Tumble Spray Coating Systems
Streamline your processes, eliminate quality issues, and achieve total coverage without multiple steps. Our innovative Tumble Spray systems deliver unsurpassed performance and reliability.
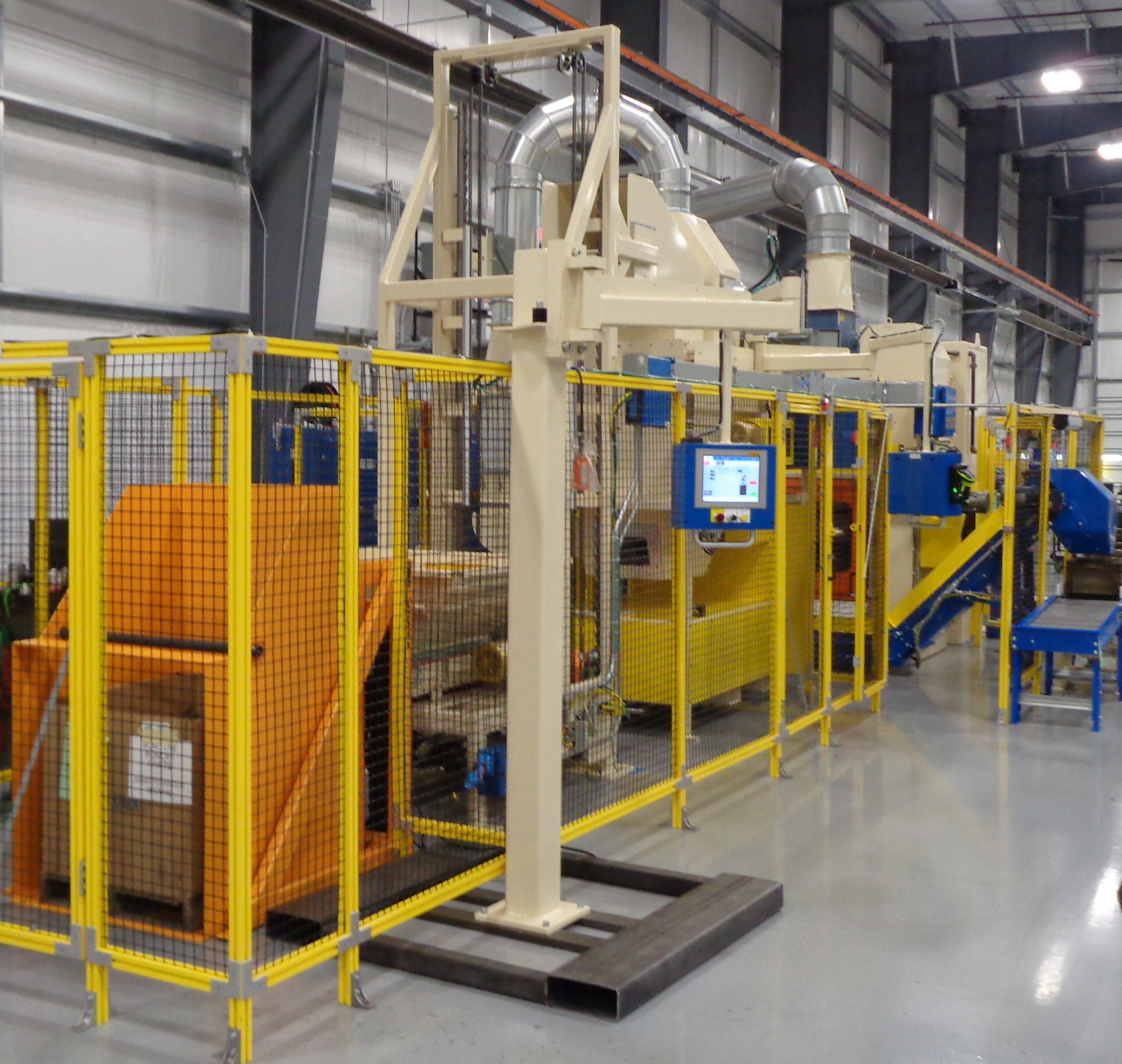
Benefits of Tumble Spray Coating Systems
How Tumble Spray Coating Systems Work
The Tumble Spray Coating process begins with loading phosphated products into the Roll-Pack Upender. Operators manually actuate the products into an Infeed Hopper, which is conveyed to an Incline Feed Hopper until the batch weight for the specific product recipe has been satisfied. This automated batch control ensures consistent outcomes for every run.
Product Pre-Treatment
The Incline Feed Hopper then raises and dumps the product onto the infeed chute of the preheat tumbler oven as the oven door is opened. The product will tumble in the preheat oven for a preset time until the preheat temp is reached. The preheat tumbler unloads into another transfer hopper, and the product automatically shuttles to a tumble spray booth.
