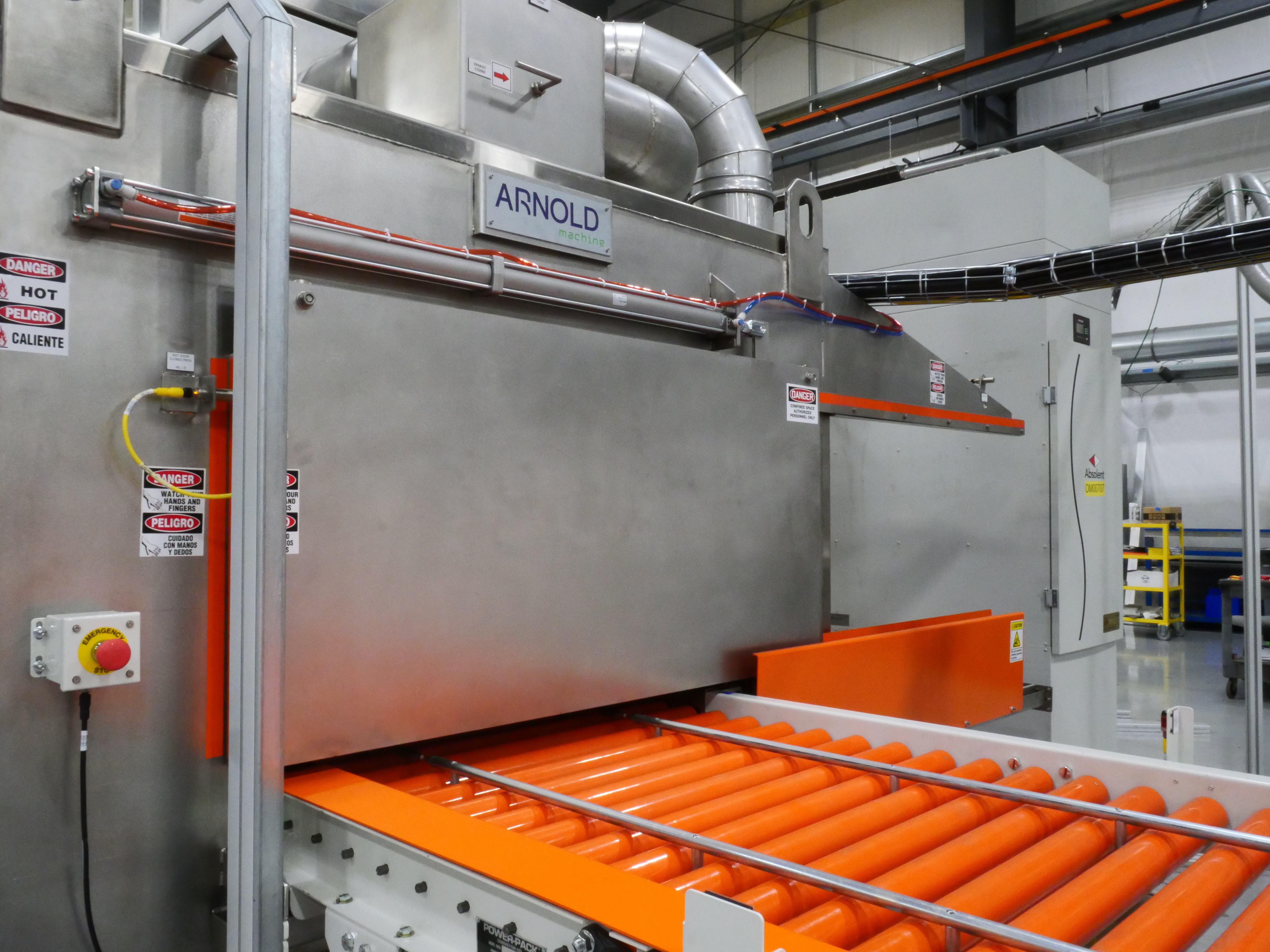
6 Most Common Problems with Washing Parts
Industrial parts washers operate in very rugged and dirty environments. While they’re manufactured to take the abuse, issues can arise occasionally. Clogged nozzles, non-starts, and parts that aren’t completely dry are just some of the parts washer problems you might encounter.
The good news is that you can fix most of these issues in-house if you discover the root cause. Read on to learn more about industrial parts washer problems and how to solve them.
What is a Heavy-Duty Industrial Parts Washer?
