Automatic Viscosity Bulk Mixing Stations
Our Automatic Viscosity Bulk Mixing Stations deliver consistent viscosity control for superior product quality. They eliminate unreliable manual measurements with dynamic real-time adjustments.
These stations offer exceptional versatility, handling solvent- and water-based adhesives, paints, and more. Once the mixture achieves the desired viscosity, it automatically transfers to a pressure pot for daily use.
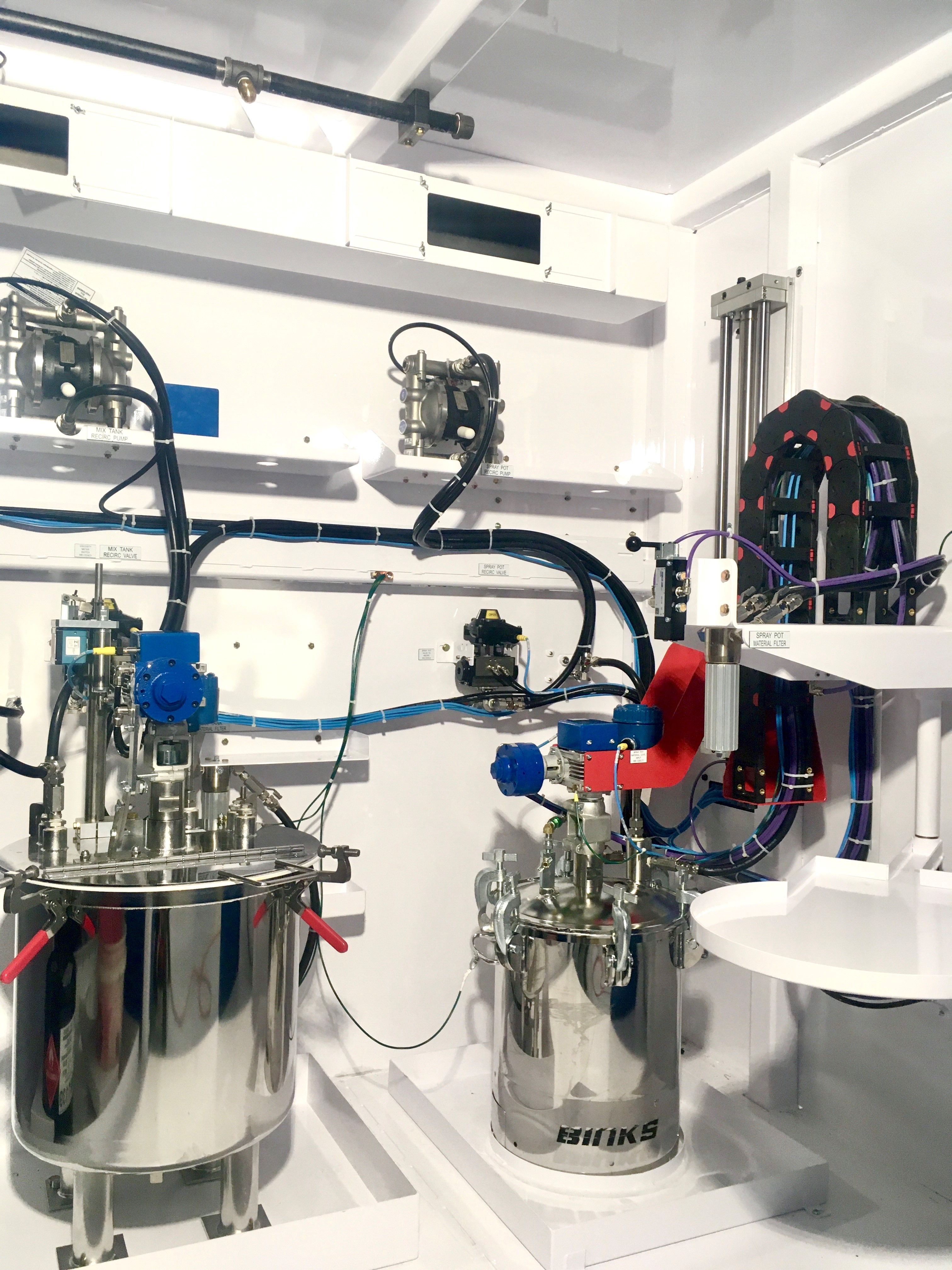
Benefits of Automatic Viscosity Bulk Mixing Stations
How Automatic Viscosity Bulk Mixing Stations Work
The process begins with 5-gallon buckets or 55-gallon drums of adhesive and solvent loaded into the cabinet. These containers are connected to fluid transfer pumps. A preset ratio of each material is then pumped into a separate mixing tank inside the cabinet.