Automated Coating
The tumble spray booth door opens, and the transfer hopper dumps the product into it. The door seals and the primer spray gun begins to apply primer material. The spray gun traverses side to side while spraying for a predetermined time. Once complete and after an adjustable timed wet out, the topcoat spray gun performs the same process. A single carriage has multiple mounted spray guns.
Finalization and Batch Management
Following the spray cycle, coated products unload to a finished outfeed conveyor and automatically fill bulk totes to your programmed batch sizes. Operators then remove the filled totes to keep the workflow moving efficiently.
Common Applications
Tumble Spray Coating Systems excel at finishing a variety of parts and materials. The average batch weight is 20-30 lbs. It must fit in the 16” deep x 40” wide spray chamber.
For example, the average batch size for a 3” OD x 3 “ Long Window Metal or a 1- ¾” x ⅛” wall tube x 3 “ long would be around 100 pieces. This combination allows for a good stir and 100% coverage.
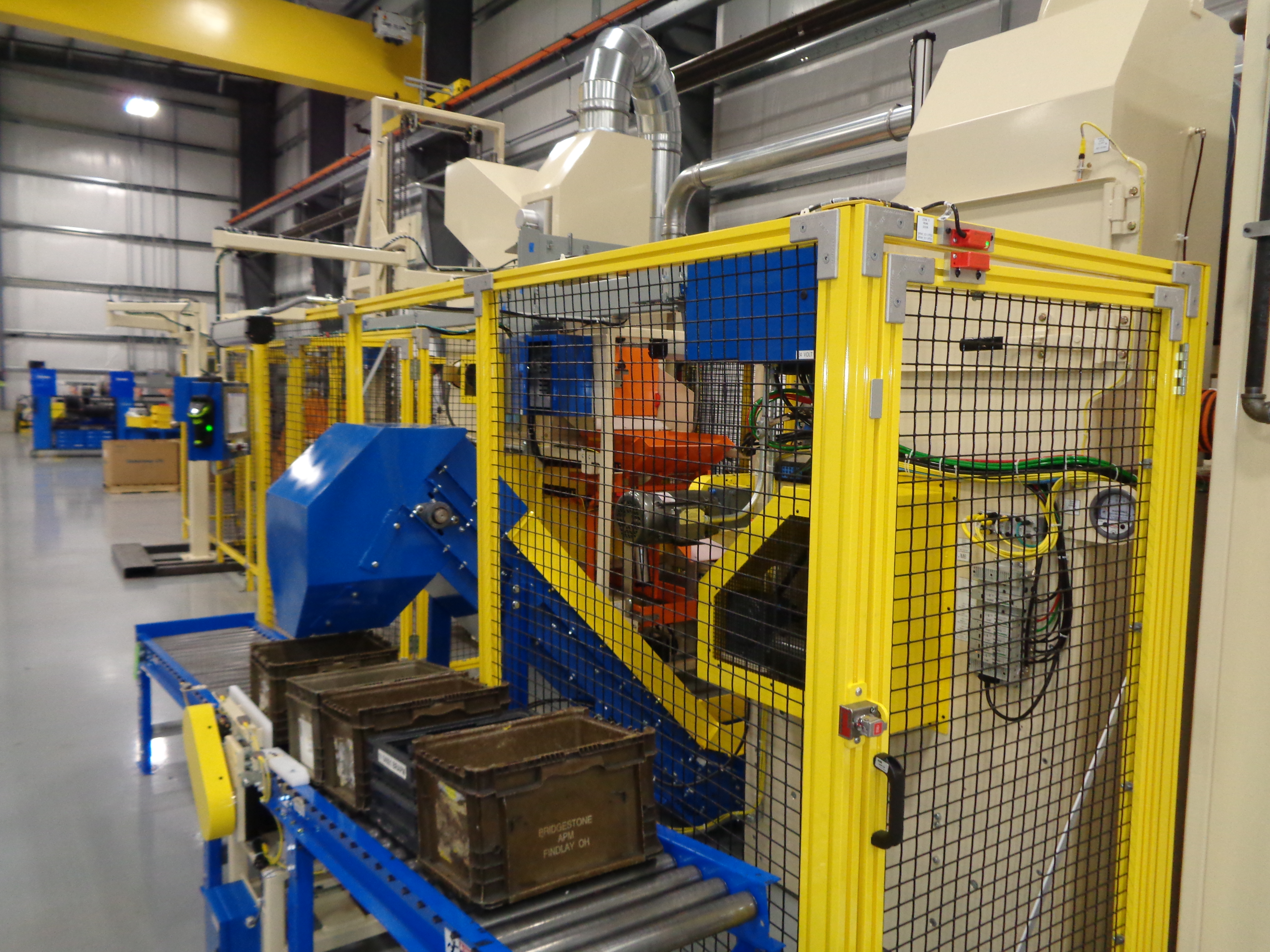
Features & Specs
Our Tumble Spray Coating Systems offer exceptional adaptability to meet your specific coating needs. We can customize it to work with solvent or water-based materials and single-coat applications. Part recipes are completely tailored to your unique requirements. Additionally, we can customize the system to fit your tote sizes and floor layout. This allows for either bulk loading into totes or using smaller totes that are easy to handle in post-processing.
