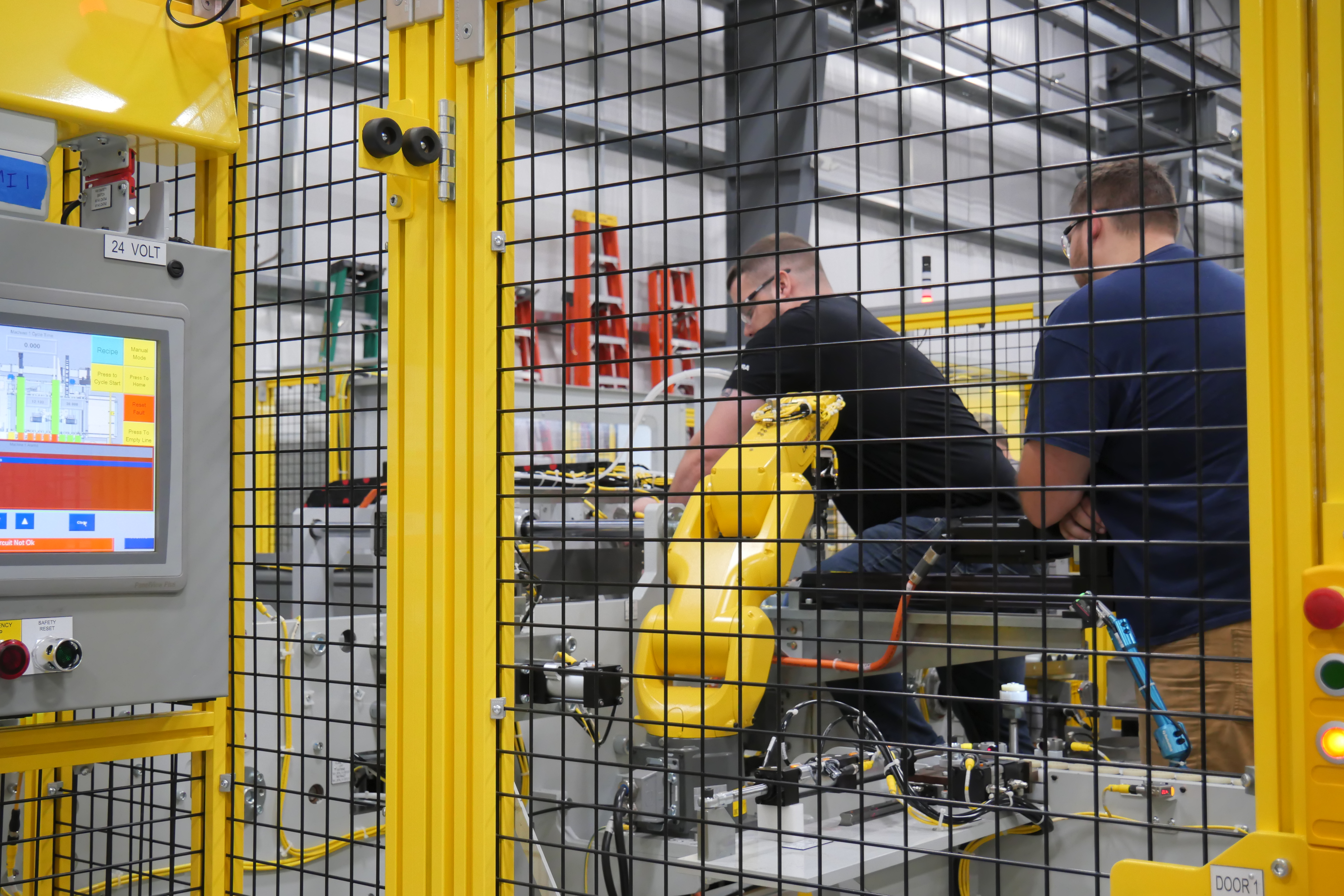
Automated Assembly for Motorized Drive Rollers
How a strategic automation solution for Honeywell Intelligrated doubled production capacity and saved over $750,000 in labor costs annually
Company Profile
Honeywell Intelligrated is a leading provider of warehouse automation solutions that streamline distribution and fulfillment operations worldwide. Their motorized drive rollers (MDR) power the conveyors used in warehouse automation systems, making them a critical component of the supply chain industry.