The materials are agitated for a predetermined time to create a homogeneous mixture that is transferred through a viscometer to measure its viscosity. Based on the target viscosity setting, additional adhesive or solvent is continuously added to the mix until the desired setpoint range is achieved.
Common Applications
Automatic Viscosity Bulk Mixing Stations are versatile systems ideal for various applications involving adhesives, paints, and other coatings.
These stations are commonly integrated with standalone automated coating systems to provide a consistent supply of properly mixed materials at the desired viscosity.

Specs & Features
The AMI Bulk Mixing station with automatic viscosity control can be configured in several ways. A standard system capable of mixing and controlling the viscosity of two separate materials includes the following:
- Two 20 Gallon Stainless Steel Mixing Tanks
- Integrated agitator for thorough mixing
- Two 5 Gallon Material Load Stations
- Drum cover and integrated agitation for efficient loading
- Two 55 Gallon Solvent Load Stations
- Pickup tube for easy solvent dispensing
- Six Stainless Steel Body Diaphragm Pumps
- Durable and reliable pumping system
- Two 10-gallon pressure Pots for Mixed Materials
- Feed daily spray application
- Pneumatic agitators for consistent mixing
- Level sensors for automated monitoring
- Integrated Viscosity Control and Level Monitoring
- Ensures optimal material properties and prevents overflow
- Mixing Tank Vent with Flame Arrester
- Safety feature for flammable material handling
- Output Material Filter Module
- Maintains material purity and prevents contamination
- Recirculation System with Pressure Pot Integration
- Prevents materials from settling during system downtime
All the above items are common standard features. These systems typically integrate with a spray system control package. However, we can provide an individual control package for mixing and monitoring viscosity and material levels as an "offline" option.
Standard safety features include:
- 100% Exhausted Containment Cabinet
- Manual Water Fire Suppression System
- Options for Automatic Temperature Activated Water or CO2 Suppression
- Cabinet interiors are rated as a Class 1/Div 1 environment. We utilize suitable components for this specific setting.
Customization options:
- Flow Sensing
- Density Measurement
- Temperature Sensing inside the cabinet (depending on application)
- Pneumatic Lid Lifts for the Pressure Pots
Trust Arnold Machine with Your Bulk Mixing Needs
At Arnold Machine, we understand the importance of precise and consistent material mixing for your coating processes. We design our Automatic Viscosity Bulk Mixing Stations to streamline your operations, reduce waste, and ensure optimal results. Our expertise in customized solutions and commitment to process control and safety make us the perfect choice for your specific bulk mixing needs.
Automatic Viscosity Bulk Mixing Station FAQ
-
What is the maximum amount of raw and mixed materials inside the cabinet?
-
How long does it take to mix a 20-gallon batch of material?
-
Does the system need to be connected to a spray machine, or can it be a central point for mixing materials?