We designed our spray coating system to utilize and apply a solvent-based adhesive primer and solvent-based adhesive top coat (e.g., 205 Chemlok Adhesive Primer and a 6411 Chemlok Adhesive Top Coat). The system also maximizes primer and topcoat utilization and minimizes all waste products, including primer, topcoat, filters, etc.
Our coating systems feature several standard safety measures designed to protect personnel. Guarding with safety interlocked doors prevents access to moving parts, and emergency stops are always available. The system displays e-stops and interlocks on the Human Machine Interface (HMI).
Other features include:
- Operators can use the HMI to control the line speed with limited tolerance options. This helps to facilitate performing secondary processes.
- The system comes with two HMI Screens. One is on a pendant arm for the spray booth setup and oven controls. The other is fixed and mounted at the load station/dump hopper.
- We use a standard partner, Allen-Bradley CompacLogix PLC control system.
- The design allows for easy access to regular maintenance items. This helps to limit downtime and ensure thorough cleaning.
- The system uses a main electrical enclosure with (1) 480V, 3PH drop, and (1) 1" airline of compressed air.
Our Tumble Spray Coating Systems stand out because they automate the entire process. From sorting parts into batches to preheating, coating, and offloading packaging, the system minimizes the need for human intervention. This automation ensures a more streamlined and efficient spray coating.
Trust Arnold Machine with Your Coating System Needs
Partnering with Arnold Machine means working with an experienced team committed to innovation and exceeding expectations. Our expertise spans numerous industries and allows us to create safe, efficient, and reliable systems to meet your needs. We use the latest automation technologies and collaborative approaches to provide comprehensive coating solutions.
Tumble Spray Coating System FAQ
-
How many operators does the tumble spray coating equipment consume?
-
What should I expect for maintenance?
-
What should I expect for throughput?
Other Coating Systems and Related Machines
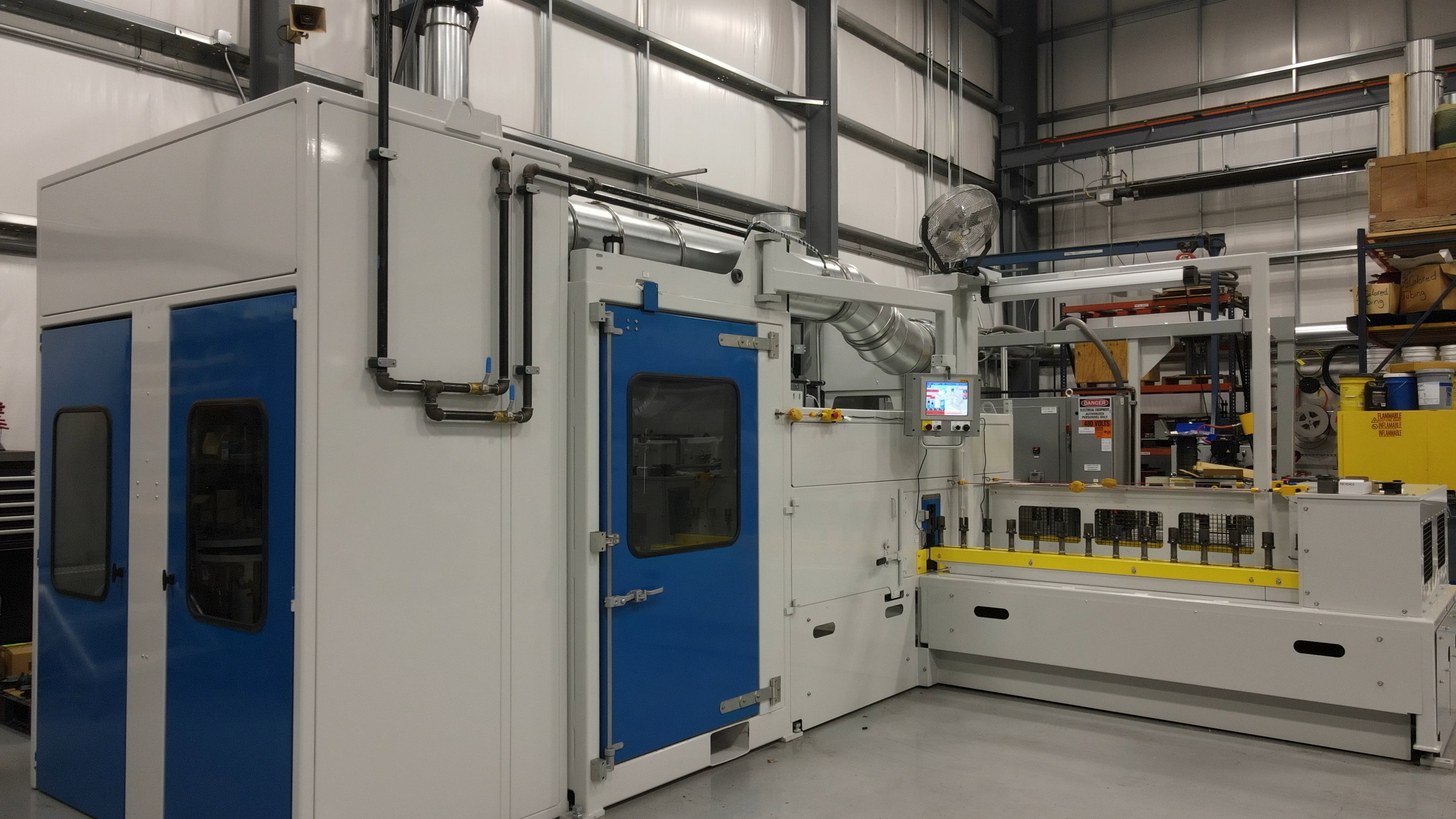
Chain-on-Edge Conveyors
Improve efficiency and performance with automated Chain-on-Edge (CoE) Conveyor & Spray systems. Our robotic-powered machines deliver consistent coating thickness and coverage compared to manual spraying.
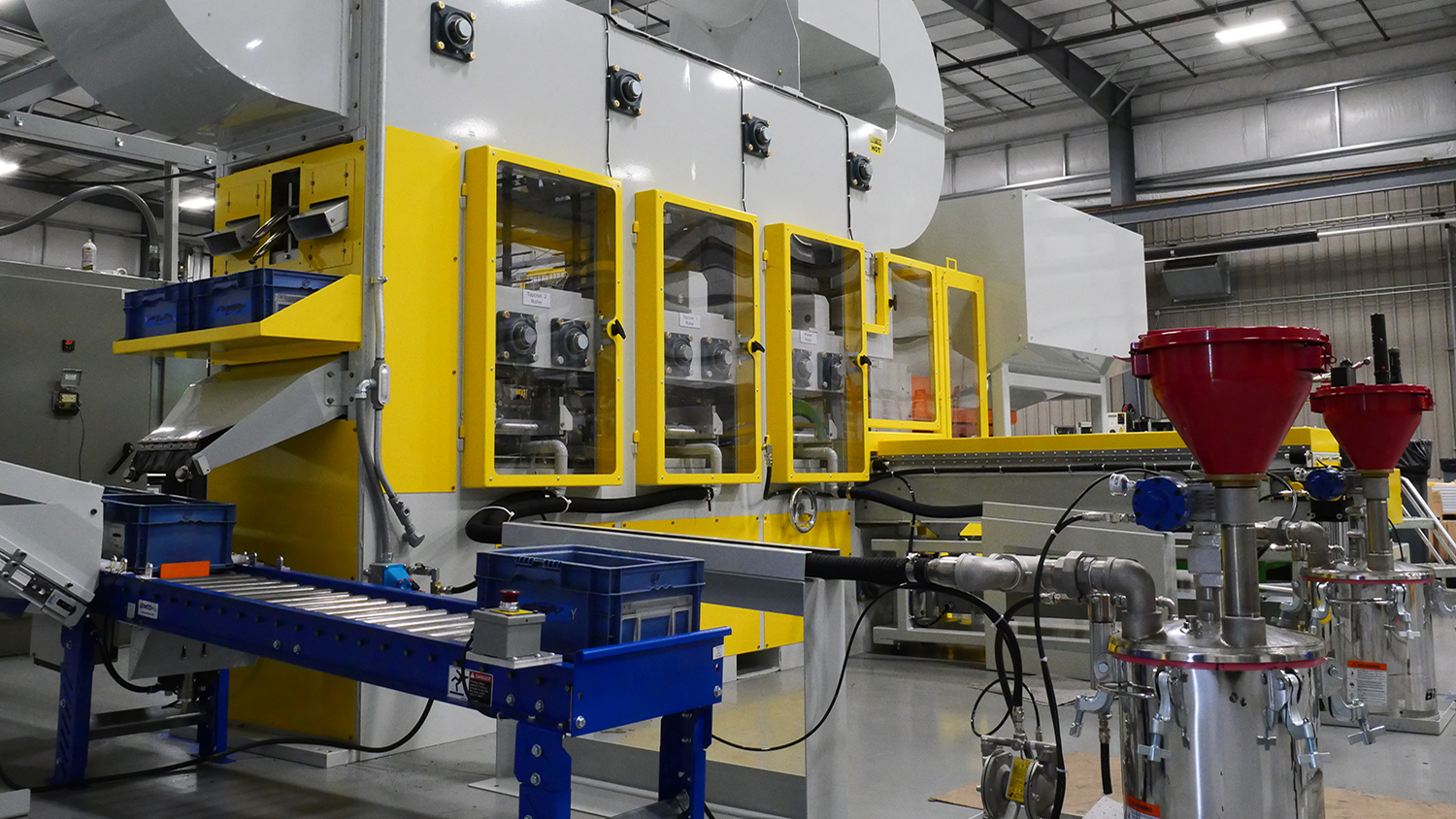
Roll Coater Systems
Precise application of coatings for consistent and high-quality finishes.
