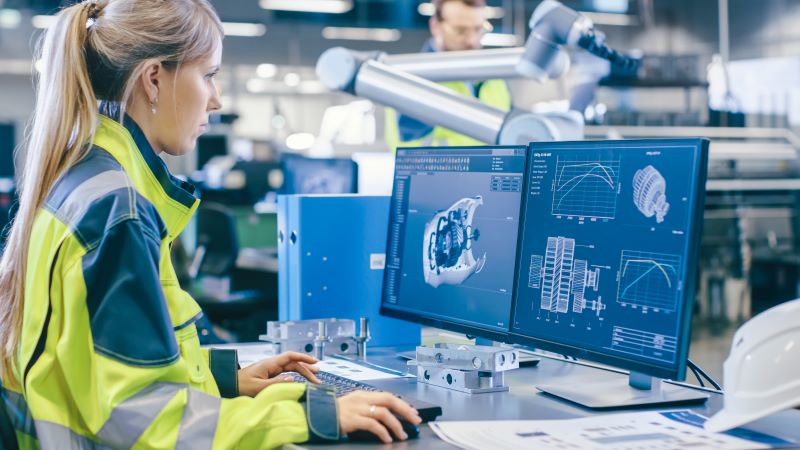
Time & Cost Saving Considerations in the Manufacturing Process
Today’s manufacturing is as competitive as ever; it’s also the most advanced. In this ever-evolving landscape in which competition is at its highest, technology is constantly growing, and efficiency is paramount, it is crucial to keep costs down. Furthermore, downtime is not an option. Time is money, so time savings must be well integrated into the cost-saving plans.
There are many factors to consider when the goal is to remain at an economic advantage during the entire manufacturing process. What’s important to remember is that cost savings begin in the design of the product itself. After that, there are many specific cost considerations to keep in mind.
In this blog, we will take a look at all of the specific ways to keep time and cost savings at their optimal levels, factoring in all of the principles, requirements, and practices that keep the manufacturing process as cost-efficient as possible.
Cost Savings Start in the Design
While there are many factors to take into consideration when looking at the specifics of manufacturing a part or product, it’s critical to know and understand that time and cost savings all begin with the design of the part. But before you can look at each of the specific methods and considerations within product design, you must look at the big picture.
Keep these numbers in mind: 80% of the cost of a product is determined by product development/design. About 60% of the cost is simply the concept phase of the project. These are huge cost-determining factors.
When looking at the big picture—to let the savings trickle down to all areas of design—there are three cost reduction strategies that successful companies employ: Design for Manufacturability, Lean Manufacturing, and Concurrent Engineering.
Design for Manufacturability (DFM)
Simply put, this process means to proactively design your products to optimize all functions (from fabrication and assembly through shipping and repairs) while simultaneously optimizing and ensuring quality, safety, compliance, reliability, customer satisfaction, and cost. It is a proven, time-tested methodology that works for any size business, and its implementation keeps costs and time at a minimum.
The ultimate goal with Design for Manufacturability is products that are easier to build and assemble, and are done so in less time with fewer parts. Everything is designed for ease of use, repeatability, and maximum use of parts. In the end, DFM saves time and money by making the best use of what’s already been made and done, and results in significant time-to-market savings, sometimes half of what it used to be.
Lean Manufacturing
Lean manufacturing is a successful methodology whose basic philosophy is the elimination of waste. Its ultimate goal is to make use of what’s valuable while eliminating everything else. This can involve the use of a set of “tools,” or strategies, that identify what's being wasted and then remove the source of waste. In the end, it’s all about efficiency.
This can mean reducing excess parts, workspaces, inventory, and practices—anything that isn’t completely necessary to the functioning and manufacturing of a company and product, respectively. It’s often said that there are seven sources of waste to identify and eliminate:
- Labor
- Overproduction
- Space
- Defects
- Unnecessary Human Motion
- Inventory
- Transportation
Once a company implements proven procedures that identify and eliminate waste within these seven areas, benefits include higher quality products, reduced inventory, less space required, higher safety, improved employee morale, and ultimately, higher customer satisfaction.