Other Coating Systems and Related Machines
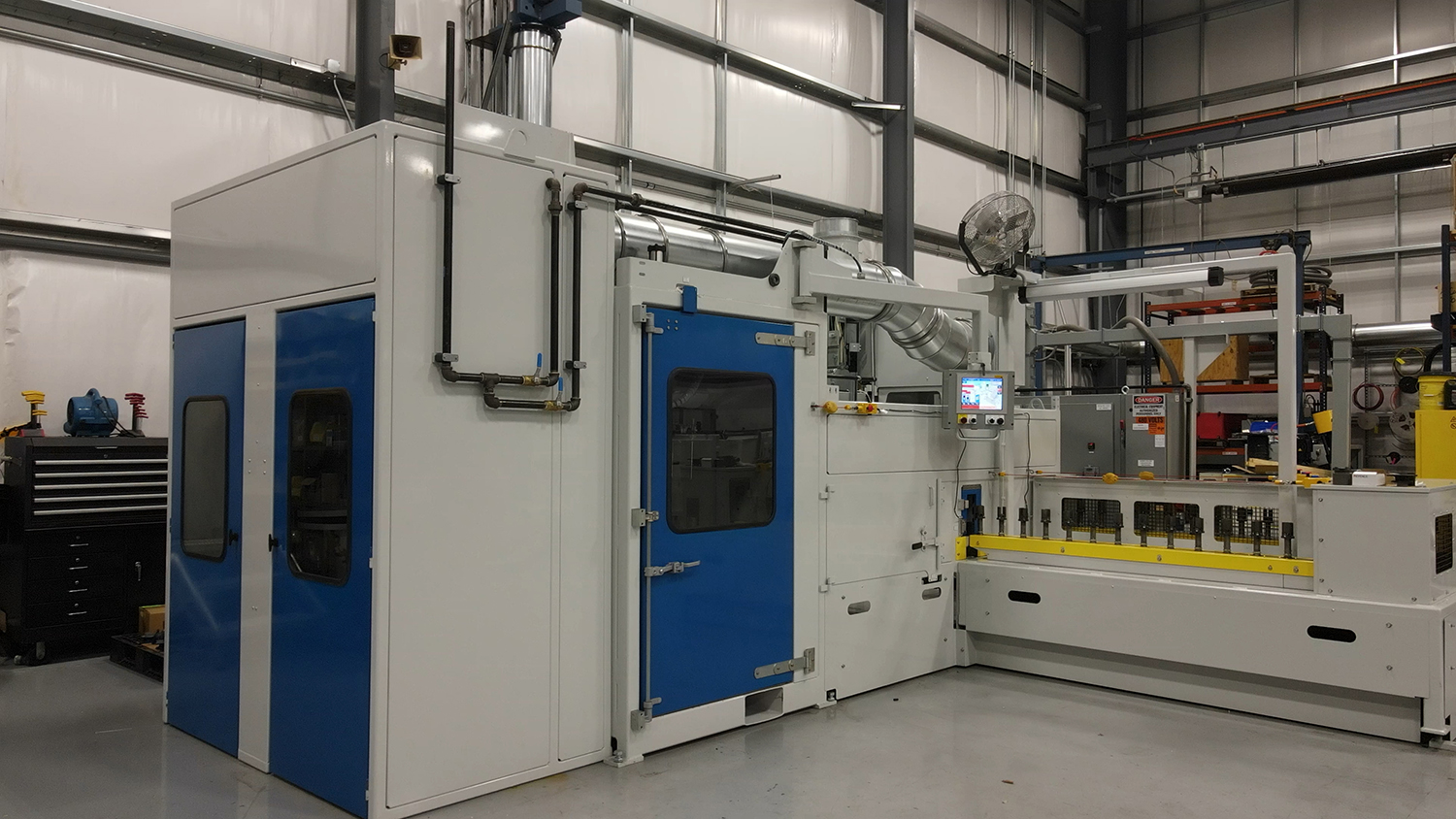
Chain-on-Edge Conveyors
Boost your profitability with our innovative CoE systems. Advanced robotics automate your processes to increase transfer efficiency and reduce labor costs.
