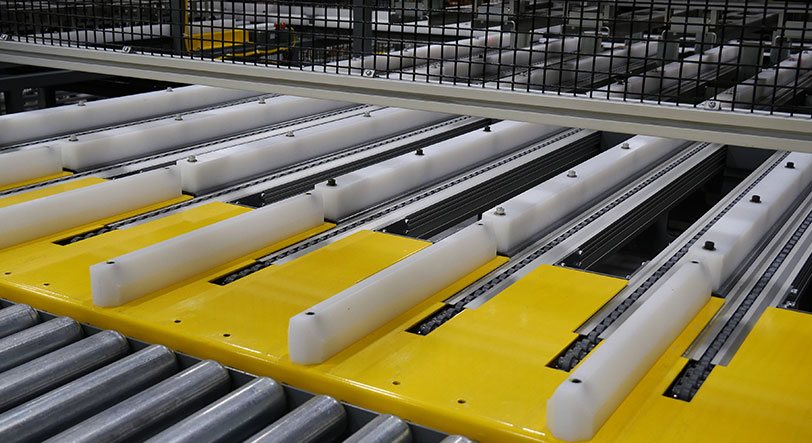
Combining Automation and Parts Washing
Creating an automated load/unload Inline-6 Rotary Basket Parts Washer for a firearms manufacturer
The Challenge:
A world-renowned manufacturer of firearms, ammunitions and firearm accessories reached out to Arnold Machine after making the decision to bring magazine production in-house.
The customer needed to wash magazines after their stamping process, prior to welding. A defined clean specification was needed to ensure there was no contaminant or oil that could interfere with the welding process. If any residue is left on the magazine prior to welding, it could lead to quality defects.
To better prepare for supply demands and any future labor issues, the company also decided to incorporate automation into most of the processes.
Due to the nature of the parts, we could not allow the magazines to tumble against each other. This could cause damage to some of the delicate features of the part.
Another challenge was due to different part lengths. Because there were numerous lengths of parts, we needed to ensure thorough cleanliness and still be able to wash different part lengths at the same time for efficiency.
For Arnold Machine, this was our first collaborative project between the former FMT Parts Washer team and the automation team. It was an excellent project to kick off the acquisition and combine unique knowledge and skillsets.
The Solution:
After discussing these challenges with the company, our team designed an automated, rotary basket parts washer utilizing:
- FANUC Vision Guided 6-axis Robot
- FANUC 2D Vision
- Multiple Conveyor Systems
To make sure the parts remained stable during the wash and didn’t come in contact, our engineering team determined that the baskets would have a 3D printed insert attached to the bottom of the baskets. This insert separated the parts while keeping them stable so they could be loaded onto the baskets easily and prevent the parts from tumbling against each other during the wash, rinse and drying stages.
To solve the multiple part length issues, our engineering team designed a “top-hat” solution. The top-hat would move down until about 0.040” from the top of the parts, thus allowing the parts to move slightly which would allow a proper amount of solution to flush around the parts to ensure proper cleaning and maintain the company’s cleanliness specifications.
The Data:
By bringing this process in-house, the customer gained much needed quality control and the ability to produce the quantity needed to overcome potential product shortages.
This automated parts washing system can run 4 cycles per hour, which totals 24 baskets per hour. Since each basket holds 40 parts, the washer is capable of washing a total of 960 magazines per hour.
It only requires one part-time employee to operate the system. The operator loads parts in the baskets and feeds the baskets onto the infeed conveyors.
The Results:
Upon completion of this system, the end user was beyond pleased and future projects are already being discussed.
“[Redacted for Privacy] could not be more pleased with the equipment received and the work performed by Arnold Machine. The entire team was professional, knowledgeable, and courteous. The design, quality, and craftsmanship of the Automated Washer is top notch, a machine we’ll be proud to display within our facility. We look forward to running full production volume so that the machine can demonstrate its true capabilities. [Redacted] is happy to have found a hard-working company willing to step up to our demanding requirements and hopes to work together again on future projects.”
Arnold Machine’s acquisition of the parts washer division from FMT, Inc. continues to prove that combining our engineering staff and automation knowledge to the already robust FMT Parts Washers will be a combination that few can compete with when a client is looking for a fully automated solution to parts washing.