Concurrent Engineering
This proven design methodology means the practice of concurrently designing products and their manufacturing processes. It can utilize existing processes, for which the product must be designed, or new processes, for which the product and its processes must be designed concurrently.
One of the key factors in Concurrent Engineering is that all members of the teams involved in product design and all manufacturing processes work together early and actively. Everyone, from the designers and vendors to the marketers and compliance specialists, works together and takes an active role in ensuring quality, cost reduction, and time savings. Early consideration with a focus on concurrence minimizes costs and downtime and keeps everyone on the same page.
When a company works to successfully implement all three manufacturing methodologies, time and cost savings are measurable and significant. It’s important to remember that they don’t happen overnight, but if every member of the team is on board and involved, the benefits are great.
Manufacturing/Engineering In-House
It’s now widely accepted, especially following the days of overseas outsourcing and the subsequent reshoring initiatives, that the smaller the supply chain, the better. Companies that outsource much of the design, engineering, procurement, and manufacturing of their parts and products find that the greater the distance between them and their suppliers, the less control they have over the entire process. What this ultimately meant was that the opposite of the three aforementioned methodologies was taking place; therefore, efficiency was at a minimum.
As manufacturers aim to be competitive and save time and money, they are bringing production closer to home. This also means that they are eliminating the number of players involved. While manufacturing and engineering in-house are the best way to keep everything under control and most efficient, this isn’t possible for the majority of manufacturers either due to overall cost, space issues, or manpower.
However, the next best thing is to employ a trusted “one-stop-shop” designer and manufacturer, preferably one who can provide custom designs and fabrications all under the same roof. The advantages of a full-service contract manufacturer include:
- A specialized, experienced manufacturer with expertise in the process
- Advanced skills of all members of their team, from designers through fabricators, and everyone in between
- Use of their resources and connections, meaning lower-cost parts
- The dependability of a proven manufacturer and their technology
- Their entire focus is on what they make, including your parts and products
- Overall time and cost savings, as these manufacturers have mastered the lean, efficient DFM practices
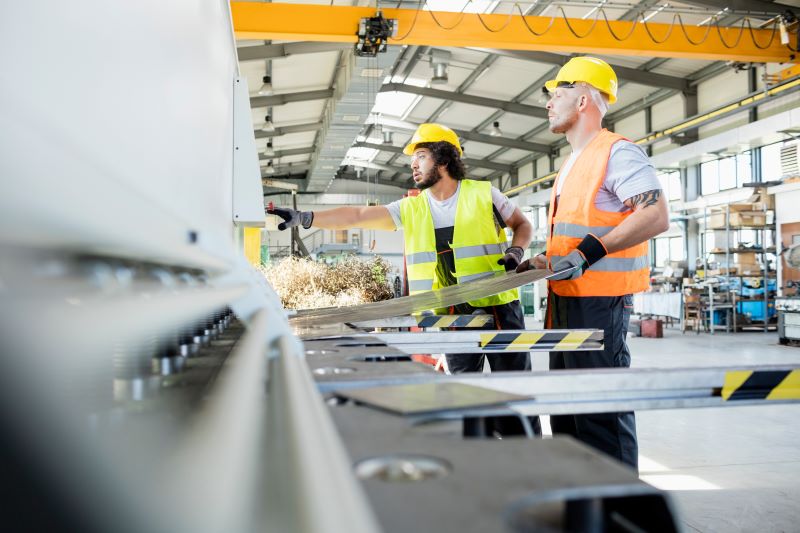
Specific Cost Considerations
Once a company has mastered, or begun implementing, the big-picture time- and cost-saving measures (DFM, Lean Manufacturing, and Concurrent Engineering), there are specific key points and areas on which to focus.
Looking at each area within the design of a product ensures the overall lean practices are being taken into account (less waste, more savings) and that every individual area of design is working most efficiently.
