Interior Diameter (ID) Tube Spray Machines
Achieve superior tube coating efficiency and reduce material costs. Protect your workforce with a safer and more controlled coating process.
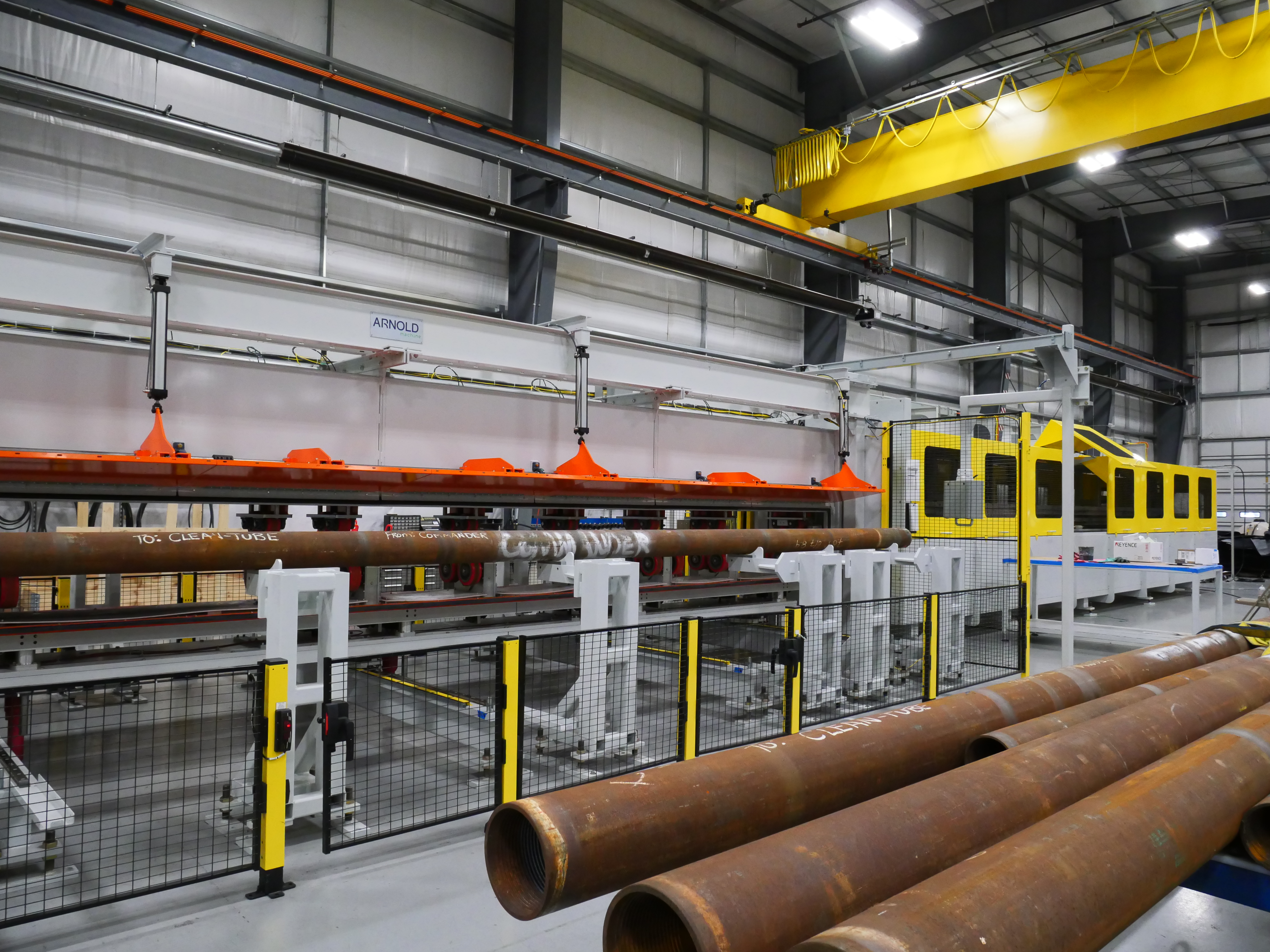
Benefits of ID Tube Spray Machines
How ID Tube Spray Machines Work
This automated system utilizes a multi-step process to achieve consistent, high-quality interior tube coating:
- The system loads and preheats a tube for optimal coating adhesion.
- A spray lance extends into the rotating tube, applying an even adhesive or primer layer.
- The tube enters a drying oven to cure the coating.
- If needed, a second spray booth applies a topcoat, followed by a final drying cycle.
- The system unloads the finished tube for further processing.
Common Applications
Arnold Machine ID tube spray machines excel in demanding industries, including:
- Oil & Gas: Coating downhole tools for harsh environments.