A heavy-duty industrial parts washer is a powered machine that efficiently and effectively removes dirt, grime, grease, oil, and other lubricants from various parts. There are many different parts washers on the market that are used to clean certain types or quantities of parts.
Types of Parts Washers
Parts washers can use solvents or aqueous-based, biodegradable solutions to get the job done.
Solvent-based—Solvents remove dirt, grease, and grime by dissolving it in a chemical solution that includes petroleum naphtha, benzene, xylene, trichloroethane, or mineral spirits.
Aqueous-based—These types of cleaning solutions are water-based and biodegradable. Some aqueous-based parts cleaning solutions can contain corrosion inhibitors for steel to prevent flash corrosion.
The most common types of parts washers include:
Conveyor parts washers—Ideal for high-volume production cleaning applications. They’re highly versatile and allow for a wide range of cleaning methods and a number of potential stages.
Gladiator parts washers—Aqueous-based parts washers that are ideal for smaller operations. They are pre-engineered, less expensive, and often have far shorter lead times than custom parts washers.
Immersion washers—A parts washer that immerses a part or parts into a solution. Parts can range in size from very small to very large.
Rotary basket washers—These types of parts washers are ideal for batch, precision, and ultrasonic cleaning and come in various configurations.
Rotary drum washers—The drum sizes can vary from 12 to 72 inches and are ideal for continuous in-line, high-volume small parts cleaning operations.
Rotary table washers—These parts washers work best for low-volume batch cleaning, parts production, and for heavy, large parts.
Specialty parts washers—Sometimes you need something a bit more custom. Specialty parts washers are custom-built to your exact specifications and application.
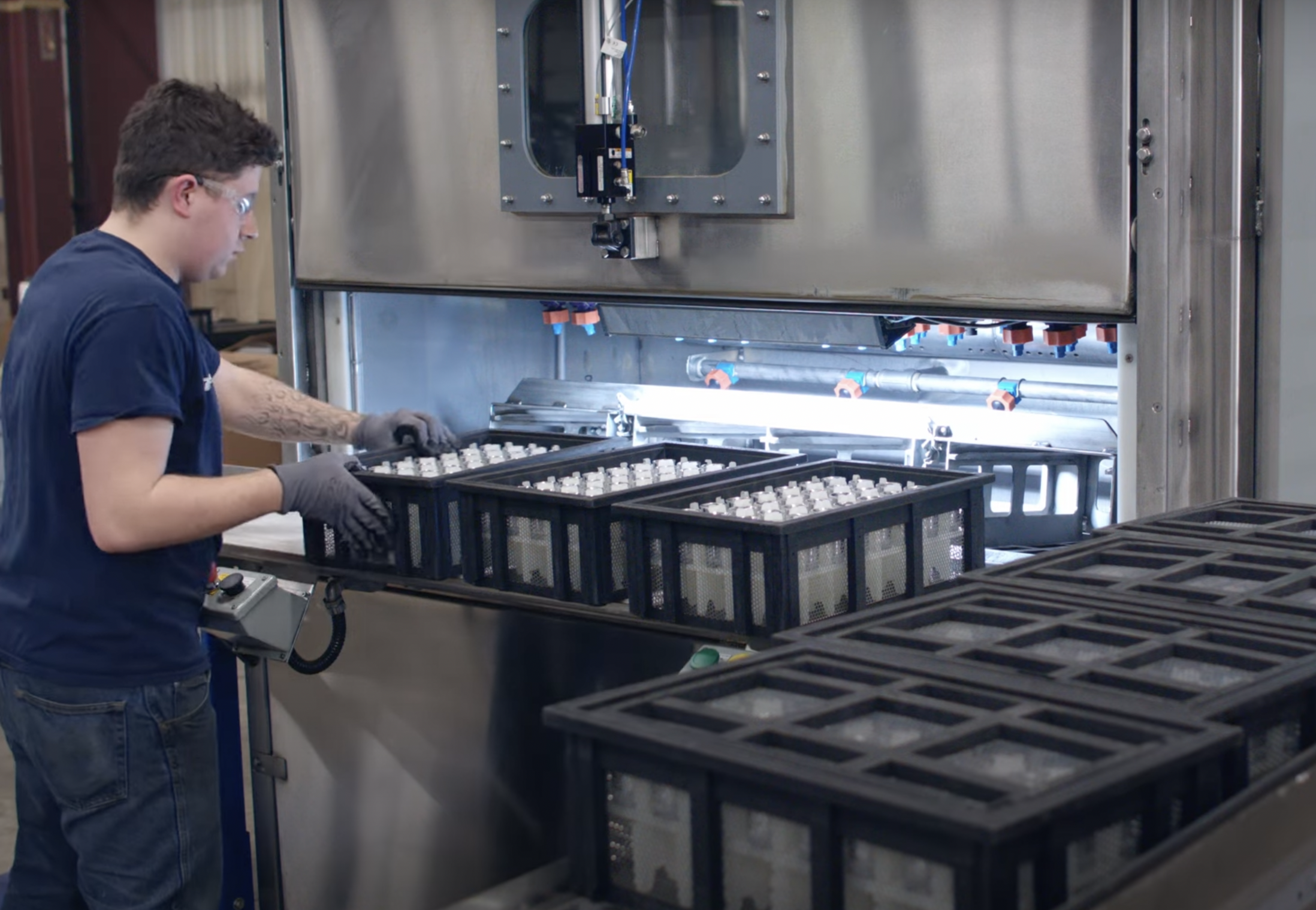
6 Common Parts Washer Problems
Here are some of the most common issues you might encounter with a heavy-duty industrial parts washer:
1. Non-start
The first problem you could encounter is the parts washer not turning on when you press the button. However, this doesn’t necessarily indicate that the machine is defective or broken.
