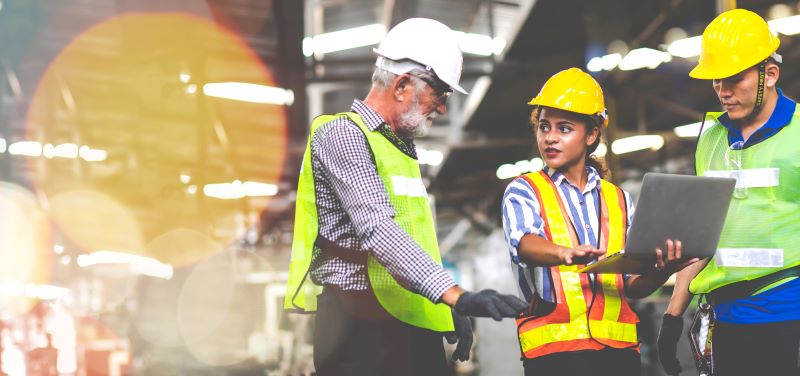
Estimating & Cutting Costs Without Impacting Quality of Machined Parts
When designing components for a new project, there are several factors to consider. Whether it’s cost estimation hurdles or a lack of information when designing for manufacturing, early issues can hurt either your budget or the quality of the finished component in the future. In this blog, you’ll find details on some of the leading cost estimating methods and tactics for using those methods in designing for manufacturing to reduce costs.
Leading Cost Estimating Methods for Machining
Manufacturing firms need to have an accurate estimate of product design and development costs. This is especially important in the current economy because the shorter lifespan of products accentuates the importance of design and development stages. There are two main cost estimation algorithms: feature-based cost estimation and parametric cost estimation.
Feature-Based Cost Estimation
The estimation algorithm that most closely follows the machining processes used to manufacture a part will be feature-based cost estimation. Manufacturing cost is determined by shape complexity, product precision, and the tooling process.
If these requirements can be obtained and considered during the design stage, estimating manufacturing cost during the early product development stage should become a reasonable task. Feature-based cost models use bottom-up estimating principles and formulas (speeds and feeds, machine cut/bend rates, etc.) to generate cycle times, so estimating is not only much faster than traditional methods but extremely accurate.
The ultimate feature-based cost estimation would be to do the CAM work for the part, generate the code, run it through a simulator, and base estimates on that information. Unfortunately, that is generally too complicated. An experienced machinist can look at a print for a part, or even a simple sketch, and pretty quickly decide on a set of machining operations that will produce the part.
Or you could use feature recognition software to analyze a CAD model and output a set of features. And once the set of features needed to manufacture a particular part is determined, you can add details until you have a full-fledged feature-based cost estimate.
Parametric Cost Estimation
However, suppose the part you’re trying to estimate is similar to a lot of other parts you’ve estimated in the past. Perhaps you are a socket manufacturer and you have detailed knowledge about the cost to manufacture sockets on hand.
The idea behind parametric cost estimation is to create a model that allows you to tell it the overall specifications, or parameters, for one of these parts, and it will use the accumulated data to produce an estimate. Parametric cost estimation works well provided the type of part you’re estimating is nominally standard and you have data on hand for what it will cost to build.
There are cost estimation vendors that have such databases as well, but the difficulty is in knowing how consistent their database is and whether it matches costs closely enough to be useful. Unfortunately, the only way to tell this is to buy the cost estimation software and use it for a while, which is an expensive way to find out.
Today, parametric estimating is usually applied to large systems, such as those performed for the Department of Defense. While many parametric analysts use commercially available general-purpose cost models, many others have created their models to satisfy specialized needs. Your level of expertise and experience will dictate your choices in this crucial area.
Saving Money with Design for Manufacturing
Today, technological and cultural changes in manufacturing are trimming the lines between all steps in the product development lifecycle, leading to leaner, greener, more competitive, and more profitable production methods. One of these changes in perspective goes by the name Design for Manufacturing (DFM), which promises to simplify the production process by emphasizing the importance of pre-production planning, especially in the product design phase.
DFM describes the process of designing or engineering a product to facilitate its manufacturability and reduce its overall manufacturing costs. Properly implemented, DFM should enable potential future problems to be fixed in the design phase, which is the least costly area to address them. And because most product lifecycle costs are committed at the design stage, it is also the phase in which cost estimates are most likely to affect a product’s financial expectations.
The key term in DFM is producibility. Naturally, the design of a product will have enormous consequences for how it will be produced, which has always been true. While DFM is not new (it’s been around quite a while), it has only recently grabbed the spotlight as a celebrated cause because of the renewed focus on industrial processes in general, in light of the “manufacturing renaissance” currently taking place in the United States. Certain “best practices” have already been established for DFM by engineers. So let’s take a look at a few of them.