Objective
Honeywell sought to significantly increase production capacity for motorized drive rollers to meet growing demand while reducing labor dependency. Their goal was to replace a labor-intensive process with a cost-effective, automated solution that maintained quality and consistency.
Previous Process and Challenges
The previous assembly process for MDRs was manual and labor-heavy, requiring eight people per shift to assemble around 2,000 MDRs daily. The need for human oversight in pressing, drilling, riveting, and flaring steps led to inconsistent production rates and quality, making it challenging to scale operations. To meet production demands of up to 4,000 MDRs per day, Honeywell would have needed to duplicate the current process—doubling floor space and staffing, which was impractical due to the difficulty of finding and retaining skilled labor.
Project Scope
Arnold Machine was tasked with developing an automated system that could:
- Assemble up to 4,000 MDRs per day
- Reduce labor from eight people to three per shift
- Automatically handle five different MDR part variations with minimal operator intervention
- Ensure the highest levels of quality and consistency by integrating automated quality control systems
Timeline
While typical projects of this size take 12 to 14 months, customer demands and a change in the final production location extended the project timeline. Despite this, Arnold Machine adapted quickly and delivered a successful solution.
Project Challenges
The primary challenges included designing a system that:
- Reduced human dependency while maintaining fast cycle times
- Automatically handled varying MDR part sizes and internal components
- Implemented robust quality control to prevent defects
Honeywell required an automation solution that could produce MDRs ranging from 16 to 34 inches in length with two different types of internal components. The automation had to ensure the correct parts were used and automatically reject incorrect components.
System Overview
Arnold Machine designed an automated assembly line featuring:
- Roller Handling: A 3D vision system guides a robot to pick randomly placed roller bodies from dunnage and place them for assembly.
- Flaring: The roller body is flared on both ends to allow for component insertion.
- Hub Insertion and Drilling: The drive hub is robotically inserted into the roller body, followed by automated drilling and riveting to secure the hub in place.
- Motor Installation: An operator manually inserts the drive motor, which is then pressed and crimped into place by the system.
- Bearing Installation: Bearings are robotically inserted and crimped to secure them within the roller body.
- Quality Control: The system includes automated testing stations to verify motor performance and roller runout. Any failures are quarantined for further inspection.
The system requires only two operators for assembly and one for material handling, reducing the labor requirement from eight people to three per shift.
How the End Product Helped the Company
The automation solution doubled Honeywell’s production capacity from 2,000 to 4,000 MDRs per day while reducing labor costs by $750,000 annually. Quality and consistency improved with automated assembly, reducing the likelihood of human error and material waste.
Results, ROI & Future Plans
- Labor Reduction: Reduced from 8 people per shift to 3, saving 15 positions across three shifts daily.
- Enhanced Quality: Automated quality checks at various stages improved overall product quality.
- Material Savings: Reduced part defects led to decreased material costs.
- Production Impact: Production doubled, allowing Honeywell to meet customer demand more effectively.
- Cost Savings: By automating the MDR assembly process, Honeywell avoided the cost of duplicating manual assembly lines. The project’s estimated budget was $2.25 million, with a labor savings of $750,000 annually. Factoring in increased production rates, the payback period for this solution is approximately nine months.
- Future Expansion: With a more efficient and scalable MDR production process, Honeywell is well-positioned to pursue new business opportunities. The success of this project opens the door for future collaborations with Arnold Machine to further optimize warehouse automation solutions.
Lessons Learned
Key insights from this project include the importance of adapting to part variability in automated systems and the value of integrating automated quality control measures. By reducing labor and improving consistency, Arnold Machine demonstrated the ability to deliver cost-effective, high-performance automation solutions for complex assembly processes.