- Automotive: Efficiently coating high volumes of various components.
- Construction: Applying protective coatings to construction components.
These systems effectively work with solvent-based primers, adhesives, and two-component materials.
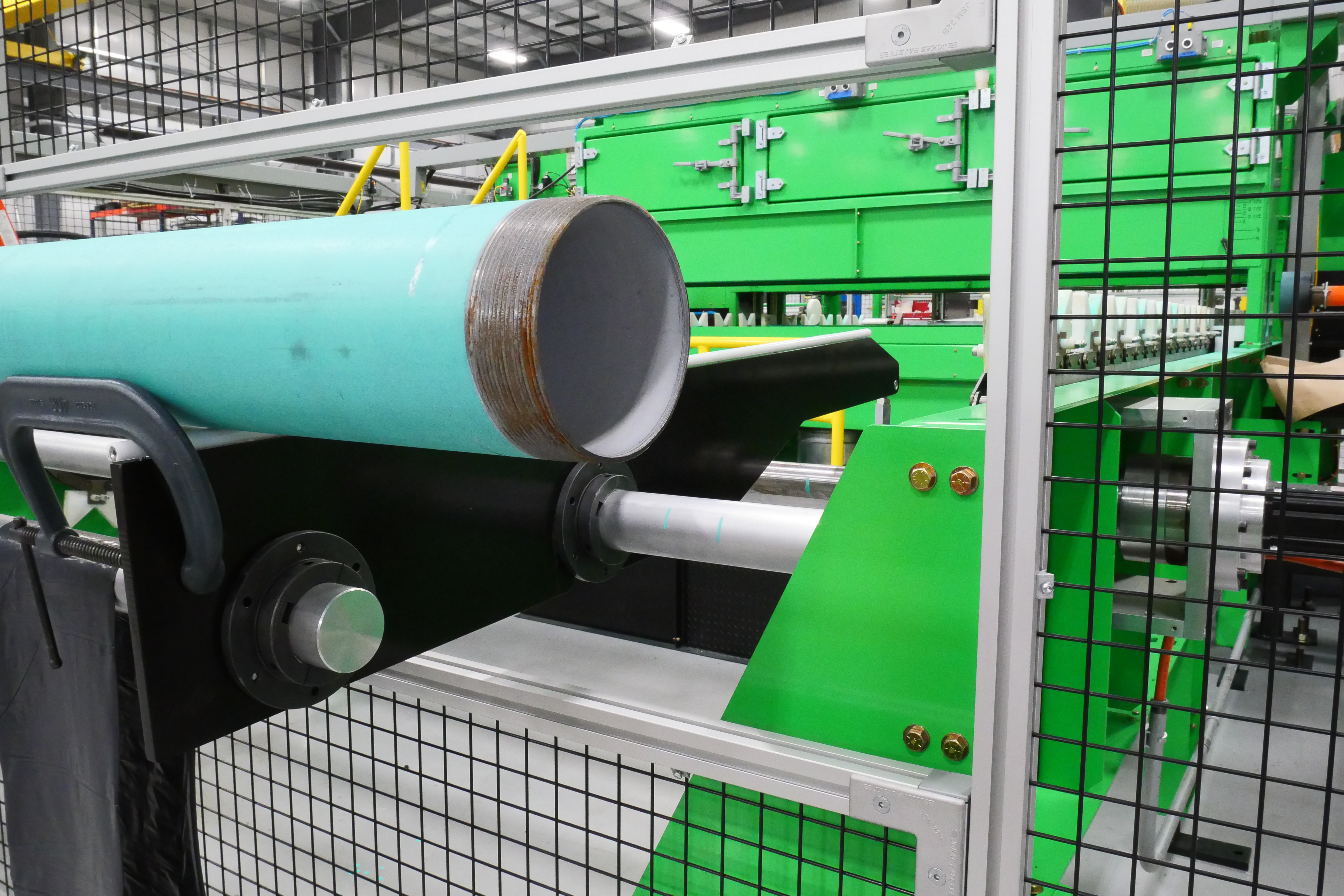
Specs & Features
We offer a range of customizable features and specifications to meet your precise coating needs. These systems are designed to handle various materials and applications while ensuring safety and efficiency.
Adaptability: Handles both adhesives and paints (water and solvent-based), including 2-component materials.