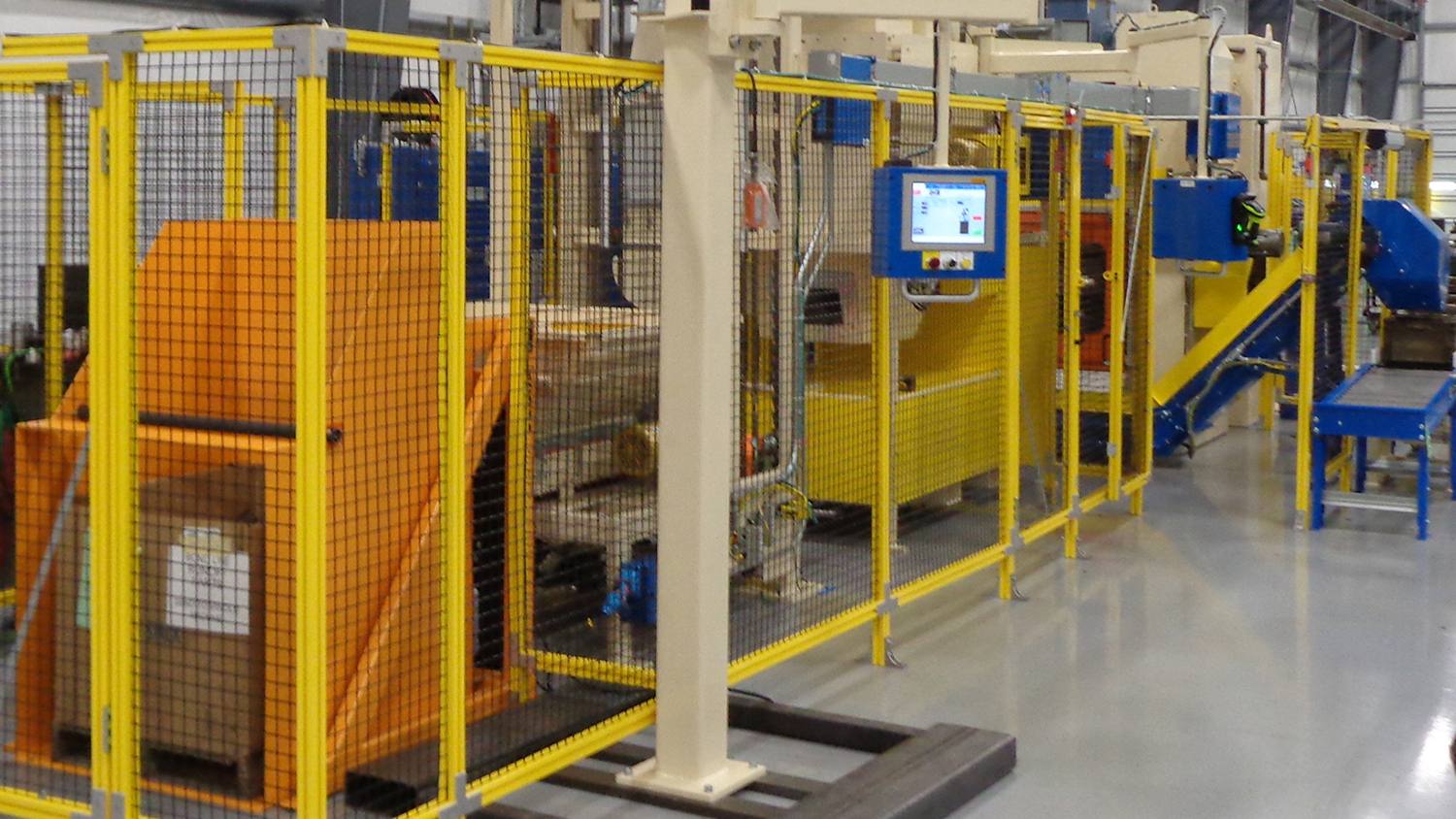
Tumble Spray Coating Systems
Achieve unmatched protection and efficiency with our fully automated Tumble Spray systems. Experience 100% coverage, significant labor savings, and consistent results in your coating operations.