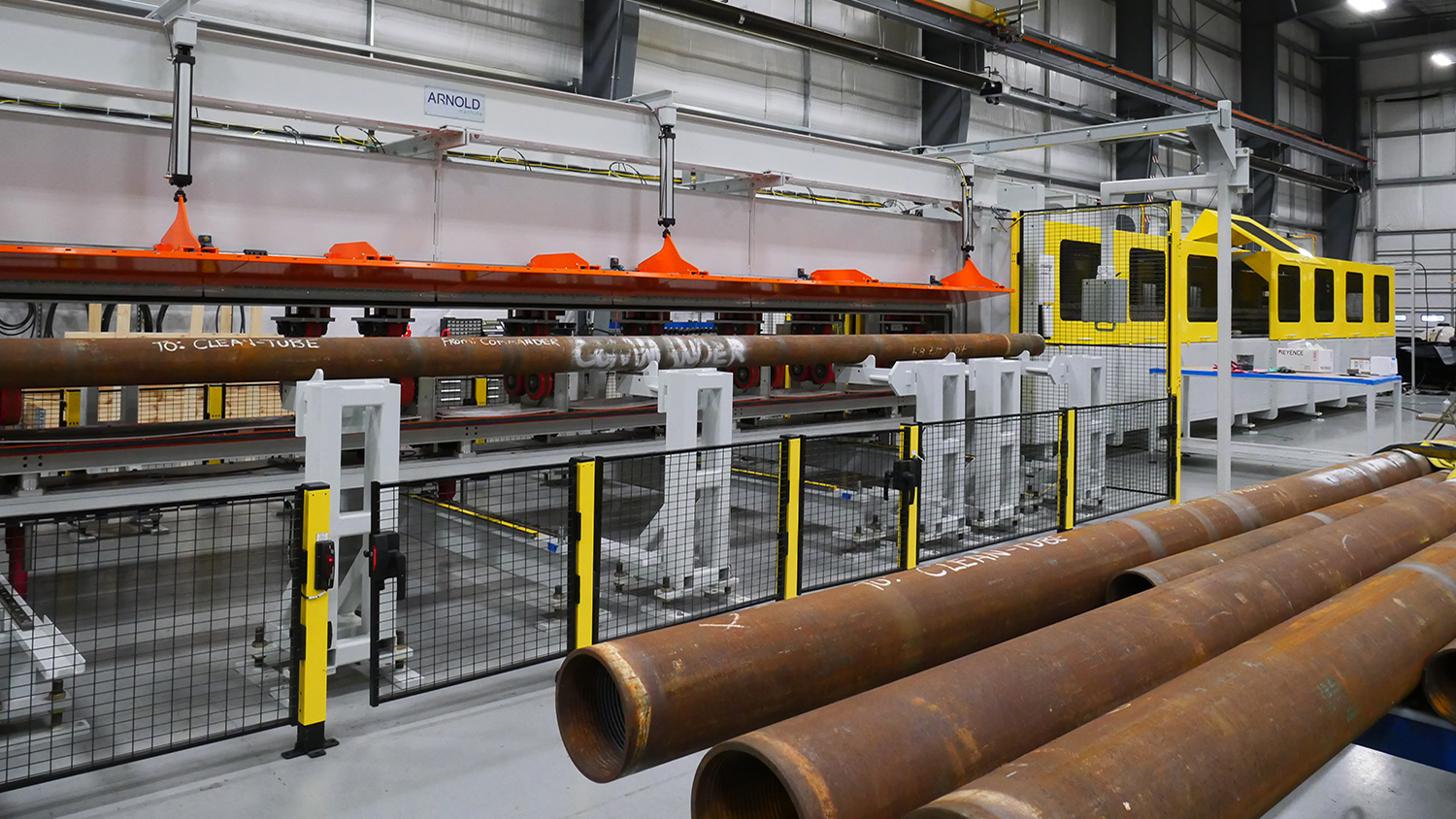
Interior Diameter (ID) Tube Spray Machines
Achieve superior tube coating efficiency and reduce material costs. Protect your workforce with a safer and more controlled coating process.
