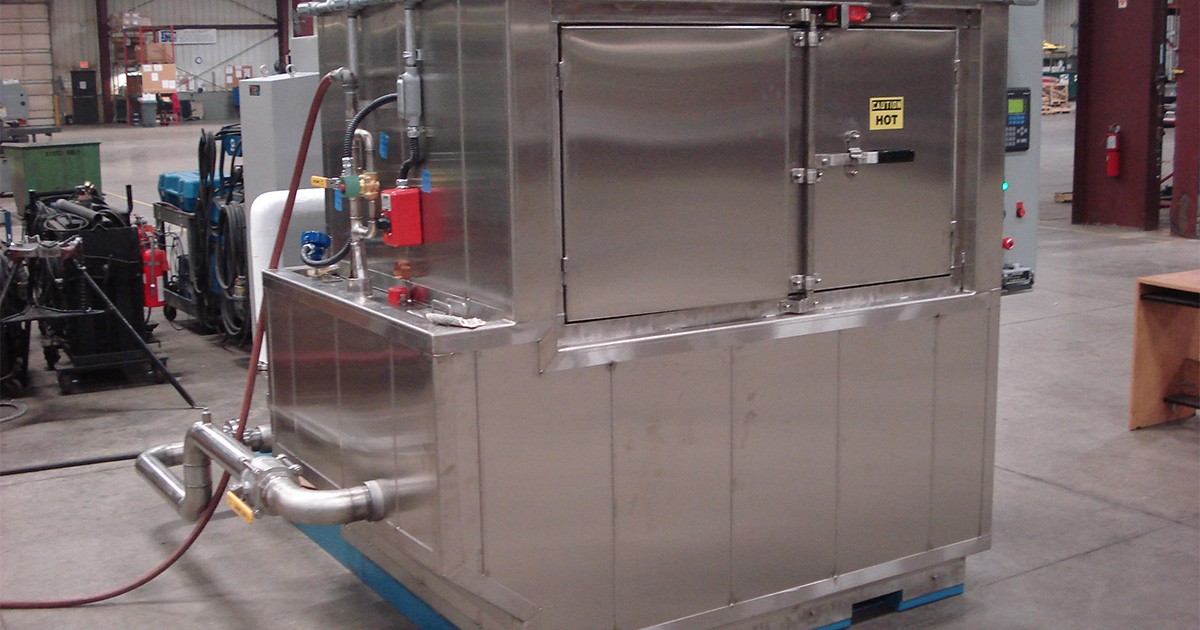
Ultrasonic Immersion Tanks
Ultrasonic Immersion Parts Washer for Heavy-Duty Equipment
A large North American heavy-duty construction equipment manufacturer needed a parts washer to clean cast-iron turbo center housings covered in oil and carbon deposits.
The previous process used by the client was several stations set up with parts being hand washed and dried. The customers requested to create two washers that would clean miscellaneous parts to eliminate employees hand cleaning with harsh chemicals. Removing heavy oils and carbon deposits by hand was extremely time consuming and exposed their employees to harsh fumes in the cleaning process.
Challenges:
- Create a safer and more efficient cleaning method
- Increase the cleaning of parts per hour
- Maintaining a specified operating temperature with a specific warm-up period
- Design to accommodate the installation of an additional ultrasonic plate if requested.
The Solution:
- Our parts washer team designed a closed loop immersion tank system:
- The customers’ parts would be hand loaded on a lift table that had a 500 lb. capacity.
- The table would then be lowered into the tank where the dirty parts would be introduced to the heated cleaning solution and the 10,000 watts of Ultrasonic power.
- The dirty water had to be cleaned using a combination of bag filters and our Stainless Steel Satellite Oil Coalescing Unit.
Ultrasonics in a parts washer work through a process called cavitation. High-frequency sound waves, produced by transducers in the cleaning solution, create alternating high-pressure and low-pressure cycles. During the low-pressure cycle, small vacuum bubbles form and grow. Once these bubbles reach a critical size, they collapse during the high-pressure cycle, releasing energy in the form of shockwaves and micro-jets. This energy dislodges dirt, grease, and contaminants from the parts being cleaned. The cleaning solution, usually containing a detergent or solvent, helps dissolve and remove the dislodged contaminants. Overall, ultrasonics provide a powerful and efficient cleaning method, reaching difficult-to-access areas and minimizing manual scrubbing.
These units would not only allow them to clean multiple parts at the same time but also keep their operators from breathing and touching the strong soaps they were using.
The Results:
Our customer was happy with the solution that we had created. Shortly after our team was able to get the units up and running, the customer purchased an additional unit to be added.
*Formerly FMT parts washers, Arnold Machine purchased the washer division in 2020 and retained the original FMT Parts Washer staff. You can expect the same excellence in manufacturing, materials, and service with the added benefit of automation integration.
Level Up Your Parts Washing with an Immersion Washer
Immersion Parts Washers can improve the safety of your employees, the cleanliness of your parts, and the capacity of your operation, all at the same time. Use the link below to learn more about our Immersion Parts Washers and see if they are the right fit for your business.