Material Type
The type of material chosen for the part will greatly affect manufacturability. For example, plastic, aluminum, and brass are very easy to machine compared to titanium and hard steel alloys. If the part must be accurately made of steel, specify low-carbon hot rolled rather than cold rolled. It is much more stable, whereas the cold rolled can warp and require multiple machining operations to achieve the same precision.
Material Shape
Choosing a stock shape that is close to the final part shape can reduce both material waste and machining time. For example, if a part is primarily cylindrical, starting with round bar stock instead of square or rectangular saves the extra effort and cost of machining away corners. Likewise, if a part is flat and thin, plate stock may be a better starting point than a thick block. Selecting the right initial shape helps keep your material costs down and your machining operations more efficient.
Material Size
When deciding your part’s dimensions, visualize how they will interact with the rough stock sizes that are available. You need an allowance for machining that doesn’t require too much step up in rough stock size; otherwise, you waste the time and the material cost of turning that extra stock into chips.
Tolerances
The tighter the tolerances, the higher the manufacturing costs. Don’t specify tight tolerances unless they’re needed. One of the most expensive tolerances is thread depth, which often doesn’t matter. Specifying thread depth to three decimal places is seldom going to accomplish much, other than driving up costs substantially.
Minimize Machine Time
The volume and shape of the material to be removed, as well as how fast the tools can be fed, will determine the machining time. The shorter the tool is relative to its diameter, the faster it can be fed through the material.
Minimize Tooling Requirements
Be aware that the machine tool has a limited number of slots in its tool changer, and each one is valuable. Try to design the part to use as few different tools as possible.
Minimize Setups
Possible design parts should be made in as few setups as possible, preferably in one setup.
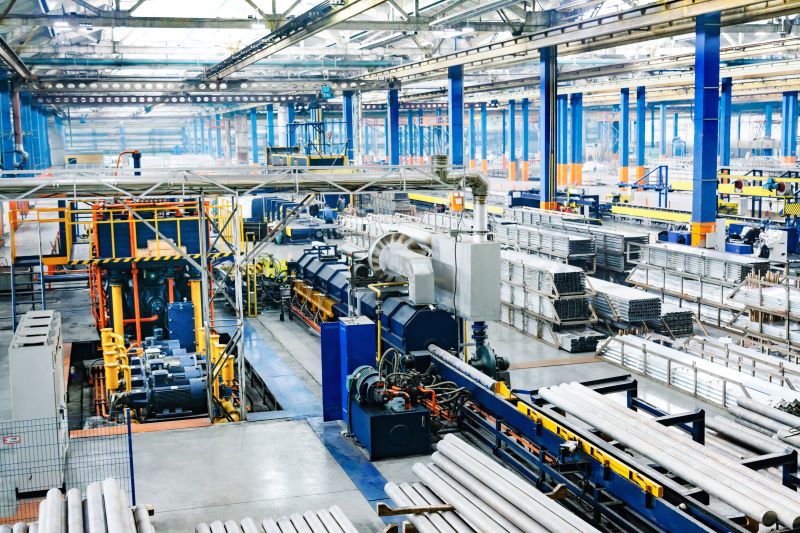
The Significance of Tight Tolerances
In manufacturing, we can’t take a chance that the parts won’t fit. That is unacceptable to the parts maker and the customer. That’s where tolerances come into play.
To fabricate components, a manufacturer follows dimensional specifications. For the part to be accurately made, the dimensions must be met. Although this is acceptable, loose tolerances are not what any manufacturer is aiming for. It is important to the client that a manufacturer strives for the tightest tolerances they can manage, so that parts will fit perfectly into the final assembly or system. At the same time, tolerances tighter than they need to be can be a costly proposition for your machined parts.
Engineering for tight tolerances is the first step in precision machining. This is of utmost importance with extremely complex components. In the design process, understanding how materials will react in the environment, as well as understanding shrink rates and warp, aids the manufacturer in maintaining and controlling not just tight, but properly matched, tolerances.
When a component is ready for manufacturing, precision CNC machining is an extremely reliable process. Even though CNC offers a tighter control of the machining process, there are additional ways to improve tolerances. Advanced CNC equipment and controls, improved coatings and inserts, and better machining techniques all work together to arrive at the tightest tolerances possible.
If all factors are taken into account and any problems are realized up front, controlling tolerances could help to reduce manufacturing costs, even as they become tighter. Components manufactured to tight tolerances save in the long run by being accurate and ready for assembly.
Strategies to Reduce Costs & Increase Quality in Your Part Design
There are few components for which costs cannot be cut. The key is to do so without sacrificing quality. That’s why so many companies turn to Arnold Machine. Our core focus is on providing the best possible machined components for our customers, combining our range of skills in developing automation systems, machining diverse metal and elastomer materials, and offering value-added services like assembly and finishing.
To learn more about Arnold Machine and how our approach to cost savings in manufacturing, design processes, and quality in everything we do can benefit your next project, contact us today or request a design consultation.