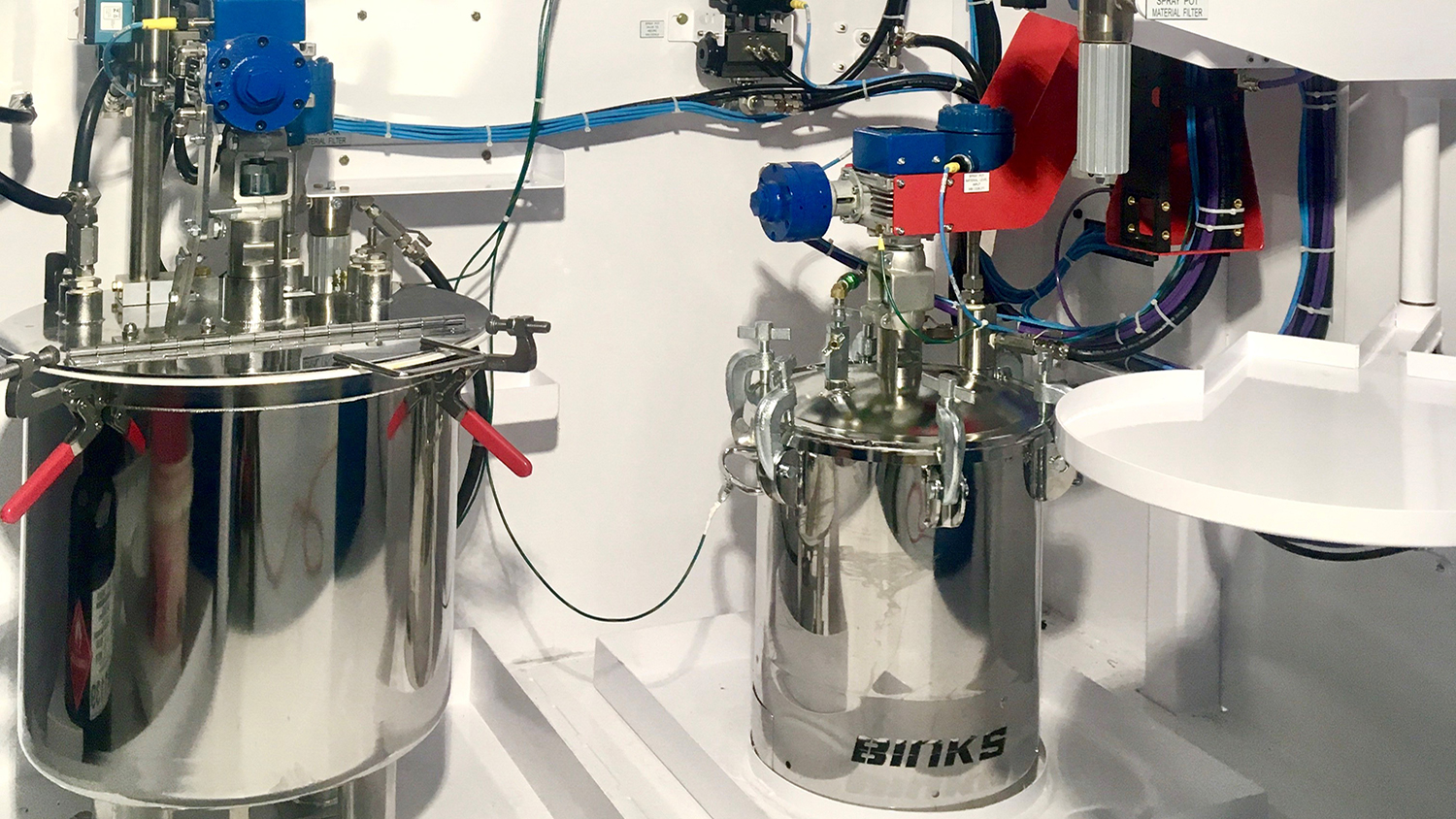
Automatic Viscosity Bulk Mixing Stations
Achieve flawless coatings and reduce waste with precise viscosity control. Upgrade your production process for consistently superior results.
