The ID Tube Spray system addresses the numerous challenges traditional coating methods face. It offers superior performance and many benefits for pipe coating in the oil and gas industry.
How ID Tube Spray Machines Work
These cutting-edge pipe coating machines use a multiple-stage, automated system to ensure consistent and high-quality adhesive applications. It can handle adhesives and paints (water and solvent-based), including 2-component materials.
A typical workflow is as follows:
- The machine loads and preheats a tube for optimal coating adhesion.
- A spray lance extends into the rotating tube, applying an even adhesive or primer layer.
- The tube then enters a drying oven to cure the coating.
- If needed, a second spray booth applies a topcoat, followed by a final drying cycle.
- The system unloads the finished tube for further processing.
FEATURES AND BENEFITS
The ID Spray Coater system offers many features and benefits that set it apart from traditional coating methods:
Adaptability and Flexibility
This state-of-the-art pipe coating machine excels in environments with a high product mix and low volume production. It can automatically accommodate various part specifications and adjust on the fly. This capability eliminates the need for operator intervention during changeovers.
It also integrates easily with existing equipment and automation levels and can handle various pipe diameters and lengths. This helps to ensure that the system meets the unique requirements of any production environment.
The ID Coater can work with current blasting equipment or connect to existing ovens, minimizing disruptions to established workflows. This flexibility makes the system ideal for facilities looking to upgrade their coating processes without overhauling their current setups.
System Design Based on Pipe Dimensions
The system applies adhesive to the inside diameter of pipes for the oil and gas industry. It enables strong rubber bonding for applications like drilling and pumping. It offers two main setup options to handle various pipe sizes. Factors like pipe diameter, length, and desired automation level influence the optimal design. This ensures the chosen system maximizes efficiency and effectiveness for each client's unique application.
Integration with Existing Equipment
The ID Coater system is designed to integrate existing oil and gas production lines easily. It can be customized to work with current blasting equipment or connect to existing ovens. This feature allows for smooth incorporation into various facility setups.
The system's flexible design helps it coordinate efficiently with other equipment in the production line, minimizing workflow disruptions. As a result, the ID Coater is a great choice for facilities that want to upgrade their coating processes without completely overhauling their current systems.
Consistent Coating Thickness
Achieving consistent coating thickness is critical for effective pipe protection. The ID Coater system guarantees even distribution of coating material, tackling issues related to inconsistent DFT (Dry Film Thickness) that often trouble traditional methods. Its precision application methods prevent higher DFT readings at the top of the tubes, delivering reliable protection across the entire pipe surface.
Process Control
The ID Coater system offers advanced process control capabilities for the oil and gas industry. It mixes coating materials on demand, allowing operators to control levels and ratios. They can adjust RPMs, feed rates, and spray patterns to meet specifications.
Features like material flow monitoring and application validation ensure consistent dry film thickness and coating quality. It adapts automatically to different parts, making it ideal for high-mix, low-volume production environments.
Complete VOC capture in an enclosed spray booth addresses safety and environmental concerns. This design protects operators and reduces environmental impact while maintaining airflow, resulting in consistent coating thickness and quality.
Airflow Control and Enhanced Durability
Advanced airflow control within the enclosed spray booth is a key feature of the ID Coater. This management ensures a controlled environment crucial for oil and gas components used in underground drilling and pumping.
It contributes to repeatable dry film thickness and durable coatings, which are essential for preventing rust and degradation. The system maintains airflow during the application, creating a uniform coating that protects parts and minimizes costly failures.
Multiple Coating Materials
The machine can handle up to four coating materials simultaneously, enhancing its versatility for various oil and gas industry requirements. It features cabinets that store readily mixed materials for immediate use, allowing quick changes without interrupting production.
This capability is especially beneficial for facilities that produce a high mix of products and low volumes. It efficiently handles different project needs and adapts to various part requirements.
Efficient Material Use
The ID Coater system drastically reduces adhesive waste. Most of the coating material adheres to the pipe's inner surface. Traditional methods can waste around 50% of the material, costing between $50 and $100 per gallon. The ID Coater helps lower operational costs and improves sustainability for oil and gas companies.
Worker Safety
Worker safety is a top priority in the oil and gas industry. The ID Coater system enhances safety through automated processes. This helps to eliminate safety risks associated with climbing and handling volatile adhesives. Workers no longer need to manually handle heavy parts or be exposed to coating materials' VOCs. This automation leads to a safer work environment and reduced workplace incidents.
Streamlined Drying Process
The ID Coater system features a streamlined drying process. It significantly reduces the overall processing time compared to other methods. This efficiency improvement translates to higher production capacity and faster turnaround times.
These methods often require 10-12 hours from the first application to final drying. The ID Coater system completes the entire process in 1-2 hours. This dramatic reduction in processing time boosts productivity and operational efficiency.
Quality Control
Quality control is a key aspect of the ID Coater system. It provides real-time feedback on coating thickness and quality. Non-destructive testing occurs throughout the coating process. There is no need to sacrifice completed tubes for quality checks. This method saves materials and verifies that every coated pipe meets the required standards.
SUCCESS WITH THE ID COATER SYSTEM
A major global equipment manufacturer faced challenges with their adhesive application process for down-hole tubes. Their existing method was slow, wasteful, and posed safety risks to workers. We developed a five-stage automated system to address these issues.
The new system reduced processing time from 12 to 2 hours per part, significantly increasing production capacity. It also improved worker safety by eliminating the need for manual handling of heavy parts and exposure to volatile adhesives.
PRECISION COATING FOR OPTIMAL PIPELINE PROTECTION
Pipe coating is essential for the longevity and reliability of oil and gas infrastructure. The ID Coater system is the best solution for this critical application. It offers superior efficiency, safety, and quality control compared to traditional methods.
Arnold Machine is the leading expert in coating systems for the oil and gas industry. Our commitment to innovation and customer satisfaction is evident in the ID Coater's performance.
We invite you to explore how the ID Coater system can improve your operations. Click below for more details on implementing this game-changing coating solution.