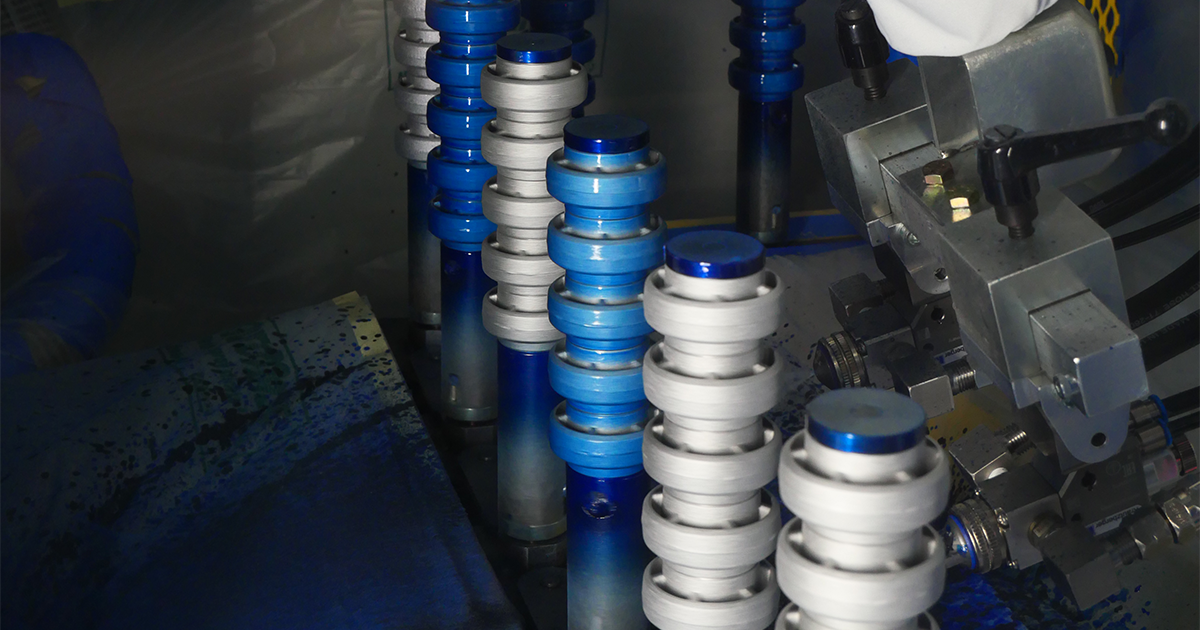
Chain on Edge System for Adhesive Coating
Robotically Applied Single Coat Adhesive for Urethane Bonding
A global leader in polyurethane product manufacturing reached out to Arnold Machine to create a process that maximizes coating material usage and control the efficiency of the process. They provide process engineering services and produce components for OEM and Tier 1 & 2 manufacturers. With a reputable background in manufacturing and molding within the industry, the client is dedicated to developing and delivering polyurethane products that solve demanding challenges.
Previous Process Client Used:
The previous process that the client was working with was a purely manual process. This led to material waste and a low efficiency production rate. Each step below was done manually by an operator:
- Surface Preparation: Clean metal substrate thoroughly to remove contaminants.
- Prepare the Adhesive: Follow manufacturer's instructions for preparation.
- Apply the Adhesive: Use a brush/applicator to apply an even adhesive layer. In some cases, handheld spray guns were used.
- Curing: Allow the adhesive to cure per manufacturer's recommendations in a separate curing oven.
- Post-bonding Inspection: Inspect the bond for defects and ensure it meets specifications.
- Cleanup: Clean excess adhesive from work area and tools.
Project Scope:
The client aimed to utilize a smaller mini-Chain on Edge Coating Machine to maximize coating material utilization and control the process efficiently. This machine features an automatic indexing design, an operator or robotic load area, twelve preheating stations, one spray coating station, and twelve post-heating stations. The system allows for consistent operations, with 48 fixture spindles and a 25-30 second cycle time per part.
Company Challenges:
The client faced several challenges:
- New staff learning the equipment and process requirements.
- Customer Tooling: Accommodating customer-designed tooling that required many dimensions and masking.
- Robot Mounting: The robot mount needed repositioning, requiring modifications to the frame.
Machine Solution/Function:
The client needed a solution that could handle a high product mix with various shapes and sizes. Arnold Machine showcased options focusing on flexibility, expandability, and dependability. The system allowed for future automation and quick-change tooling, accommodating a wide range of shapes and sizes for adhesive application.
Operation Steps:
- Operator prepares the system by adding adhesive to a pressurized pot and setting the pressure.
- Operator places the part fixtures onto the chain on edge system.
- Operator uses a test part to set spray gun controls.
Production Steps:
- Operator loads and unloads parts on the conveyor chain.
- Parts are pre-heated in a tunnel oven, indexed through twelve stations.
- A FANUC Robot applies adhesive using a programmed path.
- Parts continue through a drying oven, indexed through twelve stations, then unloaded.
How End Product Helped Company:
Implementing this system brought significant improvements for the client:
- Consistent coating thickness and quality across all part models.
- Reduced rejection rates and increased uptime.
- A 20% increase in production throughput due to automation, reducing manual intervention and enabling continuous operation.
Improve Your Adhesive Application with Automation
We designed a Chain on Edge Coating System to help a global leader in polyurethane product manufacturing automate their adhesive coating process. This innovative system maximizes material usage, improves process control, and significantly boosts production efficiency. If you're looking to enhance your automation process, contact us to discuss your project and explore custom solutions.