Featured Posts
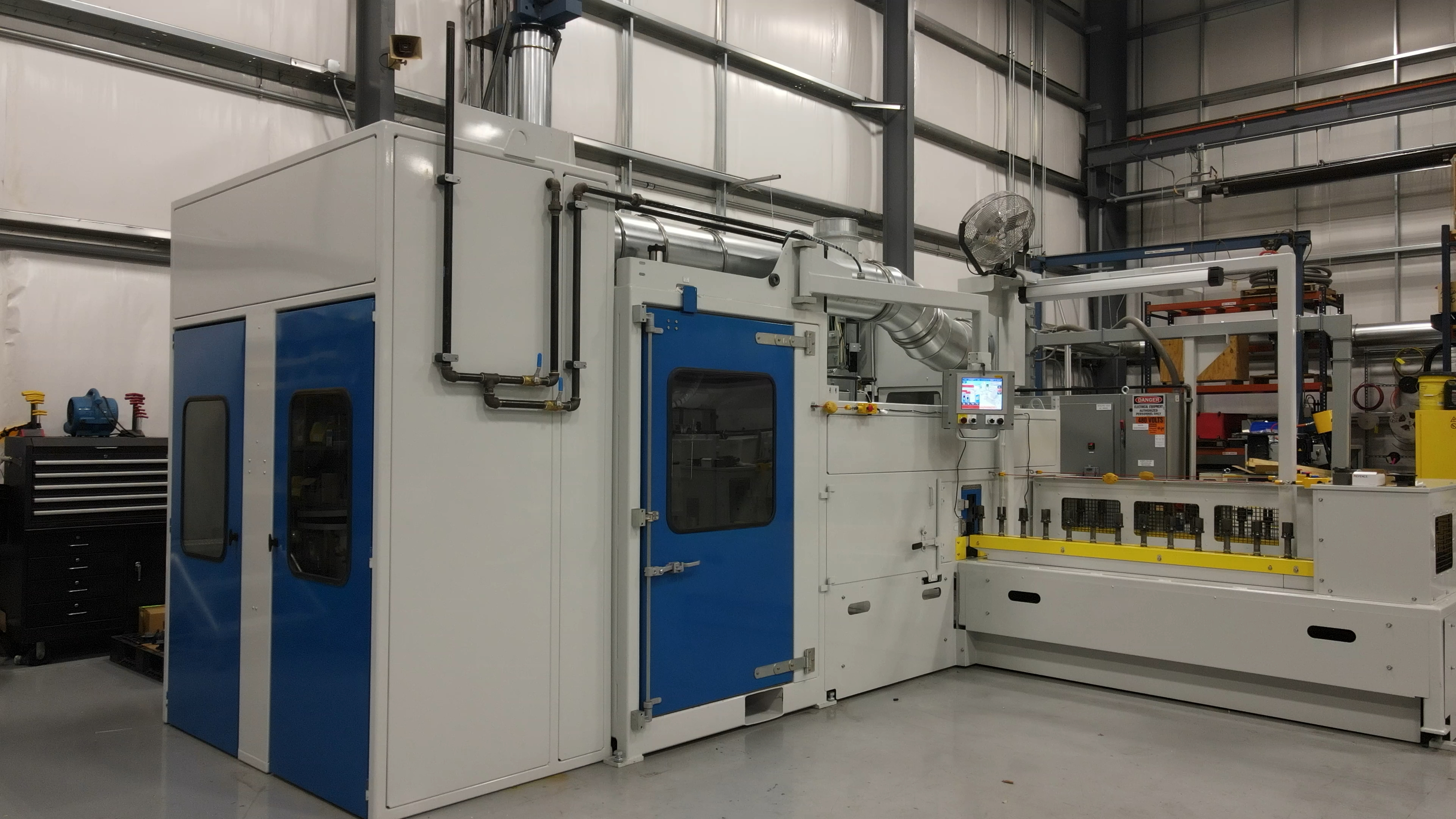
Automatic Coating Systems: Minimize the Cost of Investment
Discover a proven way high-volume manufacturers can boost throughput and eliminate the up-front capital costs of purchasing a machine.