Standard Specs:
- Inside diameter range: 2" to 10"
- Tube length: Up to 40'
- Up to 4 adhesives per spray booth
- Material usage monitoring
- Coating material recirculation
Customization Options:
- Adjustable number of spray lances
- Bulk mixing cabinets with automatic viscosity control
- Automated material handling for increased efficiency
Optional Upgrades:
- Primer and topcoat drying ovens to optimize cycle times
- Additional spray booths for higher production throughput
Safety Features:
- Safety guarding and/or light curtains
- Interlocked doors for secure operation
- Full exhaust system for VOC management
- Heater safety alarms and fail-safe mechanisms
Competitive Advantages:
- Automated handling options for streamlined workflow
- Automatic spray adjustment based on tube diameter for precise application
- Automatic viscosity adjustment for coating consistency
- Fluid usage monitoring for efficiency and cost control
Trust Arnold Machine with Your Coating System Needs
At Arnold Machine, we blend innovation with experience to deliver coating solutions that surpass your expectations. Our commitment to collaboration and our deep expertise in automation make us the ideal partner for your ID Tube Spray Machine project.
Experience that Innovates. Our team of industry experts combines proven automation expertise with a passion for innovation to deliver results that exceed your expectations.
Efficiency You Can Count On. Our automated systems are designed to streamline your operation. Typically, only one operator is needed to oversee the entire coating process, maximizing your output and minimizing labor costs.
Adaptability to Your Needs. ID Tube Spray Machines handle a wide range of materials, including adhesives, paints, and even 2-component materials. With up to 4 adhesives per spray booth, you can switch between coatings quickly and efficiently.
Uncompromising Quality. We ensure consistent, high-quality results through real-time monitoring and data tracking. Material flow and usage are constantly monitored, guaranteeing a uniform coating thickness that meets your strictest standards.
Let Arnold Machine be your trusted partner in coating automation. Contact us today to discuss how our interior diameter tube spray machines will transform your operations!
ID Tube Spray Machine FAQ
-
How many operators are required?
-
How many adhesives can be used in a single spray booth?
-
How is coating consistency validated?
Other Coating Systems and Related Machines
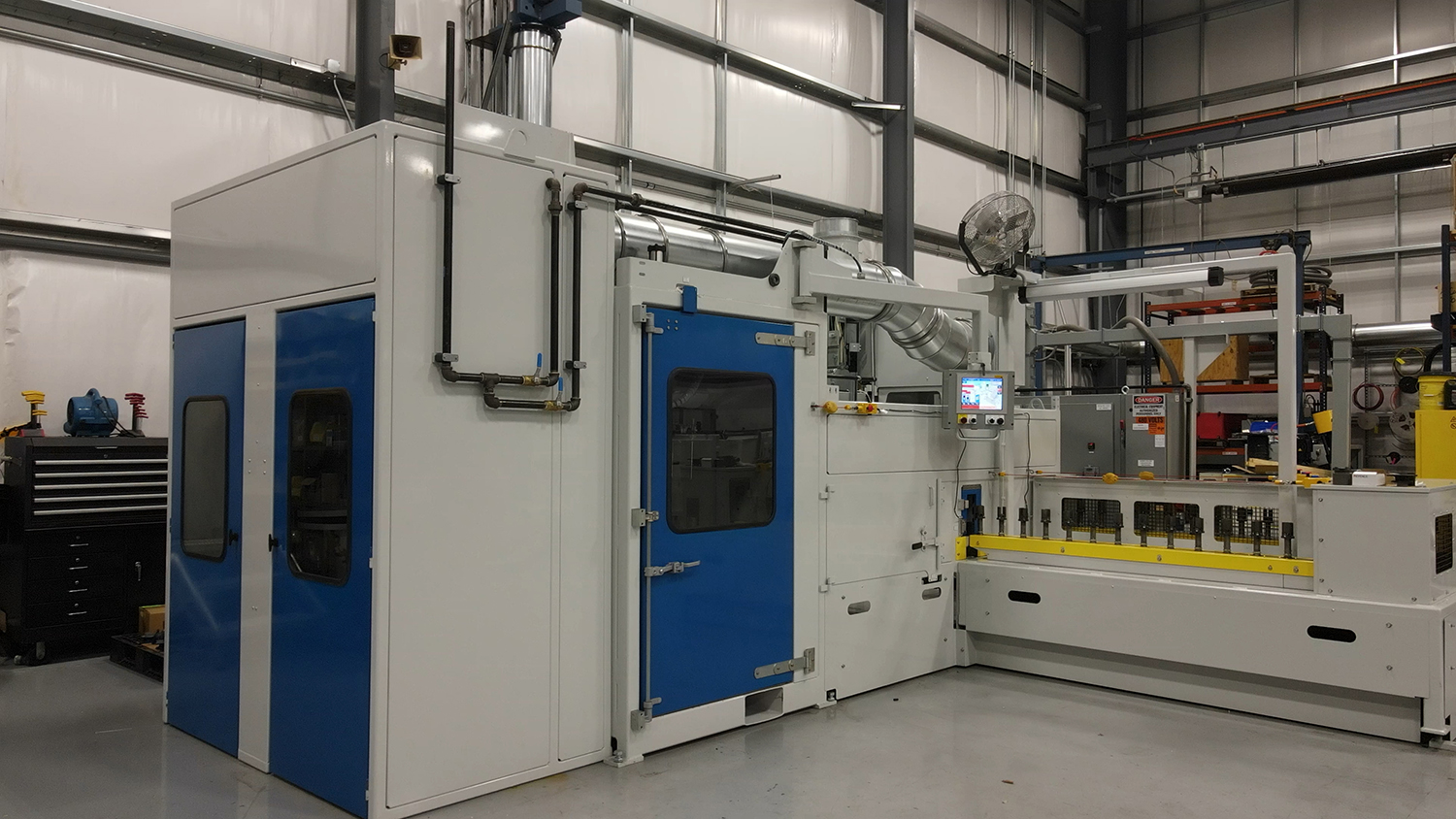
Chain-on-Edge Conveyors
Upgrade handling of complex parts and save valuable floor space with our specialized CoE conveyor solutions.
