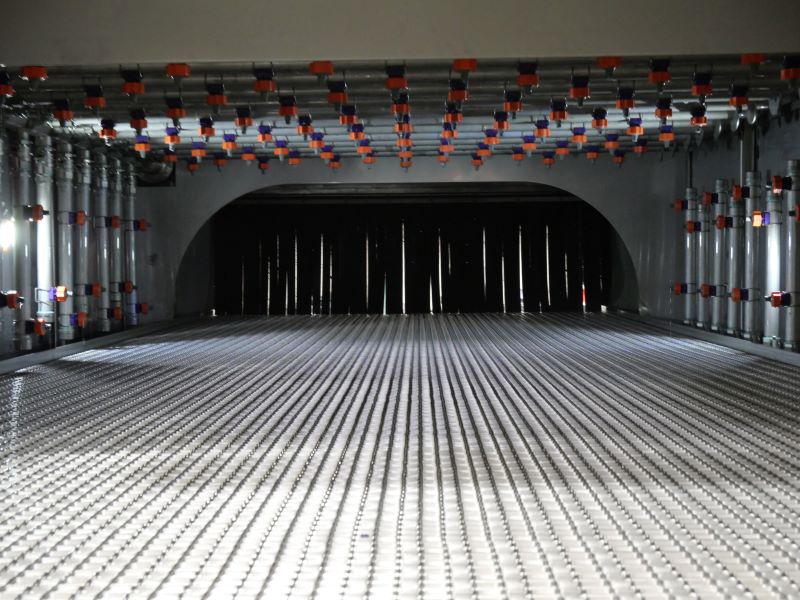
Factors to Consider When Choosing a Conveyor Parts Washer
Conveyor parts washers are critical for maintaining smooth manufacturing operations. Dealing with stubborn grease, intricate part geometries, or high production demands can make the cleaning process difficult. This is a frustrating and costly challenge for many companies.
The right solution makes it easier to overcome these challenges and boost efficiency. Choosing the best conveyor parts washer starts with knowing your operation's needs. Read on to learn more about the essential factors to consider when selecting a conveyor parts washer.
WHY CHOOSING THE RIGHT CONVEYOR PARTS WASHER MATTERS
Choosing the wrong conveyor parts washer can lead to parts not being properly cleaned, dried, or prepared for the next stage in your manufacturing process. This compromises product quality and increases cycle times, slowing production and driving up costs.
Factors like the soil load on dirty parts, material content, and the next step in your manufacturing process determine the number of stages your washer may need.
For example, basic systems may only require a 2-stage process (wash and dry), while more complex applications may need multiple stages (e.g., wash, rinse, surface prep, rinse, rinse, dry).
CRITICAL FACTORS TO EVALUATE FOR YOUR APPLICATION
Evaluating specific factors directly impacting its effectiveness for your unique application is essential when selecting a conveyor parts washer. These considerations ensure the washer meets your operational requirements and delivers consistent results.
DRYING SPECIFICATIONS
Proper drying is essential so your parts are ready for the next step in your manufacturing process or shipping. Parts that aren’t dried correctly may not function properly or could be rejected, leading to delays and added costs.
We assess the required dryness level to customize the following parameters:
- Belt speed
- Dry stage length
- Dry stage temperature
- Dry stage blower CFM (cubic feet per minute)
- Dry stage blower pressure
CLEANING SPECIFICATIONS
The level of cleanliness required for your parts is critical when choosing a pass through parts washer. It is often determined by the next step in your manufacturing process or your customer’s requirements. Parts failing to meet these standards may be rejected. This can result in production delays, increased costs, and potential customer penalties.
Consider the types of contaminants on your parts and the cleaning agents needed to remove them to achieve your desired cleanliness levels. For example, heavy grease may require higher temperatures or stronger cleaning solutions. Or delicate parts may need gentler handling methods.
We carefully consider the required level of cleanliness when designing or quoting a conveyor parts washer.
This ensures we can best determine the following:
- Wash solution temperature
- Spray pressure of the wash solution
- Flow (volume) per spray nozzle
- Spray pattern and quantity of nozzles
- Belt speed
- Percentage of soap concentration
- Wash stage length
These elements work together to maintain the washer's ability to consistently deliver the required cleanliness levels for your parts.