Check whether the emergency stop button has been accidentally pressed or activated. Although it goes without saying—is the machine plugged in and turned on? Press the master start button on the control panel and then look at the PLC screen to confirm it’s powered on.
2. Is the machine receiving power?
Check the fuse box and see if a fuse has been tripped. Check the amperage and voltage on the control panel as well.
When you turn the switch to the “ON” position, do the control panel lights turn on? If the lights are amber or red, this indicates there is a problem with the machine. Refer to the owner’s manual for the next steps.
3. Component issues
Are there any obstructions or physical jams that occurred with the pumps, nozzles, motors, or heating elements? Check all wires that lead to each component to ensure they haven’t been damaged or accidentally pulled out. If your machine has a blower, check the air inlet to see if it’s clogged.
Inspect all filters to make sure they don’t need replacing or cleaning. Refer to the operating manual to determine if the filters are reusable or one time use only.
4. Spray headers and nozzles
Check the spray headers and nozzles to ensure that they’re dispensing the proper amount of cleaning solution in the correct spray pattern. Look for dirt and/or debris that could be clogging up the nozzles.
Are the headers and nozzles in the proper position? Sometimes nozzles and headers can get bumped around or broken when parts bump into them during the loading or unloading process.
5. Level of cleanliness is no longer meeting specifications
You can typically resolve this parts washer problem quickly by checking if:
- The wash solution isn’t too soiled. If so, it may need to be drained and refilled. Use a heated high-pressure power sprayer to clean the tank after you remove the solution.
- Are you using the proper amount of wash detergent?
- Are the originally designed operating temperatures being met?
- Is the filtration adequately maintained?
Overall, you’ll need to manually go through each component of the parts washer to determine what factors have changed.
6. Parts are not completely dry
As mentioned above, you’ll need to troubleshoot the parts washer to determine what factors had changed—because the parts were coming out of the parts washer clean and dry when the system was new.
Those items could be due to the following:
- Are you using the proper air temperature?
- Is the pressure correct?
- Are the air knives free and clear of debris (not clogged)?
- Is there anything obstructing the parts from being dried?
If the parts washer has a blow-off system, check the air blower to ensure that it’s running at the correct pressure. Inspect the hoses that lead from the blower to the air knives/nozzles. Make sure they’re not cracked or obstructed in any way.
Finally, check the opening from the fan box to the drying stage and make sure that there are no obstructions that would prevent hot air from being recirculated.
How to Solve the Majority of Parts Washer Problems
Parts washers are notorious for being neglected once in the manufacturing environment. If your company keeps the recommended spare parts in stock and completes proper suggested preventative maintenance, your parts washer could last a very long time.
At Arnold Machine, we’ve seen our washers last 30+ years following our recommended maintenance practices.
Arnold Machine Parts Washers
If you follow the above recommendations, there’s an excellent chance that you’ll be able to get your parts washer up and running again without professional help. However, if your current parts washer is on its last legs, contact the experts at Arnold Machine to learn more about our line of expertly-engineered industrial parts washers.
If you need help troubleshooting your Arnold Machine or Findlay Machine & Tool (FMT) washer, contact our service department at (419) 957-2517 or check out our service page.