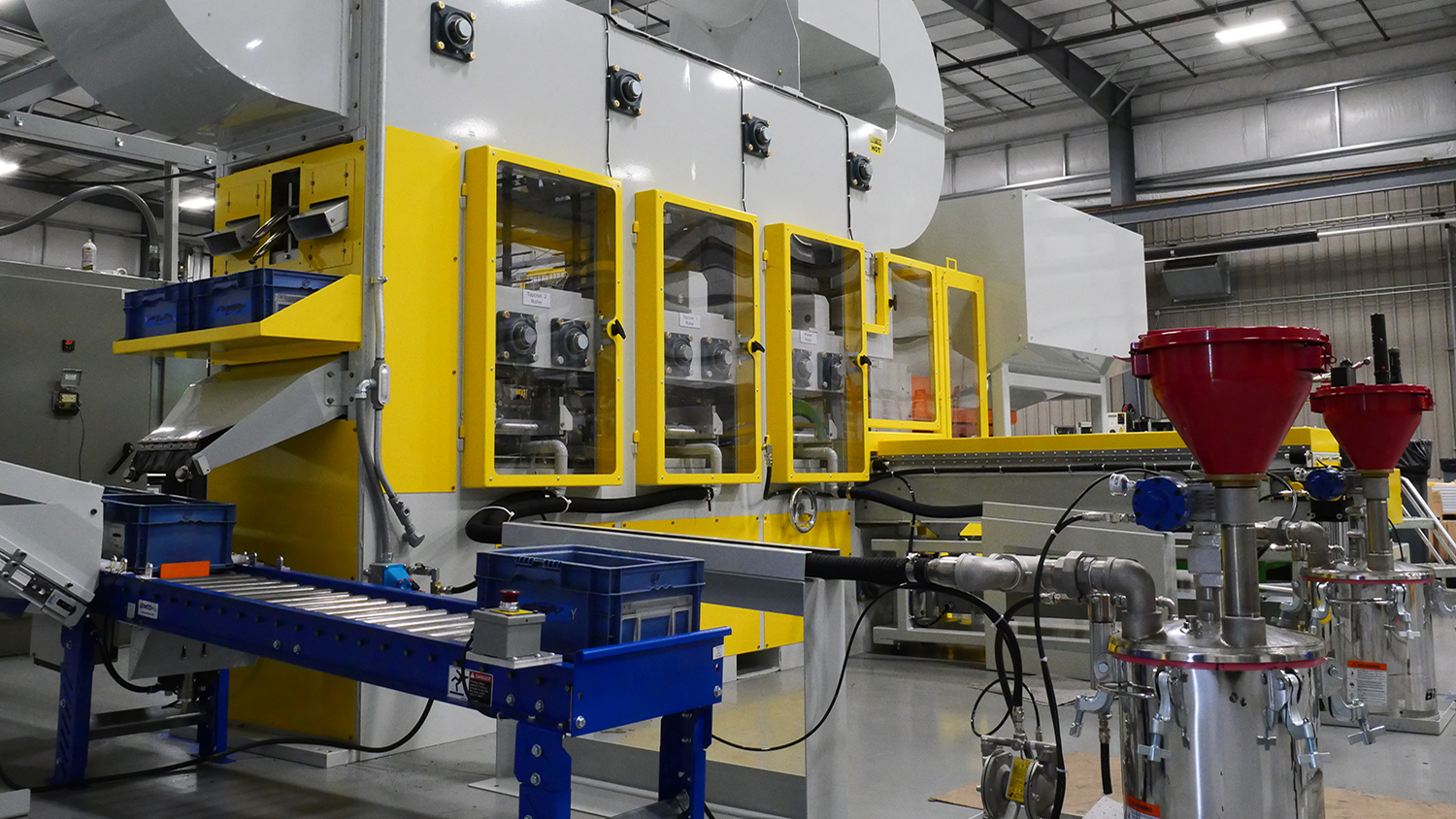
Roll Coater Systems
Our customized Roll Coater Systems seamlessly integrate into your existing processes, delivering consistent high-volume coating results. Experience unmatched throughput, minimal adhesive waste, and reduced labor requirements.