For these purposes, there are 12 distinct areas of focus:
- Material
- Tooling
- Quality Control
- Tolerance
- Specific Requirements
- Regulations
- Safety Factors
- Reduced Scrap
- Lead Times
- Volume
- Automation
- Packaging and Shipping.
Now, let’s take a look at each of these individually.
Material
The material chosen greatly affects the manufacturing process, and considerations include: material type (e.g. plastic and aluminum are easier to manufacture than titanium, making them more cost effective), material shape (e.g. low carbon hot rolled is often preferable to cold rolled), material size (e.g. try to allow for machining that doesn’t require too much step up in stock size, to keep waste down), etc. All of these factors contribute greatly to the time and money being spent. Be sure to talk to your product designer about all options.
Tooling
If there are multiple tooling requirements, more tool changes will be necessary, and more time will be spent. Whenever possible, try to design a part to use as few different tools as possible. Minimize tools and setups to keep costs down. Review your design and see if all machines and processes are really necessary for the finished part.
Quality Control
If your part has been in use for some time, and you have enough performance data to analyze, it’s a good idea to take a look at the current design and see if you can identify areas that can be modified to reduce costs. Perhaps the quality and integrity of the design can be adhered to while eliminating some areas of waste and/or excess. This can be done regularly to bring costs down.
Tolerance
As a general rule, the tighter the tolerance, the higher the manufacturing costs. Therefore, if tight tolerances aren’t necessary, don’t specify them. Also, keep this in mind: thread depth is one of the most expensive tolerances, and rarely matters to the part or product.
Specific Requirements
The more specific the requirements for a part’s design, the more chances there are of time and costs rising. For instance, multiple tooling requirements or complex shape requirements will ultimately cost more and require more time and labor. Factor this into the design whenever possible.
Regulations
It’s very important to regularly review the latest versions of all standards and specifications to which your part has been designed. Sometimes standards have changed or are no longer applicable, and changes can be made that bring an unexpected cost advantage to you.
Safety Factors
Similar to standards and regulations, safety factors can and often do change. If your part was originally designed with a safety factor that is no longer necessary, modifying this can save you money.
Reduced Scrap
Material use should always be kept to a minimum—this aligns with the Lean Manufacturing principles and is proven to keep waste and costs down. Analyze all of the layouts of your components and see how and where more parts can be made using fewer materials. If you can get even one more part out of a material, the savings will quickly add up.
Lead Times
Lead times have a significant impact on the cost of your product design. Take a good look at your lead time requirements, while seeing whether or not a reduction is possible and cost-effective. Analyze how lead times, in general, affect your costs and productivity, and plan for this accordingly with each particular product design.
Volume
Take a careful look at your volume requirements, which are a large part of the overall cost. If they have, for instance, increased since you began, this may offer the opportunity to streamline the design while increasing the production and manufacturing timeframe. Volume makes a big difference, so always keep it in mind.
Automation
Talk to your manufacturing/automation partner, and ask if there are any opportunities to increase automation during the production of your part. Automation is synonymous with saving time and money, and the more automation that is involved, the greater your savings.
Packaging & Shipping
Packaging and shipping are huge cost factors and should not be overlooked. You must determine the maximum volume you can get per package, and analyze ways to make the packaging most efficient. By making subtle changes, you can get a lot more out of a single package. Also, keep in mind that working with a domestic partner, rather than an overseas one, will drastically reduce shipping costs and impact your bottom line.
Partner with Arnold Machine to Improve Your Manufacturing Processes
In today’s highly competitive manufacturing landscape, time and cost considerations are critical to the success of a business. Every area in which there are ways to save money must be explored. The design of a part or product is where most of the time and money are spent; it is also where most of the opportunities for savings are. By implementing the overall, big-picture manufacturing principles—Design for Manufacturability, Lean Manufacturing, and Concurrent Engineering—and simultaneously focusing on the 12 key areas of savings, a business of any size will have significant advantages over the competition and will attract and keep the most customers.
Arnold Machine specializes in helping manufacturers optimize their processes, saving them time and money, and giving them a leg up on their competitors. Contact us today to learn how we can help you improve your processes.