PART SIZE AND SHAPE
Part shape and size play a large part because of the intricacies that may be involved in the part. There may be difficult areas/passages to consider that a basic conveyor washer wouldn’t be sufficient to handle.
Our engineers need to take into account the part shape/size so we can determine the following:
- Part opening
- Belt width
- Stage length
- Spray pressure of the wash solution
- Belt speed
- Percentage of soap concentration
- Flow (volume) per spray nozzle.
- The spray pattern and quantity of nozzles
- Wash stage length
- Dry stage temperature
- Dry stage blower CFM (cubic feet per minute)
- Dry stage blower pressure
VOLUME AND THROUGHPUT
Part volume plays a significant role in the design of a conveyor parts washer. For low-volume applications, the washer is typically smaller. The belt speed is slower, giving parts more time in each stage. This allows the stages to be shorter in length.
For high-volume applications, the belt speed is faster. To maintain the same dwell time, each washer stage must be longer.
We consider the volume level to determine the following:
- Belt speed
- Belt width
- Stage length
TYPES OF CONVEYOR PARTS WASHERS OFFERED BY ARNOLD MACHINE
Arnold Machine offers a variety of conveyor parts washers, each designed for specific applications and industries. Understanding each type's unique features and benefits can help you make a more informed decision when selecting a pass-through parts washer.
ROLLER CONVEYORS
Roller conveyor washers are perfect for cleaning flat or irregularly shaped parts. This design is commonly used in manufacturing and metalworking industries.
These washers are best for large, heavy parts that are typically fed by a conveyor and unloaded onto a conveyor. They are often used for applications like transmissions and engine blocks. Their ability to handle heavy loads makes them a practical solution for demanding environments.
BELT CONVEYORS
Belt conveyor washers are the most common type and fit many applications. They are ideal for continuous cleaning of small to medium-sized parts. The flat belt system efficiently moves parts through the cleaning, rinsing, and drying stages.
These washers are best suited for high-volume production environments with consistent part sizes. They work well for both smaller and larger parts, as well as low and high-volume production runs. Their versatility makes them a reliable choice for many industries.
PARALLEL CHAIN CONVEYORS
Parallel chain washers are designed for heavy-duty cleaning of large or heavy parts. They use parallel chains to transport parts securely through the cleaning process. This design is particularly suitable for aerospace and automotive industries, where durability is critical.
These washers are best for larger parts that require fixturing for proper cleanliness. They are also very suitable for robotic loading and unloading. Common applications include transmissions and engine blocks, where precision and reliability are essential.
INCLINE BELT CONVEYORS
Incline belt washers are designed for parts that require efficient cleaning and drying. The inclined belt allows for gravity-assisted drainage and drying. This design is suitable for industries like food processing and pharmaceuticals.
These washers are ideal for high-volume parts that need inline washing with an existing set of conveyors before and after. They work well for smaller, uniform parts like nuts, bolts, and washers. Their efficiency and compact design make them a popular choice for high-throughput applications.
IMMERSION CONVEYORS
Immersion washers excel at cleaning parts with complex geometries or heavy contamination. They submerge parts in cleaning solutions to remove contaminants from hard-to-reach areas. Immersion helps “burp” parts by filling internal passageways and cleaning all surfaces effectively. Ultrasonics can be added to achieve higher internal and external cleanliness levels.
These washers are best for precision cleaning applications, such as in the medical or electronics industries. They are particularly effective for complex part geometries like fuel system components.
MONORAIL CONVEYORS
Monorail washers are well-suited for large, heavy, or delicate parts that require careful handling. They use a monorail system to suspend parts during cleaning. This design is widely used in automotive and heavy machinery industries.
These washers are best for assembly lines where parts are already on a monorail system. The washer is designed to envelop the existing overhead monorail, making it a seamless addition to the production process. Typical applications include larger parts or assemblies like transmissions and motors.
ARNOLD MACHINE IS YOUR CONVEYOR PARTS WASHER EXPERT
At Arnold Machine, we’re dedicated to providing top-tier conveyor parts washers tailored to your specific needs. Our expertise ensures that each washer we manufacture is designed to meet the highest standards of cleanliness and efficiency. Whether you're dealing with small parts or large assemblies, we have the right solution for you.
Explore our range of conveyor parts washers below to find the perfect fit for your application. If you have any questions or need a custom quote, don't hesitate to speak with one of our experts. We're here to help you achieve unparalleled cleaning results.