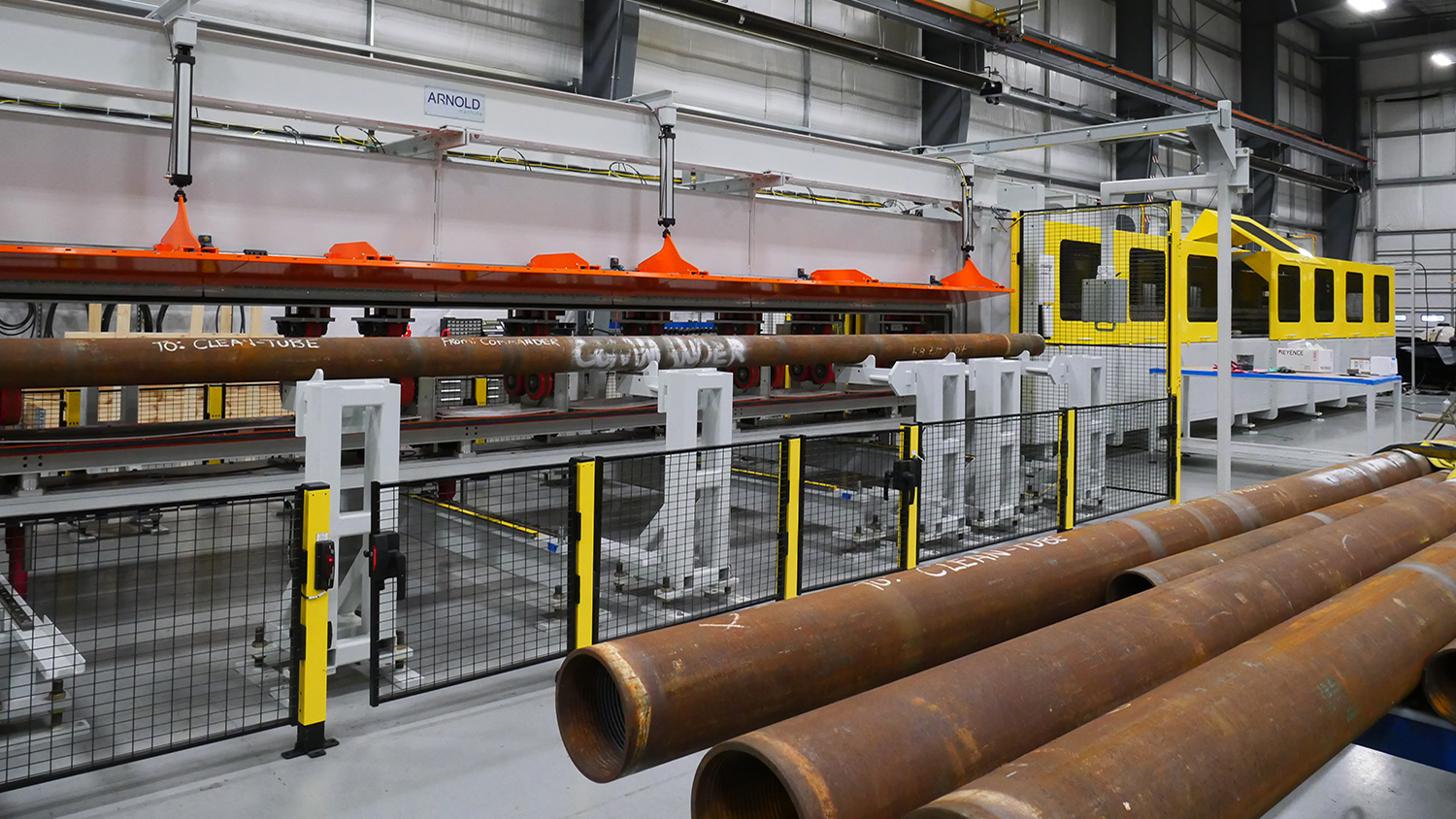
ID Tube Spray Machines
Protect your workforce and achieve superior tube coating efficiency with our automated ID Tube Spray Machines. Reduce cycle times, verify material usage, and eliminate harmful VOC exposure for your operators.