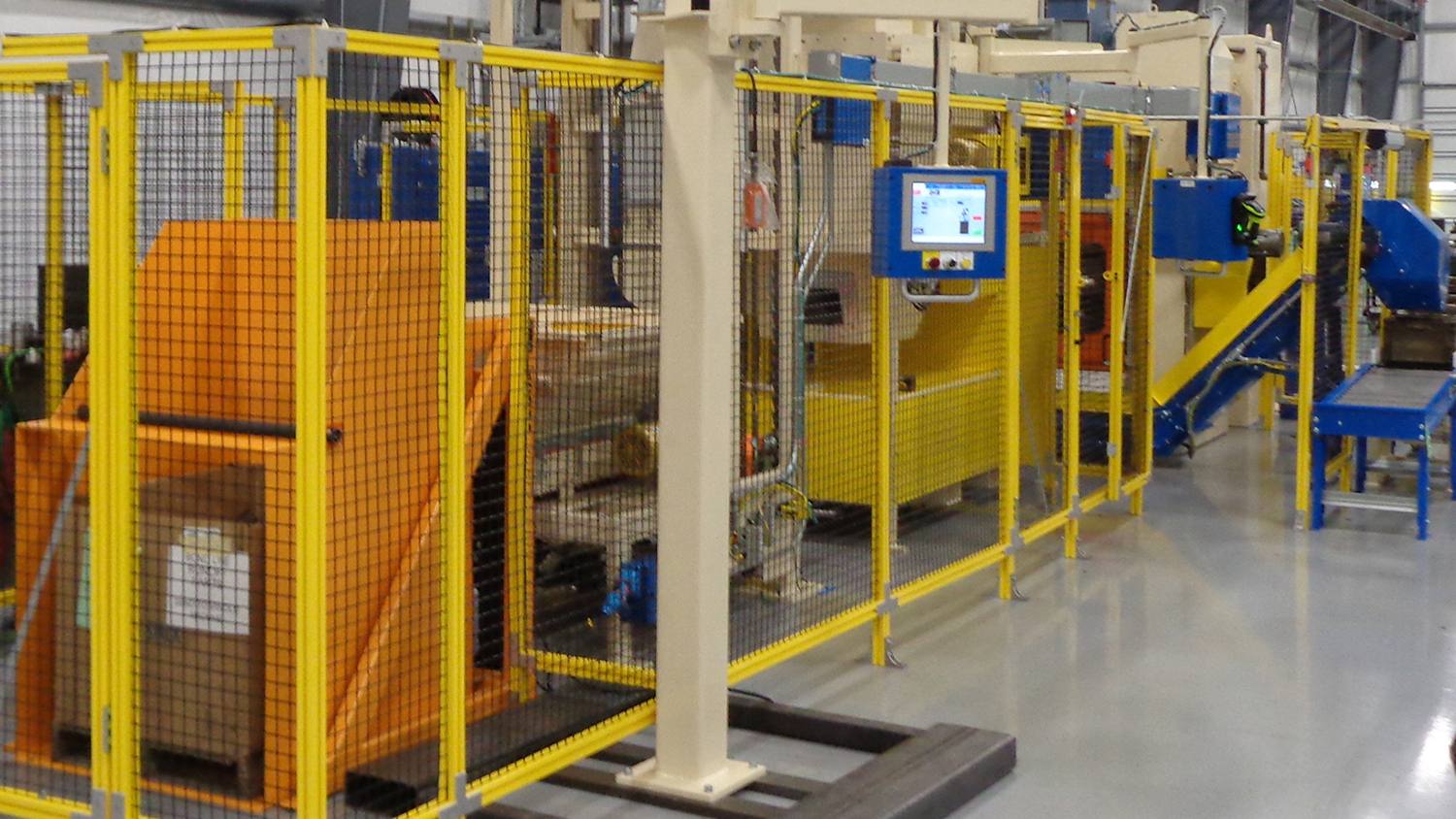
Tumble Spray Coating Systems
Automate your coating process for increased throughput and reduced material waste.
