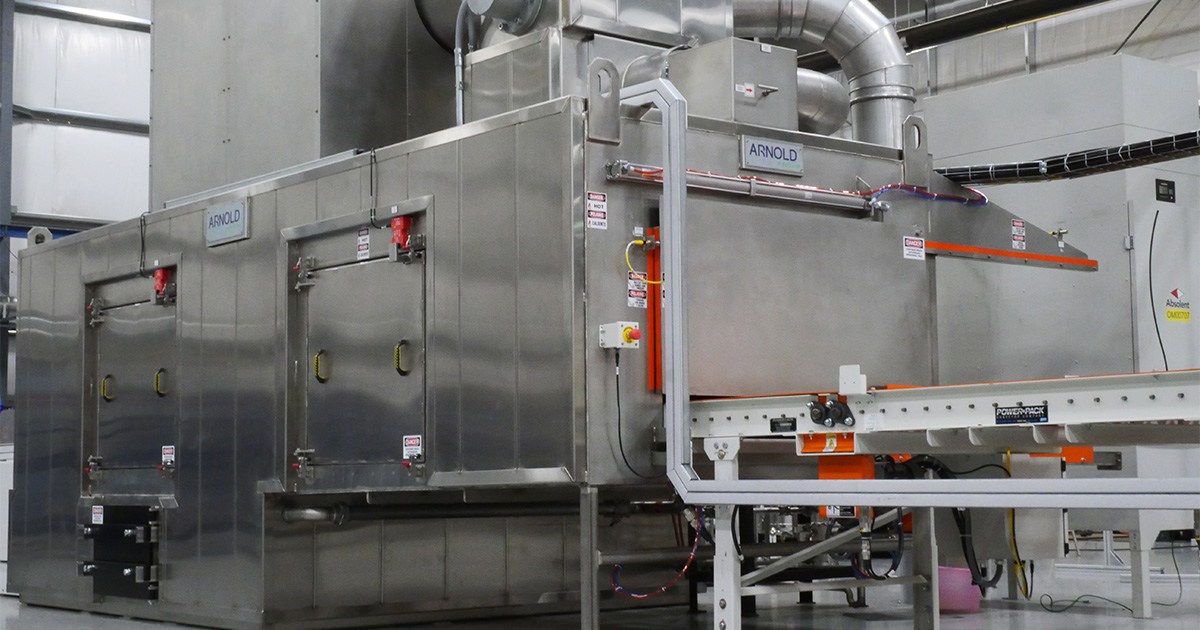
Two-Stage Powered Roller Conveyor Cleaning System
Automated Transmission Washer and Conveyor System
A global production engineering company, a system integrator of production equipment, was awarded a multi-million-dollar contract here in the United States to complete the final assembly of automatic transmissions. They contacted Arnold Machine to handle the last portion of the project, which included weighing each transmission, conveying it to the cleaning system where they were washed and dried, and then conveying them to various inspection and queuing stations before shipment.
Their customer was already familiar with Arnold Machine and the quality of equipment they produce, as they already had some of their systems on their floor. Their client requested the integrator to contact us for the new assembly line washer portion of this project.
Challenges:
There were a few requirements the customer asked for:
- Clean each transmission of excess transmission fluid and particulates.
- Achieve an output of 32 assembled transmissions per hour.
- Accommodate the complex geometry of the transmissions to ensure each part was washed and dried.
The Solution:
Arnold Machine created a washing, drying, and conveyor system that allowed each transmission to be fully cleaned. The transmissions would first go through a heated wash stage. Upon entering the wash stage, a heated washing solution was introduced to all sides of the parts using stainless steel headers and spray nozzles. The wash solution would be filtered and cycled through 6 stainless steel bag filter housings. After the washing stage, the transmissions would enter a drain vestibule prior to entering the blow-off stage. The blow-off utilized a high-volume blower in conjunction with an electric air circulation heater and a stainless steel air knife to ensure complete dryness before the next stage.
In addition to part cleanliness and dryness, the movement or conveyance of the transmissions was also important:
- There were 25 feet (5 sections of CDLR conveyor, each section with independent VFD drives) between the weigh station and the powered turntable, which would rotate the transmission 90 degrees.
- Once rotated, the transmission would travel over a 5-foot section of CDLR conveyor to the cleaning system. The cleaning system had 17 feet of CDLR conveyor.
- Then the transmissions would exit the cleaning system onto two 5-foot sections of unload CDLR conveyor.
- Next, there were seven (7) 2 feet 3 inches CDLR conveyors, which were used for some final assembly work as well as final inspection. The last of the seven (7) sections would rotate, allowing the transmission to be inspected on the sides and both ends.
- Lastly, there were eight (8) sections that were 2 feet 6 inches long of CDLR conveyor, which served as a queuing area prior to crating or palletizing each transmission for shipment to the customer.
The transmissions were conveyed directly on the CDLR conveyor. Each roller had a urethane sleeve to prevent damaging the transmission's oil pan, as there were no pallets or fixtures for the transmission to sit on. All sections of the conveyors had independent drives and part sensors to allow the part to queue through the system to the next available open area of the conveyor. Once the transmissions entered the cleaning system, that section of the roller conveyors ran continuously through the washer/dryer.
Both the integrator and their end customer were pleased with the entire project. It is now installed on the customer's floor and being used in production.
Take Control of Your Parts Washing with a Conveyor System Washer
At Arnold Machine, we take the time to learn the unique requirements of your application and build you a custom solution. Our custom Conveyor System Washers provide an excellent opportunity to streamline even the most complicated parts washing operations. Use the link below to learn more about our Conveyor System Washers and see if they are the right fit for your business.