Featured Posts
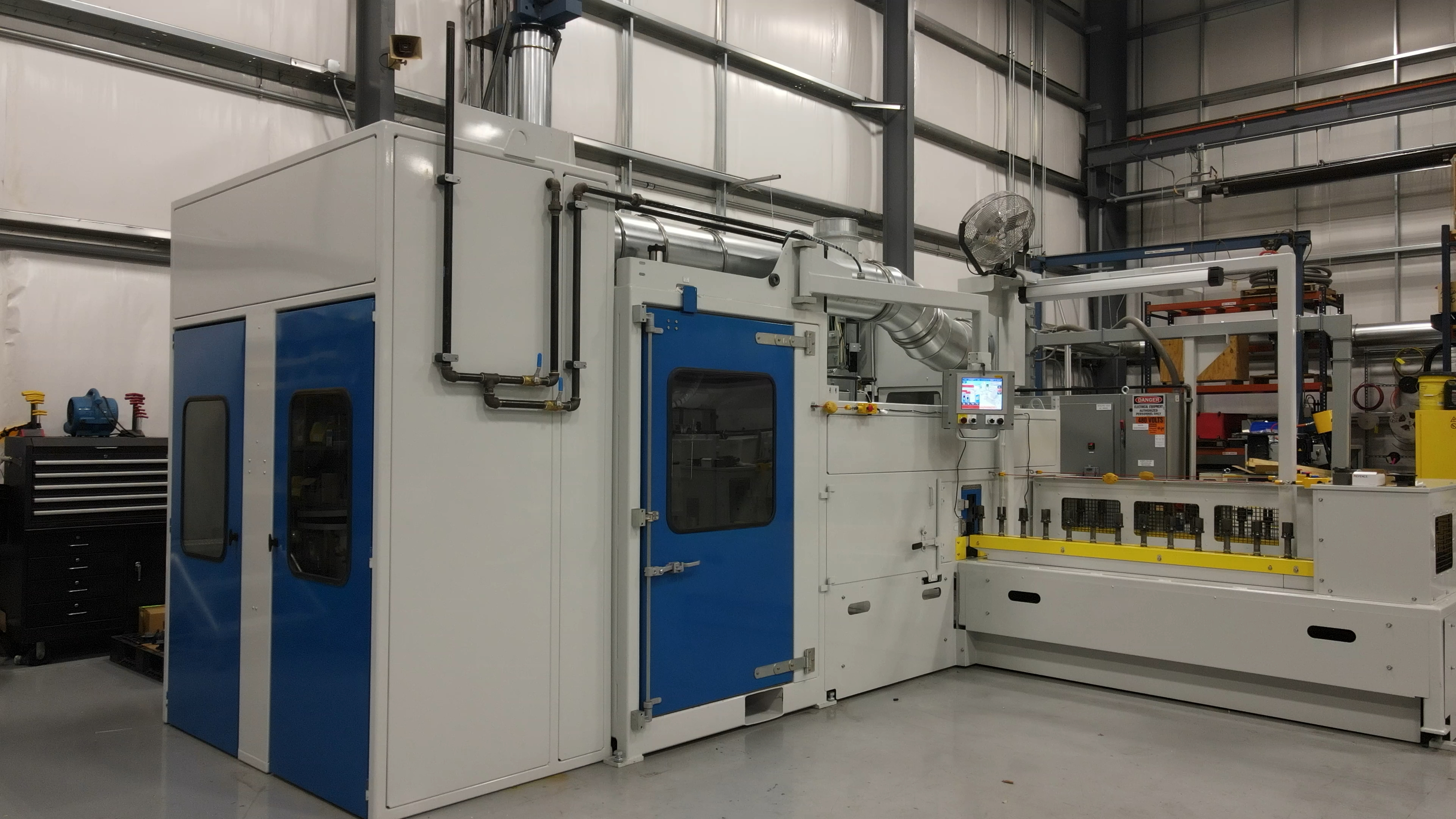
[Case Study] Designing a Custom Automated Anti-corrosive Coating System for Auto Parts
Discover how a major automotive manufacturer achieved superior results and increased productivity with Arnold Machine's innovative solutions.