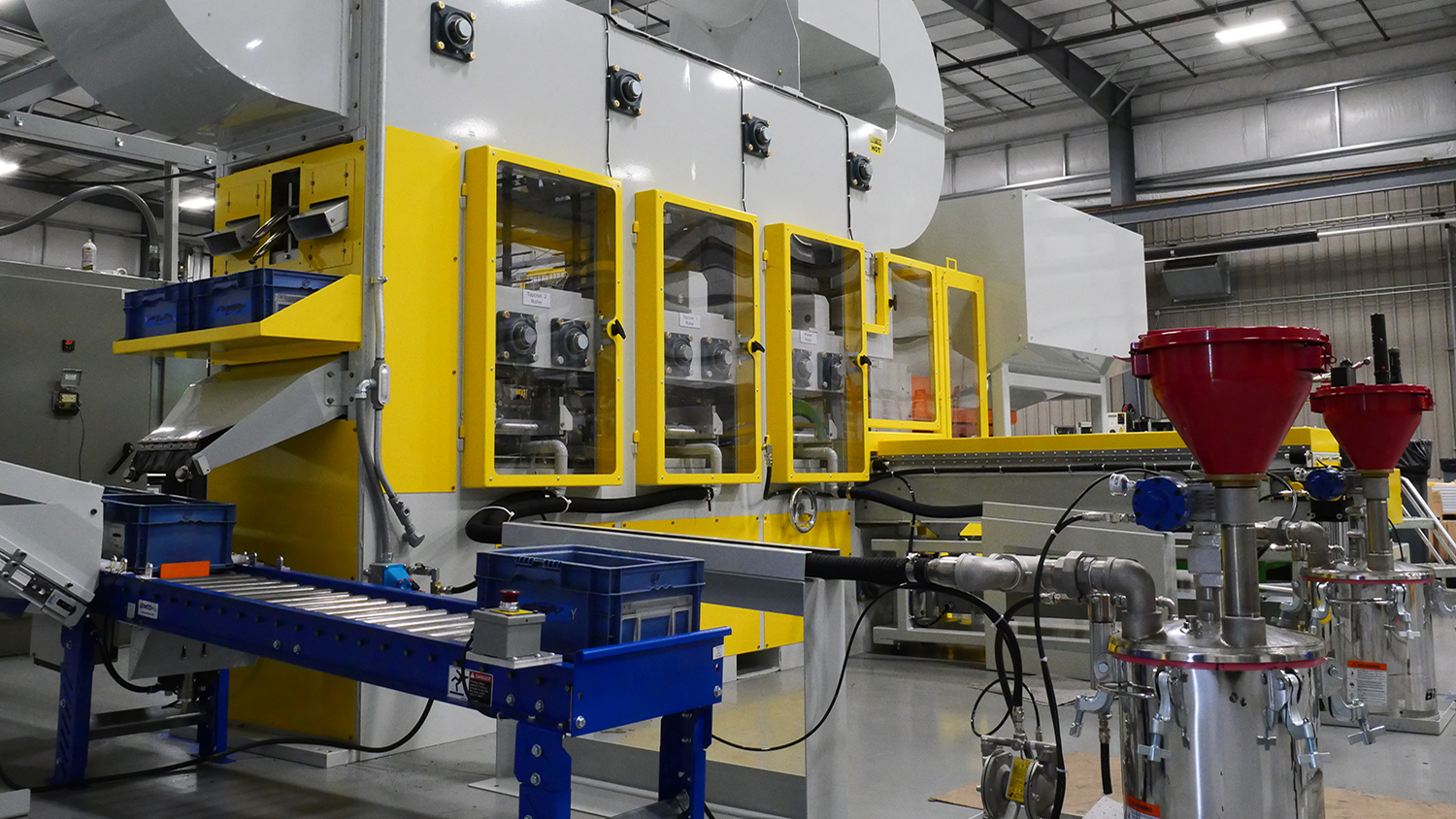
Roll Coater Systems
Precise application of coatings for consistent and high-quality finishes.