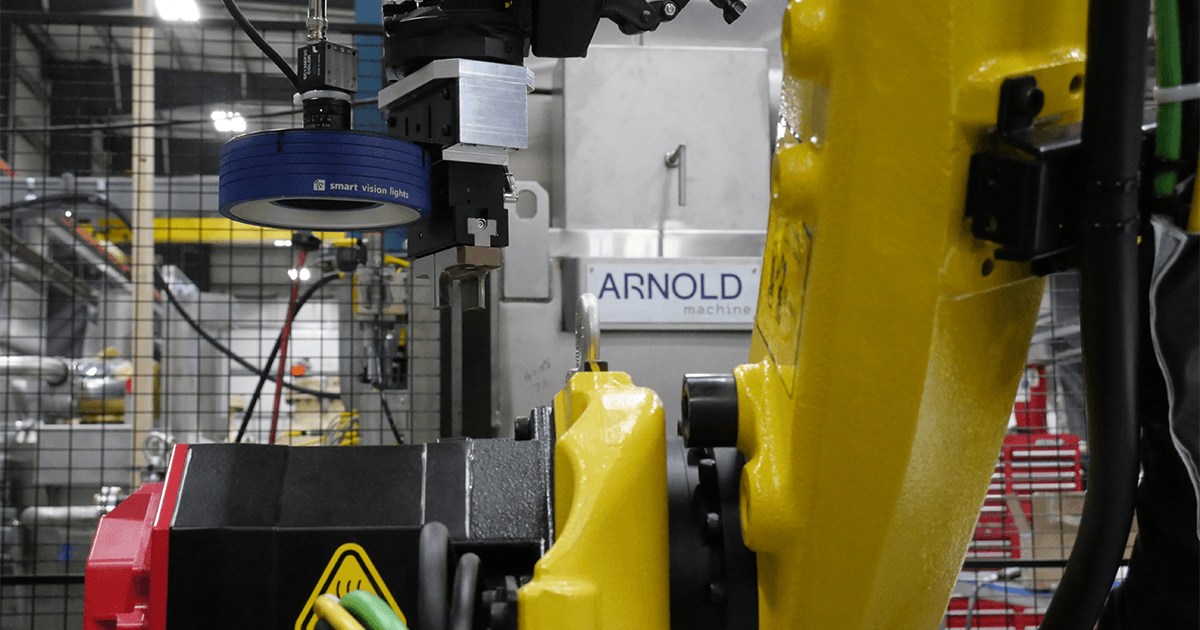
3 Key Reasons to Consider Spray Equipment Automation
Learn more about the value and advantages of automated spray equipment over manual processes.
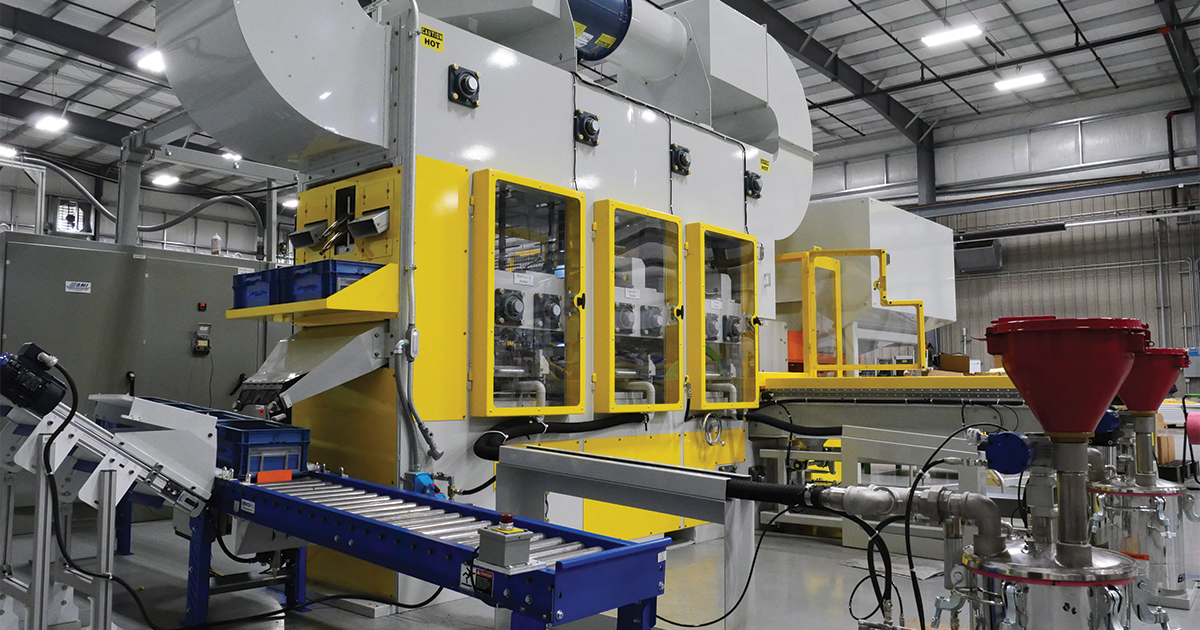
Realizing Potential Savings with Spray Automation Equipment
Explore seven ways spray automation equipment can lead to huge cost savings for manufacturers.