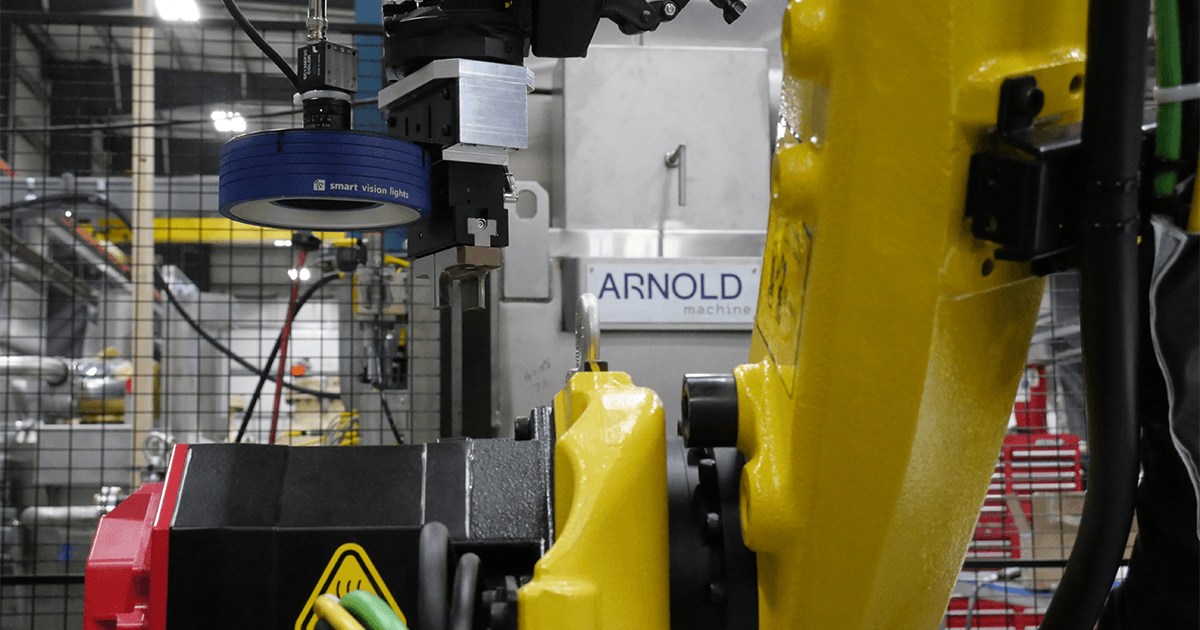
Benefits of Automated Spray Coating Systems
Automated spray coating systems enhance production efficiency while ensuring consistent and high-quality finishes.
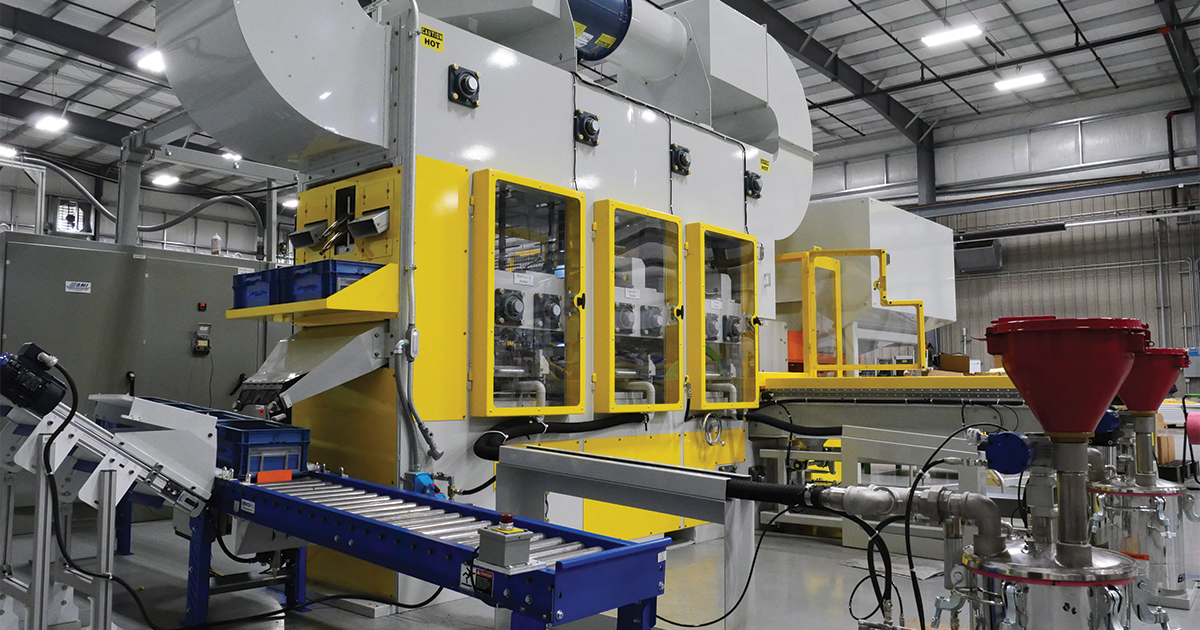
Choosing the Right Paint Conveyor System: Factors to Consider
Learn about the key factors to consider when choosing a paint conveyor system that will transform your coating operation.