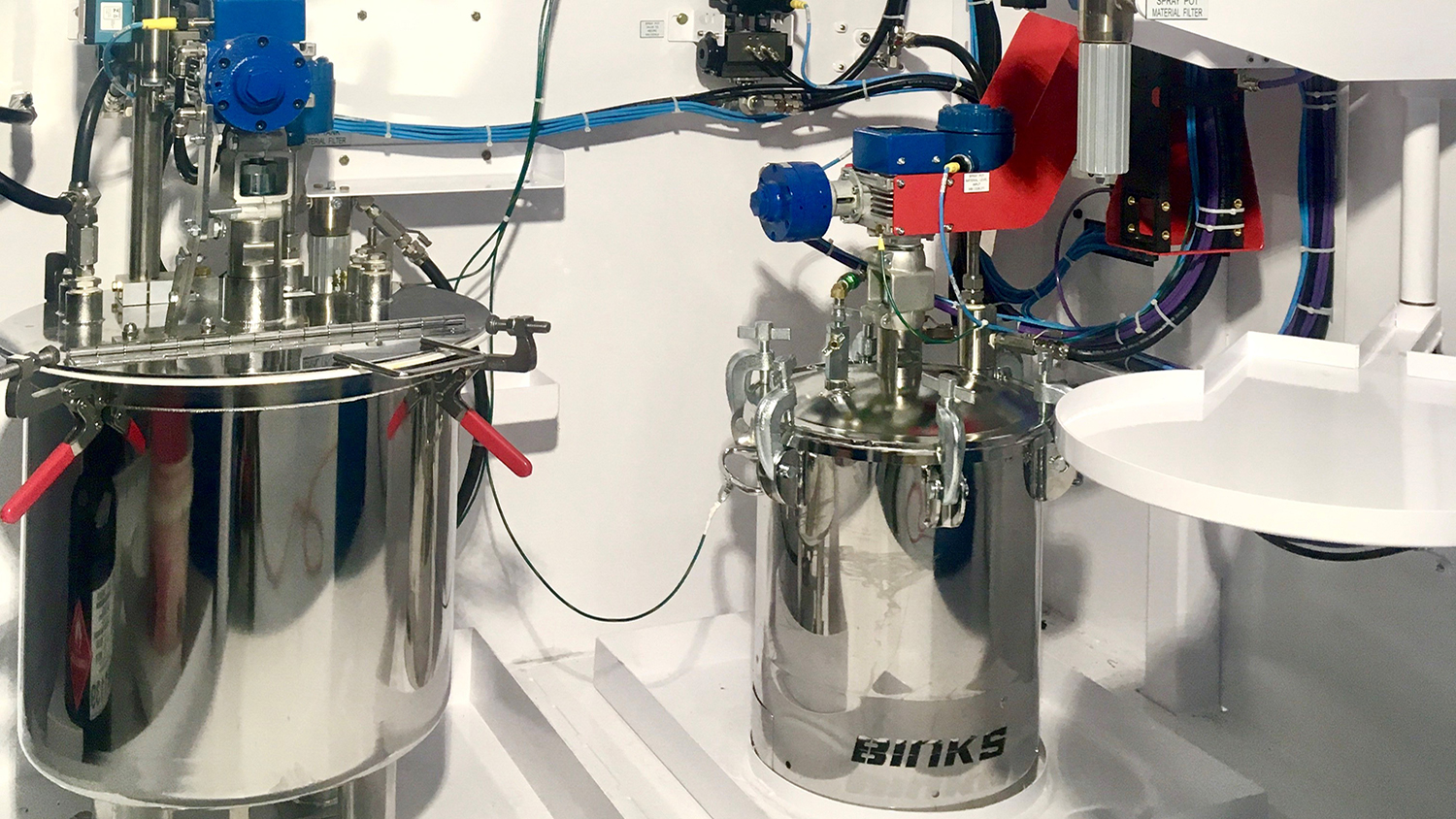
Automatic Viscosity Bulk Mixing Stations
Optimize production with consistent mixing, precise viscosity control, and reduced labor requirements.
Featured Posts
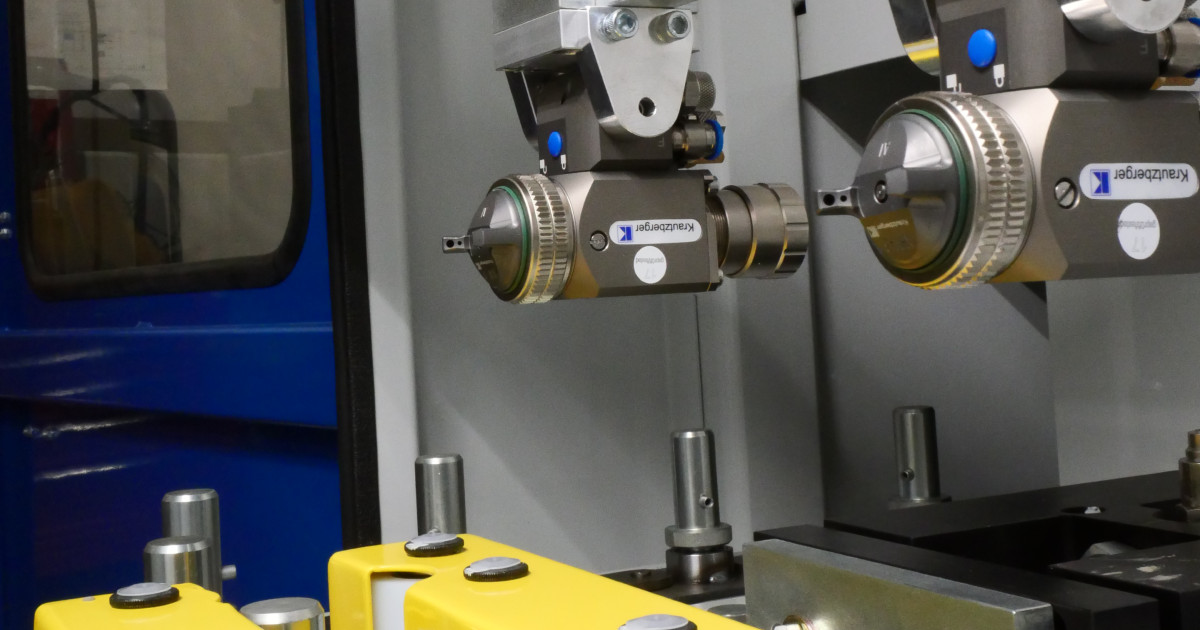
Benefits of Automated Spray Coating Systems
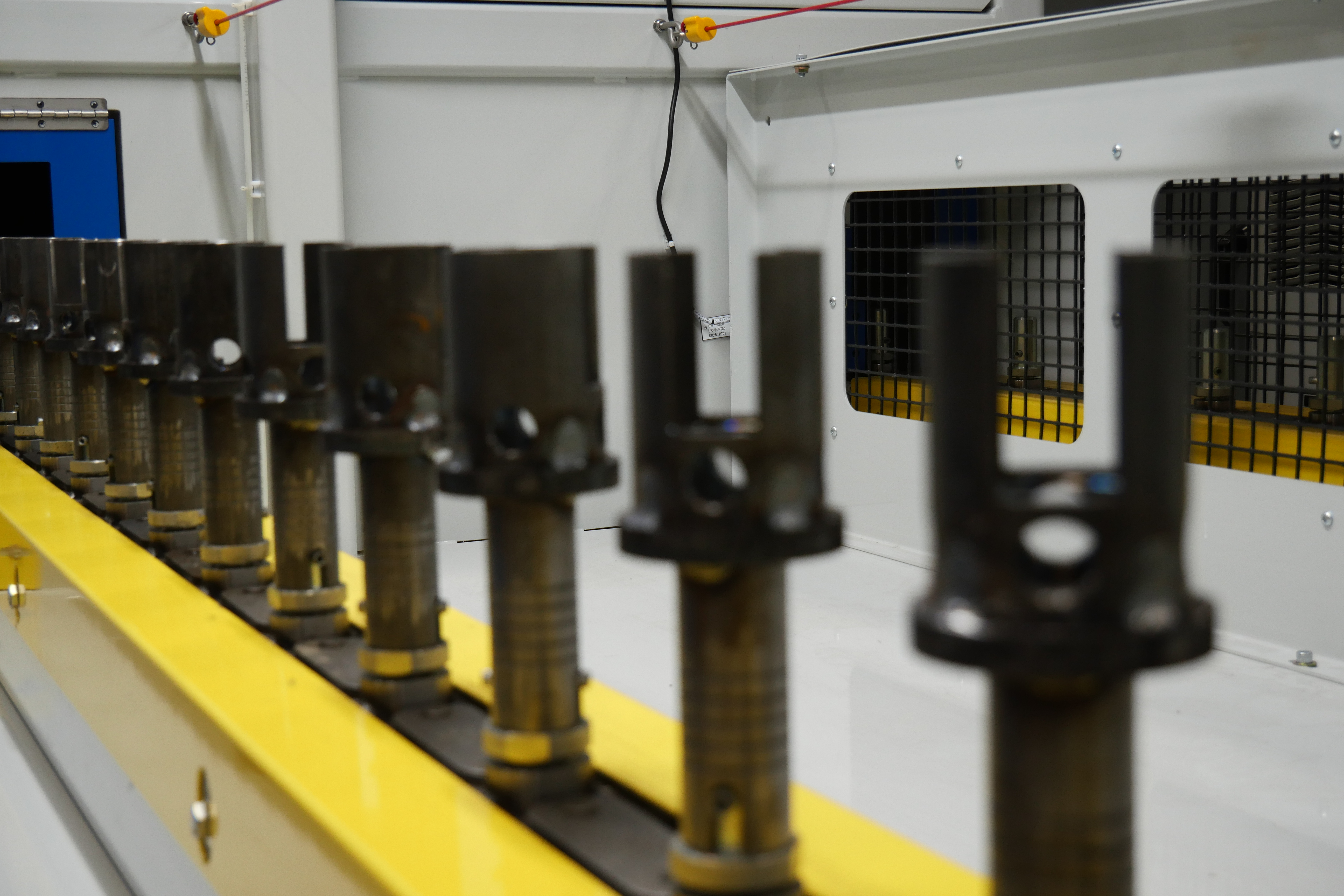
Chain-on-Edge Anti-Corrosive Spray System
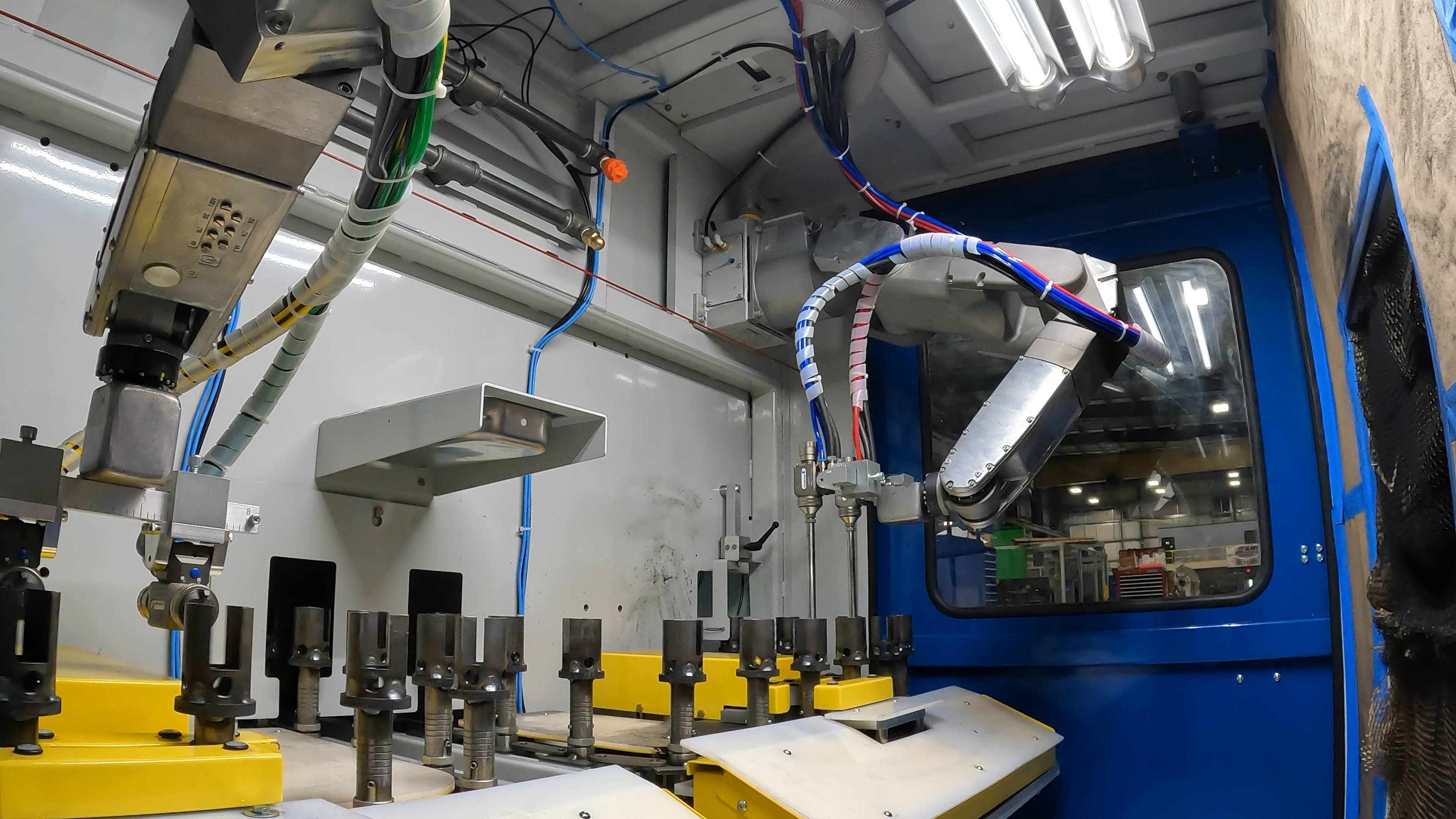